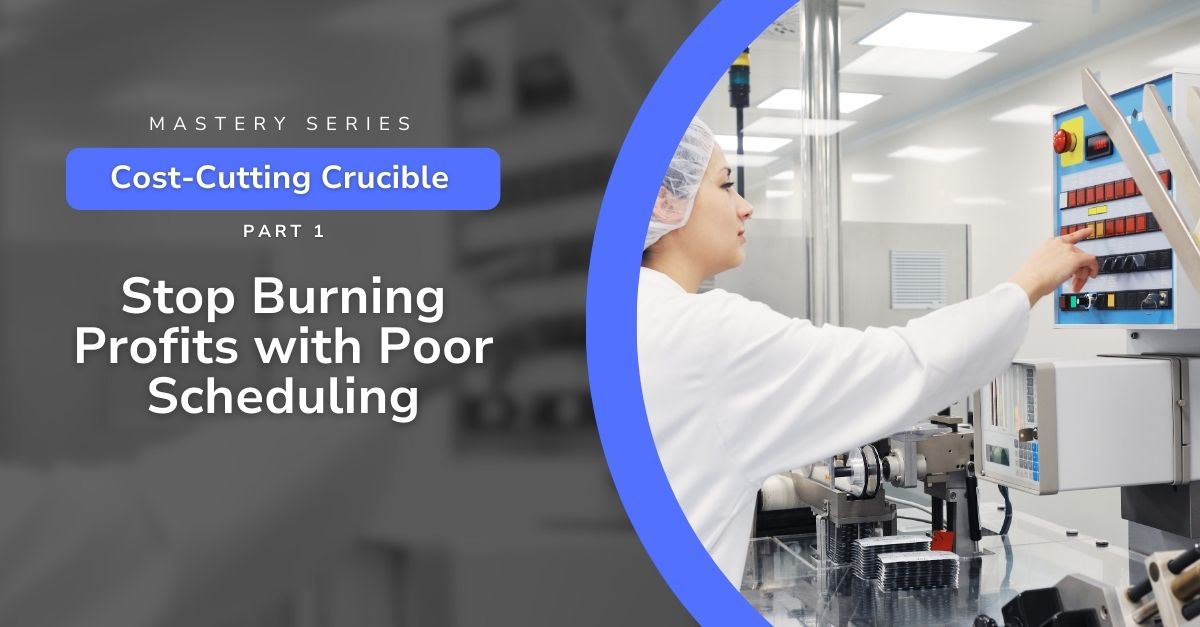
Profitability hinges on efficiency, and unseen drains on profit can quietly erode financial performance if not addressed. One of the most pervasive culprits is inefficient production scheduling.
Still, they are often responsible for hidden costs that ripple throughout an organization, from wasted labor hours to increased wear and tear on machinery.
Consider a less obvious impact: When production schedules are poorly optimized, it’s not just about machines sitting idle or workers left underutilized. For example, if a key piece of equipment is forced to endure inconsistent loads, it might accelerate unbalanced wear. This leads to unplanned maintenance and, in some cases, permanent damage to the machine. The overlooked cost here isn’t only the direct expense of repair and the extended downtime and subsequent production delays, which can result in missed delivery deadlines and lost client trust. Over time, these inefficiencies accumulate, manifesting in excess inventory in storage, tying up valuable capital, and increasing overhead costs.
These unseen drains on profit extend to various parts of operations, and their secondary symptoms—such as poor alignment between production and logistics or underutilization of shared resources—exacerbate inefficiencies. Manufacturers can better understand the importance of strategic planning by taking a closer look at how inefficient production scheduling silently eats away at margins. Recognizing and addressing these hidden costs can unlock significant opportunities for improving productivity and safeguarding profitability.
1Prolonged Machine Idle Times Waiting for Previous Processes to Finish:
Machines frequently sit idle when production schedules are not optimized, waiting for upstream processes to complete. This downtime doesn’t just represent wasted potential—it’s a missed opportunity to maximize overall equipment effectiveness (OEE). Machines are valuable capital assets, and their underutilization can delay order fulfillment, reduce throughput, and create a bottleneck that amplifies inefficiency across the shop floor. Over time, this can even lead to underperformance penalties in client contracts.
Solution: Advanced scheduling software can provide real-time updates on process status, dynamically adjusting the schedule to keep machines running efficiently. Manufacturers can synchronize equipment usage with workflow demands by investing in automated scheduling systems that use data analytics. These systems can predict potential slowdowns and rearrange tasks to optimize machine productivity, ensuring minimal idle time and increased asset utilization.
2Inefficient Use of Skilled Labor During High-Demand Periods:
Production peaks and valleys often create significant labor inefficiencies. High-demand periods may force manufacturers to rely heavily on overtime or bring in temporary workers, which drives up costs and increases the risk of burnout among permanent staff. Conversely, skilled labor may be underutilized during low-demand periods, reducing overall productivity and leaving workers feeling disengaged and undervalued.
Solution: Implementing a robust workforce management system can optimize labor allocation by predicting high-demand periods and scheduling staff accordingly. This system should also support cross-training initiatives, enabling workers to cover multiple roles as needed. Cross-training improves workforce flexibility, allowing employees to adapt to various tasks seamlessly, minimizing overtime expenses, and reducing the negative impact of fluctuating demand on productivity.
3Misallocation of Specialized Technicians to Low-Priority Tasks:
Specialized technicians are often overqualified for routine work but perform low-priority tasks due to poor scheduling. This misallocation wastes their unique skills and delays more critical, high-impact maintenance or process improvement activities. Furthermore, it can demotivate these highly skilled employees, as they become frustrated performing work that does not leverage their expertise.
Solution: Employing a task management system that assigns jobs based on skill levels ensures that specialized technicians focus on the most important and technically demanding work. A competency-based task assignment strategy helps managers allocate resources where they provide the most value. Additionally, periodic skill audits can help ensure the workforce remains aligned with current operational needs, optimizing technician utilization and productivity.
4Miscommunication Between Departments Leading to Uncoordinated Workflows:
Siloed operations and lack of effective communication between departments can disrupt production schedules. When logistics, procurement, and quality control teams aren’t aligned, it creates bottlenecks and inefficiencies. For example, a delay in raw material delivery might not be promptly communicated to the production team, causing downtime and resource wastage. These misalignments can severely impact delivery timelines and customer satisfaction.
Solution: An integrated communication platform that offers real-time updates and visibility across departments can eliminate these bottlenecks. Regular interdepartmental meetings to review production goals and challenges can help keep everyone aligned. Ensuring that all departments have access to a shared data system reduces the likelihood of miscommunication and improves overall workflow efficiency.
5Unplanned Maintenance Due to Unbalanced Equipment Loads:
When production schedules aren’t designed to evenly distribute workloads, certain machines experience excessive strain, leading to faster wear and tear. Unplanned maintenance becomes a frequent and disruptive issue, causing unscheduled downtime and increasing the risk of prolonged operational shutdowns. This reactive maintenance approach escalates repair costs and disrupts workflow continuity.
Solution: Utilizing predictive maintenance and load-balancing strategies can significantly reduce unplanned maintenance. Sensors and data analytics can monitor equipment usage and performance, allowing teams to distribute workloads more evenly and perform maintenance proactively. Scheduled maintenance windows can be incorporated into production plans, ensuring that maintenance activities do not interfere with critical production runs.
6Suboptimal Use of Flexible Work Schedules During Fluctuating Demand:
Rigid, traditional work schedules are often ill-suited for the ebb and flow of manufacturing demand. When demand spikes, a fixed workforce may struggle to keep up, while labor costs escalate unnecessarily during slow periods. Inconsistent workforce planning also leads to underperformance, as employees may be overburdened or idle, affecting morale and productivity.
Solution: Flexible workforce strategies, such as on-demand staffing or flexible shift rotations, can mitigate these inefficiencies. Data-driven scheduling that anticipates demand fluctuations ensures labor resources are optimally used. Allowing employees to adjust shifts in response to production needs, clear communication, and well-defined policies can lead to smoother operations and a more engaged workforce.
7Strain on Logistics When Production Doesn’t Align with Transport Availability:
Logistical inefficiencies arise when production schedules fail to consider transportation timelines. Mismatches between manufacturing output and transportation availability can lead to expensive rush orders or the need for additional storage space. If deliveries are delayed or inconsistent, these strains not only increase operational costs but also jeopardize customer relationships.
Solution: Collaborating with logistics providers can help synchronize production schedules with transportation plans. Using just-in-time (JIT) principles and real-time inventory management systems ensures a streamlined flow of goods, minimizing extra storage and shipping costs. Regularly reviewing logistics performance and adjusting plans based on seasonal trends or market demands can further optimize efficiency.
8 Poor Utilization of Shared Resources Like Cranes and Forklifts:
Shared resources, such as cranes, forklifts, or loading docks, are often bottlenecks when schedules don’t account for availability. Inefficient resource allocation leads to downtime, waiting periods, and, in worst-case scenarios, safety incidents when workers rush to make up for lost time. This mismanagement negatively impacts productivity and creates hazardous working conditions.
Solution: Centralizing the scheduling and monitoring of shared resources can improve efficiency. A booking system that prioritizes tasks based on urgency and provides visibility into resource availability can reduce wait times and improve productivity. Training employees on resource-sharing protocols can also foster a safer and more organized work environment.
9Operator Fatigue from Mismanaged Workloads and Shift Patterns:
Operators who work in poorly managed shifts are more prone to fatigue, which leads to a higher likelihood of errors, accidents, and lower productivity. Erratic schedules that don’t consider human limitations can create a disengaged workforce prone to absenteeism, further complicating scheduling and output.
Solution: Shift optimization strategies should consider the operator’s well-being. Using fatigue management tools, ergonomic shift designs, and ensuring sufficient rest periods between shifts can improve efficiency and reduce workplace accidents. Additionally, rotating high-intensity tasks among employees can help maintain consistent productivity levels and reduce fatigue-related errors.
10Reactive Problem-Solving from Schedule Crises:
Ineffective production scheduling leads to a constant cycle of reactive problem-solving, where managers spend more time putting out fires than planning strategically. This short-term focus prevents investment in process improvements and limits the organization’s ability to adapt to new opportunities or mitigate risks. The inability to plan proactively keeps operations stuck in a cycle of inefficiency.
Solution: Allocating time for regular performance reviews and strategic planning can encourage a proactive culture and break this cycle. Lean management practices, such as continuous improvement initiatives, can help teams anticipate challenges and incrementally improve processes. Empowering employees to contribute ideas for efficiency improvements fosters innovation and long-term operational gains.
Conclusions for Operations Leaders
Unseen drains on profit, like inefficient production scheduling, have far-reaching impacts that silently erode your margins. From unplanned maintenance costs to the misalignment of labor and resources, these hidden inefficiencies can create significant financial challenges. Recognizing and addressing these areas is crucial to maintaining productivity and staying competitive.
With our tailored consulting services and the introduction of DPS—our advanced Digital Production System—your manufacturing business can achieve unprecedented efficiency and productivity.
How POWERS Can Help
Our team has the expertise and technology to transform your production scheduling and operational efficiency. Here’s how our DPS solution empowers your organization:
- End-to-End Production Visibility: Track every aspect of your production process in real-time with comprehensive dashboards that highlight inefficiencies and identify opportunities for improvement.
- Optimized Resource Allocation: Leverage AI-driven insights to efficiently schedule labor and equipment, ensuring every resource is utilized to its fullest potential.
- Proactive Maintenance Strategies: Predict equipment failures before they occur and schedule maintenance during optimal windows, reducing unplanned downtime and extending machinery lifespan.
- Seamless Cross-Department Communication: Streamline workflows and improve coordination across departments, reducing delays caused by miscommunication and ensuring everyone has the data they need to excel.
- Smart, Data-Driven Scheduling: Utilize predictive algorithms to balance production loads, adapt to demand fluctuations, and keep operations running smoothly, even in the most complex environments.
Ready to Elevate Your Manufacturing Operations with Real-Time Data and AI-Driven Insights?
At POWERS, our commitment goes beyond consultation. We deliver a comprehensive approach tailored to your needs, combining decades of industry expertise with cutting-edge AI technology. With DPS, your organization gains the tools to pinpoint inefficiencies and implement sustainable solutions that drive profitability and growth.
Let’s discuss how we can transform your production systems and elevate your manufacturing operations.
- Speak to an Expert: Call +1 678-971-4711 to discuss your specific challenges and goals.
- Email Us: Get tailored insights by emailing info@thepowerscompany.com
- Request an Assessment: Use our online contact form, and one of our expert manufacturing consultants will reach out to schedule an in-depth analysis of your operations.
Continue Reading from this Mastery Series
- Part 1 – How Poor Scheduling Burns Through Your Profit Margins
- Part 2 – How Hidden Energy Wastes Burn Through Your Bottom Line
- Part 3 – How Dead Weight in Your Safety Stock Undermines Your Bottom Line
- Part 4 – The Hidden Costs of Ignoring Preventive Maintenance Programs
- Part 5 – Mismatched Skills and Wasted Workforce Potential
- Part 6 – Poor Quality Control is Dragging Down Your Productivity and Profits
- Part 7 – Being Slow to Market Undermines Your Bottom Line
- Part 8 – Supplier Missteps That Drain Profitability
- Part 9 – The Cost of Continuing to Use Manual Processes
- Part 10 – The Financial Fallout of Fragmented Compliance