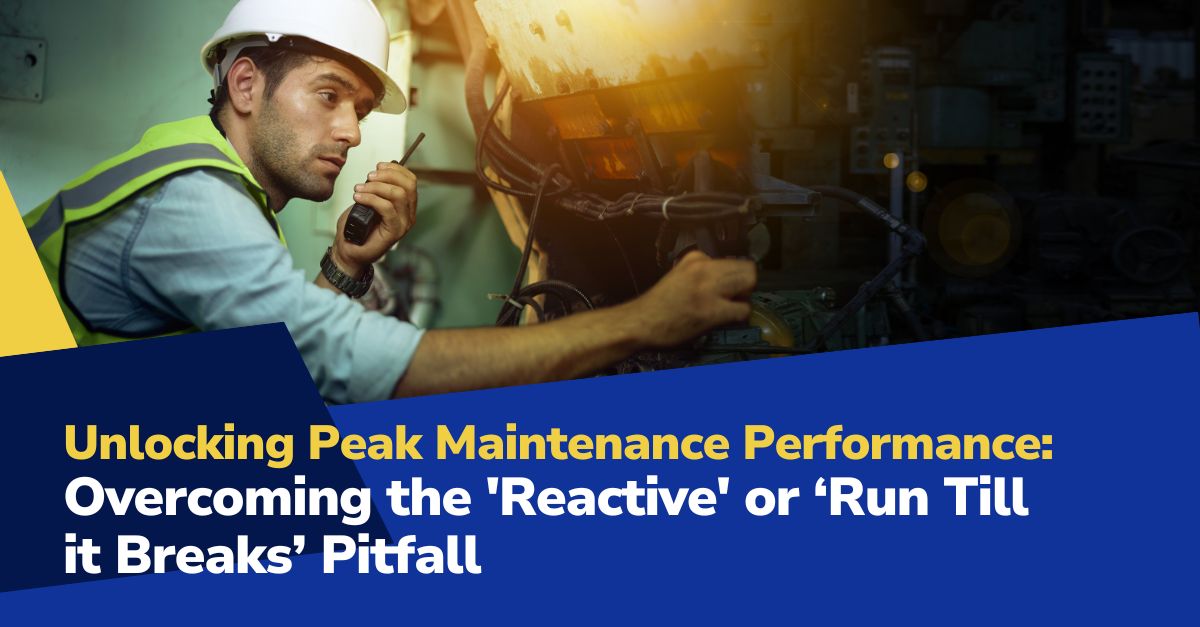
In the complex day-to-day execution of manufacturing maintenance, the overall strategic approach adopted can significantly impact operational efficiency, cost-effectiveness, and product quality. A prevalent issue in many organizations is the tendency to rely on a reactive maintenance model.
Reactive maintenance, often called a ‘run till it breaks’ strategy, can deeply impact overall productivity and profitability.
This final installment of our series delves into how this seemingly straightforward approach can lead to numerous pitfalls and the importance of shifting towards more proactive and predictive maintenance strategies.
The Downfalls of Reactive Maintenance
1Increased Downtime:
Reactive maintenance typically means waiting for a failure before taking action. This approach leads to unexpected breakdowns, which can result in prolonged downtime. Studies suggest that unplanned downtime can cost manufacturers significantly, directly impacting production schedules and on-time deliveries.
2Higher Maintenance Costs:
The cost of repairing equipment after a failure is substantially higher than regular, planned maintenance. As illustrated by the Caterpillar Company, repairs post-failure can exceed 65% of the equipment’s value, compared to just 5-25% if the issue is addressed proactively.
3Reduced Equipment Life:
Reactive maintenance does not address the wear and tear of equipment over time, often leading to premature equipment failure and the need for more frequent replacements.
4Safety Risks:
Emergency repairs, often conducted under pressure, can compromise safety standards, putting workers at risk.
5Quality Compromise:
Equipment failures can lead to defects in the manufacturing process, impacting the quality of the final product.
6Inefficient Use of Resources:
Reactive maintenance requires more staffing and resources as technicians scramble to fix problems, often leading to inefficient resource allocation.
7Lower Productivity:
Every equipment breakdown interrupts the manufacturing production cycle, reducing overall productivity.
8Energy Inefficiency:
Poorly maintained equipment often consumes more energy, increasing operational costs.
9Compliance Issues:
Equipment failures can lead to non-compliance penalties in industries with stringent regulatory standards.
10Customer Dissatisfaction:
Frequent breakdowns can lead to delayed orders and lower product quality, impacting customer satisfaction and trust.
The Shift to Proactive and Predictive Maintenance and Beyond
The shift from reactive to proactive and predictive maintenance is vital to mitigate these challenges. Proactive maintenance involves regular and planned maintenance activities, while predictive maintenance takes this a step further by using data and analytics to predict and prevent equipment failures before they occur.
Benefits of Proactive and Predictive Maintenance
- Cost Savings: Predictive maintenance, in particular, offers significant cost savings. Regular condition assessments and monitoring can prevent costly breakdowns and extend equipment life.
- Improved Safety and Quality: Regular maintenance ensures equipment operates within safety standards and maintains consistent product quality.
- Resource Optimization: Proactive and predictive maintenance allows for better planning and use of resources, including workforce and spare parts.
- Energy Efficiency: Regularly maintained equipment operates more efficiently, reducing energy consumption.
- Compliance and Customer Satisfaction: Ensuring equipment reliability helps maintain compliance with industry standards and improves customer satisfaction through consistent product quality and on-time deliveries.
Implementing a Shift in Maintenance Strategy
1Assess Current Maintenance Practices:
Understand the proportion of reactive, proactive, and predictive maintenance in your current strategy.
2Cost-Benefit Analysis:
Conduct a detailed analysis of the costs associated with each type of maintenance.
3Tailor the Maintenance Program:
Depending on your industrial activity, choose between centralized or decentralized maintenance approaches.
4Invest in Training, Development, and Tools:
Equip your team with the necessary tactical and technical skills and tools for effective predictive maintenance.
5Monitor and Adjust:
Continuously monitor the effectiveness of your maintenance strategy and make adjustments as needed.
6Leverage Technology:
Use data analytics and IoT devices to predict and prevent equipment failures.
Conclusions for Senior Operations Leaders
Transitioning from a reactive to a proactive or predictive maintenance model requires a strategic shift in mindset and operations. By understanding the pitfalls of a reactive approach and leveraging the benefits of more advanced maintenance strategies, manufacturers can achieve peak maintenance performance, resulting in cost savings, improved safety, and enhanced product quality.
As we’ve seen from industry leaders like the Caterpillar Company, the investment in proactive and predictive maintenance pays dividends in the long run, both financially and operationally.
Embracing Total Productive Maintenance with POWERS AMP Program
The journey to enhanced maintenance practices is transformative, and the concept of Total Productive Maintenance (TPM) plays a pivotal role in this transformation. TPM focuses on proactive and preventive maintenance to maximize the operational efficiency of equipment. It integrates maintenance into the manufacturing process, aiming to eliminate unplanned downtime, increase productivity, and maintain optimal quality.
POWERS, leveraging its vast experience in manufacturing maintenance, offers a holistic solution with the AMP (Advanced Maintenance Performance) program.
This program provides tactical and technical training and development, guiding your maintenance teams from reactive strategies to predictive and ultimately to Total Productive Maintenance (TPM).
Dive into the POWERS difference. Embark on a journey of maintenance excellence with a detailed Overall Equipment Effectiveness (OEE) analysis, address skill and training gaps, create an actionable plan, and seamlessly implement it. Elevate your maintenance workforce and boost performance with the POWERS AMP program.
For a deeper understanding, download the FREE Maintenance Assessment Guide. Jumpstart your journey to optimized maintenance by contacting the POWERS team at +1 678-971-4711 or email info@thepowerscompany.com. Transform your maintenance practices and witness the tangible impact on your manufacturing operations.
Continue Reading from this Mastery Series
- Part 1 - The Critical Link Between Maintenance and OEE
- Part 2 - How Maintenance Practices Shape Product Quality
- Part 3 - How Poor Maintenance Standards and Practices Impact Schedule Adherence
- Part 4 - How Maintenance Practices Echo Along the Supply Chain
- Part 5 - The Impact of Maintenance on Maximizing Return on Assets (ROA) in Manufacturing
- Part 6 - Poor Maintenance Practices Lead to Out-of-Control Operational Costs
- Part 7 - Navigating the Safety and Compliance Minefield in Manufacturing
- Part 8 - The High Cost of Overlooking Maintenance in Manufacturing Strategic Planning
- Part 9 - Poor Maintenance Practices Are a Hindrance to Technological Innovations
- Part 10 - Overcoming the ‘Reactive’ or ‘Run Till it Breaks’ Pitfall