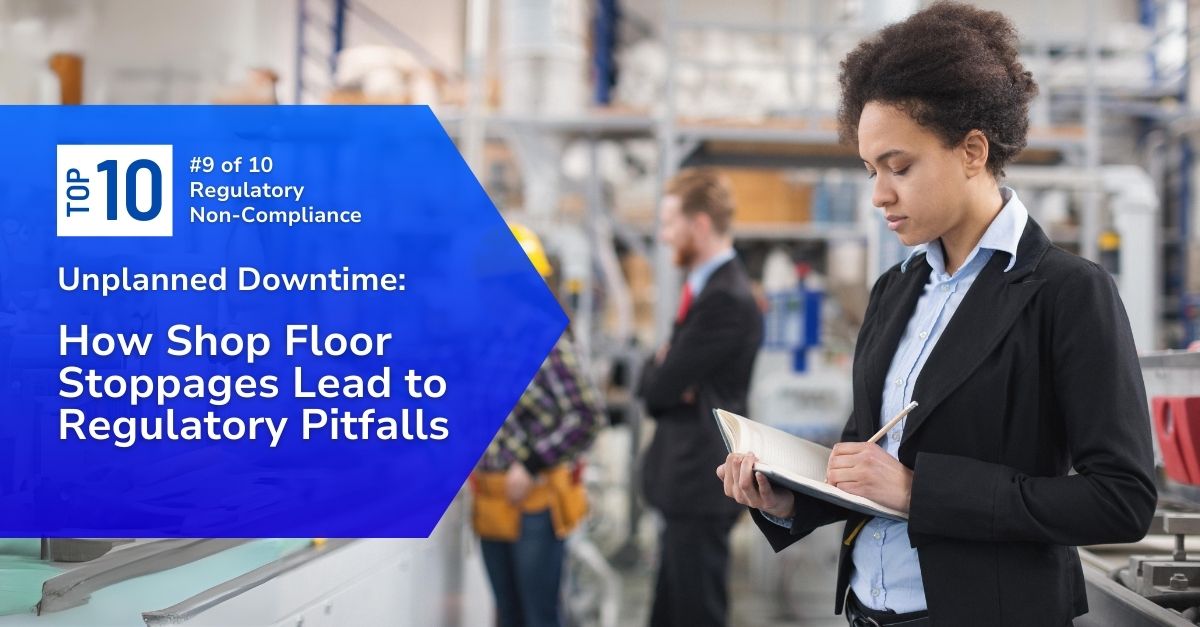
Recovering from unplanned downtime presents significant challenges that extend far beyond the immediate disruption.
Regulatory non-compliance is a major and often overlooked consequence, which can result in severe penalties, legal challenges, and long-term operational setbacks.
For instance, consider hazardous materials management. Unplanned downtime can disrupt the carefully scheduled disposal of hazardous waste, leading to improper storage and disposal practices. This mismanagement violates environmental regulations and poses serious health risks to employees and the surrounding community. The resulting regulatory fines and clean-up costs further strain the company’s resources and divert attention away from productivity improvements.
Unplanned downtime can also derail the meticulous documentation processes required to maintain regulatory compliance. Without accurate records, manufacturers risk failing audits and inspections, leading to further compliance issues and potential shutdowns.
The following sections will explore the top 10 ways unplanned downtime leads to regulatory non-compliance. We’ll explore the specific secondary symptoms and their detrimental effects on productivity, providing real-world examples and practical mitigation strategies to help managers navigate these challenges effectively.
1Inadequate Documentation Processes:
During unplanned downtime, the focus shifts to immediate problem-solving, often leaving documentation by the wayside. This results in incomplete or inaccurate records, which is critical for regulatory compliance. Regulatory bodies require detailed logs of operations, maintenance, and incidents to ensure proper procedures are followed.
Mitigation: Implement a robust digital documentation system that automates the logging of key activities. Training staff to prioritize documentation, even during crises, ensures that records remain up-to-date. Regular audits of documentation practices can also help maintain accuracy and completeness.
2Lapsed Certifications for Specialized Equipment Operators:
Unplanned downtime can disrupt scheduled training and recertification programs. Operators of specialized equipment require regular certification to comply with regulatory standards. Lapsed certifications can lead to non-compliance, fines, and operational delays.
Mitigation: Establish a proactive certification management system that tracks expiry dates and schedules training sessions well in advance. Integrate this system with your HR platform to automate reminders and ensure continuous compliance.
3Delayed Safety Inspections:
Regular safety inspections are mandatory to ensure workplace safety and regulatory compliance. Unplanned downtime can postpone these inspections, leading to potential safety hazards and non-compliance issues.
Mitigation: Create a flexible inspection schedule that allows rescheduling without significant delays. Employing mobile inspection tools can streamline the process and ensure inspections are conducted timely, even during unexpected downtimes.
4Increased Risk of Fines and Penalties:
Non-compliance with regulatory standards often results in hefty fines and penalties. These financial burdens affect the bottom line and divert resources away from productivity-enhancing initiatives.
Mitigation: Invest in compliance management software that monitors regulatory changes and ensures all aspects of operations meet the required standards. Regular compliance training for employees can also minimize the risk of infractions.
5Backlog of Pending Document Revisions:
When downtime occurs, the urgency to get back online can cause a backlog in document revisions. Outdated standard operating procedures (SOPs) and maintenance logs can lead to non-compliance.
Mitigation: Implement a document management system that prioritizes and tracks revisions. Designate a compliance officer to oversee document updates and ensure they align with current regulatory standards.
6Improper Waste Disposal:
Unplanned downtime can disrupt waste disposal schedules, leading to improper disposal methods that violate environmental regulations. This not only results in non-compliance but also poses environmental hazards.
Mitigation: Develop a contingency waste management plan that includes alternative disposal methods during downtime. Regular training on proper disposal techniques ensures employees are prepared to handle waste correctly, even in emergencies.
7Insufficient Training for Employees:
Regular training is crucial for maintaining safety and operational standards compliance. Downtime can interrupt training schedules, leaving employees underprepared and increasing non-compliance risk.
Mitigation: Adopt e-learning platforms that allow employees to complete training modules remotely and on demand. This flexibility ensures continuous training regardless of operational disruptions.
8Failure to Meet Health and Safety Standards:
Health and safety standards are non-negotiable in manufacturing environments. Unplanned downtime can lead to deferred maintenance and inspections, increasing the risk of non-compliance with health and safety regulations.
Mitigation: Conduct regular risk assessments and update safety protocols to include contingency measures for downtime. Establish a safety committee to oversee compliance and address any gaps immediately.
9Increased Frequency of Workplace Accidents:
The chaos of unplanned downtime can lead to increased workplace accidents, which must be reported accurately to regulatory bodies. Failure to do so can result in severe penalties and non-compliance issues.
Mitigation: Implement a comprehensive incident reporting system that simplifies the employee process. Regular accident prevention and reporting training ensures that incidents are managed promptly and accurately.
10Incomplete Incident Reporting:
Accurate and complete incident reporting is essential for regulatory compliance. Unplanned downtime can lead to rushed or incomplete reports, compromising the integrity of safety records.
Mitigation: Develop a standardized reporting protocol with detailed guidelines on what information to capture. Utilizing digital reporting tools can streamline the process and ensure completeness.
Conclusion for Manufacturing Leadership
Regulatory non-compliance caused by unplanned downtime can significantly hinder productivity in manufacturing operations. Secondary symptoms, ranging from inadequate documentation processes to increased workplace accidents, create a web of challenges that managers must address to maintain smooth and compliant operations. Each of these issues not only affects compliance but also detracts from the overall productivity and efficiency of the manufacturing process.
Addressing these secondary symptoms requires a comprehensive approach that includes proper training, meticulous documentation, and effective management practices.
How POWERS Can Help
POWERS specializes in enhancing manufacturing productivity through tailored, results-based management consulting. Our unique approach aligns organizational culture with behaviors and skills that drive higher productivity and efficiency. We work directly with leadership to implement effective root cause analysis techniques and ensure sustainable improvements and measurable ROI.
Here are the ways POWERS can help improve productivity and ensure compliance:
- Implementing Comprehensive Training Programs: Ensure all employees receive continuous training to comply with regulatory standards.
- Developing Robust Documentation Systems: Automate and streamline documentation processes to maintain accuracy and completeness, even during downtime.
- Optimizing Certification Management: Track and manage certifications to ensure operators remain qualified and compliant.
- Enhancing Waste Management Practices: Establish contingency plans and training for proper hazardous waste disposal to avoid environmental non-compliance.
With POWERS’ hands-on approach and expertise in operational excellence, your organization can navigate the complexities of regulatory compliance and unplanned downtime, ensuring sustained productivity and a competitive edge in the market.
For more insights into mitigating unplanned downtime and its impacts, stay tuned for the next installment in our Unplanned Downtime Mastery Series. Contact POWERS today to learn how we can help transform your manufacturing operations.
- Speak to an Expert: Call +1 678-971-4711 to discuss your specific challenges and goals.
- Email Us: Get tailored insights by emailing info@thepowerscompany.com
- Request an Assessment: Use our online contact form, and one of our expert manufacturing consultants will reach out to schedule an in-depth analysis of your operations.
Continue Reading from this Mastery Series
- Part 1 – The Financial Burden of Breaking Down
- Part 2 – Eroding Maintenence Leading to Eroding Margins
- Part 3 – How Disrupted Production Leads to Unhappy Customers
- Part 4 –How Production Stoppages Can Break Your Supply Chain
- Part 5 – How Breakdowns Can Lead to Safety Shortcomings
- Part 6 – How Equipment Failures Drain Employee Drive
- Part 7 – How Constant Breakdowns Lead to Spiraling Maintenance Costs
- Part 8 – How Lost Production Time Leads to Lower Competitive Edge
- Part 9 – How Shop Floor Stoppages Lead to Regulatory Pitfalls
- Part 10 – How Missed Production Uptime Means Missed Opportunities