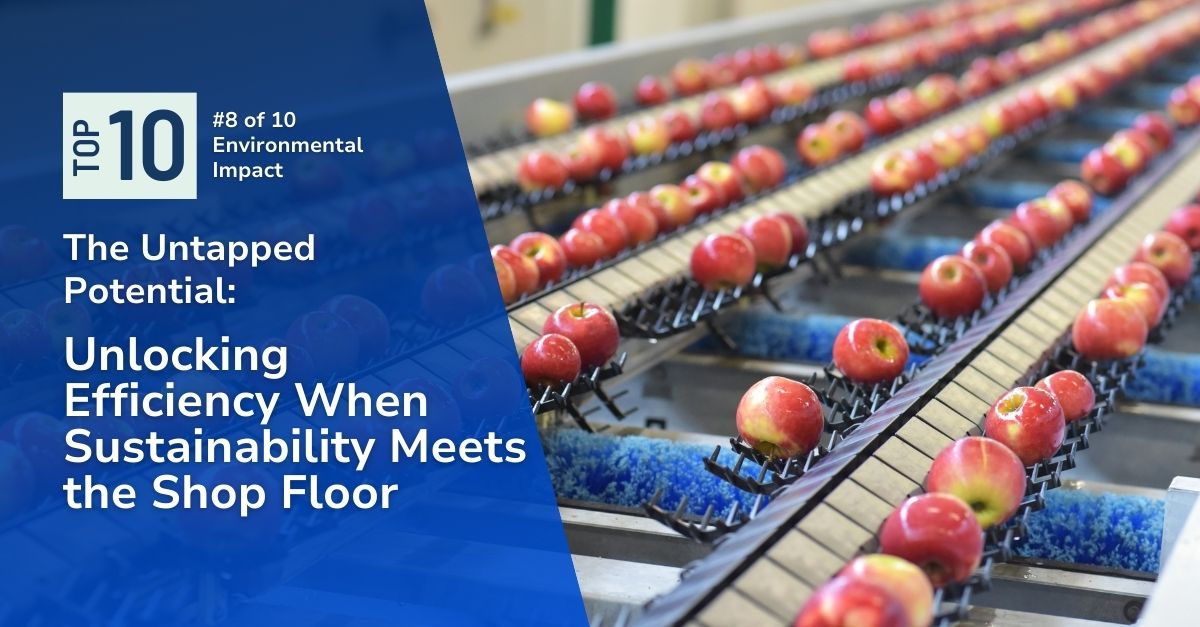
For today’s manufacturers, environmental responsibility isn’t just about ticking a box or burnishing your brand image; it’s a strategic imperative that goes hand-in-hand with maximizing your facility’s output.
While reducing environmental impact is undoubtedly a noble goal, the operational reverberations can be surprisingly complex. Unforeseen obstacles emerge, from material compatibility and equipment limitations to shifting waste streams and inflexible long-term commitments.
These roadblocks aren’t simply about eco-consciousness; they strike at the heart of capacity utilization.
When production lines stutter, costs escalate, and your ability to pivot is diminished, your entire manufacturing strategy begins to buckle. It’s no longer sufficient to view sustainability as a separate initiative;
to tap into the untapped potential lurking within your factory, you must confront environmental decisions’ subtle yet far-reaching impact on your day-to-day operations.
This analysis goes beyond abstract concepts. We’ll delve into the granular, real-world challenges manufacturing managers face as you navigate this complex landscape. Let’s explore the top ten issues where environmental impact clashes with operational efficiency:
1Performance Trade-offs with Sustainable Materials:
Negative Impact: Switching to recycled, bio-based, or lower-impact materials frequently entails trade-offs in their properties. This could manifest as reduced strength, altered durability, or inconsistent performance, ultimately disrupting production and product quality.
Positive Step: Close collaboration with material suppliers, extensive testing, and a phased implementation of new materials can mitigate these risks. Re-engineering products to optimize for sustainable materials is also key.
2Unexpected Process Changes:
Negative Impact: Eco-friendly initiatives often demand modifications to existing manufacturing processes. Changes such as altered temperatures, pressures, or chemical treatments, might lead to unpredictable issues with product tolerances, scrap rates, and overall process stability.
Positive Step: Invest in thorough process simulation and pilot runs before full-scale implementation. Engage R&D and engineering teams early to foresee and prevent potential process disruptions.
3Equipment Compatibility Issues:
Negative Impact: Existing machinery designed for traditional materials or processes may not be directly compatible with sustainable alternatives or eco-friendly practices. This can result in reduced efficiency, equipment wear and tear, or even outright incompatibility.
Positive Step: Conduct equipment compatibility audits before major shifts. Invest in retrofits, upgrades, or targeted equipment replacements as needed. Factor in compatibility for future equipment purchases.
4Waste Stream Modifications:
Negative Impact: Shifting products and processes creates new waste streams. Existing disposal systems might not be suitable or cost-effective. This can cause disruptions to waste handling, increased disposal costs, and potential non-compliance with environmental regulations.
Positive Step: Take a holistic view of waste. Analyze new waste streams and identify reducing, reusing, and recycling opportunities. Negotiate with waste disposal providers or explore alternative waste-to-value solutions.
5Batch Size Limitations:
Negative Impact: Certain sustainable materials or eco-conscious processes might necessitate smaller batches due to material limitations, equipment constraints, or quality control concerns. This disrupts established production runs and introduces inefficiencies in scheduling.
Positive Step: Rethink production scheduling models to optimize for smaller batches of specialized ‘green’ product lines. Consider just-in-time, agile manufacturing principles.
6Unintentional Greenwashing:
Negative Impact: An over-eagerness to brandish ‘eco-credentials’ can lead to overstated claims, lack of transparency, and consumer skepticism. It’s easy to fall into the greenwashing trap, risking reputational damage and erosion of trust in the company and its products.
Positive Step: Rigorous third-party certifications and life-cycle analyses substantiate environmental claims. Transparency regarding the trade-offs and ongoing improvements fosters a credible, authentic sustainability journey.
7Balancing Costs of “Doing It Right”:
Negative Impact: Eco-friendly upgrades, material changes, and process certifications often carry a premium. The perceived high cost of ‘doing it right’ hinders internal buy-in and creates challenges when competing on price-sensitive markets.
Positive Step: Look at total cost of ownership. Account for long-term energy savings, reduced regulatory risk, and potential revenue from ‘green’ consumers. Position sustainability as a value driver rather than a pure cost center.
8Maintaining Energy Efficiency Focus:
Negative Impact: Large-scale sustainability projects can divert resources and attention from ongoing energy efficiency initiatives. These day-to-day efficiency gains are crucial, but often less glamorous, and may lose momentum.
Positive Step: Make energy efficiency a core value. Empower employees to find and implement energy-saving ideas. Track and share energy use data.
9Long-Term Financial Viability:
Negative Impact: Sustainable transformations can carry risk, particularly in uncertain markets. Concerns linger about the long-term return on investment and the ability to remain commercially viable while prioritizing the environment.
Positive Step: A roadmap that artificially separates sustainability from profitability is doomed to fail. Focus on solutions that generate both environmental gains AND quantifiable returns: reduced energy costs, new revenue streams from ‘green’ products, enhanced consumer appeal, etc.
10Inflexibility Due to Long-Term Commitments:
Negative Impact: Long-term contracts for sustainable materials, energy sources, or partnerships can lock manufacturers into specific technologies or practices. This might limit their ability to adapt as markets shift rapidly, new technologies emerge, or regulations evolve.
Positive Step: Maintain a future-focused approach. Regularly review contracts and commitments. Build in contingency plans or exit clauses when feasible. Cultivate a diverse supplier network to enhance flexibility.
Conclusion for Operations Leadership
Environmental impact concerns create a hidden chain reaction that drags down capacity utilization when not proactively addressed. This is a complex challenge with no simple solutions. However, recognizing these subtle yet destructive forces is the first step toward mitigating their impact. By tackling these ten issues head-on, manufacturers can position themselves to be environmentally responsible and achieve peak operational performance, maximizing their output and potential.
Furthermore, a proactive approach to environmental impact allows manufacturers to capitalize on new opportunities. Consumers are increasingly environmentally conscious, and companies with demonstrably sustainable practices are poised to gain a significant competitive edge. Additionally, proactive environmental strategies can help manufacturers avoid costly regulatory compliance issues down the line.
How POWERS Can Help
At POWERS, we understand the delicate balance between sustainability and capacity optimization. Our team of experts offers a unique combination of environmental impact knowledge and deep manufacturing expertise. We help you:
- Identify the hidden impact: We conduct comprehensive audits of your processes, pinpointing inefficiencies and bottlenecks stemming from environmental initiatives.
- Develop strategic roadmaps: We don't just point problems out; we create actionable plans that weave sustainability into your operational fabric, maximizing efficiency and minimizing disruption.
- Unlock your facility's potential: Our customized solutions focus on unleashing your machines, materials, and workforce to their fullest capacity while being mindful of your environmental footprint.
If managing environmental impact while maximizing capacity seems like an impossible task, contact POWERS. We’ll transform this struggle into a competitive advantage.
Don’t let these challenges hold your manufacturing operations back. Contact POWERS today to explore how our expertise in both sustainability and operational excellence can propel your company toward its full potential. Let’s start the conversation: +1 678-971-4711 or info@thepowerscompany.com.
Continue Reading from this Mastery Series
- Part 1 – The Price of Lost Revenue and Profit Resulting from Underutilized Capacity
- Part 2 – How Rising Production Costs Hide Your Factory’s True Potential
- Part 3 – Poorly Managing Resources is Stealing Your Profits
- Part 4 – Break the Quality Struggle Cycle to Fix This Shop Floor Frustration
- Part 5 – From Chaos to Capacity: How to Tame Turnover and Optimize Your Operations
- Part 6 – Manufacturing Nightmares: When Your Shop Floor Can’t Keep Up
- Part 7 – When Supply Chain Disruptions Reveal Your True Capacity
- Part 8 – Unlocking Efficiency When Sustainability Meets the Shop Floor
- Part 9 – Understaffed and Underperforming on the Shop Floor
- Part 10 – How Blind Spot Vulnerabilities Impact Your Shop Floor’s Efficiency