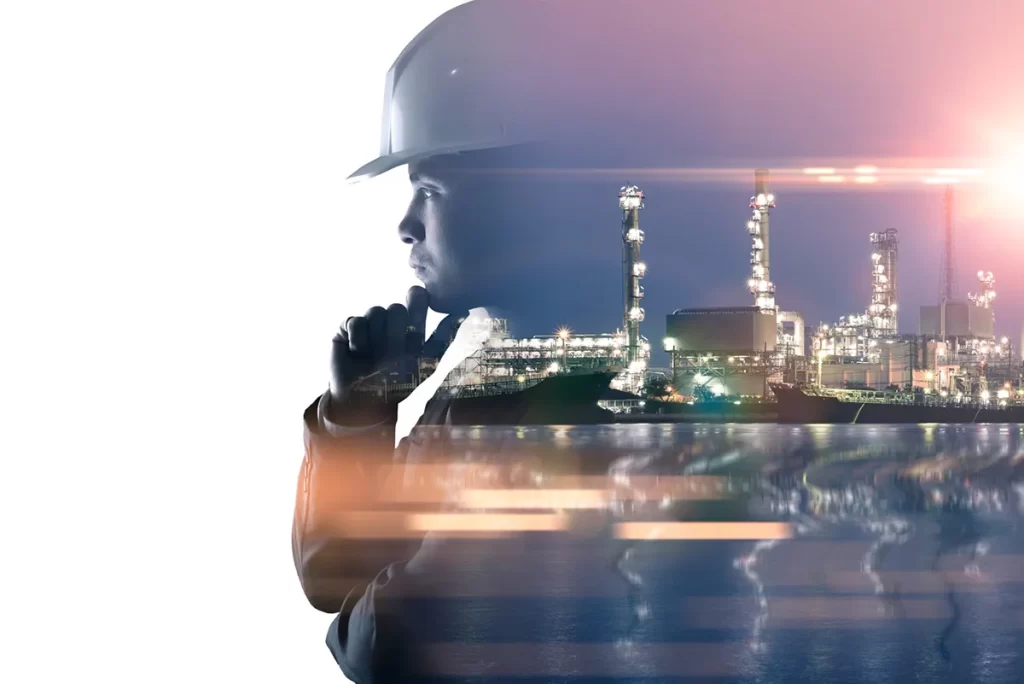
With unemployment numbers still through the roof due to economic disruption, and manufacturers struggling to keep up with diminished capacity and increased demand for products during COVID-19, it’s more important than ever to keep up with the latest trends to stay competitive. This need for professional development (and openness/curiosity about changes in the industry) comes into play most crucially when it comes to tech and innovation.
In April, Industry Week reported some fairly sobering data collected by the National Skills Coalition, which showed just how big the tech gap has gotten within the manufacturing labor force. According to their findings, “16% of currently employed American manufacturing workers have no digital skills, and an additional 19% have very limited skills.”
As the Industry Week piece states: “Workers must be able to use tools such as 3D printers on the shop floor, monitor and interpret data from sensors throughout a manufacturing facility, and even use ‘wearable tech’ to receive in-the-moment training through virtual reality.”
The staggering facts don’t end there.
According to tech blogger Laurence Bradford, “between 2016 and mid-2019, U.S. employers were only able to fill six of every 10 open tech positions, signaling a huge technology talent deficit in the U.S.”
“Furthermore,” Bradford writes, “over 50% of company learning & development leaders in a Udemy survey said technical skills were their top priority for training in 2020.”
The lackluster reaction from leaders in the face of flagging tech capabilities on their teams is especially surprising in the face of continued ramped up safety measures during the pandemic. The continuing economic disruptions we’re facing rely on companies thinking on their feet and coming up with fresh, new ways of getting things done efficiently.
Back in January, manufacturers were reportedly already talking about making major investments in “upskilling” their workers. Because of safety concerns and the rapidly shifting realities of an increasingly volatile job market, the full embrace of technology appears to be on a faster track, as is the demand for hires with a particular set of skills.
As American Machinist reported, industry experts predicted that rapid “adoption of lots of new technologies could be the way that companies can both protect their employees while continuing to produce and adhere to their new processes.”
Not only that, but without developing these new and expanding skills, you may be missing out on some significant career advancement opportunities, as some have projected that over the next decade, millions of jobs may go unfilled due to “lack of adequately trained labor.”
Here are 6 cutting-edge emerging technologies in manufacturing that you and your team may want to have at least an awareness or working knowledge of, as we move forward through the rest of 2020.
1. Artificial Intelligence (A.I.) and Machine Learning
Why? McKinsey reports that up to half of the businesses that decide to incorporate A.I. into their work processes over the next several years “have the potential to double their cash flow,” according to Forbes.
For a closer look at A.I., its exciting potential, and the increasingly integral role it plays in manufacturing, be sure to check out our blog post from earlier this year, which is entirely devoted to the fascinating topic.
2. Data Science and Analytics
Data analytics is a booming business in its own right, predicted to surpass $19 billion in sales by 2026, according to one estimate in May published by Industry Week. Many would argue that investment is worth every penny since the smart use of analytics has dramatically increased profit margins in a wide variety of cases.
As McKinsey argued in 2017, when companies harness their own data and apply advanced analytics to understand that data, it can “help manufacturers solve previously impenetrable problems and reveal those that they never knew about, such as hidden bottlenecks or unprofitable production lines.”
Not sure where to start deepening your knowledge about this area? Coursera offers some great classes online, like this one in Big Data Specialization.
3. Cybersecurity, or “Business Risk Management”
Outdated cybersecurity protocols present a real and potent threat to the soundness of businesses that haven’t done enough to combat increasingly tricky hacks, viruses, and other dangers of the digital age. This means that knowing how to help companies craft a plan on how to prevent cyber attacks, or at least combat them when they occur, has become an even more marketable skill in 2020.
If this piques your interest, you should be aware that many online learning options will get you started on the immersion track right away. One great offering among these is edX, which has an excellent certificate program that teaches all the essentials around cybersecurity.
4. Cloud Technology & Data Engineering
There’s nothing quite like a global crisis to demonstrate just how lost we’d be without the cloud as part of daily operations. As Emil Sayegh, President and CEO of Ntirety, recently argued in Forbes, the cloud has been businesses’ saving grace during the COVID-19 pandemic — across all industries.
Were it not for cloud technology, “it would be more challenging for executives to access real-time business sales information for their companies from anywhere in the world,” Sayegh wrote. “Companies would also have a harder time sharing and co-editing documents securely, with colleagues across the ocean – and even in their city. Even short physical distances would present a challenge for collaboration between coworkers without the cloud.”
Want to start digging in? The big ones are still Microsoft Azure, Amazon Web Services, and Google Big Query. Start with those and go from there.
5. Robotics
The concept of working alongside machines is no longer a hypothetical one, as this one-time futuristic vision has become a tangible reality for many in recent years. But take it easy on your robot coworkers — they’re here to help.
As CEO of Fetch Robotics Melonee Wise told Fast Company, “robots today are taking tasks, not jobs.” Often, the tasks the robots are assuming are the repetitive, monotonous ones that would otherwise detract from your ability to use critical thinking skills and perform other more complex work.
So, it’s a great benefit and one that would be wise to embrace, as COVID-19 has only accelerated the addition of automation into the flow of work.
6. Virtual Reality (V.R.)
Like Robotics and A.I., the concept of virtual reality may have once seemed like the domain of science fiction, but it is becoming ever-more incorporated into routine company practices. Particularly in industries that POWERS works with a lot, like food and beverage.
Even before COVID-19 hit, many companies were beginning to realize how much V.R. can help “eliminate errors in food processes,” “ease the learning curve in food preparation,” increase worker and customer safety, increase efficiency, and more.
This technology has also gained traction in healthcare, for instance, in treating extreme phobias or anxiety or helping doctors diagnose visual or cognitive impairments.
—
At the end of the day, what we’re looking at is a future of manufacturing that will be more optimized for productivity than we’ve ever experienced, and so we all want to make sure that we don’t get left behind.
Our team of experts at POWERS is always looking for new ways to help our clients achieve critical business performance improvements, transform operational culture, and improve your bottom line. Like what you’ve read? We’d love to hear from you — drop us a line or read more from our blog.