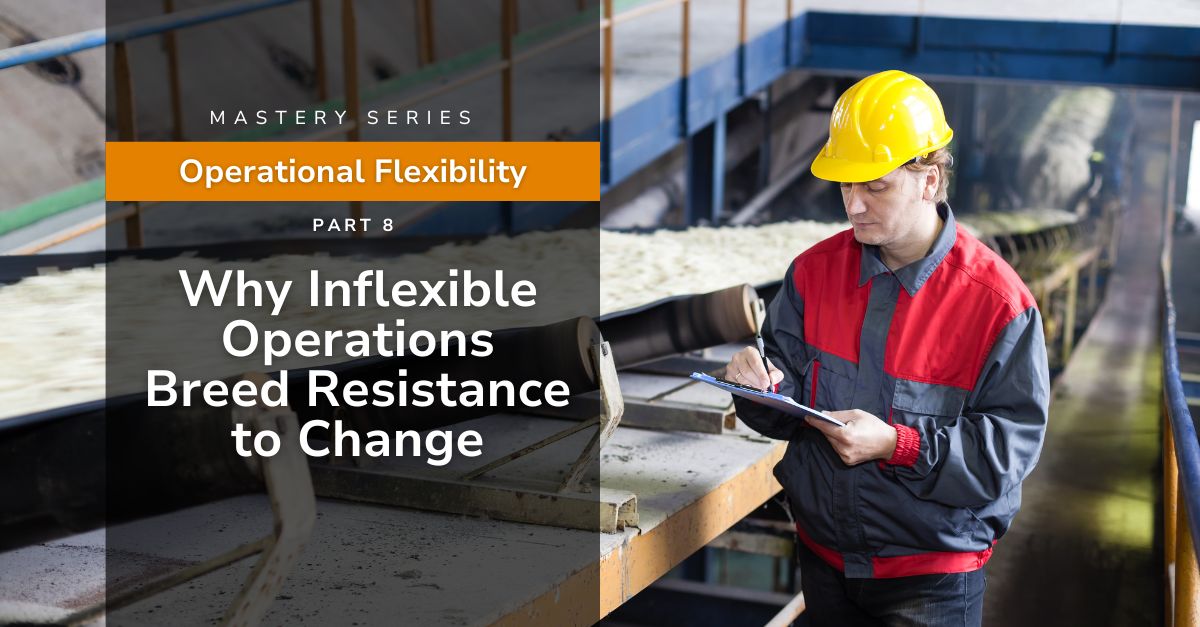
Resistance to change is one of the most significant challenges faced by organizations with inflexible operations.
While its direct impacts—such as delayed project implementation or employee pushback—are easy to recognize, the secondary symptoms it produces often go unnoticed, quietly undermining performance.
For instance, an inflexible organization may struggle to adapt its workflows to accommodate updated safety regulations. Employees accustomed to established practices might resist changes in equipment usage or documentation requirements, leading to inconsistent compliance across teams. This resistance risks regulatory penalties and results in inefficient workarounds and increased inspection times. These secondary symptoms, stemming from resistance to change, highlight how operational inflexibility creates barriers to seamless adaptation, even in areas critical to workplace safety and efficiency.
Inflexible operations amplify these challenges by fostering a culture where routine is prioritized over responsiveness. Without systems and processes designed to adapt quickly, resistance to change becomes embedded in the organization, making it harder to implement improvements or respond to external demands.
In Part 8 of the Risk of Rigidity Mastery Series we explores the less visible but equally damaging consequences of resistance to change. It focuses on how these secondary symptoms arise from inflexible operations and identifies actionable strategies to mitigate their impact. Through these insights, organizations can better prepare to align their operational practices with the demands of a dynamic manufacturing environment.
1Increased Pushback During Cross-Functional Collaboration Efforts:
Cross-functional collaboration is essential for breaking down silos and driving innovation, but inflexible operations often breed resistance when new collaboration efforts are introduced. Team members accustomed to rigid processes may view collaboration as an unwelcome disruption, leading to pushback. This creates delays in decision-making, misalignment in goals, and a lack of cohesion across departments, ultimately resulting in missed opportunities for improvement.
For example, a manufacturing team might resist collaborating with sales on demand forecasting, perceiving it as outside their domain. This hesitation leads to mismatched production schedules and inefficiencies in meeting customer demands.
Mitigation: Encouraging collaboration begins with fostering a shared sense of purpose. Implement cross-functional training programs that highlight the benefits of diverse perspectives and the value of collaboration in achieving company goals. Establish clear, documented processes for collaboration, supported by leadership endorsement, to reduce uncertainty and opposition. Regular alignment meetings where teams share progress and successes can help mitigate resistance and create buy-in.
2Overreliance on Informal, Outdated Knowledge-Sharing Practices:
When knowledge-sharing relies on informal or outdated practices, it creates inefficiencies and amplifies resistance to modern approaches. Verbal instructions, handwritten notes, or tribal knowledge—informal expertise passed between employees—can lead to inconsistent outcomes and hinder problem-solving, particularly when key personnel are unavailable. As a result, onboarding new hires becomes slower and error-prone, and teams struggle to adapt to changes without a reliable knowledge base.
Mitigation: A formalized knowledge management system is critical for overcoming this challenge. Digitize key operational procedures, guidelines, and best practices into a central repository accessible to all employees. Encourage team members to contribute to this knowledge base by incentivizing participation. Provide training on utilizing the system effectively and regularly update the content to keep it relevant. Organizations can improve efficiency and reduce resistance to process changes by integrating modern knowledge-sharing practices into daily workflows.
3Reduced Alignment Between Shop Floor Activities and Strategic Goals:
Resistance to change often stems from a lack of understanding about how individual tasks contribute to broader organizational goals. This disconnect leaves employees feeling unmotivated and disengaged, resulting in misaligned priorities on the shop floor. Without clarity, teams focus solely on routine activities, neglecting strategic initiatives that drive long-term success.
For example, a production team may prioritize completing their immediate tasks over experimenting with new efficiency-improving methods, assuming these efforts are unrelated to their core responsibilities.
Mitigation: Bridge this gap by communicating strategic goals regularly through visual management tools like dashboards, posters, or team huddles. Use relatable examples to illustrate how shop-floor activities directly impact organizational success. Establish key performance indicators (KPIs) that link individual performance to company objectives and provide feedback to reinforce alignment. When employees see how their roles contribute to the bigger picture, they are more likely to embrace change.
4Growing Disparity Between Legacy Systems and Market Demands:
Legacy systems can become a crutch in inflexible operations, fostering resistance to upgrades that better align with market demands. Employees accustomed to outdated systems may perceive new technologies as unnecessary or disruptive, causing hesitation or outright opposition. This disparity reduces efficiency and prevents the organization from keeping up with competitors adopting more agile solutions.
Mitigation: Begin modernization efforts by involving employees in the decision-making process. Solicit their input when evaluating new systems and emphasize how these upgrades address existing pain points, such as long processing times or frequent errors. Provide comprehensive training and phased rollouts to minimize disruption. Highlight measurable benefits through case studies or pilot program results to build trust and enthusiasm for the transition.
5Mismanagement of New Vendor Relationships Requiring Process Changes:
Resistance to change also impacts external relationships, particularly with new vendors that require process adjustments. Mismanagement of these changes leads to delays, quality issues, and strained partnerships, creating a ripple effect across operations. Teams may resist adopting vendor-specified workflows, arguing they conflict with established practices.
Mitigation: Design a structured vendor onboarding process that clearly outlines expectations and required changes. Involve cross-functional teams in planning to ensure alignment and prepare employees for transitions. Provide training on vendor-specific procedures and establish open lines of communication with vendors and internal teams to address concerns promptly. A proactive approach fosters smoother integration and minimizes disruptions.
6Declining Team Cohesion Due to Unresolved Conflicts About New Initiatives:
New initiatives often spark internal conflicts, particularly when team members perceive them as threats to established norms. If these conflicts go unresolved, they erode trust, reduce team cohesion, and create an environment of skepticism toward future changes. This dynamic is especially harmful in collaborative settings, where strong interpersonal relationships are critical for success.
Mitigation: Effective conflict resolution begins with transparency and open communication. Create opportunities for employees to voice concerns through focus groups or anonymous surveys. Use this feedback to tailor change initiatives to address specific pain points. Team-building exercises that emphasize trust and collaboration can also help rebuild cohesion. Leadership should model adaptability by visibly supporting and participating in new initiatives.
7Persistent Use of Inefficient Manual Processes:
Manual processes, though familiar, often remain entrenched due to resistance to automation. Employees may fear job displacement, struggle with steep learning curves, or prefer the status quo. This persistence reduces productivity, increases the likelihood of errors, and slows responsiveness to changing demands.
Mitigation: Approach automation as an enhancement rather than a replacement for human labor. Highlight tasks where automation can reduce repetitive strain and free up employees for higher-value activities. Provide hands-on training to demystify new technologies and offer ongoing support to address challenges. Gradual implementation—starting with the most critical pain points—helps employees adapt and builds confidence in the benefits of automation.
8Frequent Delays in Rolling Out Continuous Improvement Initiatives:
Resistance to change frequently manifests as delays in implementing continuous improvement initiatives. Employees may perceive these initiatives as unnecessary or disruptive, leading to half-hearted participation or outright refusal. This resistance undermines the intended benefits, leaving inefficiencies unaddressed and progress stagnant.
Mitigation: Foster a culture of continuous improvement by actively involving employees in the development and rollout of initiatives. Use pilot programs to demonstrate tangible benefits and celebrate early successes to build momentum. Communicate the long-term value of continuous improvement, emphasizing how it benefits employees and the organization. Providing adequate resources and time for adoption ensures smoother implementation.
9Poor Adaptability to Fluctuating Customer Expectations:
Inflexible operations struggle to meet shifting customer expectations, particularly when resistance to change slows the adoption of new strategies or technologies. This inability to adapt results in delays, lost business, and diminished customer trust, compounding operational inefficiencies.
Mitigation: Develop flexible scheduling and production systems, such as just-in-time (JIT) manufacturing, to better align with fluctuating demands. Gather customer feedback regularly and incorporate it into decision-making processes. Establish clear channels for communicating these changes to employees, ensuring they understand their role in meeting customer needs.
10Fragmented Understanding of Company Objectives Among Shop Floor Teams:
Resistance to change often creates a fragmented understanding of company objectives, with shop floor teams prioritizing short-term tasks over strategic goals. This disconnect leads to inefficiencies, reduced engagement, and difficulty achieving long-term success.
Mitigation: Enhance communication through visual tools like progress dashboards or infographics that tie individual contributions to company objectives. Conduct regular training sessions to clarify goals and update teams on progress. Reinforce alignment through consistent feedback and recognition programs, helping employees feel invested in the organization’s success.
The Bottom Line For Operations Leaders
Resistance to change is a complex challenge that, when left unaddressed, can quietly erode productivity and stall growth. The secondary symptoms—such as increased pushback during cross-functional efforts, overreliance on outdated knowledge-sharing practices, and persistent use of inefficient manual processes—are all rooted in operational inflexibility. By understanding and addressing these issues, organizations can overcome resistance and create a culture of adaptability and resilience.
This requires modernized systems, proactive leadership, and clear alignment between daily operations and strategic goals.
How POWERS Can Help
At POWERS, we specialize in identifying and addressing hidden inefficiencies that inhibit operational flexibility and productivity. Our comprehensive approach guides manufacturers in transforming rigid systems into adaptable operations that drive sustainable growth.
Our Digital Production System (DPS) offers unparalleled support for manufacturers striving to optimize their operations in today’s fast-paced environment. Combining decades of expertise with the latest AI-powered technology, DPS empowers manufacturers with real-time data, actionable insights, and advanced tools to stay ahead of the curve.
Here’s how POWERS and DPS can elevate your operations:
- Comprehensive Operational Insight: Gain a 360-degree view of your manufacturing processes with intuitive dashboards that uncover hidden inefficiencies.
- Seamless Integration: Connect legacy systems with modern technology to streamline workflows and align shop floor activities with strategic objectives.
- Proactive Problem Solving: Use AI-driven insights to identify and address potential bottlenecks before they disrupt production.
- Optimized Resource Allocation: Maximize the utilization of labor, equipment, and materials to improve efficiency and reduce waste.
- Empowered Teams: Equip your workforce with the tools and information needed to collaborate effectively and embrace change confidently.
POWERS doesn’t just help you overcome resistance to change; we enable you to unlock the full potential of your manufacturing operations. By fostering a culture of adaptability and leveraging cutting-edge tools like DPS, your organization can transform resistance into resilience and inefficiency into innovation.
Ready to enhance your operational flexibility and drive measurable results? Contact our team today to learn how POWERS can partner with you to achieve sustainable productivity improvements.
- Speak to an Expert: Call +1 678-971-4711 to discuss your specific challenges and goals.
- Email Us: Get tailored insights by emailing info@thepowerscompany.com
- Request an Assessment: Use our online contact form, and one of our expert manufacturing consultants will reach out to schedule an in-depth analysis of your operations.
Continue Reading from this Mastery Series
- Part 1 – How Stubborn Systems Sabotage Competitive Advantage
- Part 2 – Unadaptable Workflows Lead to Talent Turnover
- Part 3 – Why Inflexible Operations Fail to Innovate
- Part 4 – How Operational Inflexibility Undermines Your Resilience
- Part 5 – When Rigid Operations Cause Decision-Making Bottlenecks
- Part 6 – How Inflexibility Obstructs Collaboration
- Part 7 – How Inflexible Operations Sabotages Scaling Initiatives
- Part 8 – How Inflexible Operations Fuel Resistance to Change
- Part 9 – How Inflexible Operations Leave You Vulnerable to Cyber Threats
- Part 10 – Why Operational Inflexibility Undermines Your Brand Reputation