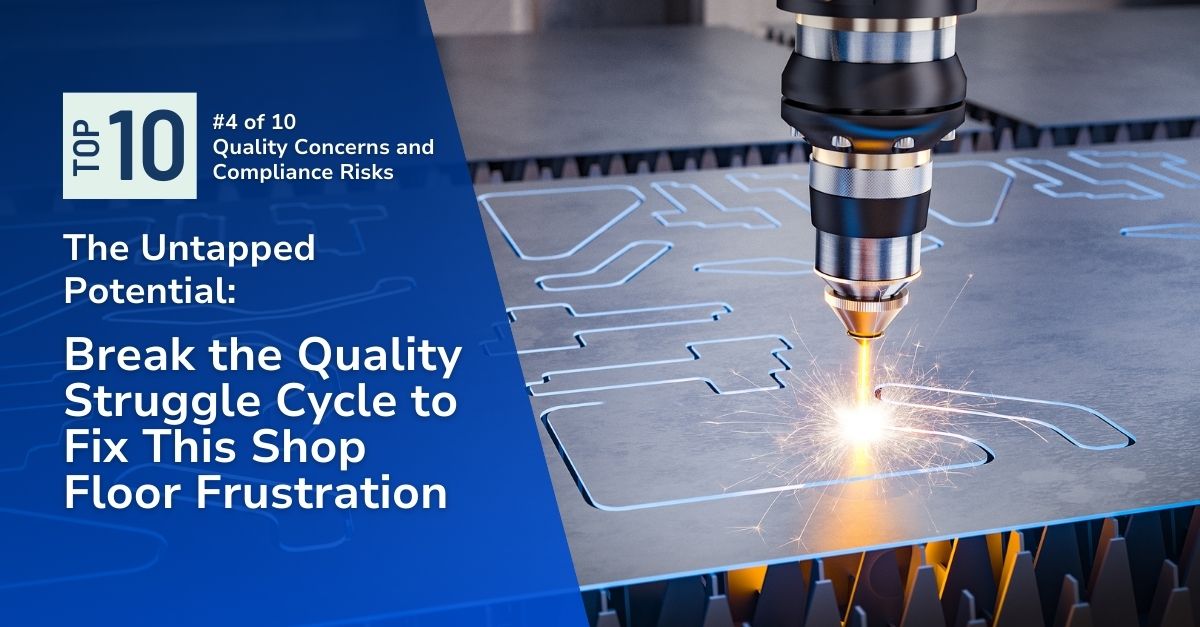
Tired of the endless treadmill? Feeling like your team is constantly sprinting, yet still falling short of targets? Sick of delayed shipments, equipment pushed beyond reasonable limits, and the nagging sense that your manufacturing operation could be delivering so much more?
Before you throw money at new lines or more overtime, it’s time to look hard at what’s driving those capacity woes.
If you suspect your production processes are falling short of their true potential, you’re likely contending with the fallout of poor resource allocation.
Pushing capacity utilization to the limit is a recipe for trouble – the quality breakdowns and compliance risks it breeds are likely sabotaging your true output.
In this installment, we’re moving past the catastrophic failures and eye-catching regulatory fines to focus on where things actually unravel: the daily frustrations on your shop floor. We’ll look at the inconsistencies, the uncertainties, the gut-check moments that create a domino effect, crippling your output. These issues collectively devour your capacity, hiding potential gains and making it impossible to unlock the full power of your investment in people and machinery.
Let’s expose the top 10 ways these ‘invisible’ quality and compliance issues rob you blind. Even better, for each issue, we’ll give you a roadmap to fight back, reclaim your lost capacity, and finally achieve the reliable, predictable productivity you and your customers deserve. Consider this your intervention to stop throwing good money after bad.
1Inconsistent Rework Patterns:
Negative Impact: Rework happens, but sudden spikes or patterns across specific products or stations should raise red flags. Blaming “worker error” is short-sighted. Poorly designed processes, confusing instructions, or inadequate training are more likely the culprits.
Positive Step: Don’t just fix the rework. Fix the root cause. Analyze rework data in context—what products, where on the line, and which workers are involved? Use tools like Pareto charts to identify the most common issues, then investigate with process mapping and ‘5 Whys’ analysis to get to the core of the problem. Invest in redesigning the process or enhancing worker training for long-term improvement.
2Equipment Calibration Drift:
Negative Impact: Measuring instruments, filling machines, and even ovens – all lose calibration over time. Seemingly minor deviations can have huge impacts on product quality. Underfilling consumer packages, for instance, might escape notice but carries legal and brand reputation risks.
Positive Step: Ditch the calendar-based calibration approach. Use statistical tools to track critical equipment parameters. Look for trends that indicate when calibration is genuinely needed, preventing problems before they occur. Investing in modern equipment with self-calibration or built-in alerts will streamline this process, reducing downtime and ensuring accuracy.
3Unexplained Variance in Test Yields:
Negative Impact: One day, your product passes quality tests with flying colors, the next it’s riddled with failures. If there’s no noticeable change, you’ve got a hidden process instability. Suspects could be anything from inconsistent raw materials to subtle environmental effects (humidity, temperature) on your processes.
Positive Step: Meticulous data analysis is key here. Track test yields over time using control charts to visualize trends. Overlay this data with information about raw material batches, machine settings, and even shift timestamps. Look for correlations that give clues as to the root cause.
4“Invisible” Process Changes:
Negative Impact: Workers find faster, easier ways to do things, but shortcuts rarely make it into the official procedures. This leads to dangerous variations in your process, potentially compromising quality or violating regulations.
Positive Step: The best way to manage informal change is to formalize it. Encourage a culture where workers feel comfortable surfacing problems with the current methods. Have a structured process for proposing, evaluating, and documenting changes. This ensures they’re vetted for safety and quality, and the updated procedures reach everyone who needs them.
5Sporadic Traceability Gaps:
Negative Impact: When a product recall strikes, you need to know exactly where every affected item went. Missing batch records, and illegible labels – these holes in your data turn traceability into a logistical nightmare and can amplify the financial and reputational damage.
Positive Step: Review your traceability system critically. Is it too reliant on manual data entry and prone to errors? Look into barcode or RFID technology to automate data capture where possible. Simplify and streamline the data collection process for workers on the line, ensuring they understand its critical importance. Conduct mock recalls to test your system’s effectiveness.
6Shift-to-Shift Variability:
Negative Impact: Does one shift consistently outperform the others? It’s not just about who’s working but how the handover between shifts is handled. Inconsistent communication about in-process work, equipment problems, etc., can lead to subtle quality differences or production delays with cascading effects.
Positive Step: Standardize shift handover protocols. Implement detailed checklists and clear ownership of issues to reduce ambiguity and ensure continuity. Consider visual management tools like whiteboards to provide real-time status updates and open communication within and across shifts.
7Training Documentation Inaccuracies:
Negative Impact: Outdated or confusing work instructions are a quality disaster waiting to happen. Even subtle errors or unclear language leave room for worker interpretation, and this variability undermines consistency, quality, and compliance.
Positive Step: Don’t let documentation be an afterthought. Review it regularly, ideally with input from line workers. Use visuals like pictures and videos to supplement text. Implement a version control system to track changes and ensure everyone has the latest, most accurate information at all times.
8Misaligned Performance Metrics:
Negative Impact: What you measure is what you get. If metrics focus solely on output speed, workers may sacrifice quality to hit targets. Metrics that don’t reflect the true cost of waste or rework can create perverse incentives.
Positive Step: Take a holistic view of performance metrics. Alongside speed and volume, track key quality indicators – yield rates, customer complaints, defect levels, etc. Regularly re-evaluate metrics to ensure they align with your overall quality goals and incentivize the right behaviors.
9Delayed Feedback Loops:
Negative Impact: Quality problems identified too late result in wasted time, resources, and potential for customer harm. If the line worker gets quality feedback only after an end-of-the-line test or customer complaint, you’ve missed many opportunities to correct the course.
Positive Step: Move towards real-time (or near real-time) quality checks where feasible. Provide tools that allow workers to check their own work throughout the process. Empower them to take corrective action immediately, reducing waste and preventing defects from being propagated down the line.
10“Gut Feeling” Decision Making:
Negative Impact: Intuition can be helpful, but over-reliance on it breeds inconsistency and undermines confidence in your processes. When decisions about product release, process settings, or troubleshooting are based on a feeling, you introduce potential bias and leave yourself vulnerable to problems slipping through.
Positive Step: Use data-driven decision-making. Establish clear quality standards and tolerances. Train staff in process control tools to detect potential problems early. Ensure the relevant data is easily accessible, allowing them to make informed decisions rather than guesses.
The Bottom Line: Don’t Let Hidden Issues Sabotage Your Success
The ten issues we’ve discussed may seem minor in isolation, but their insidious nature lies in the cumulative impact. Each one chips away at your true capacity, making your investment in equipment and people far less effective than it could be. Imagine the difference you could make if those rework delays disappeared, those gut-check decisions were replaced with data-driven confidence, and the frustrating inconsistencies gave way to predictable, high-quality production.
It’s Time to Take Control – POWERS Can Help
At POWERS, we understand the unique challenges and complexities of the manufacturing floor. We don’t believe in band-aid solutions. Our team of experts utilizes a proven methodology to analyze your processes, uncover the root causes of quality and compliance issues, and design sustainable solutions.
We’ll work hand in hand with your team, fixing immediate problems and building a culture of continuous improvement that keeps these hidden issues at bay.
Optimize your manufacturing processes and achieve unprecedented efficiency. Contact POWERS today to learn how our expertise can drive your company’s success. Let’s start the conversation: +1 678-971-4711 or info@thepowerscompany.com.
Continue Reading from this Mastery Series
- Part 1 – The Price of Lost Revenue and Profit Resulting from Underutilized Capacity
- Part 2 – How Rising Production Costs Hide Your Factory’s True Potential
- Part 3 – Poorly Managing Resources is Stealing Your Profits
- Part 4 – Break the Quality Struggle Cycle to Fix This Shop Floor Frustration
- Part 5 – From Chaos to Capacity: How to Tame Turnover and Optimize Your Operations
- Part 6 – Manufacturing Nightmares: When Your Shop Floor Can’t Keep Up
- Part 7 – When Supply Chain Disruptions Reveal Your True Capacity
- Part 8 – Unlocking Efficiency When Sustainability Meets the Shop Floor
- Part 9 – Understaffed and Underperforming on the Shop Floor
- Part 10 – How Blind Spot Vulnerabilities Impact Your Shop Floor’s Efficiency