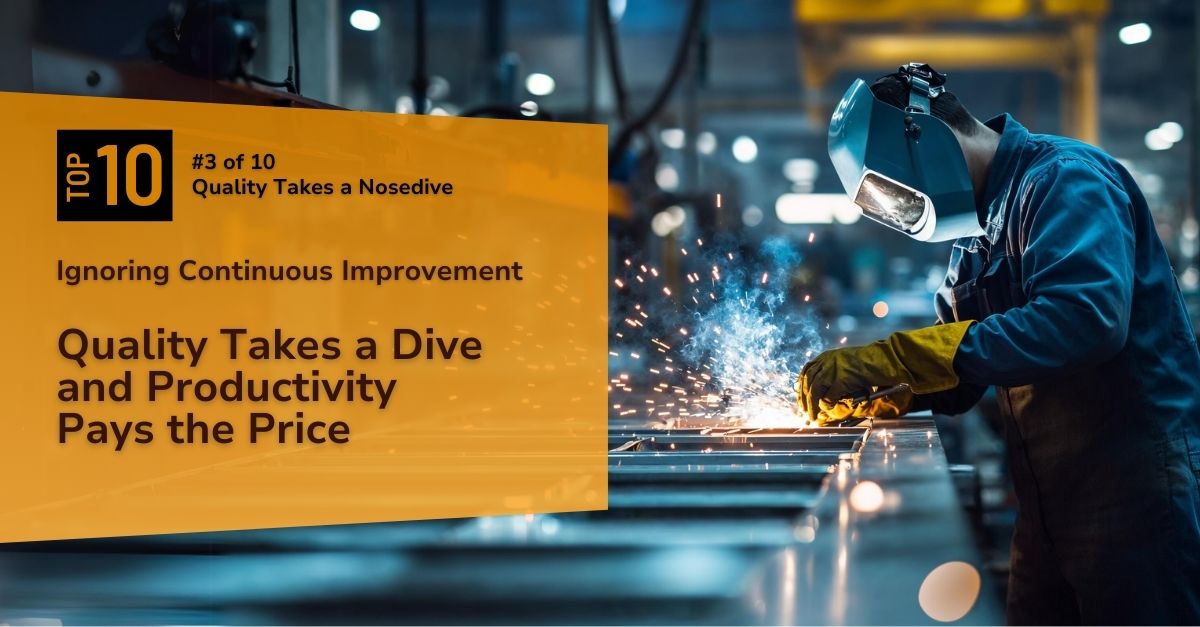
When continuous improvement is sidelined in manufacturing, product quality declines are inevitable.
The deterioration doesn’t manifest in obvious defects or missed deadlines but in more subtle and often overlooked ways that gradually erode the entire production process.
Consider a scenario where a manufacturer produces precision components for the aerospace industry. Over time, the company begins to neglect its continuous improvement processes, leading to a steady increase in micro-defects—imperfections so minute that they go unnoticed during standard inspections. While initially insignificant, these micro-defects start to cause minor but consistent alignment issues during the assembly of aircraft components. The result? Parts that require additional adjustments or, worse, fail during final testing. The cascading effect of these seemingly small quality lapses leads to increased downtime, higher production costs, and delayed deliveries.
This example highlights the less common but equally damaging consequence of ignoring Continuous Improvement: the slow, almost imperceptible decline in quality that escalates into significant operational challenges as quality standards slip, secondary symptoms such as increased rework, extended lead times, and unanticipated equipment failures emerge, each compounding the next. These issues are particularly insidious because they often fly under the radar until they’ve caused considerable damage to productivity and profitability.
The process becomes more reactive than proactive, with managers and teams constantly playing catch-up, addressing issues after they’ve already disrupted the workflow. The focus shifts from innovation and excellence to damage control, creating a cycle that becomes increasingly difficult to break. By delving into the top 10 ways this decline in quality manifests, we can better understand the true cost of neglecting Continuous Improvement and the critical steps needed to reverse the trend.
1Inconsistent Adherence to Quality Control Checkpoints:
When Continuous Improvement is overlooked, one of the first casualties is the consistency of quality control checkpoints. These checkpoints, designed to catch defects early in the process, become less rigorous and sporadic. The result is a production line that allows defects to slip through, leading to a higher incidence of rework and scrap. Over time, this inconsistency erodes trust in the process, making it difficult to maintain uniform product quality.
Mitigation Strategy: To counteract this, it’s crucial to establish a robust continuous improvement framework emphasizing regular auditing and calibration of quality control processes. Implementing automated inspection systems that provide real-time data can also help maintain consistency. Additionally, fostering a culture where employees are encouraged to report deviations ensures that issues are addressed promptly before they escalate into larger problems.
2Unnoticed Shifts in Critical-to-Quality (CTQ) Parameters:
Critical-to-quality (CTQ) parameters are the backbone of any manufacturing process, ensuring that products meet the required specifications. However, subtle shifts in these parameters often go unnoticed without continuous monitoring and improvement. While minor individually, these shifts can accumulate over time, leading to significant quality deviations that only become apparent after substantial rework is required.
Mitigation Strategy: Implementing statistical process control (SPC) tools can help continuously monitor CTQ parameters, allowing for early detection of any deviations. Training employees to recognize the importance of these parameters and providing them with the tools to monitor and report shifts can also contribute to maintaining the integrity of the production process.
3Growing Disparity Between Designed and Actual Product Specifications:
As Continuous Improvement efforts wane, the gap between designed and actual product specifications often widens. This disparity can stem from various sources, including worn-out machinery, inconsistent raw materials, or inadequate training. The product fails to meet customer expectations, leading to increased returns, warranty claims, and a damaged reputation.
Mitigation Strategy: To bridge this gap, it’s essential to regularly review and update production processes to align with the latest product specifications. This can be achieved by integrating regular feedback loops between the design and production teams, ensuring that any discrepancies are quickly identified and addressed. Additionally, investing in employee training and maintaining equipment can help reduce the variability contributing to this growing disparity.
4Amplified Risks of Cross-Contamination in Mixed-Product Lines:
In facilities where multiple products are manufactured on the same line, the absence of Continuous Improvement increases the risk of cross-contamination. This is particularly problematic in industries such as food and pharmaceuticals, where even trace amounts of contamination can have severe consequences. Neglecting continuous improvement means that cleaning protocols, changeover procedures, and equipment maintenance may not be adequately updated, leading to increased contamination risks.
Mitigation Strategy: To mitigate this risk, a Continuous Improvement approach should include rigorous validation of cleaning and changeover procedures. Implementing real-time monitoring systems that detect contamination early can also reduce the likelihood of cross-contamination. Moreover, ensuring that employees are trained in the latest protocols and understand the importance of adhering to them can help maintain high hygiene and product integrity standards.
5Over-reliance on Outdated Inspection Protocols:
When continuous improvement is not prioritized, inspection protocols often become outdated. These protocols may no longer reflect the complexities of modern manufacturing processes, leading to missed defects and substandard products reaching customers. An over-reliance on outdated methods also increases the likelihood of human error, further compromising quality.
Mitigation Strategy: To prevent this, it’s vital to regularly review and update inspection protocols to reflect the latest industry standards and technological advancements. Introducing automated inspection systems that use AI and machine learning can enhance accuracy and reduce the burden on human inspectors. Regular training sessions for quality inspectors ensure they are well-versed in the latest protocols and technologies.
6Inadequate Root Cause Analysis Leading to Recurring Defects:
Without a strong continuous improvement initiative, root cause analysis often becomes superficial, addressing symptoms rather than the underlying issues. This leads to recurring defects that not only waste resources but also frustrate both employees and customers. The lack of thorough analysis means the same problems resurface, disrupting production and eroding overall quality.
Mitigation Strategy: A robust root cause analysis framework is essential to prevent recurring defects. Tools such as the Five Whys, Fishbone Diagrams, and Failure Mode and Effects Analysis (FMEA) should be standard practice in any continuous improvement program. Ensuring that cross-functional teams conduct these analyses can provide diverse perspectives, leading to more effective solutions.
7Unstable Process Conditions Causing Unpredictable Product Outcomes:
Neglecting Continuous Improvement often results in unstable process conditions. Variations in temperature, pressure, or other critical factors can lead to unpredictable product outcomes, with some batches meeting quality standards while others do not. This instability affects product consistency and increases the likelihood of costly production stoppages.
Mitigation Strategy: Stabilizing process conditions requires a proactive approach to monitoring and control. Implementing advanced process control (APC) systems that use real-time data to adjust conditions can help maintain stability. Regular maintenance and equipment calibration are also crucial in ensuring process parameters remain within the desired range.
8Lack of Feedback Loops Resulting in Repeated Mistakes:
Without continuous feedback loops, mistakes on the shop floor will likely be repeated, leading to persistent quality issues. Employees may not be aware of the consequences of their actions, or there may be a disconnect between departments that prevents the sharing of crucial information. This lack of communication and feedback undermines the potential for continuous learning and improvement.
Mitigation Strategy: To establish effective feedback loops, it’s important to create a culture of open communication where employees are encouraged to share insights and report issues without fear of retribution. Regular debriefing sessions and cross-departmental meetings can facilitate the flow of information, ensuring that lessons learned are applied across the organization. Additionally, using digital platforms to track and analyze feedback can provide valuable insights for future improvements.
9Increased Tolerance Stack-Up Errors in Assemblies:
Tolerance stack-up errors occur when small deviations in individual components create significant defects in the final assembly. Without a continuous improvement approach, these errors are often overlooked until they become major issues, leading to costly rework and delays. The complexity of modern assemblies means that even minor variations can significantly impact product quality.
Mitigation Strategy: Mitigating tolerance stack-up errors requires precise manufacturing techniques and rigorous inspection protocols. Implementing Geometric Dimensionaling and Tolerance (GD&T) standards can help control variations and ensure that components fit together as intended. Additionally, using simulation tools to predict and address potential stack-up issues before production can reduce the risk of defects.
10Sporadic Misalignment in Supply Chain Quality Standards:
When Continuous Improvement is neglected, misalignments in supply chain quality standards become more frequent. Suppliers may not adhere to the same quality standards as the manufacturing facility, leading to inconsistencies in raw materials or components. This misalignment can result in a cascading effect, where defects introduced early in the supply chain are compounded as they move through production.
Mitigation Strategy: To address this, it’s essential to establish clear and consistent quality standards across the entire supply chain. Regular audits and assessments of suppliers can help identify and address any discrepancies. Developing strong partnerships with suppliers and involving them in continuous improvement can also lead to more consistent quality and better alignment with the manufacturer’s standards.
Conclusions for Operations Leaders
The consequences of neglecting Continuous Improvement in manufacturing extend far beyond just a decline in product quality. As standards slip, the effects infiltrate every aspect of the production process, leading to increased rework, longer lead times, and operational inefficiencies. These challenges undermine productivity and threaten a company’s competitive standing in the marketplace.
Our team specializes in helping organizations like yours revive their Continuous Improvement efforts, ensuring that quality issues are addressed before they become major problems. By partnering with POWERS, your business can unlock significant productivity gains and secure long-term success.
How POWERS Can Help
Our approach is designed to address both the immediate and underlying challenges that stem from neglecting Continuous Improvement:
- Strengthening Root Cause Analysis and Quality Control: POWERS enhances your root cause analysis processes and quality control systems, ensuring that defects are caught early and prevented from recurring.
- Stabilizing Process Conditions and Monitoring Key Parameters: We introduce advanced process control systems and Statistical Process Control (SPC) tools to maintain stable production conditions and closely monitor critical-to-quality (CTQ) parameters.
- Bridging the Gap Between Design and Production: Our team works with you to align your design and production processes, ensuring that the final product consistently meets or exceeds customer expectations.
- Aligning Supply Chain Standards: POWERS ensures that quality standards are consistent across your entire supply chain, reducing the risk of defects and improving overall product quality.
Focusing on these critical areas can help POWERS help your organization substantially improve quality and productivity. Don’t let the cost of neglecting Continuous Improvement weigh down your operations. Partner with POWERS to enhance your processes, maintain high standards of quality, and secure your place in the competitive manufacturing landscape.
- Speak to an Expert: Call +1 678-971-4711 to discuss your specific challenges and goals.
- Email Us: Get tailored insights by emailing info@thepowerscompany.com
- Request an Assessment: Use our online contact form, and one of our expert manufacturing consultants will reach out to schedule an in-depth analysis of your operations.
Continue Reading from this Mastery Series
- Part 1 – When Progress Takes a Break, it Leaves Your Productivity Stalled
- Part 2 – Profit Erosion in the Production Line
- Part 3 – Quality Takes a Dive and Productivity Pays the Price
- Part 4 – When Morale Breaks Down So Does the Shop Floor
- Part 5 – When Innovation Pauses, Your Production Line Follows
- Part 6 – How Customer Loyalty Slips Through Your Fingers
- Part 7 – When Your Slice of the Market Becomes a Crumb
- Part 8 – When Opportunities Slip Through the Cracks
- Part 9 – Safety Shortsights and Their Costly Consequences
- Part 10 – Growth and Adaptation Slows to a Crawl