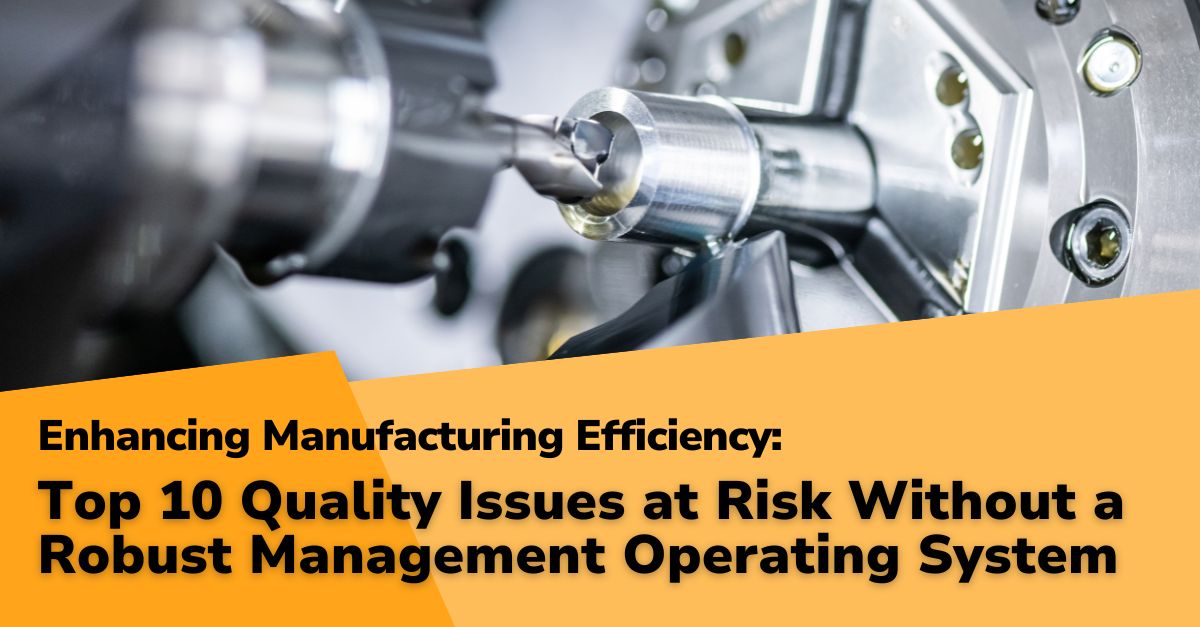
A well-structured MOS is the backbone of a manufacturing operation, seamlessly integrating various processes, from resource allocation to quality control, and ensuring that each component of the manufacturing value chain functions optimally.
The lack of such a system, or its inadequate execution, can result in operational inefficiencies and ultimately diminished product quality.
In manufacturing, product quality is paramount, directly influencing a company’s reputation, customer satisfaction, and overall market position. High-quality products reduce the likelihood of defects and recalls, safeguarding against the significant financial and reputational costs associated with these issues. They also contribute to customer loyalty and repeat business, as consumers tend to trust and prefer brands that consistently deliver superior quality.
Furthermore, maintaining high product standards is crucial for compliance with industry regulations and standards, which can vary significantly across different markets. Superior product quality can serve as a critical differentiator. It enables companies to command premium pricing, expand into new markets, and sustainably grow their market share, thereby securing a competitive advantage in the global manufacturing landscape.
Let’s explore the top 10 ways that the absence of an MOS, or a poorly implemented one, can negatively impact quality in manufacturing processes, providing insights into how these challenges can be effectively addressed.
1Increased Variability in Product Quality:
Without an MOS, standardization of processes becomes challenging, leading to significant fluctuations in product quality. This inconsistency can stem from variations in raw material handling, production methodologies, or final product checking procedures. Such variability undermines customer trust and can lead to a higher rate of product returns or complaints.
2Ineffective Quality Control Systems:
An MOS often integrates systematic quality control measures at various stages of the production process. Its absence can result in haphazard or non-existent quality checks, allowing defects to go undetected. This oversight can cause considerable financial loss due to waste, recalls, or damage to the company’s reputation.
3Poor Traceability of Quality Issues:
A robust MOS usually includes mechanisms for tracking and recording production data, facilitating easy identification and rectification of quality issues. Without this system, tracing the root cause of defects becomes time-consuming and complex, delaying corrective actions and potentially leading to recurring problems.
4Delayed and Inadequate Response to Quality Problems:
MOS structures provide a clear protocol for responding to quality issues, ensuring quick and appropriate actions are taken. In its absence, there might be confusion or delays in addressing these problems, exacerbating their impact and possibly leading to a larger-scale quality crisis.
5Limited Opportunities for Continuous Improvement:
Continuous improvement is a core aspect of quality management in an MOS. Without it, there are missed opportunities for process refinement and quality enhancement, leading to stagnation in production techniques and an inability to adapt to evolving market demands.
6Inadequate Employee Training and Engagement:
An effective MOS includes continuous training and skills development for employees, ensuring they are competent in maintaining and improving quality standards. Without such training, workers might lack the necessary skills or motivation to uphold quality, leading to increased errors and defects.
7Inconsistency in Supplier Quality Management:
An MOS extends quality management to include suppliers, ensuring consistency in the quality of raw materials and components. Its absence can lead to variability in supplier quality, directly impacting the quality of the finished product.
8Lack of Standardization Across Units:
An MOS ensures uniform quality standards across all locations in organizations with multiple manufacturing units. Without such a system, each unit may operate with different quality benchmarks, leading to inconsistency in the products offered to customers.
9Inefficient Resource Utilization:
An MOS aids in the optimal allocation of resources, including workforce, materials, and machinery, to maintain consistent quality. The absence of such a system can lead to resource wastage or overuse, impacting the cost and quality of the product.
10Eroded Customer Confidence and Loyalty:
Ultimately, the culmination of these issues can significantly erode customer confidence and loyalty. Maintaining consistent quality is critical to customer retention and brand reputation in today’s competitive market. Failure to do so can have long-lasting negative impacts on the business.
Conclusions for Manufacturing Operations Leaders
The lack of a robust Management Operating System (MOS) in manufacturing often leads to diverse quality issues, undermining operational efficiency and product quality. These range from inconsistent product standards and poor quality control to inefficient resource use and process fragmentation. Such challenges disrupt current operations and impede long-term strategic growth and innovation. Leaders in manufacturing must recognize and tackle these issues to maintain a competitive edge.
The POWERS Difference
POWERS is uniquely positioned to enhance MOS effectiveness in manufacturing. Our approach includes:
- Tailored Solutions: We design MOS solutions specifically suited to each manufacturing context, addressing unique quality and operational challenges.
- Comprehensive Integration: Beyond implementation, we integrate the MOS into your organizational culture and processes for a cohesive operational framework.
- Empowering People and Processes: Our strategy is to engage and train employees at all levels to maintain and enhance quality standards.
- Data-Driven Decision-Making: We leverage the latest analytics for informed, strategic decision-making.
- Proven Expertise: With a history of successful MOS implementations, we bring deep insights into enhancing quality and efficiency in manufacturing.
Partner with POWERS to elevate your operation’s quality, efficiency, and competitiveness. Start your journey toward operational excellence and quality leadership in manufacturing with us.
Unlock the full potential of a robust Management Operating System with POWERS and set your path toward unparalleled operational excellence. Start your transformative journey today. For expert guidance and bespoke solutions, contact our team at +1 678-971-4711 or email info@thepowerscompany.com.
Continue Reading from this Mastery Series
- Part 1 - Identifying Key Inefficiencies in the Absence of a Management Operating System
- Part 2 - Top 10 Pitfalls: Lack of an MOS Derails Productivity
- Part 3 - Top 10 Quality Issues at Risk Without a Robust Management Operating System
- Part 4 - The High Cost of an Ineffective Management Operating System
- Part 5 - Without an Optimized Management Operating System, Decision-Making is Severely Impaired
- Part 6 - Scaling Challenges of an Inadequate Management Operating System
- Part 7 - The High Price of Low Engagement: Unpacking the Operational Impact of Employee Discontent
- Part 8 - Safeguarding Success: Decoding the Impact of Compliance and Safety Issues
- Part 9 - Examining the Cost of a Slow Response to Market Shifts
- Part 10 - Charting Success: Understanding the Costs of Losing Competitive Advantage