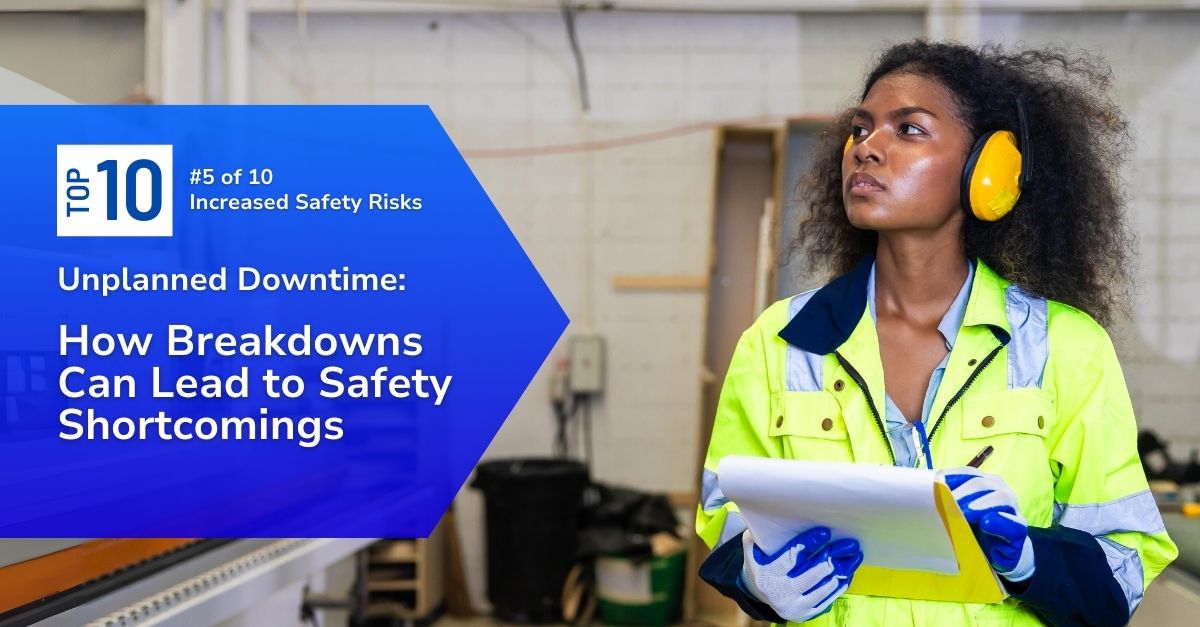
Unplanned downtime is a significant disruptor in manufacturing, leading to numerous challenges that can severely impact operations. One of the most critical consequences of unplanned downtime is the increased safety risks it introduces on the shop floor.
In manufacturing, unplanned downtime can cause workers to face increased pressure to meet tight deadlines, leading to hasty and potentially unsafe practices. For instance, a less common but highly impactful scenario is mislabeling hazardous materials due to rushed processes. When unplanned downtime disrupts the regular workflow, employees might hastily label or handle dangerous substances, increasing the risk of exposure to harmful chemicals or creating fire hazards.
This series will explore the top 10 ways unplanned downtime increases safety risks. We will explore the granular issues managers face on the shop floor, such as increased lead times, difficulty forecasting demand, erosion of supplier trust, inventory imbalances, and more. Each point will be discussed with a focus on its secondary symptoms and practical solutions to mitigate these risks, thereby ensuring a safer and more productive manufacturing environment.
1Hasty Equipment Repairs:
During unplanned downtime, there is a tendency to rush equipment repairs to resume production quickly. This haste can result in incomplete or improper repairs, leading to equipment malfunctions and accidents. For example, skipping steps in the repair process or using substandard parts to save time can compromise the integrity of the machinery, creating hazardous conditions for operators and maintenance personnel.
Mitigation: Implementing a rigorous repair protocol and ensuring that all repairs are thoroughly checked before resuming operations can mitigate this risk. Training maintenance personnel to handle repairs efficiently and safely is also crucial.
2Improperly Executed Lockout/Tagout Procedures:
In a rush to get equipment back online, workers may skip or improperly execute lockout/tagout (LOTO) procedures. These procedures are critical for ensuring that machinery is safely de-energized during maintenance. Failure to properly lock out machinery can result in accidental startup, which can cause severe injuries or fatalities.
Mitigation: Regular training and audits of LOTO procedures can ensure compliance. Creating a culture of safety where proper procedures are non-negotiable helps maintain adherence even under pressure.
3Bypassing Safety Interlocks:
Workers might bypass safety interlocks designed to prevent machinery from operating in unsafe conditions to save time. This can lead to severe accidents and injuries, as these interlocks are critical for ensuring machinery only operates when all safety conditions are met. For example, bypassing a guard interlock on a press machine could result in a serious injury if the machine is activated while an operator’s hand is in a dangerous position.
Mitigation: Reinforcing the importance of safety interlocks through training and strict enforcement of safety protocols can prevent bypassing. Using automated systems to monitor and enforce interlock usage can also be effective.
4Lack of Clear Communication During Downtime Recovery:
Unplanned downtime can lead to chaotic recovery efforts, where a lack of clear communication results in misunderstandings and mistakes that compromise safety. For example, if maintenance crews and production staff are not aligned on repair schedules and safety procedures, there is a higher risk of accidents due to miscommunication or assumptions.
Mitigation: Establishing clear communication protocols and digital tools for real-time updates can improve coordination during downtime recovery. Regular drills and simulations can also prepare teams for efficient and safe responses. Implementing a centralized communication platform where all stakeholders can access real-time updates ensures everyone is on the same page.
5Use of Untrained Personnel for Quick Fixes:
To expedite recovery, untrained personnel might be called upon to perform tasks they are not qualified for, increasing the risk of accidents and errors. For instance, asking a machine operator to perform maintenance tasks they are not trained for can result in improper repairs or unsafe equipment handling.
Mitigation: It is essential to ensure that only trained and qualified personnel are involved in recovery efforts. Cross-training employees can provide a larger pool of skilled workers to draw from during emergencies. A clear policy defining which tasks require specific training and certification can prevent unqualified personnel from performing dangerous tasks.
6Skipping Safety Audits to Save Time:
In the aftermath of unplanned downtime, safety audits might be skipped to save time and hasten the return to normal operations. This oversight can lead to unresolved safety issues and future incidents, as potential hazards that would have been identified during an audit remain unaddressed.
Mitigation: Incorporating safety audits as a mandatory step in the recovery process ensures that all potential hazards are addressed. Streamlining audit processes with checklists and digital tools can make them quicker without compromising thoroughness. Creating a culture where safety audits are considered integral to recovery can reinforce their importance. Regularly reviewing and updating audit protocols to ensure they are efficient and comprehensive can help maintain their effectiveness while minimizing downtime.
7Ignoring Minor Safety Infractions:
Minor safety infractions may be overlooked during the rush to resume production, leading to a culture where small lapses are tolerated. This eventually results in major accidents. For example, ignoring a minor spill because it seems insignificant can lead to a slip-and-fall accident later.
Mitigation: Emphasizing the importance of addressing all safety infractions, regardless of size, helps maintain a strong safety culture. Regular training and a zero-tolerance policy for safety violations can reinforce this. Encouraging employees to report all safety concerns, no matter how minor, and ensuring that these reports are taken seriously and acted upon can prevent small issues from escalating..
8Increased Use of Temporary Fixes:
Temporary fixes may be implemented to quickly get operations back on track, which can lead to recurring issues and potential safety hazards. For example, using duct tape to secure a loose wire instead of properly repairing it can create an electrical hazard.
Mitigation: While temporary fixes might be necessary, they should be accompanied by a plan for permanent solutions. Documenting temporary fixes and scheduling timely follow-up repairs can mitigate long-term risks. Ensuring that all temporary fixes are marked and communicated to relevant personnel can prevent misunderstandings and address these issues promptly.
9Slip and Trip Hazards Due to Cluttered Workspaces:
Unplanned downtime often results in hurried activities and cluttered workspaces, increasing the risk of slip and trip hazards. For instance, tools and materials left out of place during a rapid repair effort can create obstacles and increase the likelihood of accidents.
Mitigation: Regular housekeeping practices can reduce these risks by maintaining a clean and organized workspace. Implementing a 5S system (Sort, Set in order, Shine, Standardize, Sustain) can help keep workspaces safe and orderly. Regular inspections and audits of workspaces can identify potential hazards and ensure they are addressed promptly. Providing training on proper housekeeping practices and emphasizing their importance in maintaining a safe working environment can reinforce good habits and reduce the risk of accidents.
10Improper Handling of Hazardous Materials:
The rush to recover from unplanned downtime can lead to improper handling and storage of hazardous materials, increasing the risk of spills, exposures, and accidents. Failing to properly label or secure hazardous chemicals can result in dangerous leaks or unintended reactions.
Mitigation: It is critical to ensure that all hazardous materials are handled according to strict safety protocols, even during downtime recovery. Regular training and clear labeling can help maintain safe practices. Implementing a robust inventory management system for hazardous materials can provide visibility into their location and status, ensuring they are stored and handled correctly. Regular audits of hazardous materials and their storage areas can identify potential issues and ensure compliance with safety protocols.
Conclusion for Manufacturing Leadership
Unplanned downtime significantly increases safety risks in manufacturing, with far-reaching consequences that go beyond immediate disruptions. Safety risks can manifest in various ways, such as hasty equipment repairs, improperly executed lockout/tagout procedures, and the use of untrained personnel for quick fixes. These scenarios not only compromise the safety of workers but also lead to decreased productivity and efficiency.
Implementing strategies like preventive maintenance ensures that machinery is regularly checked and serviced, reducing the likelihood of unexpected breakdowns. Predictive analytics can help anticipate equipment failures before they occur, allowing for planned maintenance activities that do not disrupt the workflow. Strong supplier relationships and clear communication channels are crucial for coordinating recovery efforts and maintaining trust, even during periods of downtime. Optimizing inventory management ensures that materials are stored and handled correctly, reducing the risk of hazardous incidents.
Creating a culture where safety is prioritized, even under the pressure of downtime recovery, is essential. Regular training, clear communication protocols, and the enforcement of safety procedures can help maintain a safe working environment. By focusing on these areas, companies can mitigate the safety risks associated with unplanned downtime and enhance overall productivity.
How POWERS Can Help
At POWERS, we specialize in enhancing manufacturing productivity through our unique approach, “Operationalizing Your Culture.” We work directly with your leadership to align organizational culture with behaviors and skills that drive higher productivity and efficiency. Our expertise in root cause analysis, including methods like Fault Tree Analysis (FTA), ensures we identify and address the underlying issues leading to unplanned downtime.
By partnering with POWERS, you can expect measurable improvements in safety and productivity. Our hands-on approach ensures that our solutions are sustainable and deliver a significant return on investment. From developing preventive maintenance schedules to optimizing your supply chain and inventory management, POWERS provides tailored strategies that address your organization’s specific challenges.
With POWERS by your side, you can transform unplanned downtime from a productivity drain into an opportunity for growth and improvement, creating a safer, more resilient manufacturing environment. For more insights and resources on managing unplanned downtime and boosting productivity, visit our website and stay tuned for the next installment in The Unplanned Downtime Mastery Series.
- Speak to an Expert: Call +1 678-971-4711 to discuss your specific challenges and goals.
- Email Us: Get tailored insights by emailing info@thepowerscompany.com
- Request an Assessment: Use our online contact form, and one of our expert manufacturing consultants will reach out to schedule an in-depth analysis of your operations.
Continue Reading from this Mastery Series
- Part 1 – The Financial Burden of Breaking Down
- Part 2 – Eroding Maintenence Leading to Eroding Margins
- Part 3 – How Disrupted Production Leads to Unhappy Customers
- Part 4 –How Production Stoppages Can Break Your Supply Chain
- Part 5 – How Breakdowns Can Lead to Safety Shortcomings
- Part 6 – How Equipment Failures Drain Employee Drive
- Part 7 – How Constant Breakdowns Lead to Spiraling Maintenance Costs
- Part 8 – How Lost Production Time Leads to Lower Competitive Edge
- Part 9 – How Shop Floor Stoppages Lead to Regulatory Pitfalls
- Part 10 – How Missed Production Uptime Means Missed Opportunities