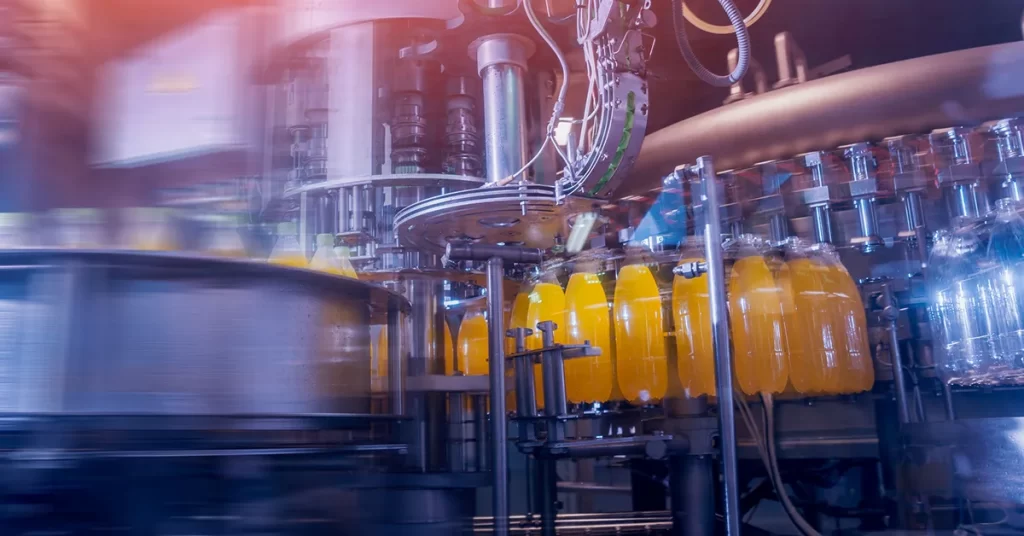
POWERS Leads Operations, Maintenance, Planning, and Inventory Control Turnaround at Major Beverage Industry Manufacturer
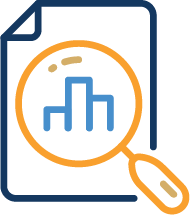
Project Overview
POWERS partnered with a major 3rd-party beverage manufacturer facing significant hurdles in meeting a 31% increase in demand forecast for 2021. Operators of two bottling and canning plants, our new client faced a sharp decrease in capacity utilization of nearly 40% due to excessive unplanned downtime, labor shortages during the pandemic, and challenges introducing and growing new product lines.
While demand was headed skyward, their ability to meet that demand was flagging or bottoming out at historic lows. Although the company had a robust stated culture, it was not aligned to performance expectations and outcomes.
Our analysis uncovered significant challenges in operations, maintenance, planning, and inventory control, but two areas of opportunity stood out: front-line leadership training and supply chain management.
A historical lack of training and development programs designed to meet flexible production and product demand left their front-line supervisors and managers ill-equipped to manage the extreme, pandemic-induced demand fluctuations. Additionally, poorly executed supply chain planning and controls led to daily raw material and packaging shortages.
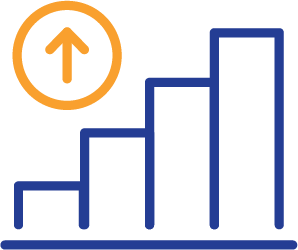
Production Improvements
- 7% YOY gain in overall plant equivalent cases
- 30% improvement in Clean in Place (CIP) times
- 30% reduction in startup delays
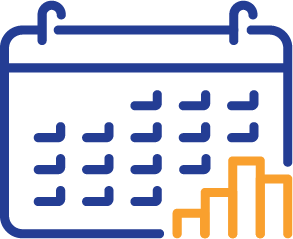
Maintenance Improvements
- 120% increase in maintenance work order execution to schedule
- 30% increase in mechanic utilization
- 39% reduction in mechanic overtime percentage
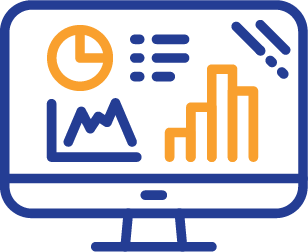
Logistics Improvements
- 44% improvement in inventory accuracy
- 100% pass rate of internal inventory audits
- 80% reduction in refrigerated truck wait times
- 3rd-Party beverage manufacturer operating two plants.
- Customer demand is projected to increase sharply by 31% in 2021.
- Capacity utilization at 30% to 40%, down drastically from a historical average of 70%.
- Excessive unplanned downtime.
- Labor shortages due to pandemic impacts.
- Struggles in new product introduction and growth.
- Lack of production/product demand training and development of front-line supervisors and managers.
- Lack of Raw Material (RM) control and planning of customer-supplied and sourced materials resulted in daily shortages of necessary brand raw materials and packaging.
- Changeovers – No Centerlines (CL) existed. Operators instead relied on past experience and adjustments while running to achieve a stable running condition. Operators struggled for hours and over shift changes to achieve a stable running condition.
- CIPs (Clean in Place) – No standards were present at the start of the project. All CIP time went into a “Planned Downtime” bucket, even if the CIP took several hours longer than needed, reducing the daily “available” hours for product runs.
- Lacking CIP standards significantly impacted the Planning and Scheduling process. No relationship or data were used to optimize line capacities and availability. These disconnects led to constant schedule attainment misses and daily negative customer communication from these missed commitments. Over and under scheduling to capacity due to lack of awareness of required CIP times, lack of change over standards, and missed coordination required for line maintenance.
- No Short Interval Follow Up, or Shop Floor visual management existed – No structured process was in place for employee engagement, participation, or ownership in area performance. No feedback loops.
- Mechanical or operational issues lingered longer than needed before they were addressed-no clear roles and responsibilities or defined escalation processes to drive urgency and support.
- No Structured Meetings were in place to discuss performance and corrective actions.
- Mechanics were poorly utilized with no daily work plan, left to choose priorities themselves, and drove a reactionary emergency response culture. As a result, mechanic utilization averaged 46%, and Preventive Maintenance (PM) completion rate averaged 40%.
- Average overtime was 23% at the start of the project.
- Shutdown planning was performed in a silo and only listed work desired to complete, leaving out estimated completion times, required resources, or required skills.
- Maintenance, Repair, and Operation (MRO) parts availability was determined at the mechanic or technician’s point of execution, allowing for excessive work time expended searching or ordering parts. This inefficiency resulted in less than 40% completion of planned work and drove up expediting or purchase pricing for needed parts.
- The maintenance team did not own their KPIs, nor were they aware of any performance-based criterion.
- Low schedule attainment.
- Incoming truckloads not spaced out, arriving at the wrong location, late, missing paperwork.
- No awareness of space limitations.
- Lines were not scheduled in terms of the time of day – just volume per day.
- Poor team development.
- Low accuracy, 64% baseline.
- Low % located, 23% baseline.
- Last-minute shortages.
- Failed audits.
- Low awareness of space limitations.
- Poor space utilization.
- Holds and Retains left unprocessed.
- Centerlines (Standard Settings) were developed and implemented with supervisors and key operators, reducing planned and required set-up times by 30%.
- Development of the Centerline (CL) criteria playbooks improved changeovers across all shifts, especially those with inexperienced crews, and reduced dependency on ‘tribal knowledge.’
- Developed Clean in Place (CIP) standards with supervisors and operators. Checklists, with allotted times for each step, are now utilized during CIPs. Times are tracked with deviations above the norms going into “unplanned downtime” and corrective actions developed to address issues. CIP times have improved by 30% over the past three months.
- Supervisor Short Interval Follow-Ups and Communication Boards were implemented early in the project, driving higher engagement and interaction between the supervisors and the operators. Issues are now identified more quickly, with corrective actions implemented in real-time.
- A Daily Meeting to discuss the previous day’s performance was implemented and a structured Action Item process, driving over 500 completed Action Items over five months.
- Overall, Plant Equivalent cases improved 7% year over year, with two lines improving over 19% each.
- A KPI dashboard was developed and is now owned and reviewed regularly by the maintenance leadership team.
- Improved the planning and scheduling process, so work orders are planned and assigned based on the Preventive Maintenance (PM) schedule, downtime data, and coordinated with production scheduling.
- Preventive Maintenance (PM) completion rate increased from 40% to an average of 88%, a 120% increase.
- Mechanic utilization rose from 46% to an average of 76%, a 65% increase.
- Mechanic overtime percentage decreased from 23% to 14%, a 39% reduction.
- Shutdown planning now follows a project plan approach with every shutdown activity in a Gantt chart starting with line shutdown activities through the first good bottle down the line, with estimated start times, durations, and assigned resources. The process now includes pre-shutdown planning meetings, daily status updates, and a post-mortem meeting to review successes and future improvement opportunities.
- Implemented min/max controls for key ingredients and packaging materials eliminated self-induced shortages for those items.
- Formalized space utilization reporting, reduced refrigerated truck wait times by 80%.
- Implemented schedule with times for each activity – production, maintenance, CIP, and changeovers, allowing better communication between Production and Planning, Maintenance with improved awareness of target times.
- Cross-functional, cross-line, and customer training improved team flexibility. A plant-based employee and labor utilization model was introduced, versus by line, sharing experience in times of absenteeism and labor shortages.
- Implemented improved receiving, moving, and consuming processes, accuracy improved from 64% to 92%.
- Implemented locating targets, and improved practices, increasing location rate from 23% to 88%.
- After introducing an audit planning process, all internal audits All audits passed.
- Red-Yellow-Green space utilization bands implemented, daily communication, excess transportation, and storage costs reduced.
- Slow-moving, obsolete, held, and retained items were all identified and moved or destroyed. This action reduced the additional freezer space budget to zero.