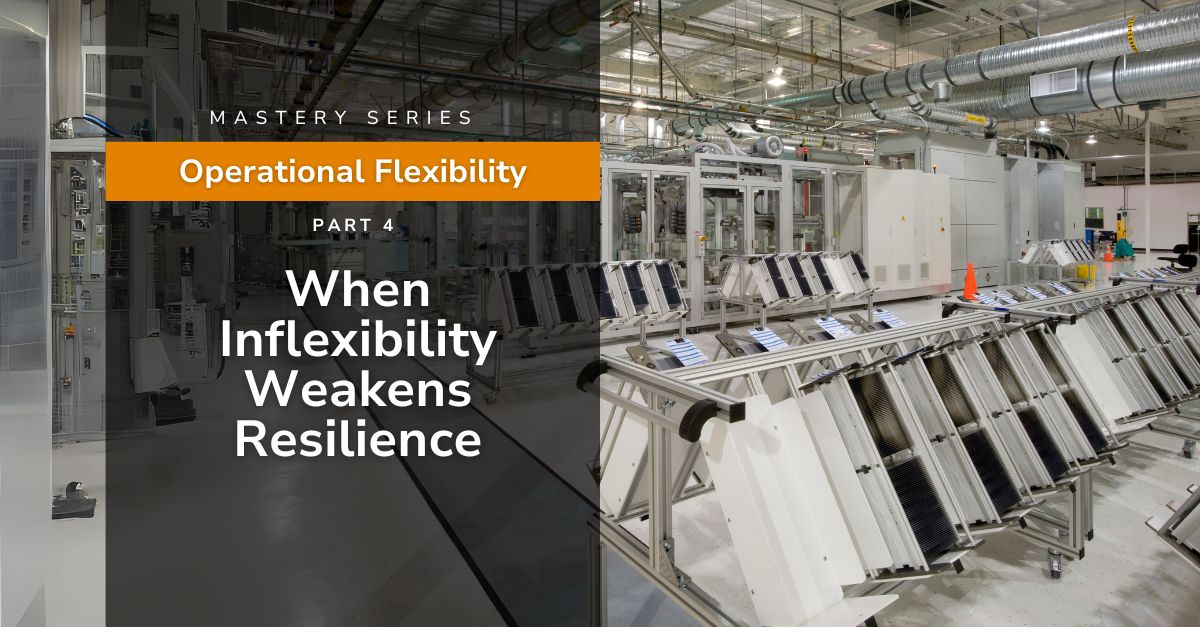
In manufacturing, operational rigidity often appears manageable until unforeseen disruptions expose deeper challenges.
These vulnerabilities due to inflexibility aren’t always dramatic; they’re often subtle, manifesting as inefficiencies that grow over time and eventually undermine productivity.
One overlooked example is the failure to maintain a robust spare parts inventory strategy. Many inflexible systems adhere to static procurement plans, assuming uniform demand for replacement components. This rigidity can result in critical shortages during periods of heightened equipment wear, such as when production ramps up in response to seasonal demand. Without the flexibility to adjust inventory planning, managers face unplanned downtime as equipment idles, waiting for parts to arrive. This secondary symptom of inflexible operations highlights the cascading effects of seemingly minor inefficiencies on overall performance.
When operational structures lack adaptability, these hidden weaknesses compound, exposing a business to disruptions that are harder to recover from. Whether it’s prolonged lead times, delayed decision-making, or fragmented collaboration, these issues often stem from the same root cause: inflexible systems that fail to evolve with the organization’s needs. Addressing these limitations isn’t just about improving efficiency—it’s about safeguarding your ability to compete and thrive in a dynamic market. This post will explore ten specific ways that operational inflexibility increases vulnerability to disruption and offer practical solutions for creating a more resilient operation.
1Dependency on Static Job Roles:
Relying on static job roles creates a highly specialized but inflexible workforce, making it difficult to adapt to unexpected disruptions. When tasks are rigidly assigned, employees cannot easily step into different roles, causing critical functions to stall during emergencies. This dependency delays recovery and results in overburdened key personnel, increasing stress and the likelihood of burnout. Over time, this creates a fragile operational system vulnerable to even minor disruptions.
Mitigation: Organizations should implement a robust cross-training program that empowers employees to handle multiple responsibilities to overcome this challenge. By rotating roles and creating dynamic job assignments, businesses can foster a versatile workforce capable of stepping into critical roles during disruptions. Additionally, maintaining updated role matrices ensures management can quickly allocate resources where they are most needed, reducing bottlenecks and enhancing overall agility.
2Underutilization of Existing Automation Capabilities:
Automation systems are often underutilized due to poor integration with workflows or a lack of user knowledge. During operational disruptions, these systems could play a pivotal role in stabilizing processes, yet they are sidelined due to insufficient understanding or outdated configurations. This results in wasted investment and missed opportunities to streamline recovery efforts, prolonging downtime and exacerbating inefficiencies.
Mitigation: A comprehensive audit of automation capabilities can identify underused functions and areas for optimization. Coupling this with targeted training ensures employees can fully utilize automation tools during routine and disruptive scenarios. Regular software updates and integrating automation systems with analytics platforms can enhance responsiveness, allowing organizations to pivot quickly and effectively during operational setbacks.
3Prolonged Recovery Times After Operational Disruptions:
Rigid and recovery protocols due to inflexibility often fail to account for disruptions’ dynamic nature. When recovery processes are overly standardized, they cannot be adjusted based on the disruption’s scale or specific impact areas. This results in extended downtime and missed opportunities for a quicker return to normal operations, creating significant productivity losses and potential reputational damage.
Mitigation: Developing flexible recovery protocols that prioritize critical operations and allocate resources dynamically can significantly reduce downtime. Scenario-based training exercises can help teams practice responding to various types of disruptions, enabling them to act decisively under pressure. By integrating recovery planning into overall operational strategies, organizations can minimize the impact of disruptions and maintain customer trust.
4Misalignment Between Production Schedules and Market Demands:
Rigid production schedules fail to adapt to rapid changes in market demand, resulting in overproduction, stockpiling, or lost sales opportunities. This misalignment creates inefficiencies across the supply chain, forcing organizations to store unsold inventory or scramble to meet unexpected demand spikes, increasing costs and eroding profitability.
Mitigation: Implementing a demand-driven production model supported by advanced analytics can address this issue. Predictive tools that use real-time market data enable production schedules to align with actual demand, reducing excess inventory and minimizing stockouts. Regularly reviewing production plans and incorporating feedback loops ensures continuous alignment with market needs, enhancing agility and customer satisfaction.
5Inefficient Utilization of Worker Skillsets in Critical Moments:
Organizations often fail to deploy their workforce effectively during disruptions, leading to inefficiencies and wasted potential. Skill mismatches can leave critical areas under-resourced while less urgent tasks receive unnecessary attention. This imbalance increases the duration of disruptions and contributes to worker frustration and disengagement.
Mitigation: Workforce management software can help allocate tasks based on employees’ skills and availability in real-time. Regular skill assessments and dynamic scheduling systems ensure workers are deployed where they are most needed. Furthermore, creating a culture of continuous learning helps employees expand their skill sets, increasing their ability to contribute meaningfully during critical moments.
6Difficulty Integrating External Partnerships Into Workflows:
External partnerships, such as those with suppliers or contractors, are critical during disruptions but often poorly integrated into workflows. Inflexible operations struggle to communicate effectively with these partners, leading to delays, misaligned priorities, and wasted resources during critical periods.
Mitigation: Adopting cloud-based collaboration tools can streamline communication with external partners, ensuring all parties are aligned during disruptions. Establishing standardized procedures for joint operations, such as shared dashboards or automated notifications, fosters transparency and improves coordination. These measures enable organizations to leverage their partnerships effectively, even under challenging circumstances.
7Delayed Incorporation of Real-Time Market Data Into Operations:
Organizations that rely on outdated or static data cannot adapt quickly to market changes, leaving them vulnerable during disruptions. Delayed decision-making based on inaccurate information compounds the effects of operational setbacks, resulting in missed opportunities and prolonged inefficiencies.
Mitigation: Investing in IoT-enabled devices and advanced analytics platforms allows organizations to incorporate real-time data into their operations. Businesses can make faster, more informed decisions that mitigate disruption impacts by automating data collection and analysis. Training decision-makers to interpret and act on this data ensures the organization can remain agile and responsive.
8Fragmented Data Sharing Between Departments:
When departments operate in silos, fragmented data sharing leads to inconsistent decision-making and reduced responsiveness during disruptions. Teams working with incomplete or outdated information may prioritize conflicting objectives, exacerbating inefficiencies and prolonging downtime.
Mitigation: A centralized data-sharing platform can bridge communication gaps between departments. Tools like ERP (Enterprise Resource Planning) systems ensure that all teams can access accurate, real-time information. Regular interdepartmental reviews and alignment meetings strengthen collaboration, creating a unified approach to handling disruptions.
9Higher Likelihood of Errors During Rapid Shifts in Production Priorities:
When production priorities shift rapidly, rigid workflows and inadequate communication increase the likelihood of errors. These mistakes can range from quality control issues to resource misallocation, further complicating recovery efforts and damaging customer trust.
Mitigation: Standardized protocols for shifting production priorities and clear communication channels reduce the risk of errors. Implementing digital workflow management tools can help streamline transitions, ensuring that all stakeholders are informed and aligned during priority changes.
10Limited Ability to Experiment With Innovative Product Prototypes:
Inflexible operations rarely allocate resources for experimentation, stifling innovation and limiting competitiveness. This rigidity becomes particularly problematic during disruptions when innovative solutions could help overcome challenges and seize new opportunities.
Mitigation: Establishing dedicated innovation teams and agile development cycles creates an environment where experimentation is encouraged. Allocating resources specifically for prototyping and iterative testing enables organizations to remain competitive and responsive to market changes, even during disruptions.
The Bottom Line For Operations Leaders
Operational inflexibility doesn’t just lead to inefficiencies—it exposes vulnerabilities that compromise your ability to respond to disruptions and maintain productivity. Whether it’s prolonged lead times, bottlenecks in decision-making, or a lack of adaptive inventory strategies, these issues can silently erode your competitive edge. Addressing these challenges requires more than quick fixes; it calls for a strategic approach to building flexibility in your operations.
Our solutions are grounded in decades of expertise and a commitment to delivering measurable, sustainable improvements.
Ready to Transform Your Operations?
POWERS goes beyond traditional consulting to offer cutting-edge tools and strategies that empower your organization to thrive in today’s demanding manufacturing environment. With DPS, our Digital Production System, you can access AI-driven insights and real-time data that unlock new productivity levels and operational resilience.
Here’s how POWERS and DPS can help you enhance flexibility and drive performance:
- Real-Time Insights: Leverage intuitive dashboards for up-to-the-minute production data, enabling faster responses to disruptions.
- Proactive Maintenance: Reduce downtime with predictive analytics that identifies potential equipment failures before they occur.
- Scalable Solutions: Adapt quickly to changing demands with modular production tools and flexible resource allocation strategies.
- Enhanced Team Collaboration: Break down silos with seamless data sharing and integrated communication tools that align your workforce.
- Smarter Decision-Making: Use advanced AI to forecast challenges, optimize production schedules, and align operations with strategic goals.
By partnering with POWERS, you’ll address the vulnerabilities of inflexible operations and create a resilient, future-proof manufacturing environment. Let us help you achieve sustainable growth, minimize risks, and maximize your productivity potential.
Contact us today to learn how POWERS and DPS can transform your operations into a model of efficiency, adaptability, and success.
- Speak to an Expert: Call +1 678-971-4711 to discuss your specific challenges and goals.
- Email Us: Get tailored insights by emailing info@thepowerscompany.com
- Request an Assessment: Use our online contact form, and one of our expert manufacturing consultants will reach out to schedule an in-depth analysis of your operations.
Continue Reading from this Mastery Series
- Part 1 – How Stubborn Systems Sabotage Competitive Advantage
- Part 2 – Unadaptable Workflows Lead to Talent Turnover
- Part 3 – Why Inflexible Operations Fail to Innovate
- Part 4 – How Operational Inflexibility Undermines Your Resilience
- Part 5 – When Rigid Operations Cause Decision-Making Bottlenecks
- Part 6 – How Inflexibility Obstructs Collaboration
- Part 7 – How Inflexible Operations Sabotages Scaling Initiatives
- Part 8 – How Inflexible Operations Fuel Resistance to Change
- Part 9 – How Inflexible Operations Leave You Vulnerable to Cyber Threats
- Part 10 – Why Operational Inflexibility Undermines Your Brand Reputation