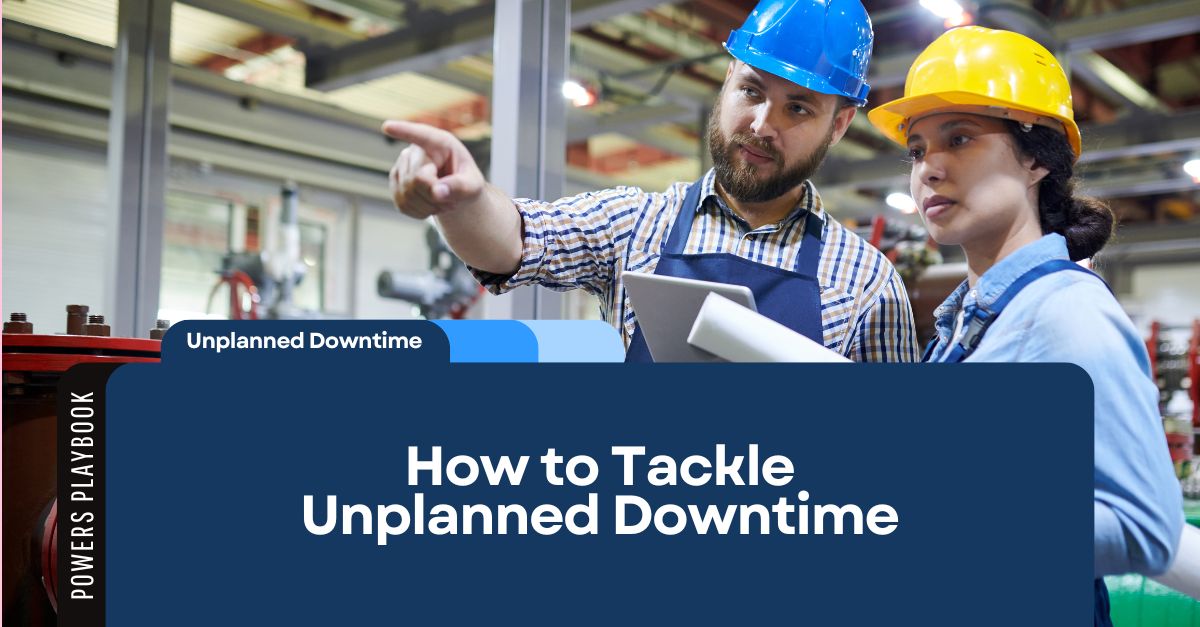
Understanding Unplanned Downtime
Unplanned downtime threatens the long-term success and sustainability of every manufacturing operation. These unforeseen production stoppages can arise from equipment failures, operational inefficiencies, supply chain disruptions, or other hidden issues. Unlike scheduled maintenance, these interruptions occur without warning, disrupting workflows and derailing production targets. Addressing unplanned downtime is crucial, as it poses significant financial and operational challenges.
The Hidden Costs of Unplanned Downtime
The financial impact of unplanned downtime is substantial. A recent industry study reveals that such disruptions can cost manufacturers up to $260,000 per hour, encompassing lost production, labor expenses, and repair costs. Beyond these direct financial losses, unplanned downtime has ripple effects on several aspects of operations. Productivity takes a major hit as idle machinery, and workers mean missed production goals.
Frequent stoppages also accelerate wear and tear on equipment, shortening its lifespan and increasing maintenance costs.
On a human level, constant disruptions can erode employee morale, creating frustration and reducing confidence in the systems they rely on. These challenges extend to customers, too, as delayed deliveries can harm client relationships and damage the company’s reputation.
Getting to the Bottom of the Problem
Mitigating unplanned downtime begins with understanding why it’s happening. Equipment failures are one of the most common culprits, often resulting from inadequate maintenance or aging machinery. Without predictive analytics, breakdowns can seem sudden and unavoidable.
Human error also plays a role, with insufficient training or unclear procedures leading to mistakes that disrupt production. Supply chain delays further exacerbate the problem, as late arrivals of raw materials or components create bottlenecks on the production floor. Quality control issues can also contribute, with defective products necessitating rework or scrapping and causing additional delays.
RCA: Effective Tools and Techniques
Root Cause Analysis (RCA) provides a structured and actionable approach to finding the culprits lurking behind unplanned downtime. Tools like the “5 Whys” and fishbone diagrams help teams systematically uncover the root causes of production disruptions.
For example, one manufacturer experiencing frequent conveyor belt failures applied RCA techniques and discovered that misalignment was the primary issue. Once identified, they implemented corrective measures such as realigning components and introducing regular alignment checks. These adjustments reduced downtime by over 30%, demonstrating how targeted actions, driven by thorough analysis, can deliver measurable results and long-term operational benefits.
Strategies to Mitigate Unplanned Downtime
Reducing unplanned downtime requires a proactive approach integrating technology, workforce development, and strategic planning. Preventive maintenance is a cornerstone of this strategy. Regular inspections and servicing can help detect potential issues before they escalate into breakdowns, extending equipment life and enhancing reliability. Predictive maintenance tools take this a step further by leveraging advanced analytics and sensors to forecast failures and schedule maintenance precisely when needed.
Workforce training is equally critical. Skilled operators and technicians can address minor issues before they escalate, ensuring that problems are resolved quickly and efficiently.
Comprehensive training programs also equip employees with the knowledge to diagnose and prevent recurring issues.
Streamlining supply chain operations is another essential step. Building strong relationships with suppliers and maintaining buffer inventories can help minimize delays that disrupt production.
Real-time monitoring systems, such as DPS, provide managers with live data on equipment performance, enabling swift and informed decision-making to prevent potential downtime.
Monitoring and Measuring Downtime
Effective downtime management hinges on comprehensive data collection and analysis. Key performance indicators (KPIs) such as capacity utilization, first-pass yield, and mean time between failures (MTBF) are essential for identifying trends and pinpointing improvement areas.
Tools like the DPS Startup Scorecard provide valuable insights into shift readiness and production performance, allowing manufacturers to assess and enhance their processes in real-time. Historical data analysis further supports strategic planning by highlighting recurring issues and helping teams anticipate future challenges.
By integrating these monitoring tools into daily operations, manufacturers can proactively manage downtime, minimize disruptions, and maximize operational efficiency.
The Long-Term Benefits of Proactive Management
Addressing unplanned downtime delivers a range of measurable benefits that extend beyond immediate cost savings. Reliable equipment and streamlined workflows ensure consistent production, boosting overall productivity. Proactive maintenance strategies not only lower repair costs but also reduce the financial losses associated with unexpected disruptions.
A stable and efficient work environment also fosters employee confidence and morale, contributing to a more engaged and motivated workforce. These internal improvements translate to external benefits, including stronger customer relationships built on timely deliveries and enhanced trust.
Conclusion: Comprehensive Solutions with POWERS and DPS
Unplanned downtime is a formidable challenge, but it can be effectively addressed through our dual approach. POWERS specializes in aligning people, processes, and performance, offering expertise in frontline leadership development and production optimization to drive immediate and sustainable improvements.
Complementing this, DPS our Digital Production System provides real-time insights, predictive analytics, and powerful tools to monitor and address downtime proactively.
POWERS and DPS offer a comprehensive solution that bridges human expertise with technological innovation. POWERS empowers leadership and workforce teams with the skills and strategies to excel, while DPS delivers the data-driven insights needed to keep operations running smoothly.
For deeper insights into mitigating unplanned downtime, explore the POWERS Mastery Series on Unplanned Downtime and learn how these strategies can transform your operations.
Discover how POWERS and DPS can help your organization achieve better planning, better decisions, and better outcomes—every shift. Visit thepowerscompany.com and powersdps.com to learn more.
- Speak to an Expert: Call +1 678-971-4711 to discuss your specific challenges and goals.
- Email Us: Get tailored insights by emailing info@thepowerscompany.com
- Request an Assessment: Use our online contact form, and one of our expert manufacturing consultants will reach out to schedule an in-depth analysis of your operations.