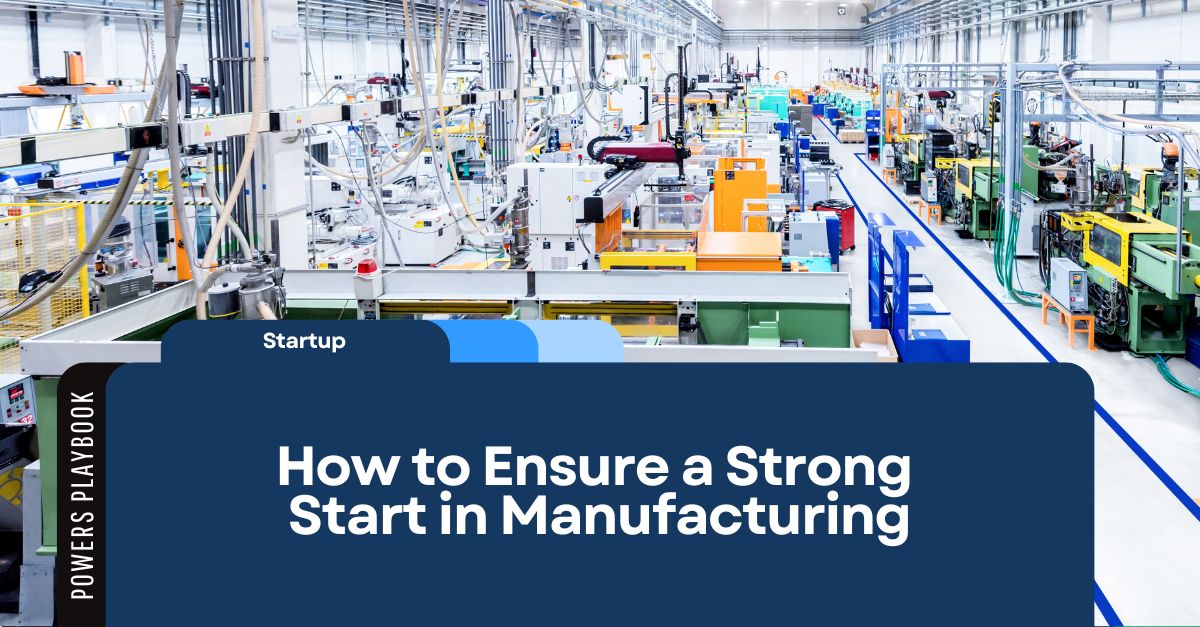
In manufacturing, the startup phase is where success begins—or costly problems are born.
Whether launching a new production line, restarting after planned downtime, or ramping up to meet a spike in demand, a successful startup sets the tone for operational efficiency, quality, and profitability. On the other hand, a poorly executed startup can lead to costly delays, wasted resources, and long-term damage to customer relationships.
According to a study, 23% of downtime events can be traced directly to poor equipment setup during startup phases. And with downtime costs averaging $260,000 per hour in automotive manufacturing alone, the stakes for getting it right couldn’t be higher.
What Defines a Good Startup?
A successful startup is built on three pillars: preparation, coordination, and execution. When these elements come together, you minimize risks and position your operation for peak performance. Let’s break it down:
1Set Clear Expectations:
- Comprehensive pre-startup inspections ensure that all machines and tools are calibrated, lubricated, and functioning as intended.
- Preventive maintenance schedules should align with startup activities to avoid equipment failure during production ramp-up.
2Processes Aligned:
- Production workflows should be reviewed and fine-tuned to eliminate bottlenecks.
- Quality control measures, such as in-line testing, must be active and accessible to catch defects early.
3People Set Up for Success:
- Employee training is key. Every team member should understand their role in the startup process and have the tools they need to execute.
- Cross-department communication ensures everyone, from operators to quality managers, is aligned on goals and expectations.
When these pieces are in place, your startup is functional and a launchpad for sustained efficiency and growth.
The High Stakes of a Poor Startup
The consequences of a mismanaged startup extend far beyond the initial phase. Without proper planning and execution, manufacturers can face:
- Extended Downtime: Startup errors can lead to cascading equipment failures or misaligned production processes that require time-consuming adjustments.
- Ballooning Costs: Errors during startup often result in wasted materials, emergency repairs, and additional labor expenses.
- Frustrated Employees: Teams forced to troubleshoot preventable issues during startup can quickly lose motivation and focus.
- Customer Dissatisfaction: Missing delivery deadlines or shipping subpar products damages your reputation and customer trust.
The costs add up quickly. Studies show that manufacturing companies spend 10-20% of their operating budget on quality-related costs, much of which stems from scrap, rework, and production delays during startup.³
Benefits of a Well-Executed Startup
A smooth startup offers benefits that ripple across your operation:
1Reduced Downtime
- By catching and addressing potential issues early, you minimize costly interruptions.
2Cost Savings
- Avoiding scrap and rework means fewer materials wasted and less labor required to fix mistakes.
3Enhanced Efficiency
- Production lines reach optimal output faster, helping you meet deadlines and maximize capacity.
4Stronger Team Confidence
- A well-prepared startup gives employees confidence in their roles, leading to better performance and morale.
5Improved Customer Relationships
- Delivering on time and with consistent quality reinforces trust and builds loyalty.
How to Get It Right
While every startup is unique, certain best practices apply universally. Here’s how you can set your operation up for success:
1Plan for Every Scenario:
- Use a detailed startup checklist to ensure equipment, processes, and people are ready.
- Conduct risk assessments to identify potential bottlenecks and plan contingencies.
2Train and Engage Your Team
- Provide hands-on training for all employees, focusing on the specific demands of the startup process.
- Encourage cross-functional collaboration to align goals across departments.
3Leverage Data and Technology
- Use real-time monitoring systems to track performance during startup. Early detection of issues can prevent larger problems.
- Analyze historical data from past startups to refine your approach and eliminate recurring issues.
4Conduct Post-Startup Reviews
- Schedule a follow-up assessment to identify what worked, what didn’t, and how to improve.
- Document these lessons for future startups to ensure continuous improvement.
Real-World Impact
Companies that prioritize strong startup practices consistently outperform those that don’t. For example, a Fortune 500 manufacturer reduced its startup time by 35% and cut material waste by 15% by implementing a detailed startup plan with robust training protocols. With the right systems, these results are not only achievable but repeatable.
How We Can Help
At POWERS, we specialize in helping manufacturers optimize their startup processes. Our team provides hands-on support, actionable strategies, and proven tools to eliminate costly missteps and get production running smoothly.
Implementing a robust startup process is crucial for manufacturing success, and POWERS’ Digital Production System (DPS) offers comprehensive tools to facilitate this. With features like the Startup Scorecard, DPS enables you to evaluate startup effectiveness through detailed metrics, ensuring that each launch is optimized for performance.
The Customizable Dashboard provides real-time data and insights at a glance, allowing for immediate adjustments during the startup phase. Additionally, the Daily Schedule Control (DSC) feature helps track, measure, and report performance, keeping your startup on schedule and within budget. By integrating DPS into your operations, you can streamline processes, increase efficiency, and drive sustainable performance improvements from the very start.
Start Right, Stay Ahead
In manufacturing, a good startup isn’t just the beginning—it’s the difference between thriving and surviving. Investing in preparation, training, and technology can reduce downtime, save costs, and build stronger relationships with your customers. Ready to take your startup to the next level? Let’s get to work.
- Speak to an Expert: Call +1 678-971-4711 to discuss your specific challenges and goals.
- Email Us: Get tailored insights by emailing info@thepowerscompany.com
- Request an Assessment: Use our online contact form, and one of our expert manufacturing consultants will reach out to schedule an in-depth analysis of your operations.