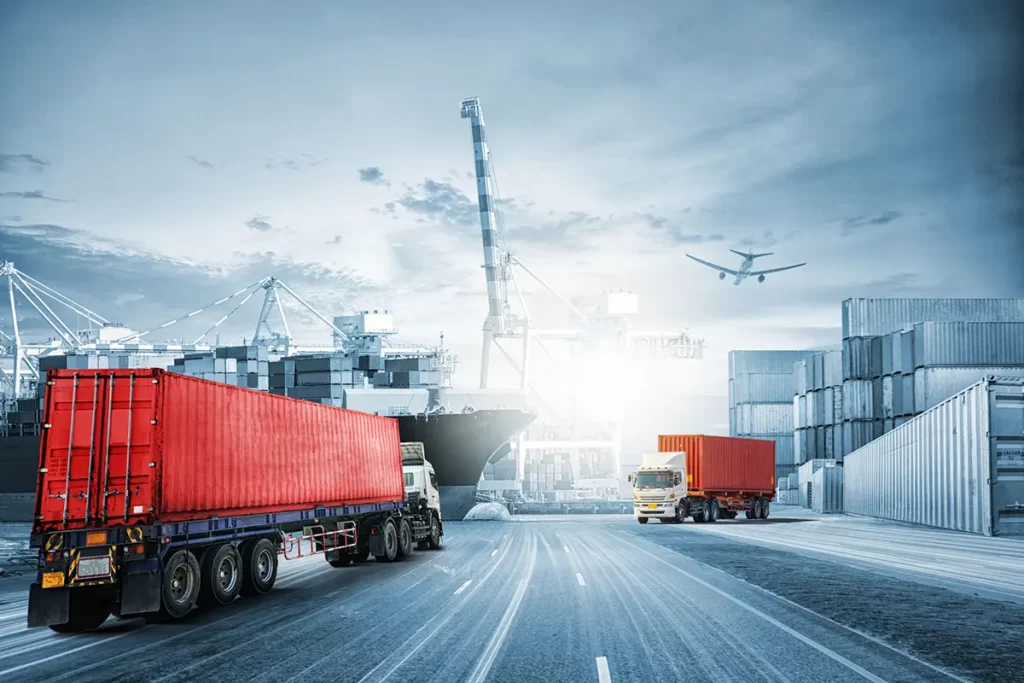
The supply chain is fragile. Nothing has proven that more than 2020 and the COVID-19 pandemic. All over the globe, supply chains have been significantly affected. These were actually not new issues, but they were a magnification of issues that supply chain professionals were always dealing with.
It has always been a best practice for supply chain professionals to have a back-up plan through the use of “B suppliers.” However, as this year has shown us, it has never been more important to put this into practice.
Supply Chain Disruptions
66% of businesses don’t have a plan B in the case of supply chain emergencies. This is in spite of the fact that supply chain disruptions can lead to serious financial and reputational damage. In addition to having B suppliers in place, it’s important to have a risk management strategy.
This year alone has given us many examples of supply chain disruptions. The global food supply chain was significantly impacted by the pandemic. There has been a shortage of aluminum cans in the United States, creating issues for breweries and beverage manufacturers. Problems with international supply chain disruptions have supply chain professionals approaching the subject with a new perspective.
What can supply chain professionals do? The last thing they want is to see a negative impact on fulfillment because their suppliers can’t meet demand. Having a backup plan is essential, but there are things that need to be considered.
Understanding B Suppliers
It needs to be understood that plan B suppliers will require long-term agreements and potentially more preparation time. They may need a commitment of several months or more. Before making any agreements, supply chain professionals also need to have a solid understanding of the supplier’s capacity.
It’s important to have total transparency with suppliers. It’s helpful to understand a supplier’s financial performance: Have they struggled financially in recent months? You also need to understand their health and safety record: How has their health and safety been in the past? Additionally, you need to identify their production capacity and quality.
Understanding a supplier inside and out will only be a positive thing. If one supplier lets you down, you already have a list of suppliers you know well.
The Importance of the Supply Chain Audit
A supply chain audit should be performed every two years. The goal of the supply chain audit is to get an overview of the company’s supply chain systems and processes as well as the supply chain organization. It can also provide more insight into supply chain risks.
Supply chain audits may require visiting vendors, warehouses, and factories. Auditors also need to be aware of any current affairs that may impact suppliers like trade agreements and economic trends. They need to fully understand the organization and the environment in which it operates.
For the stability of the supply chain, it’s absolutely essential to have a backup plan in place with B suppliers. Is your organization struggling with your supply chain management? POWERS can help. Reach out to us today to learn more.