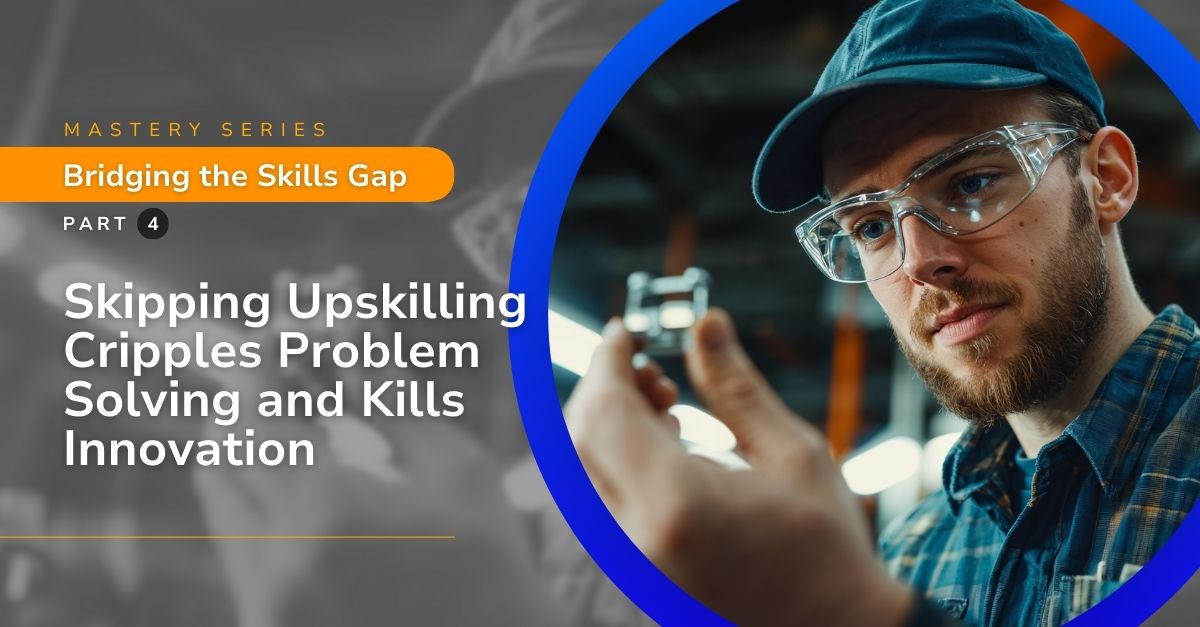
Neglecting investment in upskilling creates a significant challenge for manufacturing companies, directly impacting their ability to foster innovation and effective problem-solving.
On the surface, it may seem like a simple oversight, but the deeper consequences of this neglect can lead to a range of operational inefficiencies that stifle productivity.
When employees aren’t given opportunities to expand their skill sets, they often struggle to think creatively or adapt to new challenges, leaving managers on the shop floor with recurring problems and a workforce that can only respond to issues.
A clear example of this erosion can be seen in the way manufacturing teams handle machine maintenance. Maintenance protocols remain rigid and outdated in many facilities, even as equipment technology evolves.
Workers who lack the training to understand and implement predictive maintenance systems rely on outdated reactive maintenance methods. This leads to more frequent breakdowns and prevents teams from identifying small issues before they become costly, large-scale failures.
Neglecting upskilling initiatives also creates a larger divide between operational teams and their ability to adapt to new technologies, ultimately reducing the effectiveness of any new processes or tools introduced on the floor. Managers are left with an ill-equipped workforce to troubleshoot or improve upon these systems, which hinders overall production efficiency.
This ongoing cycle of limited problem-solving capabilities and a lack of innovative thinking limits growth and puts a company at a disadvantage when competing in an increasingly technology-driven manufacturing landscape.
1Delays in Addressing Root Causes of Recurring Issues
One of the first signs that innovation and problem-solving capabilities are eroding is when teams repeatedly face the same issues without resolution. Managers often report that employees resort to short-term fixes rather than uncovering the root causes, resulting in recurring downtime and inefficiency. As teams fall into a pattern of “putting out fires,” they lose the capacity for systematic problem-solving, prolonging issues that stifle production.
Mitigation: Invest in critical thinking and problem-solving workshops that teach employees to diagnose problems rather than treat symptoms. Empowering teams with root cause analysis techniques like Fault Tree Analysis (FTA) can significantly reduce recurring issues. Equipping employees with these skills fosters a proactive culture where problems are solved for the long term, boosting productivity and innovation.
2Inability to Capitalize on Customer Feedback for Innovation
Customer feedback is a goldmine for driving innovation, but when employees lack upskilling, they often overlook this valuable resource. Managers frequently note that customer feedback, which could be used to improve products or processes, goes unutilized. Without the right training, employees fail to see feedback as a source of innovation, missing opportunities to refine offerings and improve customer satisfaction.
Mitigation: Regularly train employees to interpret customer feedback and integrate it into their work processes. Creating dedicated sessions to review and brainstorm around customer input can lead to innovative solutions that better meet market needs. Providing tools like customer feedback analysis software can also streamline this process, enhancing responsiveness to customer-driven innovation.
3Infrequent Assessment of Competitors’ Innovations
Falling behind on competitive intelligence is another red flag that innovation is declining. Many managers admit that employees don’t proactively assess competitors’ innovations without the right skills, leaving the organization stagnant. Failing to monitor advancements in the industry allows competitors to gain an edge, often resulting in lost market share.
Mitigation: Build a cross-functional team focused on competitive analysis and innovation scouting. Companies can stay ahead of industry trends by teaching employees how to assess competitors’ strategies and innovations. Encouraging participation in trade shows and industry seminars can help employees stay informed and bring back actionable insights that drive innovation.
4Reduced Adaptability in Crisis Management
Crises test a company’s adaptability, but managers often see slower response times and poor problem-solving without upskilled employees. When teams aren’t prepared to think on their feet, crisis management becomes reactive rather than adaptive. This lack of preparedness exacerbates production delays, damages customer relationships, and can even lead to safety hazards.
Mitigation: Upskilling in crisis management techniques, such as scenario planning and decision-making under pressure, can drastically improve response times and effectiveness. Offering real-time simulations and crisis response drills ensures employees are ready to handle unexpected challenges while maintaining productivity.
5Inability to Adapt to New Technologies Effectively
As technology evolves, employees who aren’t continuously trained struggle to adapt. Managers report that teams resist new tools or technologies that could streamline processes or introduce new efficiencies without proper upskilling. This resistance slows productivity, increases errors, and hinders innovation as employees stick to outdated methods.
Mitigation: Establish a structured training program for new technologies, with continuous education that ensures all staff are proficient in the latest tools. Implement a mentorship model where early adopters can guide others through the transition. Creating an innovation-friendly environment where employees feel supported during technology changes will reduce resistance and accelerate adaptation.
6Diminished Enthusiasm for Piloting New Solutions
Innovation thrives on experimentation, but when employees aren’t encouraged to develop new skills, they lose enthusiasm for piloting novel solutions. Managers often notice a reluctance among teams to explore new processes or techniques because they lack the confidence or know-how. This hesitation to experiment can lead to stagnation, particularly in industries where innovation is key to growth.
Mitigation: Foster a workplace culture of continuous improvement by incentivizing employees to pilot new solutions. Offer rewards for experimentation and successful innovation projects. Upskilling in lean methodologies or agile management techniques can also build employees’ confidence to test new ideas without fear of failure.
7Fewer Novel Solutions Proposed for Recurring Problems
As employees face recurring challenges on the shop floor, their ability to propose new solutions diminishes when they lack the skills to think outside the box. Managers often complain that teams become complacent, relying on tried-and-true methods rather than exploring innovative approaches. This not only slows progress but also reduces efficiency.
Mitigation: Introduce creativity and innovation workshops that teach employees to approach problems from new angles. Encouraging collaboration between departments and fostering an open exchange of ideas can help break down silos that inhibit creative problem-solving. Providing time for brainstorming sessions can also spark fresh ideas for recurring issues.
8Disconnection Between Operational Staff and R&D
When there’s a lack of upskilling, a common issue is the growing disconnection between operational staff and research and development (R&D) teams. Managers often observe that operational staff do not fully understand or engage with new developments, creating a gap between what R&D proposes and what is practical on the shop floor. This disconnection stifles innovation and leads to missed opportunities.
Mitigation: Encourage cross-departmental collaboration to build stronger relationships between R&D and operations. Upskilling operational staff in R&D processes and vice versa ensures that both teams understand each other’s roles and can work together more effectively. Regular innovation meetings can also bridge this gap, ensuring that innovations from R&D are grounded in operational realities.
9Lack of Curiosity-Driven Exploration
Employees lose their curiosity for exploring new ideas, technologies, or processes without continuous upskilling. Managers frequently lament that teams seem to do only what is necessary rather than engaging in curiosity-driven exploration that could lead to breakthroughs. This mindset stifles creativity and reduces the likelihood of spontaneous innovation.
Mitigation: Encourage a learning culture by offering employees opportunities to explore areas of personal and professional interest. Investing in workshops, certifications, or even paid time for self-directed learning can reignite curiosity. Creating spaces where curiosity is valued, such as innovation labs or idea incubators, allows for the free exploration that can lead to breakthroughs.
10Loss of Informal Knowledge Sharing
When employees are engaged in continuous learning, informal knowledge-sharing begins to fade. Managers often note that teams are less likely to collaborate and share insights on how to solve problems or improve processes. This loss of peer-to-peer learning diminishes innovation and stifles problem-solving.
Mitigation: Establish knowledge-sharing platforms and programs that encourage collaboration and mentorship. Creating informal spaces for employees to exchange ideas, such as virtual forums or team lunches focused on innovation, can help reinvigorate knowledge-sharing practices. Upskilling leaders in facilitation techniques can also ensure that informal learning is structured and productive.
Conclusions for Operations Leaders
The erosion of innovation and problem-solving capabilities on the shop floor is a direct consequence of neglecting investment in upskilling. As teams face challenges they aren’t equipped to handle, productivity drops, operational costs rise, and growth opportunities are missed.
By doing so, they mitigate recurring issues and create a culture where employees are empowered to innovate and solve problems more efficiently.
At POWERS, we understand the specific challenges that manufacturing organizations face when maintaining a dynamic and innovative workforce. Our hands-on, results-driven approach equips teams with the skills they need to address root causes, leverage new technologies, and foster a culture of continuous improvement. We work closely with leadership and staff to create tailored solutions that drive sustainable productivity improvements.
Here’s how POWERS can help:
- Conduct a comprehensive skills gap analysis to identify areas where upskilling can boost innovation and problem-solving.
- Facilitate cross-functional collaboration between departments, bridging gaps between operations and R&D.
- Foster a continuous improvement mindset through targeted workshops and ongoing education initiatives.
- Introduce advanced problem-solving techniques like Fault Tree Analysis (FTA) to eliminate recurring issues at their source.
- Create structured opportunities for knowledge sharing and informal learning among teams to reinvigorate collaboration.
Partnering with POWERS allows you to equip your workforce with the tools they need to excel in today’s complex manufacturing landscape. By investing in upskilling, your teams will be better prepared to innovate, solve problems more effectively, and ultimately drive your company toward greater productivity and success.
- Speak to an Expert: Call +1 678-971-4711 to discuss your specific challenges and goals.
- Email Us: Get tailored insights by emailing info@thepowerscompany.com
- Request an Assessment: Use our online contact form, and one of our expert manufacturing consultants will reach out to schedule an in-depth analysis of your operations.
Continue Reading from this Mastery Series
- Part 1 – Why Automation Alone Won’t Boost Productivity
- Part 2 – Why Non-Technical Skills Are Increasingly the Key to Increasing Productivity
- Part 3 – The Widening Digital Divide is Leaving Some Companies in the Dust
- Part 4 – Lack of Upskilling Sabotages Problem-Solving, Decision Making, and Innovation
- Part 5 – The Link Between Upskilling and Employee Well-being
- Part 6 – Neglecting Upskilling Leaves Your Operation Vulnerable to Safety Issues
- Part 7 – How Neglecting Upskilling Erodes Legacy Knowledge and Hurts Productivity
- Part 8 – Failing to Upskill Frontline Leaders Can Derail Operations
- Part 9 – Skimping on Skills Training Sabotages the Bottom Line
- Part 10 – An Underdeveloped Workforce Means an Unscalable Operation