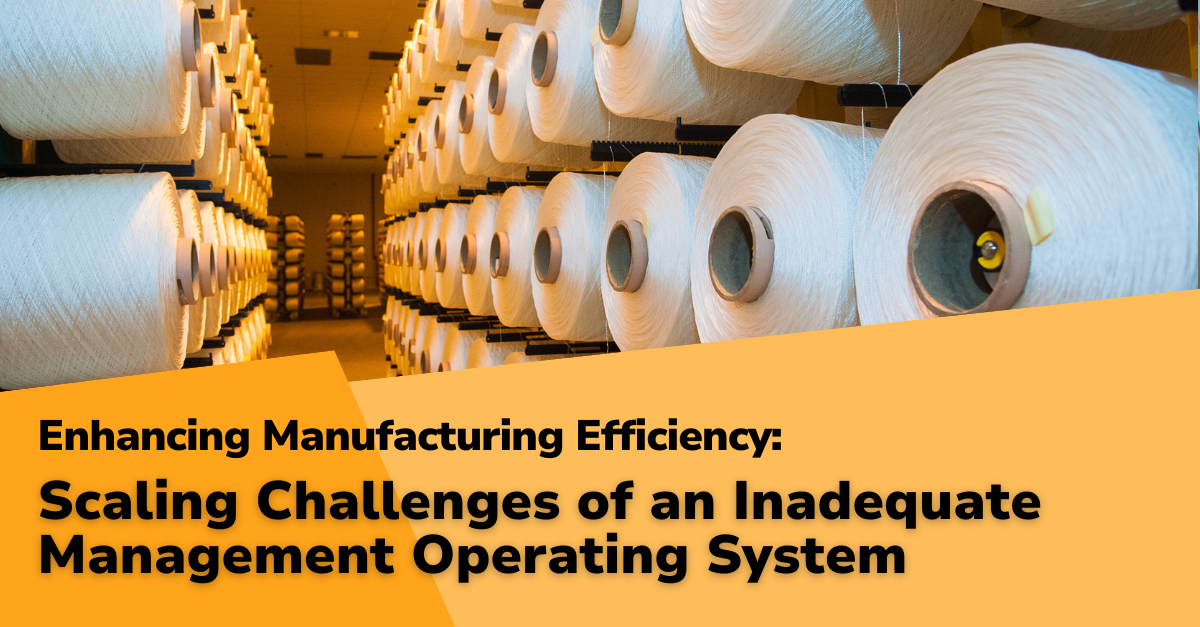
In the sixth part of our “Enhancing Manufacturing Efficiency” Mastery Series, we focus on a pivotal factor in manufacturing growth and efficiency: the role and impact of the Management Operating System (MOS) in scaling operations.
This edition is dedicated to unraveling how a deficient MOS can be a significant barrier to a company’s ability to scale up in the marketplace efficiently, take market share profitably, and build its competitive advantage over the long haul.
As organizations in the manufacturing sector aspire to expand, the ability to scale operations effectively and efficiently becomes a crucial marker of success.
However, the robustness and implementation of its MOS are often overlooked elements that can profoundly influence this scalability. This analysis provides a comprehensive view of the challenges an inadequate MOS poses to growing companies. We draw from our practical experiences, industry insights, and best practices to highlight how these challenges manifest and their implications for operations executives and stakeholders.
Understanding the pitfalls of an underdeveloped MOS is essential for any company seeking sustainable growth and market competitiveness. Our exploration delves into the top 10 areas where an insufficient MOS can hinder a company’s expansion efforts, backed by data and relevant case studies. This article aims to identify these key challenges and offer a perspective that empowers manufacturing leaders to navigate and overcome them effectively.
1Fragmented Process Management:
Fragmented process management, stemming from a disjointed Management Operating System (MOS), leads to significant operational inefficiencies. These inefficiencies often manifest in delays and increased costs, as disjointed processes can hinder operating efficiency by up to 30%. This fragmentation is particularly detrimental during scaling phases, where managing increased operational demands is critical.
2Limited Visibility into Operations:
A weak MOS often compromises operational visibility, a critical component for effective scaling. The lack of comprehensive insights into operations can result in misaligned growth strategies and operational inefficiencies. Ensuring clear operational visibility is paramount for companies to navigate the complexities involved in scaling successfully.
3Inadequate Infrastructure:
Inadequate infrastructure, such as limited facilities and outdated equipment, severely constrains scaling operations. This limitation not only restricts production capabilities but also hampers overall efficiency. Suitable infrastructure is a fundamental requirement for companies to scale up effectively, enabling them to meet the increasing demands of their market and maintain a competitive edge.
4Ineffective Resource Allocation:
Suboptimal resource allocation, a consequence of an underdeveloped MOS, is a critical challenge in scaling operations. Inefficiencies in the distribution of resources – human, financial, or material – can lead to resource wastage or overextension. Efficient and strategic resource allocation is vital to scale operations successfully while managing costs effectively.
5Difficulty in Managing Increased Complexity:
With growth, a company’s operations become increasingly complex. An inadequate MOS can struggle to manage this complexity, leading to operational bottlenecks that hinder scalability. These bottlenecks impede a company’s ability to adapt to growing operational demands, crucial for sustained growth and market competitiveness.
6Capacity Constraints:
Limited production capacity is a major barrier to meeting market demand during scaling phases. This limitation can result in significant lost revenue opportunities and adversely affect customer relationships. For example, manufacturers failing to scale may lose up to 20% of potential sales during peak demand periods, underscoring the importance of addressing capacity constraints.
7Technology Gaps:
A weak MOS often leads to underutilization of data, which is pivotal in modern scaling strategies. Such underutilization results in poorly informed decisions, hampering growth and scalability. Embracing technological advancement is essential for scaling, with industry data indicating that a lack of investment in new technologies can lead to a productivity lag of up to 25%. This lag affects both efficiency and competitive positioning in the market.
8Workforce Management Challenges:
Effective scaling often necessitates workforce expansion or restructuring. Manufacturers facing scaling challenges may encounter workforce management issues, including skill shortages and inefficient labor deployment, which can significantly impact overall productivity. Addressing these challenges is critical to maintaining operational efficiency during growth phases.
9Financial Constraints and Cash Flow Issues:
Scaling challenges can lead to inefficient capital usage, impacting ROI, OEE, and profitability. Manufacturers grappling with scaling issues might struggle with cash flow management and securing the necessary financing. This struggle can hinder their ability to invest in new technologies, expand the workforce, or upgrade infrastructure, thereby limiting growth and sustainability. Financial constraints can also force reliance on short-term solutions that are less cost-effective and sustainable in the long run.
10Market Share Erosion :
An inability to effectively scale can result in losing market share to competitors more adept at meeting market demands. This issue is particularly critical in industries characterized by rapid innovation cycles or fluctuating demand patterns. Maintaining scalability is essential for companies to stay competitive and retain or increase their market share in a dynamic market environment.
Conclusions for Manufacturing Operations Leaders
The lack of a well-implemented Management Operating System (MOS) often leads to the inability to scale operations effectively, respond to market dynamics, and create sustainable growth. The issues range from inefficient use of capital to organization-wide operational visibility to market share erosion. Such challenges disrupt current operations and impede long-term strategic growth and innovation. Leaders in manufacturing must recognize and tackle these issues to maintain a competitive edge.
These insights form a crucial part of the dialogue for operations executives and stakeholders steering their organizations toward market leadership and long-term success.
The POWERS Difference
POWERS is uniquely positioned to enhance MOS effectiveness in manufacturing. Our approach includes:
- Tailored Solutions: We design MOS solutions specifically suited to each manufacturing context, addressing unique quality and operational challenges.
- Comprehensive Integration: Beyond implementation, we integrate the MOS into your organizational culture and processes for a cohesive operational framework.
- Empowering People and Processes: Our strategy is to engage and train employees at all levels to maintain and enhance quality standards.
- Data-Driven Decision-Making: We leverage the latest analytics for informed, strategic decision-making.
- Proven Expertise: With a history of successful MOS implementations, we bring deep insights into enhancing quality and efficiency in manufacturing.
Partner with POWERS to ensure your company’s ability to scale operations effectively through an optimized MOS. Start your journey toward a more sustainable, scalable, and profitable business today.
Unlock the full potential of a robust Management Operating System with POWERS and set your path toward unparalleled operational excellence. For expert guidance and solutions tailored to your unique operational challenges, contact our team at +1 678-971-4711 or email info@thepowerscompany.com.
Continue Reading from this Mastery Series
- Part 1 - Identifying Key Inefficiencies in the Absence of a Management Operating System
- Part 2 - Top 10 Pitfalls: Lack of an MOS Derails Productivity
- Part 3 - Top 10 Quality Issues at Risk Without a Robust Management Operating System
- Part 4 - The High Cost of an Ineffective Management Operating System
- Part 5 - Without an Optimized Management Operating System, Decision-Making is Severely Impaired
- Part 6 - Scaling Challenges of an Inadequate Management Operating System
- Part 7 - The High Price of Low Engagement: Unpacking the Operational Impact of Employee Discontent
- Part 8 - Safeguarding Success: Decoding the Impact of Compliance and Safety Issues
- Part 9 - Examining the Cost of a Slow Response to Market Shifts
- Part 10 - Charting Success: Understanding the Costs of Losing Competitive Advantage