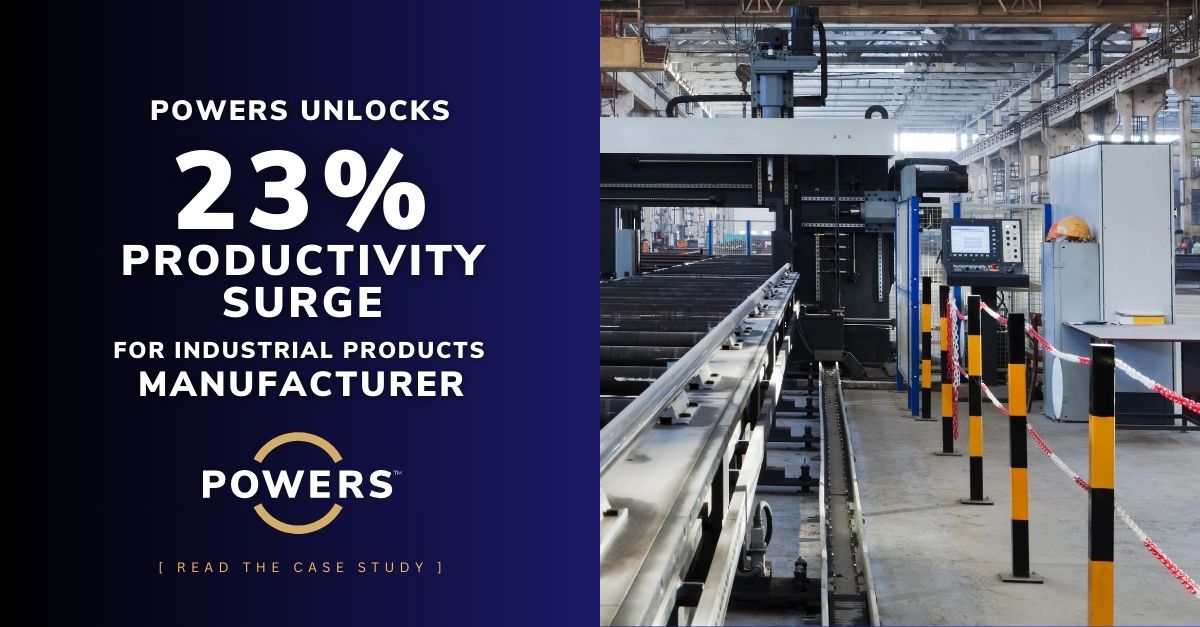
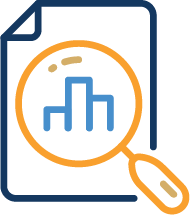
Project Overview
Introduction
A long-established manufacturer of industrial products turned to POWERS during operational turbulence, seeking to resolve significant issues caused by implementing a new Enterprise Resource Planning (ERP) system. The company, known for producing high-quality goods for diverse sectors, including healthcare, industrial, and commercial facilities, faced a backlog of over $1 million in orders. Additionally, its ability to meet manufacturing and shipping targets was severely impacted by fluctuations in headcount, reliance on temporary labor, and an impending plant closure and relocation. POWERS was engaged to optimize plant performance and ensure operational continuity during this crucial period.
With its deep experience in enhancing manufacturing productivity and leadership capabilities, POWERS quickly identified the need for a comprehensive approach that addressed the immediate operational concerns and the broader, systemic issues within the company. The goal was to restore operational efficiency and build a more resilient, adaptable workforce and leadership team capable of maintaining high performance despite future challenges.
Background
The manufacturing organization had been an industry leader for decades, known for producing durable, high-performance industrial products used in environments ranging from hospitals and data centers to factories and commercial spaces. Over time, the company had undergone several major transitions, including mergers and system upgrades, which gradually increased the complexity of its operations. Most recently, the transition to a new ERP system disrupted many established workflows and processes, causing significant delays and creating a substantial backlog in order fulfillment.
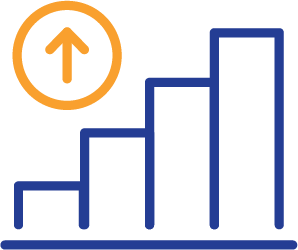
Performance Results
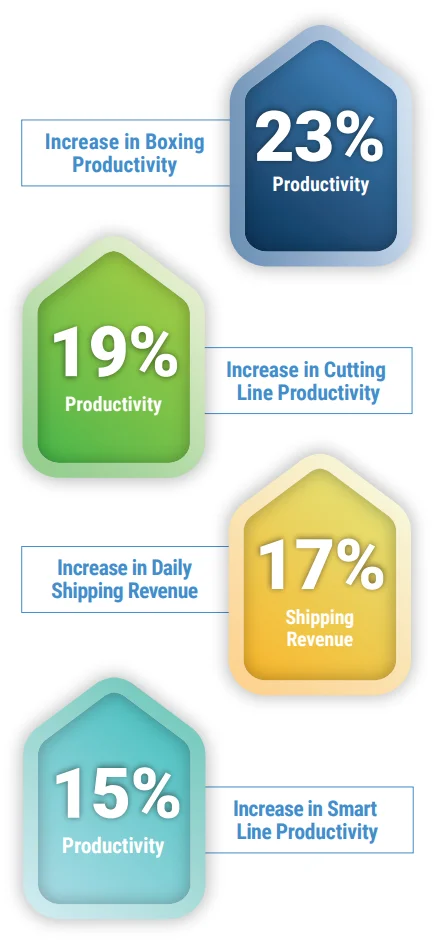
Read the Full Case Study Here
At the same time, the company was preparing to relocate its production facility, which would require careful planning to maintain inventory levels and avoid further disruptions. Due to this impending move, the workforce had been in flux, with many employees leaving or being replaced by temporary labor, which added to the challenges. Leadership was pressured to maintain current production levels and ensure the plant’s relocation would go smoothly without compromising customer satisfaction or order fulfillment.
Situation
Faced with these multifaceted challenges, the company’s leadership sought external expertise to help stabilize operations, improve efficiency, and ensure the successful transition of the plant. POWERS was tasked with several critical objectives, including:
- Meeting Manufacturing and Shipping Targets: The company needed daily manufacturing targets across multiple value streams while ensuring its distribution center met daily shipping goals of $150,000.
- Improving Departmental Productivity: The boxing department needed to achieve a production rate of 1,000 pieces per shift across both the first and second shifts, a target that had been consistently missed.
- Leadership and Team Management: To address the ongoing challenges with temporary labor, fluctuating headcount, and training gaps, the company required stronger leadership and better coordination across departments, including operations, human resources, finance, and customer service.
- Inventory Management During Transition: A major component of the plant’s transition plan was building three months of inventory to bridge the production gap during the relocation process without further straining the existing workforce or compromising quality.
Challenges
The company faced several interconnected challenges that compounded the operational disruptions caused by the ERP transition:
- ERP System Learning Curve: Implementing the new ERP system introduced a steep learning curve for leadership and frontline workers. The system’s complexity led to operational bottlenecks and delays, which, in turn, caused the backlog to grow to over $1 million.
- Inconsistent Workforce: The fluctuating workforce, which relied heavily on temporary labor due to the pending plant closure, created additional challenges in training, maintaining performance standards, and achieving consistent productivity.
- Inventory and Capacity Issues: The need to build and maintain three months of inventory to support the plant relocation further strained the company’s labor resources. The challenge was maximizing production capacity without overburdening an already stretched workforce while maintaining customer satisfaction through timely order fulfillment.
Approach
POWERS developed and implemented a multi-faceted strategy designed to address these challenges holistically. The approach focused on both immediate operational improvements and longer-term capacity building.
- Operational Efficiency and Process Improvement: POWERS implemented rapid process optimizations to meet or exceed daily manufacturing and shipping goals. By streamlining workflows, reallocating resources more effectively, and enhancing the training of both permanent and temporary staff, the company was able to restore its operational momentum. A particular focus was placed on ensuring that team leaders and supervisors maintained a laser focus on hourly production rates, ensuring each shift met its targets.
- Production Line Optimization: Special attention was given to optimizing the performance of key production lines, such as the boxing department and a critical “smart line” used for high-precision tasks. POWERS re-engineered processes within these lines, introduced performance monitoring tools, and implemented targeted training programs. Daily collaboration with the planning team ensured that production priorities were communicated, and weekly reviews allowed for continuous improvements.
- Leadership Development and Team Building: Recognizing that leadership was a key driver of operational success, POWERS focused heavily on developing the leadership capabilities of the plant’s operations team. This included the operations manager, distribution center manager, supervisors, line leads, and other key personnel. Improved communication channels were established, and leadership training programs were introduced to help managers navigate the ongoing changes, foster team cohesion, and improve overall team performance.
- Inventory Management and Capacity Maximization: To meet the need for a three-month inventory, POWERS worked closely with the company’s leadership to develop a detailed build plan that maximized production capacity while addressing labor constraints. The plan focused on optimizing resource scheduling, maintaining continuous demand fulfillment, and ensuring the workforce was adequately supported through targeted labor management strategies.
Results
The comprehensive approach taken by POWERS led to substantial improvements in operational performance, which helped the company regain stability and set the foundation for continued success during and after the plant relocation. Key results included:
- Shipping Performance: Daily shipping revenue increased by 17%, reaching an average of $134,000 per day—significantly improved over previous performance.
- Smart Line Productivity: The smart line’s productivity increased by 15%, operating at 90% of its target efficiency, representing a major step forward in overall production capability.
- Boxing Department Efficiency: The boxing department saw a 23% improvement in productivity, consistently meeting the target of 1,000 pieces per shift.
- Cutting Line Productivity: Another critical production line responsible for cutting materials saw a 19% improvement in productivity, further boosting the company’s overall manufacturing output.
- Inventory Build Success: The company built a three-month inventory for select products, ensuring customer demand could be met during the plant relocation without further disruptions.
- Leadership and Team Cohesion: The leadership team became more cohesive, engaged, and capable of navigating future operational challenges, contributing to sustained improvements in plant performance.
As a result of the engagement, POWERS was retained to provide ongoing support during the next phase of the plant’s transition, underscoring the long-term value of the strategies implemented.