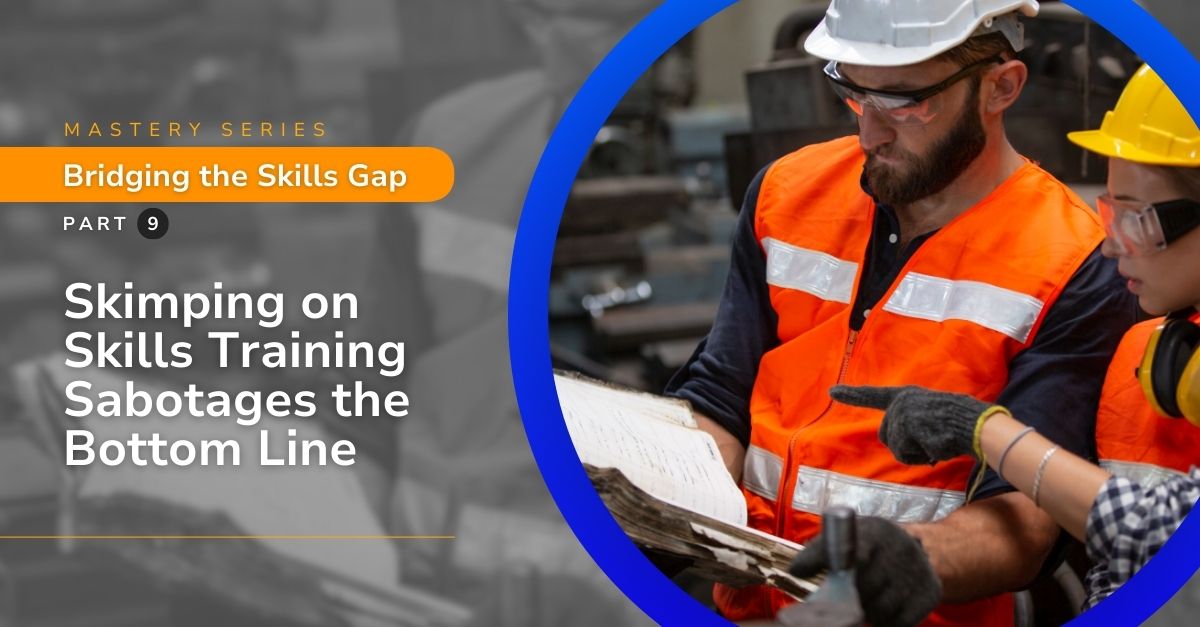
Neglecting investment in upskilling your workforce, especially your frontline leaders, creates a chain of overlooked opportunities that quietly erode manufacturing efficiency.
On the surface, operations may appear to be running smoothly. Still, deeper issues arise when your frontline managers and supervisors lack the training and skills to identify and act on cost savings and process improvement opportunities.
Take, for example, the increasing complexity of energy consumption in modern manufacturing. When employees are not trained to track and optimize energy usage, outdated practices persist. Inefficient energy consumption can result in unnecessary utility expenses and underperformance of energy-efficient machinery. Employees unaware of fully leveraging these newer machines may bypass energy-saving features altogether. Over time, this drives up operational costs, straining the facility’s budget without signs of immediate failure.
This is just one of many secondary symptoms stemming from the lack of targeted upskilling. These missed opportunities accumulate in various forms—inefficiencies in production scheduling, material usage, equipment maintenance, and workflow optimization.
When training is neglected, these opportunities for savings and process improvements slip through the cracks, undermining productivity and long-term growth.
Understanding and addressing the secondary symptoms is critical to fostering an operation where processes are continuously optimized and cost-saving measures are fully leveraged. Here are ten key areas where this gap becomes apparent and strategies to mitigate these issues.
1Inconsistent Identification of Inefficiencies:
When employees lack the skills to evaluate processes continuously, inefficiencies often go unnoticed. The absence of training in process improvement methodologies like Lean or Six Sigma leads to inconsistent waste identification and bottlenecks. This results in persistent, small inefficiencies that drain productivity over time.
Mitigation: Upskilling employees with targeted training in process improvement tools will help establish a workplace culture of continuous improvement. Regular workshops on identifying and eliminating waste will equip the workforce to address inefficiencies before they escalate. Additionally, empowering employees to suggest improvements can enhance real-time problem-solving.
2Inconsistent Use of Data Analytics for Process Optimization:
In many manufacturing environments, data analytics is underutilized due to a lack of training. Employees who are not adept at interpreting operational data miss critical insights into areas such as cycle time reduction and machine performance. This results in missed opportunities to optimize processes, leading to longer production times and higher operational costs.
Mitigation: Providing comprehensive training in data analytics platforms can enable employees to harness the power of real-time data. Implementing data-driven dashboards allows shop floor managers to visualize trends and deviations, making process optimization an ongoing effort rather than a reactive task. Regular data review sessions can keep teams aligned with continuous improvement goals.
3Delayed Adoption of Lean Manufacturing Practices:
Without upskilling in the principles of Lean manufacturing, employees may struggle to implement cost-saving methodologies like just-in-time (JIT) inventory or Kanban systems. The delay in adopting these practices often leads to higher inventory costs and increased lead times, directly impacting profitability.
Mitigation: Introducing Lean training workshops, specifically targeting employees involved in production scheduling and inventory management, can accelerate the adoption of Lean practices. Regular Lean audits can ensure that the methodologies are being followed and refined based on changing operational needs. Engaging employees in these practices fosters ownership and quicker implementation.
4Missed Chances to Automate Routine Tasks:
Automation is one of the most significant cost-saving opportunities in manufacturing, yet when employees aren’t equipped to recognize which processes are ripe for automation, these opportunities are overlooked. Simple, repetitive tasks that could be automated continue to drain human resources, leading to inefficiencies.
Mitigation: A focused investment in training employees to identify automation candidates will streamline operations. Teaching staff to evaluate tasks for automation suitability and cross-training in operating and maintaining automated systems can significantly boost productivity. Managers can also create a task force to regularly assess processes for automation potential.
5Missed Optimization of Material Usage:
In environments where employees aren’t trained in cost-saving techniques related to material usage, waste often becomes a substantial problem. Without the skills to optimize cutting or assembly processes, employees may use excess materials, resulting in higher raw material costs and increased waste disposal fees.
Mitigation: Training in material optimization techniques, such as nesting software for cutting processes or waste reduction strategies for assembly, can drastically improve material efficiency. Regular material audits, led by trained employees, can identify where waste occurs, and improvements can be implemented in real-time to mitigate these issues.
6Overproduction Due to Inefficient Scheduling:
Poor scheduling practices lead to overproduction, a form of waste in Lean manufacturing. If employees responsible for production planning aren’t trained in demand forecasting and schedule optimization, they are more likely to generate excess inventory. This leads to increased holding costs and the risk of obsolescence.
Mitigation: Upskilling production planners in advanced scheduling tools and demand forecasting techniques can reduce overproduction. Integrating these tools with existing ERP systems will allow real-time adjustments based on actual demand. Additionally, providing training in inventory management can reduce the need for large stockpiles, cutting down on holding costs.
7Inconsistent Evaluation of Equipment Performance:
Untrained employees may not consistently evaluate key equipment performance, missing early signs of wear or inefficiency. This can lead to unplanned downtime, increased maintenance costs, and inefficient resource use, all of which negatively impact productivity.
Mitigation: Establishing a regular training program that focuses on equipment performance metrics will ensure consistent evaluations. Employees trained to recognize early signs of wear and inefficiency can prevent costly breakdowns. Implementing predictive maintenance programs, where trained employees monitor equipment data, will allow for more proactive maintenance scheduling.
8Inability to Leverage Cost-Saving Technologies:
Technological advancements offer numerous ways to save costs, but without proper training, employees often miss the opportunity to leverage these tools. Whether it’s energy-efficient machinery or advanced quality control software, the lack of skills to utilize these technologies fully can result in significant missed savings.
Mitigation: Regular training on new technologies is essential. Managers should create a structured process for introducing new tools and ensure employees are adequately trained. Additionally, engaging employees in continuous learning around emerging technologies can keep operations at the forefront of innovation.
9Poor Identification of Process Bottlenecks:
Employees who lack the skills to analyze workflows often miss identifying bottlenecks that hinder production efficiency. Bottlenecks can lead to significant delays, increased lead times, and diminished throughput, affecting overall productivity.
Mitigation: Training employees in value stream mapping and other bottleneck identification tools can empower them to locate and resolve these constraints. Teams with these skills can regularly reassess workflows and reallocate resources to ensure smooth operations. Visual management tools like Kanban boards can also help teams monitor and react to bottlenecks in real time.
10Inefficient Use of Floor Space and Workflow Layouts:
A poorly optimized shop floor layout can lead to longer lead times, wasted movement, and inefficiencies in the production process. Without the proper knowledge of layout optimization, employees may fail to identify ways to improve workflow efficiency, which can slow down production and increase labor costs.
Mitigation: Educating employees on lean layout principles and space utilization strategies will help optimize workflow. Regular floor layout reviews and Kaizen events focused on lay movement can identify areas where space is underutilized or workflow inefficiencies occur. Employees trained in these principles can suggest and implement improvements that reduce waste and improve overall productivity.
Conclusions for Operations Leaders
In today’s competitive manufacturing environment, failing to invest in upskilling has far-reaching consequences, manifesting missed opportunities for cost savings and process improvement. From inefficient use of materials to underutilized technology, these gaps are not always immediately visible but compound over time to erode productivity and profitability. Addressing these challenges requires a proactive approach to training and continuous improvement—an approach that empowers employees to identify inefficiencies, optimize processes, and fully leverage the technologies at their disposal.
By fostering a culture of continuous improvement and providing targeted training programs, we help organizations unlock their full potential, driving sustainable productivity gains.
Our hands-on approach ensures that employees are trained and capable of implementing and maintaining process optimizations. The result? A more agile, efficient workforce that seizes cost-saving opportunities before they turn into operational bottlenecks.
POWERS can help by:
- Implement comprehensive upskilling programs focused on lean manufacturing, process optimization, and continuous improvement.
- Training teams to leverage data analytics and predictive maintenance for smarter, real-time decision-making.
- Identifying automation opportunities and integrating cost-saving technologies effectively.
- Optimizing workflows, floor layouts, and material usage to reduce waste and boost efficiency.
By partnering with POWERS, manufacturers can address the root causes of missed opportunities for cost savings and process improvement. Together, we can build a workforce that is not only prepared for today’s challenges but equipped to drive sustainable growth and long-term success.
- Speak to an Expert: Call +1 678-971-4711 to discuss your specific challenges and goals.
- Email Us: Get tailored insights by emailing info@thepowerscompany.com
- Request an Assessment: Use our online contact form, and one of our expert manufacturing consultants will reach out to schedule an in-depth analysis of your operations.
Continue Reading from this Mastery Series
- Part 1 – Why Automation Alone Won’t Boost Productivity
- Part 2 – Why Non-Technical Skills Are Increasingly the Key to Increasing Productivity
- Part 3 – The Widening Digital Divide is Leaving Some Companies in the Dust
- Part 4 – Lack of Upskilling Sabotages Problem-Solving, Decision Making, and Innovation
- Part 5 – The Link Between Upskilling and Employee Well-being
- Part 6 – Neglecting Upskilling Leaves Your Operation Vulnerable to Safety Issues
- Part 7 – How Neglecting Upskilling Erodes Legacy Knowledge and Hurts Productivity
- Part 8 – Failing to Upskill Frontline Leaders Can Derail Operations
- Part 9 – Skimping on Skills Training Sabotages the Bottom Line
- Part 10 – An Underdeveloped Workforce Means an Unscalable Operation