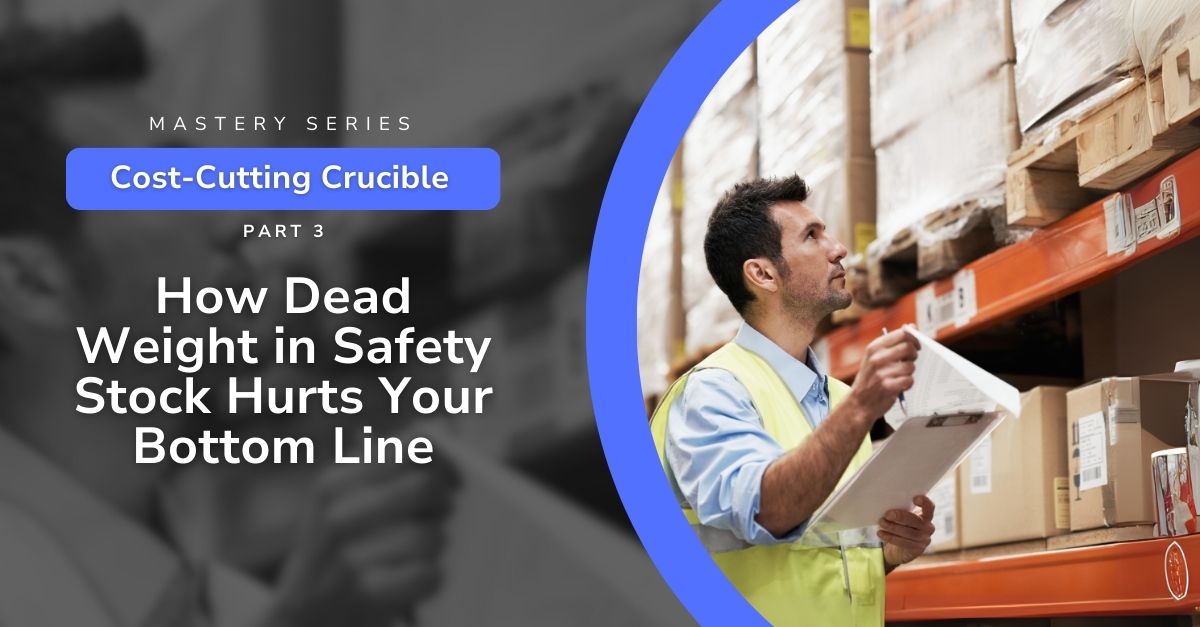
Inventory overheads from excessive safety stock and obsolete inventory are prime examples of how unseen drains on profit undermine financial performance.
Even more problematic, these hidden costs don’t just rest in physical storage—they can also spread into various operational areas, amplifying inefficiencies and reducing productivity on the shop floor.
Take, for example, the challenge of excessive safety stock. While it’s meant to shield against production delays, holding too much inventory introduces new problems, including overused resources for warehouse space, increased labor for managing this stock, and the eventual spoilage or obsolescence of certain items.
A less obvious, but no less costly, secondary symptom emerges when employees are forced to sift through surplus items daily, extending picking and staging times and increasing the likelihood of human error. In cases where multiple, outdated items clutter storage, employees may inadvertently pick incorrect components, leading to production errors, delays, and rework—all of which add layers of cost.
Excessive and outdated inventory introduces risks across several key operations. Logistics, procurement, and production teams may struggle communicating accurate inventory data, compounding misalignments in production planning and stock replenishment. In some cases, valuable storage areas are occupied by obsolete goods that could have been repurposed or sold, while high-priority items are relegated to less accessible spaces. These disruptions erode efficiency and increase labor costs without clear visibility to management, making them an unseen drain on profit.
This post explores ten common issues tied to inventory overheads, examining the operational consequences of these hidden costs and presenting strategies to reduce their impact. Identifying and mitigating these drains is essential for manufacturers looking to reclaim profitability and streamline operations.
1Inability to Swiftly Adjust Safety Stock Thresholds:
Safety stock is intended as a buffer to prevent production interruptions, yet when thresholds are rigid or outdated, they fail to reflect real-time demand changes. This often leads to excessive stock, taking up storage space, draining resources, and locking up working capital. Managers often struggle to adjust safety stock thresholds promptly, especially in volatile markets where demand can change overnight.
Solution: Leveraging dynamic inventory modeling and demand forecasting tools can help adjust safety stock levels in real-time. Machine learning algorithms analyze historical sales data, upcoming production schedules, and market trends to recommend optimal safety stock levels. This aligns inventory closer to actual demand and reduces the costs of overstocked items. By making these adjustments, manufacturers can maintain liquidity, avoid unnecessary warehousing expenses, and better serve fluctuating customer needs.
2Limited Ability to Repurpose or Remarket Obsolete Stock:
As products evolve and technology advances, inventory can quickly become obsolete, accumulating outdated warehouse items. Obsolete stock occupies valuable storage space and sometimes requires special disposal methods that increase overhead. Many manufacturers lack processes to remarket, recycle, or repurpose this inventory, leading to gradual but significant profitability drains.
Solution: Regularly scheduled inventory reviews can identify items at risk of obsolescence. Developing partnerships with secondary markets or industries using obsolete products can provide a revenue recovery stream. Additionally, creating a process for recycling or donating outdated stock reduces waste, benefits the community, and may offer tax incentives. Manufacturers free up storage and reduce carrying costs tied to non-movable stock by prioritizing repurposing.
3Challenges Integrating Automated Inventory Management Systems:
Automated inventory systems are invaluable for providing visibility, accuracy, and control over stock levels, yet many managers face obstacles during implementation. Integration challenges include compatibility issues with legacy systems, incomplete data migration, and staff unfamiliarity with new technology. These challenges limit the system’s ability to help optimize inventory and reduce overhead effectively.
Solution: A thorough assessment of current operational needs and legacy system compatibility is critical before selecting an inventory management system. A phased integration approach allows for incremental changes and minimizes disruption. Involving key staff in training sessions ensures the team understands the new system’s capabilities, reducing errors and maximizing automation’s benefits. Over time, this investment streamlines operations, providing accurate inventory data that helps cut down on excess stock and overhead.
4Unawareness of Cost-Saving Alternatives to Excessive Safety Stock:
Manufacturers frequently rely on high safety stock levels to avoid disruptions, but this strategy incurs substantial costs. Alternatives like demand-driven planning and just-in-time (JIT) inventory management, which rely on precise forecasting and supplier coordination, can effectively minimize stock while meeting production requirements. Unfortunately, these strategies are often overlooked or inadequately implemented due to insufficient awareness or resources.
Solution: Building a collaborative relationship between procurement, production, and supply chain teams allows for a balanced approach to inventory management. Demand-driven planning and JIT strategies, supported by forecasting technology, minimize the dependency on high safety stock levels. Implementing these strategies with well-coordinated supplier relationships ensures that materials arrive as needed, preventing overstock and significantly reducing carrying costs while maintaining efficient production schedules.
5Limited Auditing of Non-Moving Inventory:
Slow-moving or non-moving inventory tends to go unnoticed, accruing storage and maintenance costs over time. Without consistent auditing practices, these items occupy valuable warehouse space, and the inventory often remains undetected until it becomes unsellable or obsolete. This oversight is a common pain point for managers who lack the tools or resources to conduct regular audits.
Solution: A systematic approach to inventory audits, with clear metrics like turnover rate, can help identify items that consume space and resources without contributing to sales. Routine analysis of slow-moving stock also enables informed decisions on stock adjustments, liquidation, or repurposing. By introducing automated alerts for inventory exceeding a set holding period, managers can prevent unnecessary accumulation of slow-moving items and reduce associated costs.
6Poor Knowledge Transfer for Managing Inventory Surpluses:
Inventory management knowledge is often highly specialized, and high staff turnover can result in losing critical skills and insights. This leads to missteps in managing surplus stock and underutilization of warehouse space. In some cases, new hires are not adequately trained in inventory best practices, causing surplus stock to grow unchecked.
Solution: Implementing a standardized training program emphasizing inventory best practices helps ensure incoming staff understand how to manage surpluses effectively. Training resources, documented workflows, and mentorship programs enhance knowledge transfer, allowing staff to adapt quickly. This approach optimizes surplus management and improves efficiency by ensuring continuity in inventory processes despite personnel changes.
7Siloed Communication Between Logistics and Production:
Effective inventory management requires seamless communication across departments. When logistics and production operate in silos, misalignment in stock levels and production schedules often occurs, resulting in overproduction or underutilization of stock. Managers frequently cite a lack of cohesive communication as a source of inefficiency and waste in inventory management.
Solution: A shared digital platform where logistics, production, and warehouse teams can share and update information on stock levels, demand, and forecasts helps eliminate communication gaps. With real-time data sharing, teams can align on needs and prevent overproduction. Improved coordination minimizes unnecessary safety stock, reduces storage costs, and ensures that production output matches demand, optimizing resource allocation.
8Overhead Costs Associated with Expired Goods Disposal:
Managing expired goods can be a hidden but substantial cost in certain industries, especially those handling perishable materials. Expired goods can go unnoticed without robust tracking systems until their disposal becomes necessary, incurring storage and disposal expenses that quickly add up.
Solution: Implementing a first-in, first-out (FIFO) inventory policy helps prevent stock from reaching expiration. Additionally, establishing clear disposal or recycling processes for expired goods can help reduce storage and disposal costs. For perishable items, predictive demand planning ensures that stock is ordered based on anticipated usage, minimizing waste and preventing expired goods from accumulating.
9Inadequate Benchmarking of Inventory Performance:
Benchmarking inventory metrics is vital to assess the efficiency of inventory practices. Without regular benchmarking, manufacturers may fail to notice inefficiencies, allowing excessive safety stock or obsolete inventory to continue accruing costs. Managers who lack access to performance data often find it challenging to identify improvement opportunities.
Solution: Define specific performance metrics, such as carrying costs, turnover rate, and stock-out frequency, to provide insight into inventory efficiency. Tracking these metrics and benchmarking against industry standards helps identify trends and improvement opportunities. By regularly setting and reviewing these benchmarks, managers can fine-tune inventory practices and prevent excess inventory from eroding profitability.
10Suboptimal Resource Allocation for Inventory Tracking Tools:
Limited budgets often lead to underinvestment in inventory tracking technologies, leaving managers without the tools to accurately monitor stock. Without these tools, managing inventory levels becomes more time-consuming and error-prone, increasing the likelihood of excess safety stock and stockpiling obsolete items.
Solution: Prioritize investment in inventory tracking tools that align with business needs, such as barcoding or RFID technology, to enhance visibility and accuracy. Tracking technologies streamline stock monitoring, providing insights that facilitate timely adjustments and prevent overstock situations. A calculated investment in these tools can yield significant long-term savings by reducing surplus inventory and enhancing decision-making accuracy.
Conclusions for Operations Leaders
Inventory overheads from excessive safety stock and obsolete inventory are more than just financial drains—they directly impact productivity, cash flow, and operational efficiency. By addressing these unseen costs, manufacturers can unlock hidden potential within their existing resources. Resolving issues like outdated stock, excessive safety thresholds, and inefficient storage management requires a nuanced approach that aligns inventory practices with overall business goals.
Our approach is not limited to consulting—we offer a holistic solution with our DPS (Digital Production System). This AI-powered platform integrates real-time data with decades of manufacturing expertise. DPS provides manufacturers with a seamless way to identify and address these hidden costs, enhancing productivity and profitability.
Here’s how POWERS and DPS can support your business in transforming inventory challenges into productivity gains:
- Complete Visibility: Gain real-time insights into inventory levels, track performance, and pinpoint inefficiencies using intuitive dashboards that make data actionable.
- Streamlined Resource Allocation: Use predictive AI to optimize stock levels, reduce excess safety stock, and free up capital that can be reinvested into core operations.
- Enhanced Collaboration: Foster collaboration across logistics, production, and procurement with centralized data, minimizing communication silos and aligning teams around key objectives.
- Data-Driven Decision Making: Harness advanced analytics to proactively address inventory issues, optimize storage, and make strategic decisions that reduce inventory overheads.
- Boosted Productivity and Efficiency: Lower downtime, maximize workforce allocation, and streamline inventory tracking processes, allowing your team to focus on high-value activities.
Ready to reclaim hidden profit and streamline your operations? POWERS and DPS are here to equip your business with the insights and tools needed to drive sustainable productivity improvements and achieve your strategic goals. Reach out to our team today to explore how POWERS can turn hidden costs into new growth opportunities.
- Speak to an Expert: Call +1 678-971-4711 to discuss your specific challenges and goals.
- Email Us: Get tailored insights by emailing info@thepowerscompany.com
- Request an Assessment: Use our online contact form, and one of our expert manufacturing consultants will reach out to schedule an in-depth analysis of your operations.
Continue Reading from this Mastery Series
- Part 1 – How Poor Scheduling Burns Through Your Profit Margins
- Part 2 – How Hidden Energy Wastes Burn Through Your Bottom Line
- Part 3 – How Dead Weight in Your Safety Stock Undermines Your Bottom Line
- Part 4 – The Hidden Costs of Ignoring Preventive Maintenance Programs
- Part 5 – Mismatched Skills and Wasted Workforce Potential
- Part 6 – Poor Quality Control is Dragging Down Your Productivity and Profits
- Part 7 – Being Slow to Market Undermines Your Bottom Line
- Part 8 – Supplier Missteps That Drain Profitability
- Part 9 – The Cost of Continuing to Use Manual Processes
- Part 10 – The Financial Fallout of Fragmented Compliance