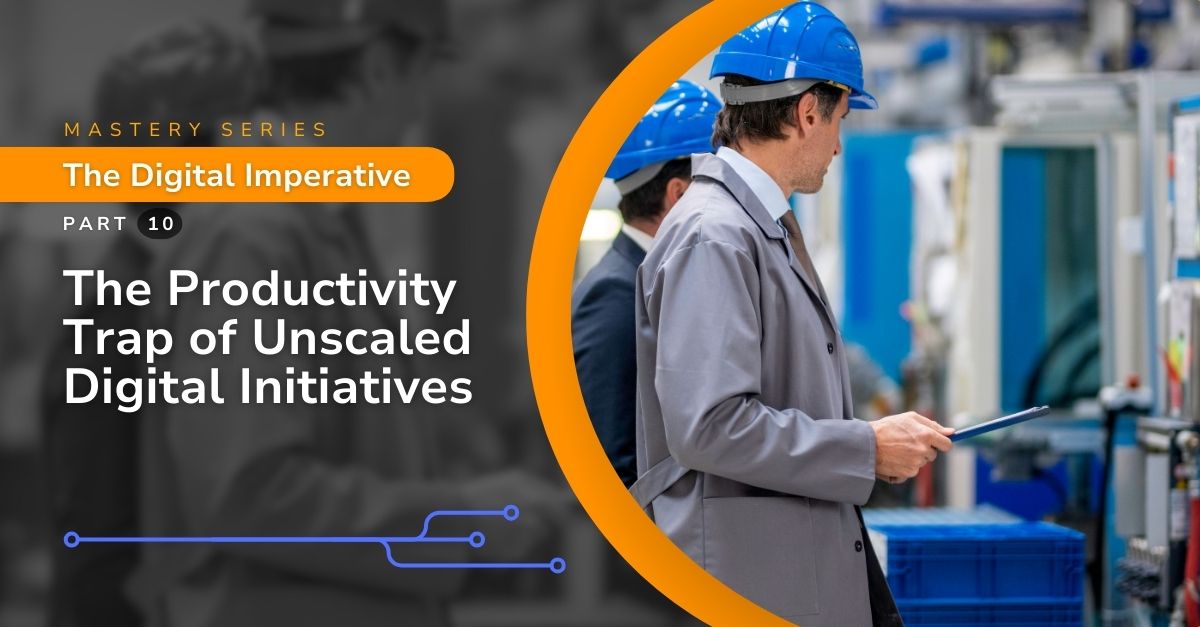
Neglecting digital transformation often leads to stagnant pilot projects, preventing companies from scaling these initiatives and missing out on the full potential of Industry 4.0.
This failure to scale can manifest in numerous ways, with far-reaching consequences for productivity and operational efficiency.
This results in fragmented systems and isolated successes that don’t impact the broader business.
One example is the inability to scale a pilot project that integrates IoT-enabled sensors for real-time machine performance monitoring. A small pilot might reveal significant cost savings and downtime reductions on a single production line. Still, without scaling, the rest of the plant continues to rely on outdated manual monitoring methods. The disconnect between the isolated pilot and the rest of the factory operations leads to inconsistent data flow, which makes it difficult to generate reliable predictive maintenance insights. As a result, while one production line improves, the broader facility struggles with unscheduled breakdowns, eroding the overall productivity gains the pilot initially promised.
This failure to scale pilot projects is a common symptom of neglecting digital transformation, leaving manufacturers unable to fully leverage the technologies available. It leads to missed opportunities for efficiency, cost savings, and operational improvement, ultimately making competing in a rapidly evolving industry harder.
By failing to bridge the gap between initial digital experiments and full-scale implementation, manufacturers miss the chance to optimize their operations and fall behind competitors who have successfully integrated Industry 4.0 technologies.
1Fragmented Data Collection Due to Isolated Pilot Systems:
When pilot projects operate in isolation, data collection becomes fragmented, resulting in disjointed insights that are challenging to consolidate across the broader organization. Managers frequently encounter this issue when a pilot generates valuable data, but this data cannot seamlessly integrate into the company’s larger data infrastructure. This leads to inefficiencies, as the insights from the pilot may be lost or underutilized due to inconsistent data management practices.
Mitigation: To mitigate fragmented data collection, it’s crucial to establish data pipelines from the onset that are compatible with the organization’s broader systems. A unified data management strategy ensures that information gathered during the pilot can be easily scaled and shared across departments. Implementing cloud-based platforms or robust ERP systems can enable real-time data access, allowing managers to make more informed decisions.
2Misalignment Between Pilot Outcomes and Broader Business Goals:
A common issue is that pilot projects, while innovative, may not align with the overall strategic objectives of the business. For example, a pilot focusing on predictive maintenance may yield insights. Still, it can be viewed as a misstep if it doesn’t directly contribute to the company’s key performance indicators (KPIs). This disconnect leads to wasted resources and diminishes the perceived value of digital transformation efforts.
Mitigation: Ensure that pilot projects are designed and aligned with business goals. Engaging leadership in the project planning phase helps clarify how the pilot will drive broader organizational objectives. This can be achieved through strategic KPIs that measure pilot-specific outcomes and their potential to contribute to company-wide targets.
3Inadequate Training for Teams Beyond the Pilot Group:
When only the pilot group is trained, scaling the initiative becomes difficult due to a lack of expertise across the organization. Managers often struggle to implement changes when only a small workforce understands the new technologies. This limits productivity, as knowledge gaps across teams hinder the smooth execution of scaling efforts.
Mitigation: Expand training efforts early in the pilot phase to include the pilot team and key organizational stakeholders. This might involve creating training modules, workshops, or ongoing coaching sessions to build a foundation of understanding across teams. Investing in continuous learning and upskilling helps ensure that the knowledge necessary for scaling is distributed and that employees are ready to handle new responsibilities.
4Failure to Establish a Cross-Functional Implementation Team:
Many managers experience difficulty scaling pilot projects due to a lack of cross-functional collaboration. The pilot remains siloed without a dedicated team representing various departments— IT, operations, and supply chain. As a result, productivity suffers because the initiative lacks a comprehensive understanding of how the project impacts all areas of the organization.
Mitigation: Form a cross-functional implementation team from the beginning. This group should include representatives from all relevant departments to ensure that the pilot’s insights are translated into meaningful action across the organization. Clear communication channels and defined roles within the team help bridge the gap between the pilot project and its broader implementation.
5Underutilization of Pilot Program Insights in Other Operational Areas:
Pilot projects often generate valuable insights, but many managers fail to apply these learnings outside the specific area where the pilot was conducted. This creates missed opportunities for process improvement across the organization, as valuable data and techniques are not shared or applied to other operations, reducing the overall impact of the pilot on productivity.
Mitigation: Create a system for disseminating learnings from pilot projects across departments. Regular cross-departmental meetings or digital knowledge-sharing platforms can help spread the pilot’s insights to areas that could benefit from similar improvements. Documenting best practices and lessons learned allows other teams to adapt these strategies to their processes.
6Lack of Clear Metrics for Measuring Pilot Scalability Success:
Without clear metrics, it’s challenging for managers to assess whether a pilot project is successful or ready for scaling. This often leads to ambiguity about whether to proceed, causing delays that directly impact productivity. Managers may struggle to demonstrate ROI or the value of expanding the pilot across the organization.
Mitigation: Develop clear and measurable criteria for scalability success before the pilot begins. These metrics should include short-term indicators—such as cost reductions and efficiency improvements—and long-term scalability measures, such as the ease of integration with other systems. By defining these benchmarks early, managers can more confidently push forward with scaling efforts.
7Pilot Project Fatigue Due to Excessive Trial-and-Error Approaches:
When pilot projects become too experimental, managers may experience “pilot fatigue,” where the organization becomes stuck in an endless loop of trial-and-error approaches. This causes frustration, reduces motivation to innovate, and ultimately hampers productivity, as resources are continually spent on pilots without moving toward full implementation.
Mitigation: To combat pilot fatigue, adopt a more structured approach to piloting. Limit the number of pilot projects running simultaneously and establish strict timelines for each pilot phase. A phased approach allows for manageable experimentation while ensuring that successful pilots rapidly move toward scaling, boosting long-term productivity.
8Poor Stakeholder Engagement in Scaling Discussions:
Scaling pilot projects often requires buy-in from various stakeholders, including executives and department heads. If these key players are not engaged in early discussions, securing the necessary support to scale successfully can be difficult. Lack of stakeholder engagement frequently leads to stalled projects and reduced enthusiasm for digital transformation efforts.
Mitigation: Engage stakeholders early and often, providing regular updates on pilot progress and how the outcomes will benefit their departments. Building a strong case for pilot scaling requires transparent communication and alignment with each stakeholder’s goals. This can also involve demonstrating quick wins from the pilot to gain their confidence.
9Difficulty Justifying Additional Investment Post-Pilot:
After a pilot, managers’ biggest challenge is securing the budget and resources needed to scale. If the ROI of the pilot isn’t immediately clear, or if the scaling process appears too costly, upper management may be hesitant to provide further investment. This leads to stalled progress and diminished productivity as the benefits of the pilot remain unrealized.
Mitigation: Prepare a detailed financial case outlining the long-term cost savings and productivity improvements from scaling the pilot. Include projections for ROI, efficiency gains, and reduced operational costs over time to justify additional investments. Additionally, consider phased investments, starting with small-scale expansions to demonstrate success before committing to full-scale implementation.
10Unrealistic Timelines for Scaling Across the Organization:
Establishing unrealistic timelines for scaling a pilot project is a common issue, especially when upper management pushes for quick results. This pressure often leads to rushed implementations that overlook critical steps, such as training, integration, and change management, resulting in reduced productivity as teams struggle to adapt.
Mitigation: Create realistic, phased timelines that account for all aspects of scaling, including system integration, workforce training, and gradual process changes. A detailed project roadmap with clearly defined milestones helps manage expectations and ensures that each scaling stage is done thoroughly. This methodical approach minimizes disruptions to productivity while allowing the project to grow sustainably.
Conclusions for Operations Leaders
Failure to scale digital pilot projects in manufacturing can limit the transformative benefits that Industry 4.0 offers. The inability to move beyond initial experimentation, such as isolated IoT or AI integrations, can severely hinder overall productivity. Fragmented data systems, misaligned goals, and underutilized pilot learnings all contribute to missed opportunities for operational improvements. By addressing these challenges, manufacturers can ensure that their pilot projects lead to widespread productivity gains across the organization.
Our Digital Production System (DPS) offers tools that provide real-time visibility, predictive insights, and enhanced collaboration, allowing your organization to fully embrace Industry 4.0.
How POWERS and DPS Can Help You Scale for Success
Here’s how POWERS can assist you in achieving sustainable productivity improvements:
- Real-Time Monitoring: DPS provides complete visibility into your operations, allowing you to immediately monitor machine performance and identify inefficiencies.
- AI-Driven Insights: Leverage DPS’s advanced AI to predict maintenance needs, optimize production schedules, and make data-backed decisions that enhance productivity.
- Reduced Downtime: Minimize unplanned downtime with predictive maintenance strategies powered by DPS’s real-time data analytics.
- Maximized Resource Allocation: Optimize material and labor use with intelligent scheduling and resource management, all accessible through DPS’s intuitive dashboards.
POWERS will guide you through your digital transformation journey, helping you scale your pilot projects and unlock your operation’s full potential. With the DPS system, you’ll streamline your processes and position your organization for long-term success in an increasingly competitive manufacturing landscape.
Are you ready to elevate your manufacturing operations and fully embrace the digital era? Contact POWERS today to learn how we can help you scale your pilot projects and achieve measurable productivity gains across your entire value chain.
- Speak to an Expert: Call +1 678-971-4711 to discuss your specific challenges and goals.
- Email Us: Get tailored insights by emailing info@thepowerscompany.com
- Request an Assessment: Use our online contact form, and one of our expert manufacturing consultants will reach out to schedule an in-depth analysis of your operations.
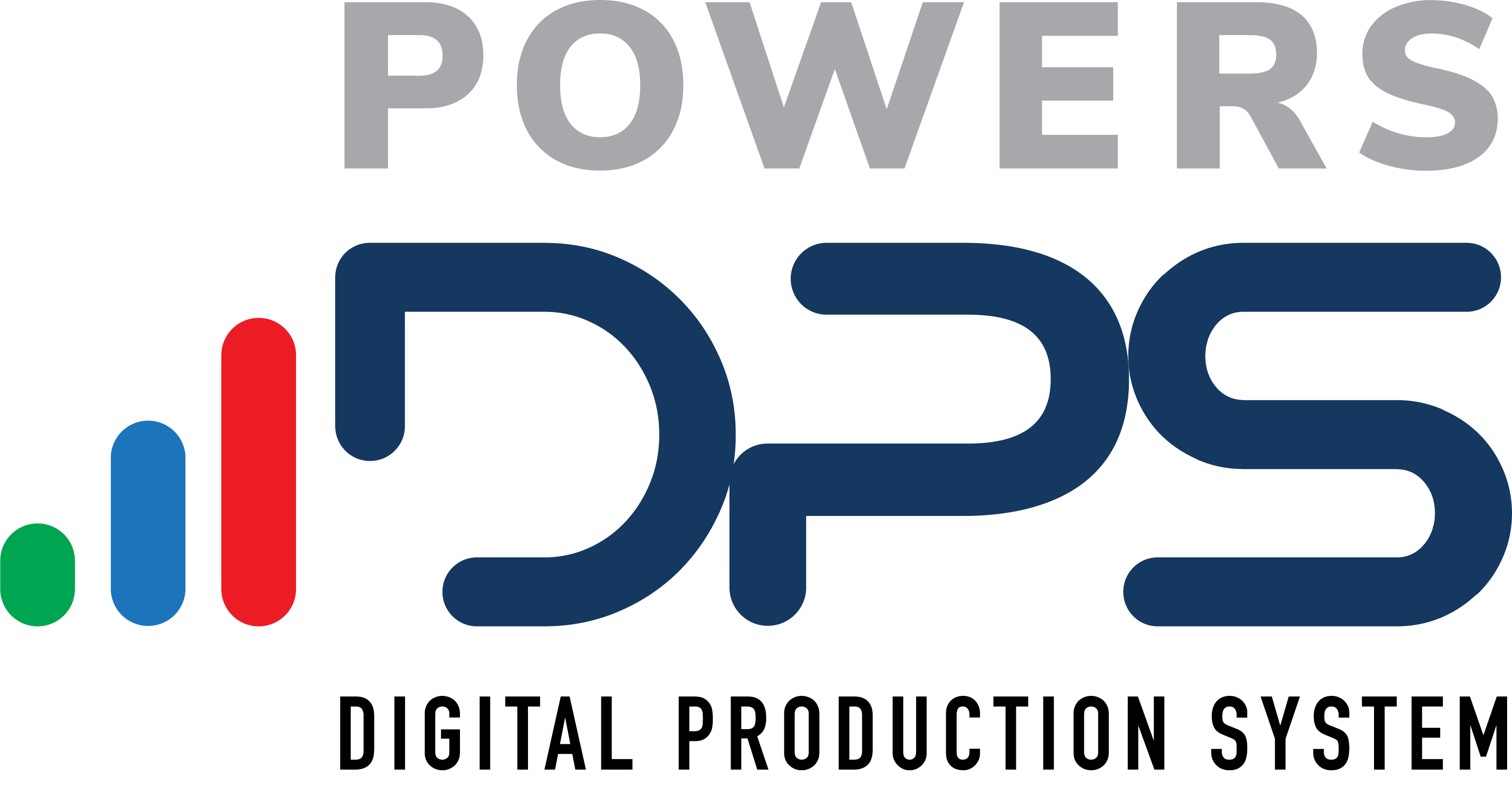
Start transforming your operations today with POWERS DPS. Contact us for a free consultation and see how digital transformation can revolutionize your manufacturing future. Learn More about DPS
Continue Reading from this Mastery Series
- Part 1 – Outdated Tech is Weakening Your Talent Pipeline
- Part 2 – How Legacy Systems Sabotage Your Cybersecurity and Productivity
- Part 3 – How Ignoring Digital Tools Leaves You Vulnerable to Downtime
- Part 4 – When Digital Stagnation Leads to Poor Communication and Production Chaos
- Part 5 – The Real Cost of Trying to Keep Up in the Market Without Digital Transformation
- Part 6 – Missing Out on Real-Time Data Drains Productivity and Profit
- Part 7 – How Failing To Go Digital Jeopardizes Regulatory Compliance
- Part 8 – How Outdated Inventory Practices Sabotage Your Operations
- Part 9 – Limited Customization Options are Driving Your Customers Away
- Part 10 – The Productivity Trap of Failing to Scale Digital Initiatives