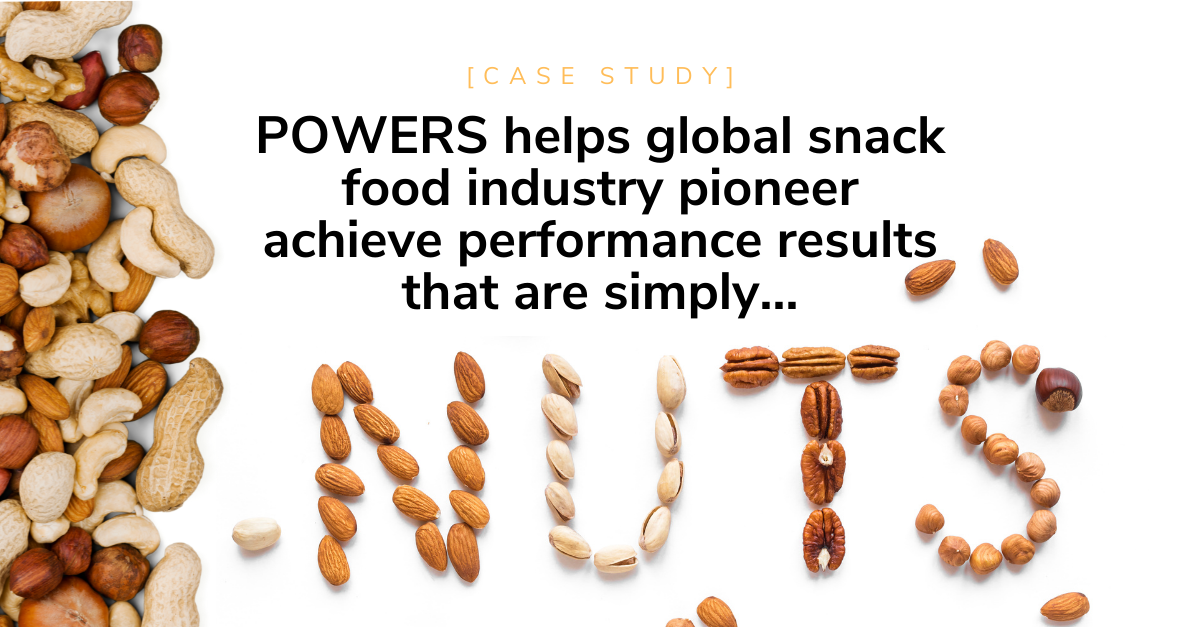
Facing aggressive annual growth and significant operational and cultural performance challenges, POWERS facilitates rapid and sustainable improvements for snack food industry pioneer.
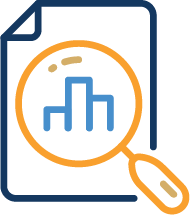
Project Overview
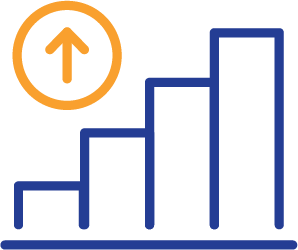
Performance Results
Background
Our client is one of the nation’s premier nut and trail mix snack manufacturers. The company is a pioneer in the industry and strives for responsible, transparent, and sustainable practices throughout its extensive global supply chain. Their responsibly sourced materials from thousands of farmers worldwide contribute significantly to local farming economies.
When partnering with POWERS, their primary operational performance goal was to increase production capacity on two key production lines to satisfy customer demand for the mix of products produced on these special lines. In addition, to keep pace with 14% annual sales growth, production capacity and inventory positions were required to increase continually.
Plant Management was struggling with a shorthanded and undertrained workforce, filling in a substantial number of positions with temporary labor and covering for open supervisor positions by expanding the work scope of other supervisors and lead hand roles.
To meet customer demand, the plant was being run six
to seven days a week with the same crewing, an unsustainable plan resulting in elevated levels of employee call-offs.
On-Time-in-Full (OTIF) delivery suffered because of limited capacity, limited ingredient supply, and labor constraints. For these same reasons, there was no fixed schedule in place. Instead, schedules were constantly being changed based on available ingredients and operators.
Many MOS (Management Operating System) meetings had been eliminated due to concerns about the spread of the COVID-19 virus. e.g., shift handover meetings.
Significant production line mix variations make it challenging to develop meaningful production line trend data and establish daily/weekly production targets.
Plant Management was convinced that the only way to increase plant capacity and throughput was by increasing headcount and staffing up key supervisory roles.
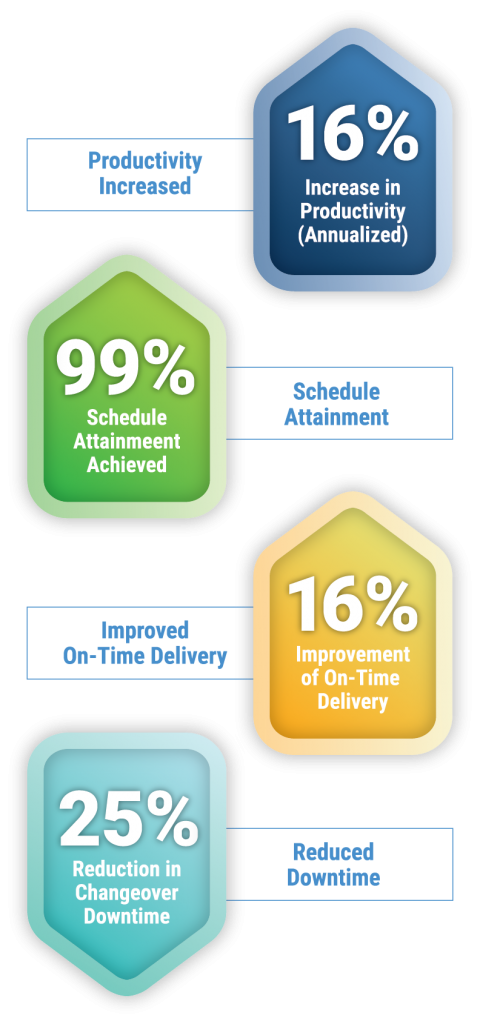
Situation
Our client is one of the nation’s premier nut and trail mix snack manufacturers. The company is a pioneer in the industry and strives for responsible, transparent, and sustainable practices throughout its extensive global supply chain. Their responsibly sourced materials from thousands of farmers around the world contribute greatly to local farming economies.
Their primary operational performance goal when partnering with POWERS was to increase production capacity on two key production lines to satisfy customer demand for the mix of products produced on these special lines. To keep pace with 14% annual sales growth, production capacity and inventory positions were required to continually increase.
Plant Management was struggling with a shorthanded and undertrained workforce, filling in a substantial number of positions with temporary labor as well as covering for open supervisor positions by expanding the work scope of other supervisors and lead hand roles.
To meet customer demand, the plant was being run six to seven days a week with the same crewing, an unsustainable plan resulting in elevated levels of employee call-offs.
On-Time-in-Full (OTIF) delivery suffered because of limited capacity, limited ingredient supply, and labor constraints. For these same reasons, there was no frozen schedule in place. Schedules were constantly being changed based on available ingredients and operators.
A number of MOS (Management Operating System) meetings had been eliminated due to concerns about the spread of the COVID-19 virus. E.g., shift handover meetings.
Significant production line mix variations make it difficult to develop meaningful production line trend data and establish daily/weekly production targets.
Plant Management was convinced that the only way to increase plant capacity and throughput was by increasing headcount and staffing up key supervisory roles.
Analysis
- Production targets have been lowered to match historical OEE (Overall Equipment Effectiveness) measures. Targets are not based on best demonstrated or EOM theoretical run times.
- Problem Solving Process was not robust and disciplined which led to waste, scrap, rework, lost capacity, and increased cost/lb.
- Lack of standard work for Supervisors led to a variety of supervisory approaches across the shifts. No Best Practices had been defined.
- Poor sanitation procedures before and during changeovers significantly increased changeover times. Procedures to maintain parts washer temperature and cleaning cycles resulted in significant rework due to failed quality inspections.
- Front Line Supervisors lacked understanding of the Plan/Actual/Variance/Action (PAVA) cycle on the floor and required additional coaching and development.
- Performance reporting and review were not well defined as Key Performance Indicators and weekly measurements were frequently revised and redefined. No Identification, documentation, or follow-up of production issues. Corrective actions were not discussed in meetings.
- Start-ups and changeovers were taking longer than planned and driving significant levels of unplanned downtime.
Solution
- Developed a comprehensive Management Operating System (MOS) supported by 24 Standard Operating Procedures (SOPs) which we shared with the client team, coached, and monitored to these standards.
- The MOS (Management Operating System) includes Daily Supervisor Huddle meetings, Shift Handover meetings, Weekly Performance Review meetings, Gemba Walks and action logs as well as performance standards. Installed action log reporting in all meetings.
- Worked with the Maintenance and Engineering Manager to identify equipment issues/Quick Wins following shop floor observation by the project team. The action log is being monitored to assure the completion of the maintenance actions.
- Reduced the time required for Change Overs by identifying all changeover tasks, developing a comprehensive changeover plan, and applying SMED (Single Minute Exchange of Die) to streamline the process.
- Developed sanitation checklists and standard operating procedures to improve the sanitation process during changeovers significantly improving first-time passes on quality inspections.
- Improved completion of Start-Up activities and increased throughput during the first hour of production by use of a start-up checklist and provided scorecards and coaching for the startup team.
- Improved the bags per minute by developing an equipment centerline process to reduce variation in the way equipment is run.
- Installed issue escalation processes to quickly identify and escalate the causes of production losses.
- Developed Standard work for Frontline Supervisors to ensure alignment of expectations across all shifts. Coached Frontline Supervisors on the new expectations and improved communication between shifts.
- Defined and reported key performance indicators. Coached meeting behaviors to expect the team to identify corrective and preventative actions in response to underperforming KPIs
- Trained Supervisors and Equipment Operators on performing Root Cause Analysis. Modeled RCA using a fishbone chart as well as 5 Why to identify the root cause and take corrective actions.
- Defined Root Cause Analysis triggers. Followed-up to see triggers were routinely identified and that the Root Cause Analysis process was effectively completed.
Results
- Improving equipment conditions, establishing Operator’s centerlines, and improving Supervision practices, procedures and behaviors helped to improve the average Bags Per Minute production. An analysis of the high-volume products produced on lines 1&2 indicated a 2.64% improvement in productivity in the first 8 weeks of the project (annualized 12-16%).
- Schedule attainment improved during the project from 94.7% in the baseline period to an average of 98.5% during the project.
- The identified improvement in changeover processes will allow our client-partner to compress changeover times and reduce overall changeover downtime by 15-25%.
- The improved changeover times, the escalation process, and use of RedZone for proactive supervision will help reduce unplanned downtime as plant personnel becomes accountable for using the tools implemented.
- On-Time-in-Full (OTIF) deliveries improved during the project from 70.8% to 81.8%.