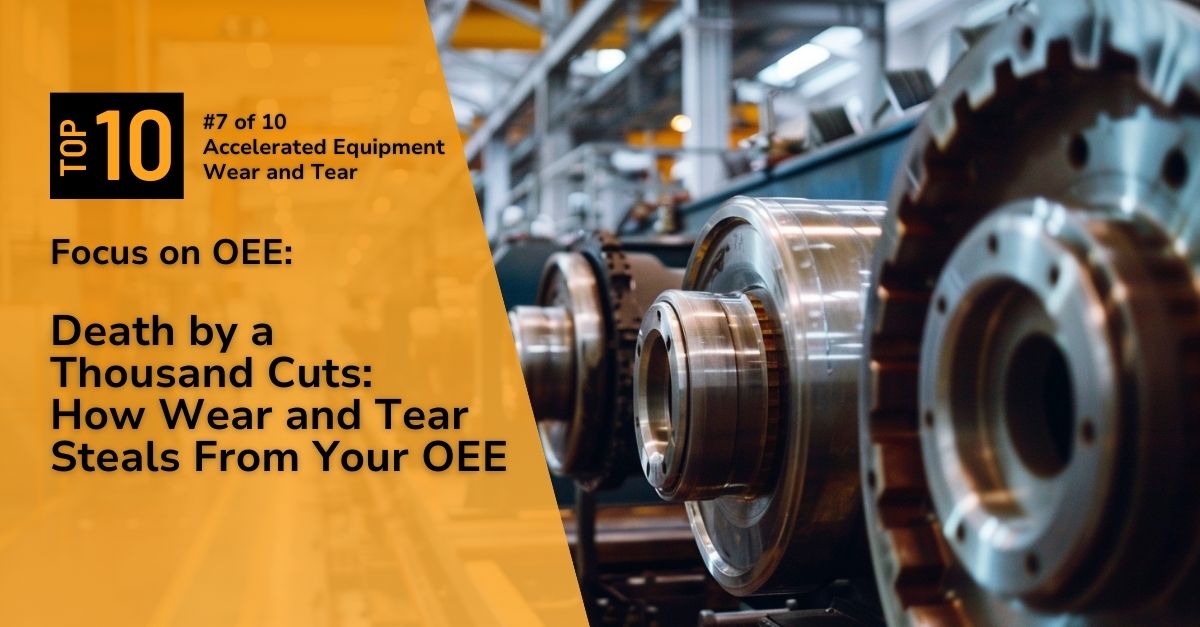
Solely relying on headline OEE numbers can leave you blind to hidden forces steadily eroding your productivity and profitability. Accelerated equipment wear and tear is one such force.
Think of it as the manufacturing equivalent of termites—unseen, seemingly minor damage accumulates until the very foundation of your operations is at risk.
Imagine a packaging line where inconsistent sealing temperatures become the norm. Operators tweak settings constantly, waste rises, and throughput slows. Initial gut feelings may point to “operator error” or general “equipment unreliability.” But, if the heater element is wearing out, no amount of adjustments will fix the underlying cause. Without OEE analysis tied to equipment condition, you’re simply fighting symptoms, and the problem will worsen.
In this Focus on OEE Mastery Series segment, we won’t just list how wear damages your bottom line. We’ll dive deep into the secondary symptoms – the subtle changes in machine behavior, those annoying yet persistent problems that operators learn to ‘live with.’ These are the signs your equipment is crying for help, and they directly impact your OEE score in ways that might surprise you.
1Increased Frequency of Preventative Maintenance:
Worn components demand more frequent PM cycles to keep production running, creating hidden labor and material costs. This labor diversion also affects OEE availability. Beyond the obvious inconvenience, this approach masks deeper problems and doesn’t stop accelerated wear.
Mitigation: Implement condition-based monitoring using sensors and predictive analytics to optimize PM scheduling. This helps prevent breakdowns while avoiding unnecessary interventions, freeing up resources for proactive, wear-reducing actions.
2Cascading Failures:
A worn component stresses others around it, causing a failure domino effect with major OEE damage. A loose fan belt might cause a pump to overheat, damaging its seal leading to a breakdown. Each downtime episode hurts OEE, and the root cause of the initial wear problem might be missed.
Mitigation: Treat every breakdown as a root cause analysis opportunity. Seemingly complex problems are often linked back to a simple worn component. This investigative approach prevents future stoppages.
3Troubleshooting Complexity:
Worn equipment doesn’t behave predictably, making problems harder to find. A stamping press with a worn hydraulic cylinder might act erratically, leading to hours of chasing phantom issues before the source is uncovered, destroying OEE availability.
Mitigation: Train technicians on wear-related failure patterns specific to your equipment. Invest in diagnostic tools like thermal cameras or vibration sensors. Targeted diagnostics save time compared to generalized troubleshooting.
4Tolerance Creep:
As wear takes hold, precision is lost. Worn machine tools introduce variability; conveyor systems slip and surge. This inconsistency hurts throughput (OEE performance) and leads to quality problems (OEE quality), resulting in scrap and rework.
Mitigation: Institute more frequent quality checks, but this is a short-term measure. Develop a predictive maintenance program to catch the underlying wear before tolerances become unacceptable. Learn how 7 Steps to Amp Up Manufacturing Maintenance Performance to Boost Productivity and Profitability
5Inconsistent Cycle Times:
Worn machines lose their rhythm, introducing unpredictable variations into cycle times. This hurts throughput and overall OEE performance. Worn bearings, gears, or other moving parts often lead to inconsistent speeds, hesitations, and unexpected stops.
Mitigation: Monitor cycle times closely. Use statistical process control to spot trends before they become serious. Vibration analysis or other condition monitoring can pinpoint trouble areas before performance degrades fully, saving time and finished parts.
6Lubricant Consumption:
Worn seals, loose clearances, and other issues often cause excessive lubricant use. Not only is this a direct cost hit, but improper lubrication itself accelerates wear, creating a vicious cycle that further damages OEE.
Mitigation: Track lubricant use per machine. Set alerts for unusual increases. Implement oil analysis to reveal excessive metal particles, indicating internal wear problems early on.
7Increased Warranty Claims:
If your products are failing prematurely due to internal components manufactured on worn equipment, your warranty costs can spiral out of control. Each claim diverts resources away from productive activities, undermining your OEE.
Mitigation: Analyze warranty data carefully. If failure patterns point to issues with machine wear affecting component quality, implement upstream corrections and stricter quality checks on your production line.
8Vibration and Noise:
Excessive vibration and noise are classic signs of wear, damaging both the machine and the working environment. Beyond OEE availability concerns (safety stoppages), vibration itself accelerates wear on other machine components.
Mitigation: Utilize vibration monitoring tools for early detection. Don’t wait for audible problems – address vibration trends proactively for a quieter, safer, and more productive shop floor.
9Operator Morale:
Worn equipment is frustrating to work with. Operators face inconsistent outputs and constant adjustments and may feel powerless to improve situations. This leads to lower productivity (OEE performance) and even resignation to problems as ‘normal’.
Mitigation: Involve operators in troubleshooting and root cause analysis. Empower them with simple diagnostic tools or checklists to report problems early. Celebrating fixes, even small ones, builds morale and keeps everyone engaged in fighting wear and tear.
10Contamination:
Components generate fine particles or introduce lubricant leaks into a system as they wear. In sensitive processes (like food or semiconductor manufacturing), this can be catastrophic for quality, drastically hurting OEE.
Mitigation: Upgrade filtration systems if contamination risks are high. Oil analysis (checking for particles) can be a leading indicator of contamination issues. Ensure maintenance procedures emphasize cleanliness to prevent outside contamination during repairs.
Conclusion for Senior Operations Leaders:
Don’t Let Wear Dictate Your OEE
The secondary symptoms of accelerated wear and tear relentlessly chip away at your OEE, causing problems that seem disconnected from the root cause. This hidden cost is entirely preventable. You can break this destructive cycle by establishing a proactive maintenance strategy, investing in condition monitoring technologies, and empowering your team to identify the early signs of wear.
POWERS: Your Partner in Transforming Equipment Health
At POWERS, we go beyond reactive maintenance and equipment repair. Our unique AMP (Advanced Maintenance Performance) Program is designed to achieve long-term OEE excellence. This comprehensive approach includes:
- In-depth OEE Analysis: Uncovering hidden wear patterns affecting your efficiency.
- Customized Maintenance Strategies: Tailored plans that combine predictive, preventative, and precision techniques to protect your equipment investment.
- Skills Development: Empowering your team with the knowledge to be your first line of defense in maintaining peak equipment performance.
- Ongoing Support: Ensuring your OEE improvement initiatives are sustainable and successful.
Take control of your manufacturing future. Optimize your processes and achieve unprecedented efficiency. Contact POWERS today to learn how our AMP Program can drive your company’s success. Let’s start the conversation:
- Speak to an Expert: Call +1 678-971-4711 to discuss your specific challenges and goals.
- Email Us: Get tailored insights by emailing info@thepowerscompany.com
- Request an Assessment: Use our online contact form to schedule an in-depth analysis of your operations.
Don’t wait – unlock your hidden manufacturing potential today!
Continue Reading from this Mastery Series
- Part 1 – The Hidden Costs Undermining Your OEE Score
- Part 2 - Dig Deep to Eliminate Inefficiencies that Silently Sabotage Your OEE
- Part 3 – How Guesswork Kills OEE
- Part 4 – When Nobody Takes Ownership OEE Suffers
- Part 5 – When “Pushing Production” Costs You OEE Points
- Part 6 – The Customer Connection: When Dissatisfaction Drains Your OEE
- Part 7 – Death by a Thousand Cuts: How Wear and Tear Steals From Your OEE
- Part 8 – Competitive Disadvantage: The Hidden Enemy of OEE Excellence
- Part 9 – How Missed Opportunities for Improvement Means Missed OEE Potential
- Part 10 – Is Stagnant Innovation Stagnating Your OEE Results