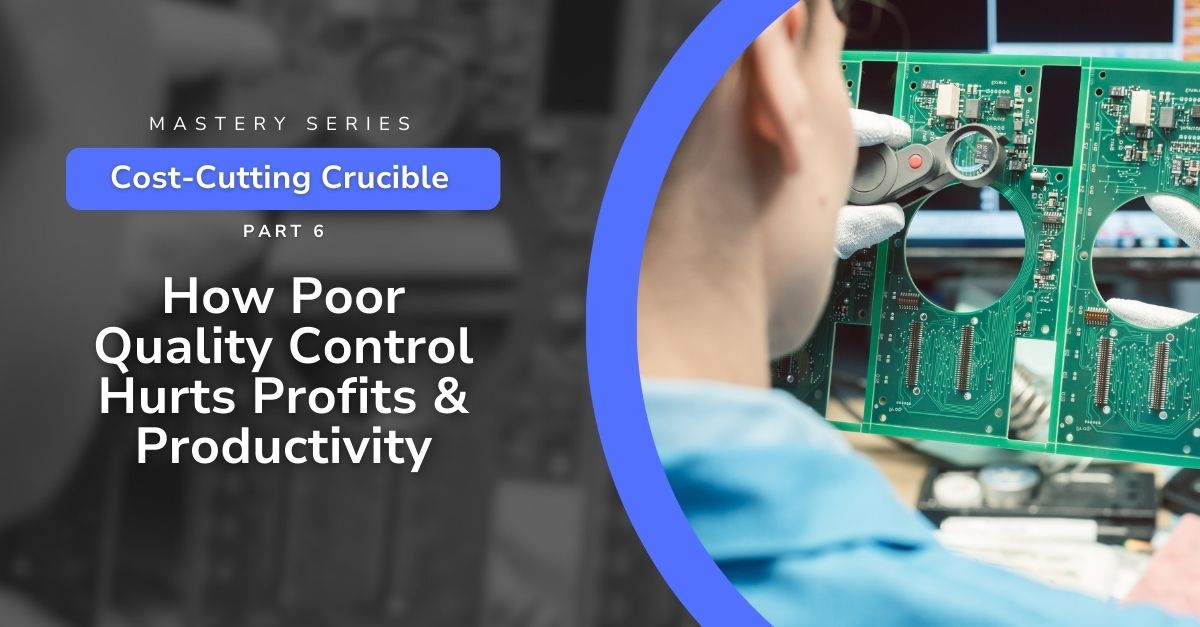
For manufacturers, significant financial drains often occur quietly in the background, hidden within quality-related costs from scrap, rework, and returns.
These overlooked costs create secondary issues that can ripple through production, gradually eroding profitability.
The impact of excessive quality-related costs often goes far beyond the direct expense of wasted materials. Take, for example, the downstream consequences of a slight misalignment in a machine part. This minor oversight can lead to consistent inaccuracies in production output, requiring rework or resulting in returned items due to quality issues. This mechanical misalignment also forces operators to make frequent adjustments, interrupting workflow and adding unplanned machine downtime. Over time, these disruptions can diminish production capacity, as more labor hours are devoted to corrective actions instead of completing scheduled tasks. And because such quality issues may not appear severe enough to trigger immediate action, they often go unnoticed, steadily draining profitability.
When managers investigate these secondary symptoms more deeply, they uncover a web of hidden costs. The added burden on labor, the extra time spent on machine recalibrations, and the unforeseen inventory delays represent unseen drains on profit that quietly hinder productivity.
Addressing these hidden costs, especially in quality control, requires more than surface-level adjustments. It involves a strategic approach to understanding the less obvious ways quality-related issues can negatively impact overall performance and financial results.
1Inconsistent Application of Quality Checks
Issue: When quality checks are inconsistently applied, it creates variations in product quality, leading to defects slipping through unnoticed. For example, one shift might implement strict inspection protocols while another applies them less rigorously, causing inconsistent quality levels across production cycles. Over time, this disparity increases rework, scrap, and returns, adding to operational costs and eroding profitability. Inconsistencies also affect customer perception of quality, impacting brand reputation.
Mitigation: Use detailed checklists and consistent monitoring tools to standardize quality protocols and reinforce compliance across all shifts. Conduct training sessions to keep team members updated on quality requirements and ensure adherence to these protocols. Using automated quality control systems can further reduce the impact of human error, and implementing regular audits can help maintain consistent quality standards across shifts.
2Underreporting of Minor Defects Leading to Customer Dissatisfaction:
Issue: Minor defects are often underreported, especially when seen as non-critical or unlikely to impact functionality. However, these small flaws can build up over time, creating a larger quality control issue that ultimately reaches the customer. Even minor defects can damage customer trust and increase the rate of returns, not to mention the costs of managing these returns and replacing the products.
Mitigation: Create a quality-focused culture that encourages logging every defect, regardless of its perceived importance. Use defect-tracking software to record and analyze trends and share insights with the team to promote a proactive approach to quality. By linking defect reporting with feedback on cost impacts, you can better understand how even minor defects can influence profitability and customer satisfaction.
3Poor Handoff of Quality Standards Across Shifts:
Issue: Quality standards can degrade during shift changes, particularly if information transfer is informal or insufficiently documented. When standards and expectations are not communicated, the next shift may inadvertently apply inconsistent quality checks, causing increased scrap and rework rates. This lack of continuity in quality standards affects productivity and results in hidden costs from rework and scrap materials.
Mitigation: Implement structured shift-change protocols to ensure seamless handoffs. Use digital logging tools where operators can document any quality issues encountered during their shifts, creating a transparent and detailed record for the next team. Supervisors can review these digital records, ensuring accountability and helping standardize quality expectations across shifts.
4Over-reliance on Visual Inspection Instead of Precise Measurements:
Issue: Visual inspection alone is inherently subjective and limited in detecting subtle defects, leading to errors that may not be detected until later stages. While visual checks have their place, over-reliance on them can result in defects going unnoticed, ultimately increasing rework and scrap rates. Additionally, visual inspection fatigue, especially over extended periods, can lead to further inconsistencies in quality.
Mitigation: Incorporate precise measurement tools for critical inspection points to ensure reliable quality assessment. Train employees on using measurement equipment and calibrate these tools regularly to maintain accuracy. Implement a mix of both visual and measurement-based quality checks, with measurement checks for areas where minor defects can significantly affect product performance or customer satisfaction.
5Over-dependence on Last-Minute Inspections:
Issue: Last-minute inspections, conducted solely at the end of the production line, can be too late to correct defects without costly rework or scrapping entire batches. Final-stage inspections might catch problems, but by this point, the costs associated with correcting them are high, involving additional labor, material waste, and potential delivery delays.
Mitigation: Adopt in-process inspections that allow quality issues to be identified and addressed at earlier stages. By implementing checks at strategic points throughout production, teams can catch and resolve issues before they accumulate, reducing the need for end-stage rework and lowering overall scrap levels. Early-stage quality interventions save costs and contribute to more efficient workflows and faster production cycles.
6Misallocation of Skilled Labor to Remedial Tasks:
Issue: Skilled labor is often diverted to address quality issues, impacting core operational productivity. Instead of focusing on their primary tasks, skilled workers spend valuable time fixing preventable quality problems, slowing production and causing delays. This misallocation of resources represents a hidden cost, as highly trained employees are not fully utilized for their intended roles.
Mitigation: Clearly define roles related to quality ownership so skilled labor can stay focused on primary tasks. Invest in cross-training other team members in quality control basics so that skilled workers are less frequently diverted. For larger facilities, consider establishing a dedicated quality assurance team to handle quality-related tasks, freeing up skilled operators to drive productivity improvements in their specialized areas.
7Lack of Knowledge About the Cost Impact of Returns:
Issue: Many employees, from operators to mid-level managers, may not fully appreciate the financial burden that returns place on the company. This lack of awareness can lead to a lower emphasis on quality, inadvertently increasing defect rates and returns. Returns are costly and time-consuming, affecting resources that could be used more effectively elsewhere.
Mitigation: Provide cost awareness training highlighting the full impact of returns on profitability. Use case studies or examples of recent returns to show how even minor issues can lead to significant financial losses. By increasing transparency and data-sharing regarding return-related costs, you can foster a team-wide commitment to quality that reduces the likelihood of returns.
8Overlooking Minor Rework Issues That Accumulate Over Time:
Issue: Small rework tasks may seem insignificant when considered individually. However, they accumulate and contribute to substantial labor and material costs over time. When left unchecked, these minor adjustments can disrupt workflow, increase cycle times, and consume resources that could be allocated to higher-value tasks.
Mitigation: Implement a systematic approach to track and analyze rework data to identify and address recurring issues. By pinpointing the root causes behind frequent rework activities, managers can prevent similar issues from occurring, saving valuable resources and improving the efficiency of the production line. Encourage a culture where even small errors are taken seriously to prevent them from becoming major cost drivers over time.
9Poor Escalation Processes for Complex Quality Issues:
Issue: When complex quality problems arise, poor escalation processes can cause delays in resolution. These issues often remain unresolved without a clear protocol, leading to prolonged downtime, additional rework, and increased scrap rates. Furthermore, unresolved quality issues can lead to widespread disruptions, impacting production schedules and overall productivity.
Mitigation: Establish a clear and formal escalation protocol to ensure that complex quality issues receive prompt attention. Define criteria for when and how problems should be escalated and assign team members with the expertise to handle these escalations. Training employees to recognize when an issue requires escalation can significantly reduce the time it takes to address complex quality issues, preventing costly delays and downtime.
10Limited Ability to Apply Lean Techniques to Reduce Scrap:
Issue: Lean principles, such as root cause analysis and value stream mapping, can be highly effective in minimizing waste, yet they are often underutilized for reducing scrap. Without lean techniques, companies miss opportunities to identify and eliminate inefficiencies that contribute to high scrap rates. This limitation increases material costs and affects overall profitability.
Mitigation: Review scrap data regularly and engage lean experts to identify the root causes of waste. Integrate lean techniques like kaizen events, 5S, and value stream mapping into the quality process to reduce scrap rates. By encouraging a culture of continuous improvement, manufacturers can systematically address inefficiencies and reduce quality-related costs over time, resulting in a leaner, more cost-effective operation.
Conclusions for Operations Leaders
Excessive quality-related costs from scrap, rework, and returns represent a significant yet often overlooked drain on manufacturing profitability. Addressing these hidden profit leaks isn’t just about reducing material waste; it’s about strategically enhancing productivity and uncovering the underlying issues that impact efficiency on the shop floor. By proactively managing these hidden costs, manufacturers can improve workflow, reduce unplanned downtime, and boost operational effectiveness.
Our approach goes beyond traditional consulting—we equip you with DPS, our advanced Digital Production System designed to directly bring real-time data and AI-driven insights to your operations. With DPS, we help you identify and eliminate costly inefficiencies and empower your team to make data-driven decisions that lead to sustainable growth.
Here’s how POWERS and DPS can elevate your productivity:
- Real-Time Production Visibility: DPS offers complete transparency into production lines, enabling managers to spot inefficiencies as they happen and make immediate adjustments.
- Enhanced Team Collaboration: DPS fosters a connected environment, allowing seamless communication across shifts and teams, reducing miscommunication that can lead to errors and material waste.
- Data-Driven Decision-Making: Using the power of AI, DPS provides actionable insights to improve resource allocation and ensure your workforce and materials are used to their full potential.
- Continuous Improvement Tools: DPS enables you to track quality metrics, pinpoint recurring quality issues, and implement long-term process improvements that enhance productivity.
Ready to tackle hidden profit leaks in your manufacturing operations? Partner with POWERS to harness real-time data and AI insights through DPS, transforming how you manage quality, efficiency, and productivity. Let us help you drive sustainable results, lower costs, and maximize profitability in today’s competitive manufacturing landscape.
- Speak to an Expert: Call +1 678-971-4711 to discuss your specific challenges and goals.
- Email Us: Get tailored insights by emailing info@thepowerscompany.com
- Request an Assessment: Use our online contact form, and one of our expert manufacturing consultants will reach out to schedule an in-depth analysis of your operations.
Continue Reading from this Mastery Series
- Part 1 – How Poor Scheduling Burns Through Your Profit Margins
- Part 2 – How Hidden Energy Wastes Burn Through Your Bottom Line
- Part 3 – How Dead Weight in Your Safety Stock Undermines Your Bottom Line
- Part 4 – The Hidden Costs of Ignoring Preventive Maintenance Programs
- Part 5 – Mismatched Skills and Wasted Workforce Potential
- Part 6 – Poor Quality Control is Dragging Down Your Productivity and Profits
- Part 7 – Being Slow to Market Undermines Your Bottom Line
- Part 8 – Supplier Missteps That Drain Profitability
- Part 9 – The Cost of Continuing to Use Manual Processes
- Part 10 – The Financial Fallout of Fragmented Compliance