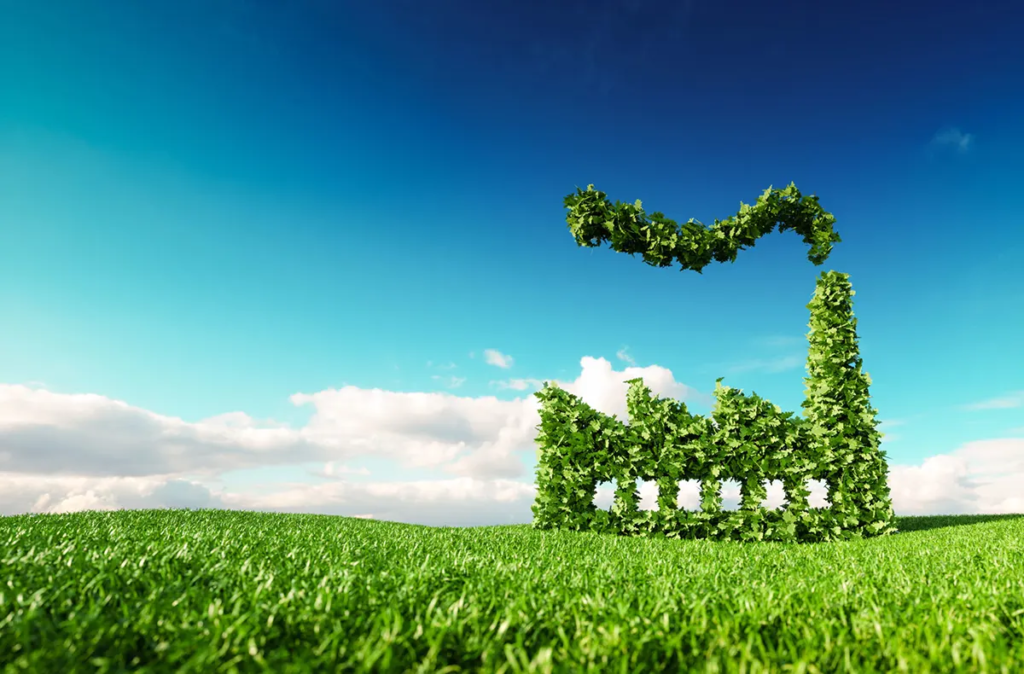
Consumers are becoming more aware of the environmental impact of their purchasing decisions. As a result, it’s affecting their choices. In response, manufacturers are making significant strides to lower their environmental impact through product lifecycle management, e-waste management, and implementing more sustainable manufacturing practices.
Sustainability has become an essential component of manufacturing practices in recent years. This is partly due to the increasing eco-consciousness of consumers, who are now more aware of the impact their purchasing decisions have on the environment. In response, businesses are making concerted efforts to reduce their carbon footprint and implement more sustainable manufacturing practices. Let’s explore five areas where manufacturers can achieve more sustainable practices while keeping their businesses profitable.
Evaluate and Optimize Your Use of Fossil Fuels
The industrial sector is a major contributor to global energy-related CO2 emissions, accounting for about 37%. By switching to renewable energy sources such as solar, wind, and hydro power, manufacturers can significantly reduce their carbon footprint and contribute to the transition to a low-carbon economy. In addition to reducing emissions, renewable energy sources can also provide cost savings over the long term through lower energy bills and reduced exposure to volatile fossil fuel prices. There are several ways that manufacturers can optimize their use of energy and reduce their reliance on fossil fuels. These include:
1Conducting energy audits
2Investing in energy-efficient technology
3Implementing energy management systems
4Switching to renewable energy sources
5Implementing energy-saving practices
Decrease Pollution
Decreasing pollution is an essential step in achieving more sustainable manufacturing practices. More countries around the world are seeing the importance of decreased environmental waste and pollution. By implementing pollution prevention practices, product lifecycle management, e-waste management, using eco-friendly materials, implementing pollution control measures, implementing a pollution monitoring program, and partnering with regulatory agencies, manufacturers can reduce their environmental impact, promote compliance with environmental regulations, and meet the growing demand from eco-conscious consumers for sustainable products.
There are several ways that manufacturers can decrease pollution:
1Implement pollution prevention practices
2Use eco-friendly materials
3Implement pollution control measures
4Implement a pollution monitoring program
5Partner with regulatory agencies
Engage in Time-Saving Practices
Engaging in time-saving practices is an important step in achieving more sustainable manufacturing practices. By optimizing production processes and implementing lean manufacturing principles, manufacturers can reduce their operating costs by up to 20%. By implementing lean manufacturing principles, using technology to optimize processes, implementing a continuous improvement program, implementing standard operating procedures, and partnering with suppliers, manufacturers can reduce the time required to complete manufacturing processes, improve efficiency, and meet the growing demand from eco-conscious consumers for sustainable products.
There are several ways that manufacturers can engage in time-saving practices:
1Implement lean manufacturing principles
Lean manufacturing principles focus on reducing waste and increasing efficiency throughout the production process. This can include implementing just-in-time manufacturing practices, reducing inventory, and optimizing production processes to minimize waste.
2Use technology to optimize processes
Technology can be used to optimize processes and improve efficiency. This can include using sensors and monitoring systems to optimize energy consumption, implementing real-time data analysis to identify areas where efficiency can be improved, and using automation to streamline production processes.
3Implement a continuous improvement program
A continuous improvement program can help manufacturers identify areas where efficiency can be improved and implement changes to improve performance over time. This can include conducting regular assessments of manufacturing processes, implementing training programs to improve employee skills, and using feedback from customers and suppliers to identify opportunities for improvement.
4Implement standard operating procedures
5Partner with suppliers
Adopting a comprehensive Management Operating System (MOS), or increasing compliance and proficiency with an existing MOS, is fundamental to achieving these goals. Read our Enhancing Manufacturing Efficiency Mastery Series to learn more
Recycle
Recycling is an important step in achieving more sustainable manufacturing practices. About 30% of plastic packaging is never reused. By using recycled materials, implementing closed-loop manufacturing processes, implementing a waste management system, partnering with suppliers, and educating employees, manufacturers can reduce their reliance on virgin materials, lower their production costs, and reduce their environmental impact. This helps meet the growing demand from eco-conscious consumers for sustainable products and benefits the bottom line of manufacturers.
There are several ways that manufacturers can incorporate recycling into their operations:
1Use recycled materials
By using recycled materials in their products, manufacturers can reduce their reliance on virgin materials and lower their carbon footprint. This can include using recycled paper, plastics, and metals in packaging materials, as well as using recycled raw materials in the production process.
2Implement closed-loop manufacturing
Closed-loop manufacturing (or the ‘circular economy’ as it is now better known) involves designing products and production processes so that materials can be easily recycled or reused. This can include designing products for disassembly, using recyclable materials, and implementing closed-loop recycling processes.
3Implement a waste management system
4Partner with suppliers
Manufacturers can partner with suppliers to promote recycling and reduce waste. This can include working with suppliers to use recycled materials, as well as implementing closed-loop supply chain processes.
5Educate employees
Reduce Waste Production
Reducing waste production is an important step in achieving more sustainable manufacturing practices. Currently, approximately 300 million tons of plastic waste is produced every year. By implementing a waste reduction program, designing products for sustainability, implementing lean manufacturing principles, using technology to optimize processes, product lifecycle management, e-waste management, and partnering with suppliers, manufacturers can reduce waste, conserve resources, and minimize their environmental impact. This helps meet the growing demand from eco-conscious consumers for sustainable products and benefits the bottom line of manufacturers.
There are several ways that manufacturers can reduce waste production:
1Implement a waste reduction program
2Design products for sustainability
3Implement lean manufacturing principles
4Use technology to optimize processes
5Partner with suppliers
To optimize production and profitability, businesses must prioritize equipment maintenance, production scheduling, and workforce training. Read our Untapped Potential Mastery Series to learn more.
Conclusion
The increasing eco-consciousness of consumers is driving manufacturers to adopt more sustainable practices. By evaluating and optimizing their use of fossil fuels, reducing pollution, engaging in time-saving practices, recycling, and reducing waste production, businesses can improve their bottom line while also reducing their environmental impact. Implementing sustainable manufacturing practices is not only good for the environment, but it also helps to improve brand reputation and attract eco-conscious consumers. By making sustainability a priority, businesses can stay competitive in an increasingly environmentally aware market.
At POWERS, one of the ways we help organizations to be more efficient is by helping reduce the resources, time, and energy that it takes to produce a finished product. Not only is this helpful in terms of sustainability, but it can greatly cut costs as well, making it a win-win scenario.
The POWERS Difference.
POWERS management consulting’s unique Culture Performance Management™ methodology connects the dots between optimized company culture and your desired operational performance outcomes.
POWERS has helped global leaders across many industries operationalize their culture for rapid and sustained performance improvement, increased competitive advantage, greater value, and a stronger bottom line.
To put our experienced team and proven track record to work for you, schedule an initial discovery and analysis by calling +1 678-971-4711, or emailing us at info@thepowerscompany.com
Continue Reading from other Mastery Series
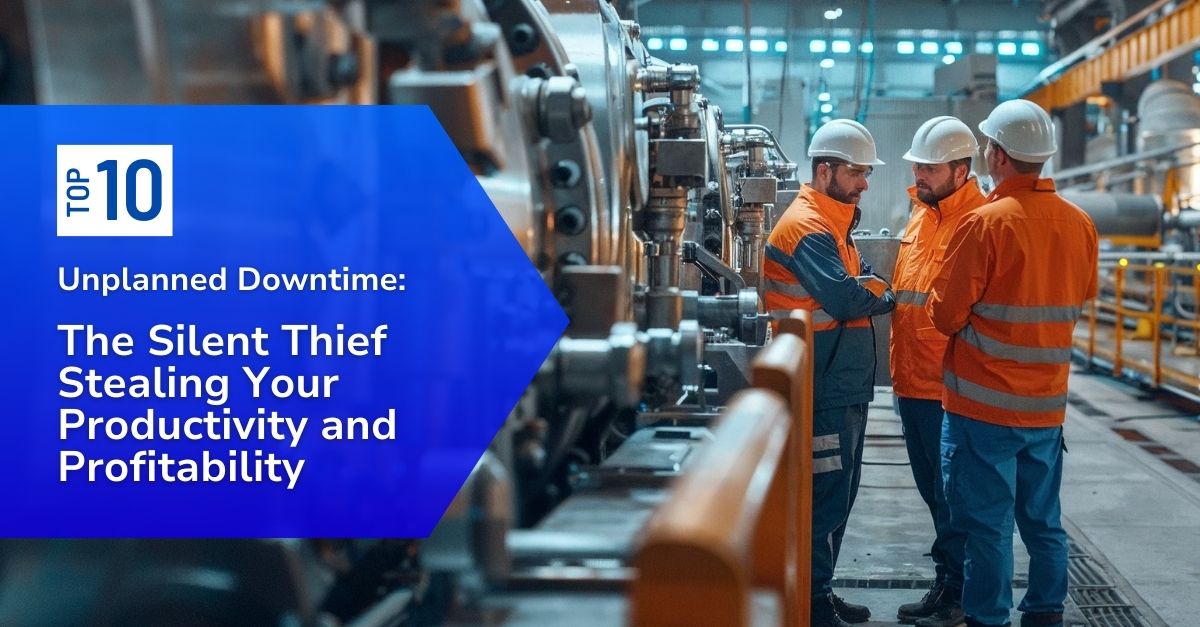
Unplanned Downtime: The Silent Thief Stealing Your Productivity and Profitability
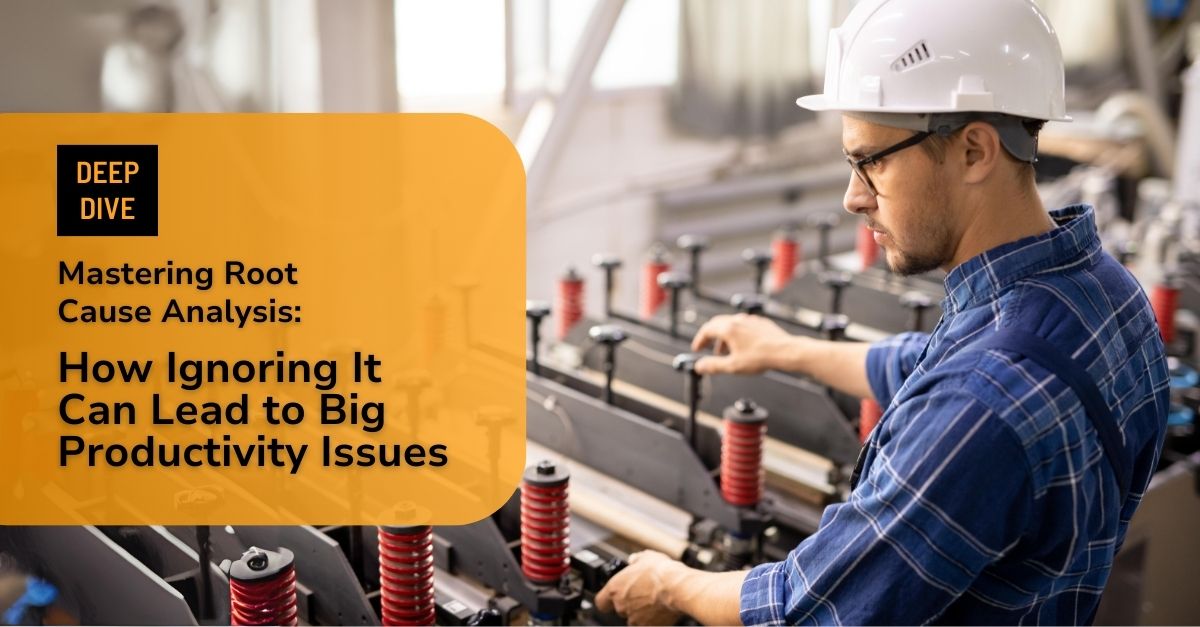
Mastering Root Cause Analysis: How Ignoring It Can Lead to Big Productivity Issues
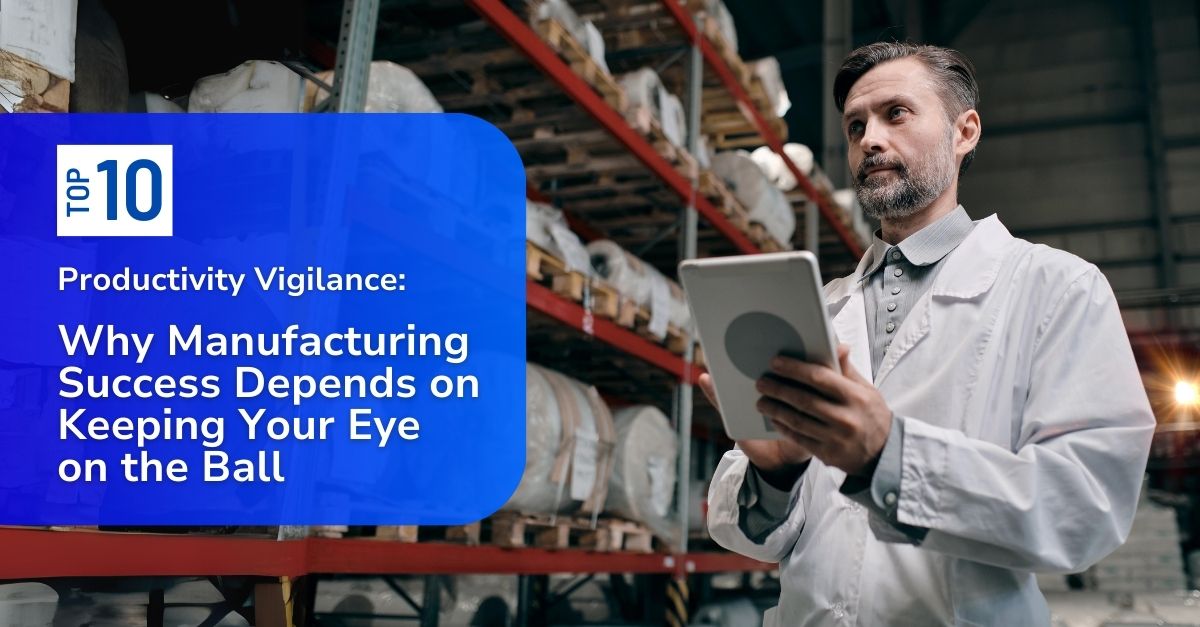
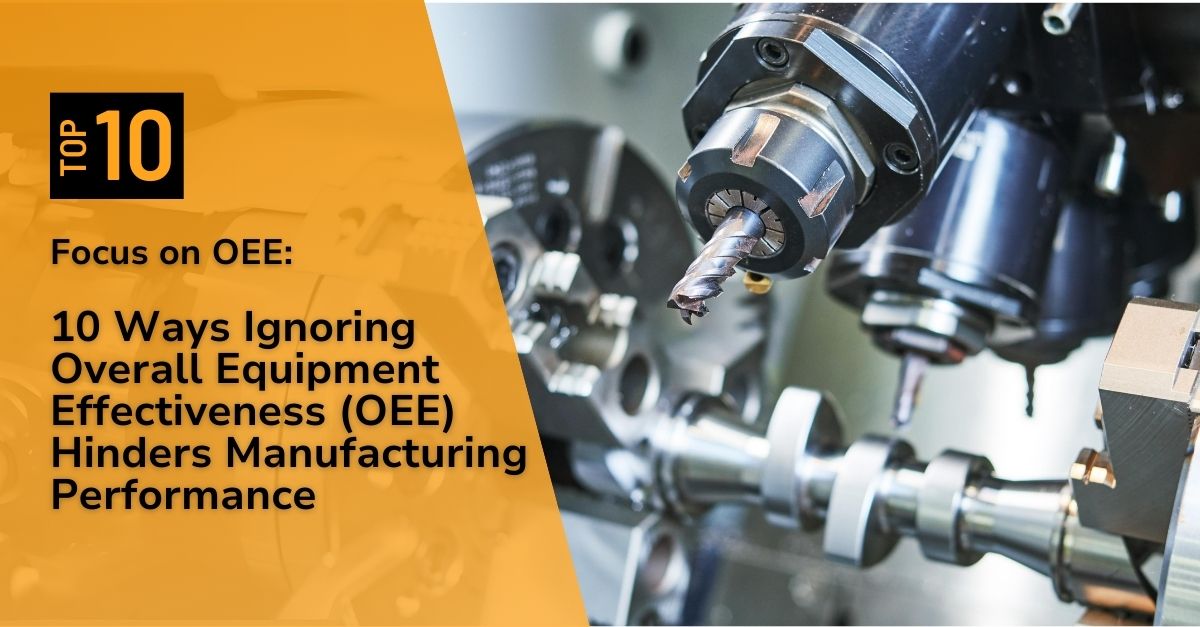
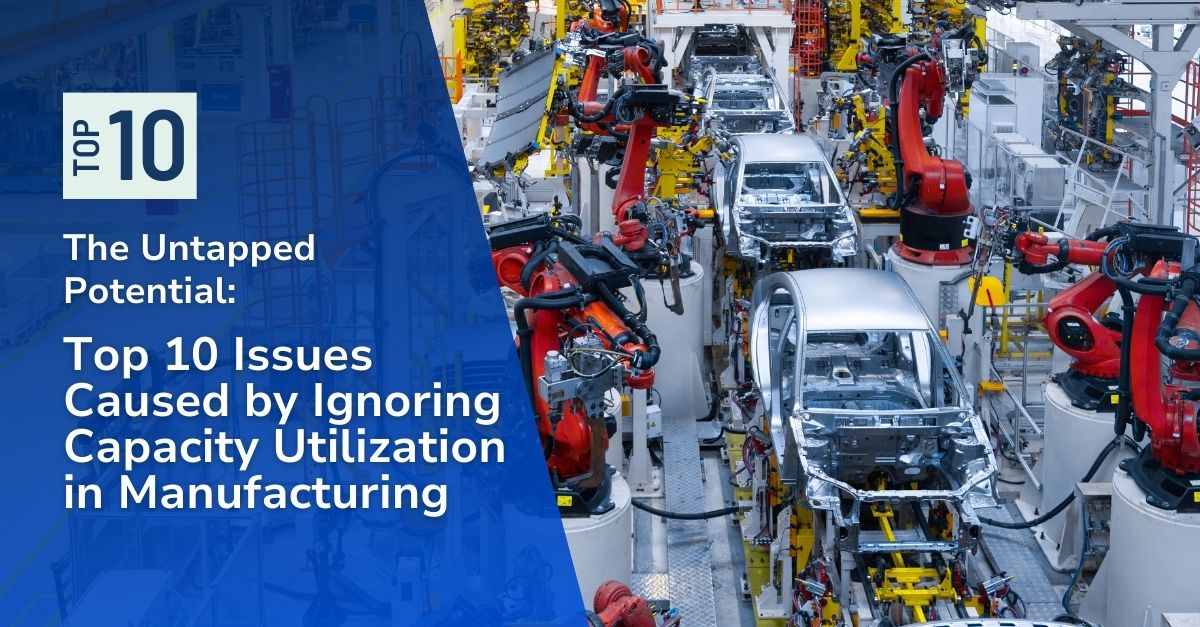
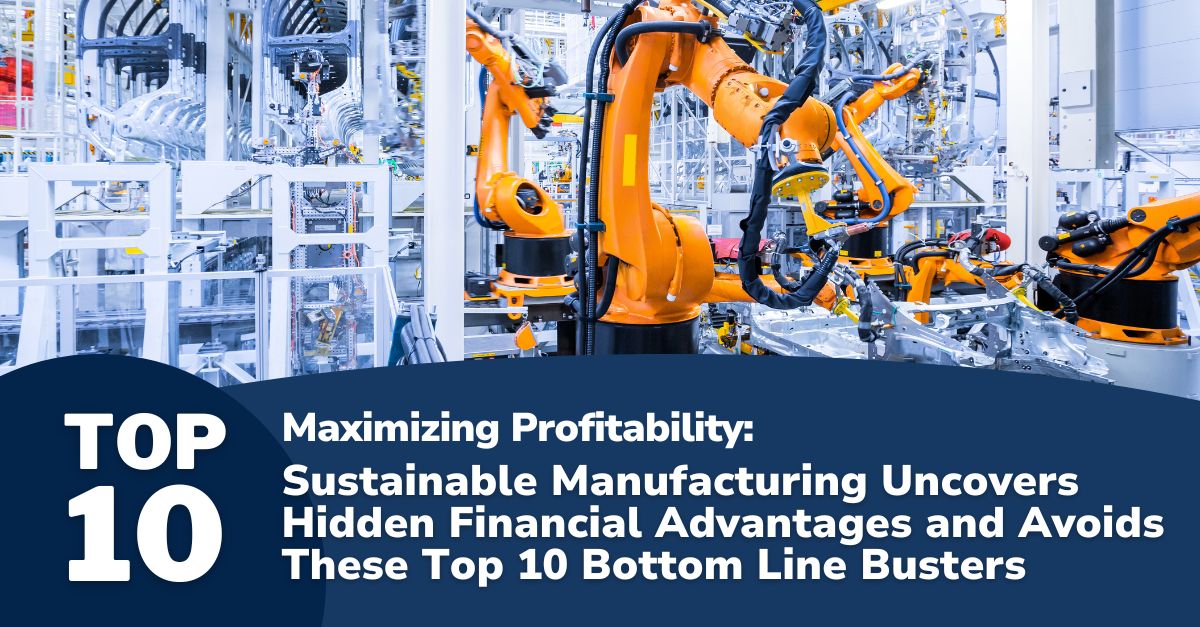