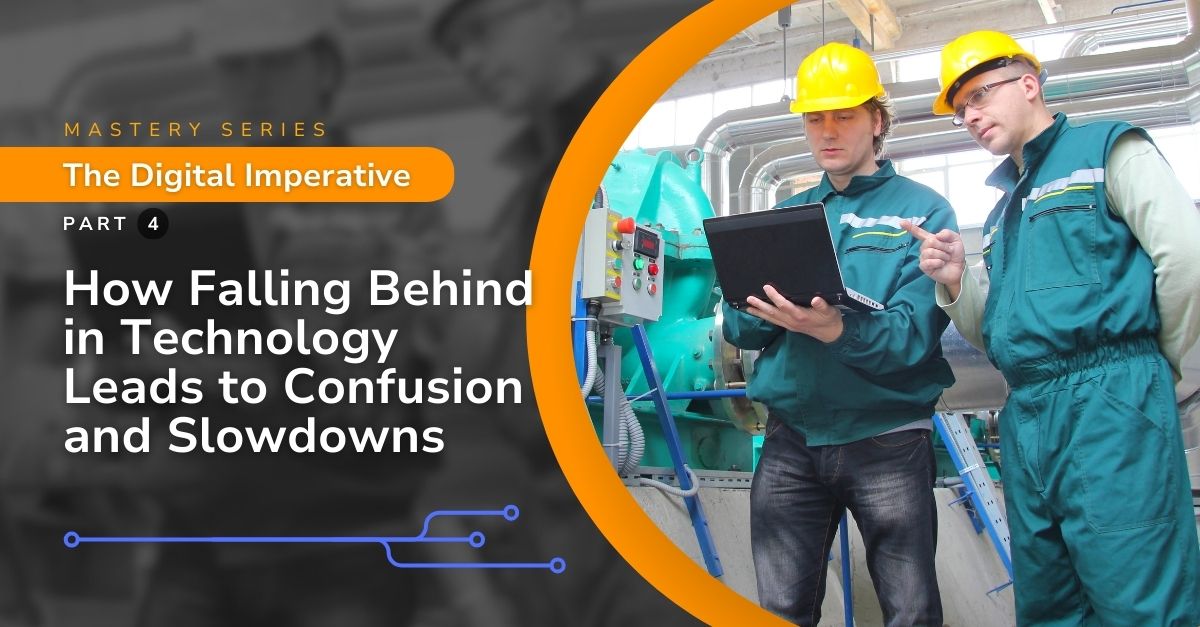
One of the most significant consequences of organizations failing to embrace Industry 4.0 and neglecting digital transformation is the breakdown of collaboration and communication across departments.
This lack of connectivity often goes unnoticed in the short term but can lead to major inefficiencies and lost productivity in the long run.
Without these systems, manufacturers rely on outdated, manual processes that create gaps in information flow and delay critical decision-making.
A less common but equally damaging example is the misalignment between machine operators and quality assurance (QA) teams. When operators detect potential quality issues, they may rely on manual logs or verbal communication to inform the QA team. In a digital-first environment, real-time alerts and shared dashboards could immediately notify QA of the issue, allowing for a swift investigation and corrective action. Without these tools, the time between detection and resolution increases, often producing more defective products before the problem is addressed.
The failure to implement digital tools leads to numerous secondary symptoms related to ineffective collaboration and communication. These issues manifest in delayed responses to production problems, miscommunication of goals, and siloed decision-making, all of which reduce overall efficiency.
The nuts and bolts of these issues highlight how digital transformation is not just a technological upgrade but a critical strategy to improve communication and collaboration on the shop floor. Embracing Industry 4.0 is key to breaking down these barriers and ensuring teams are aligned and equipped with the information they need to drive productivity.
1Delayed Response Times to Production Issues:
When communication tools and collaboration platforms are outdated or nonexistent, production issues that require quick responses are often delayed. In a modern factory, a minor equipment malfunction can cascade into significant downtime if maintenance teams aren’t notified in real time. Without proper digital tools, these delays can last longer than necessary and cost significantly more, exacerbating the problem and reducing productivity.
Mitigation: Implementing real-time communication tools like mobile-enabled alerts and collaboration platforms can drastically reduce response times. These tools can automatically notify the appropriate team members when issues arise, streamlining the troubleshooting process. Managers can monitor response metrics to ensure timely interventions, leading to less downtime and smoother production cycles.
2Miscommunication of Production Goals Across Departments:
Without a unified digital platform, departments can easily fall out of sync, leading to miscommunication of production goals. For instance, production suffers if sales set unrealistic targets without considering the shop floor’s capacity. This disconnect causes frustration, missed deadlines, and wasted resources.
Mitigation: Integrating ERP systems (Enterprise Resource Planning) allows all departments to align their objectives in real time. With such a system, production teams can receive immediate updates on order volumes and timelines, ensuring that expectations are managed and met effectively. Consistent alignment between departments prevents bottlenecks and improves resource utilization.
3Inconsistent Coordination Between Design and Production Teams:
A lack of coordination between design and production teams is a frequent source of frustration. If design changes are not communicated effectively to production, errors in execution become more common. Misaligned processes between these teams can lead to rework, defects, and increased waste on the shop floor.
Mitigation: Digital twin technology can serve as a bridge between design and production teams. Design teams can collaborate seamlessly with production personnel by creating virtual models that simulate the production process, ensuring that changes are communicated and implemented correctly. This reduces rework, improves product quality, and enhances efficiency.
4Misinterpretation of Customer Feedback by Production Teams:
When customer feedback is not effectively communicated to production teams, the result is often product deviations that don’t meet customer needs. This miscommunication can lead to defects, increased returns, and dissatisfied customers, eroding a company’s competitive edge.
Mitigation: Establishing a closed-loop feedback system where real-time customer data is shared across all departments can address this issue. CRM (Customer Relationship Management) software can be integrated with production tools to ensure that any feedback or product adjustments are communicated to the shop floor. This proactive approach ensures that production teams are always aware of customer needs and can adjust accordingly.
5Poor Feedback Loops from Frontline Employees to Management:
Critical issues go unnoticed when feedback loops between frontline employees and management are inefficient. Workers on the shop floor often spot problems before they become major issues, but without a formal communication channel, these insights may never reach management.
Mitigation: Implementing digital communication platforms that allow frontline employees to report issues in real time can significantly improve productivity. These systems enable management to identify recurring problems, prioritize solutions, and make data-driven decisions that improve overall operations. Engaging employees in this process also boosts morale and creates a company culture of continuous improvement.
6Inefficient Handoff Between Shifts:
In many factories, the handoff between shifts is a weak point in the production process. Without a proper communication mechanism, vital information about equipment status, outstanding tasks, or unresolved issues may be missed, leading to slow start ups or unnecessary downtime at the beginning of each shift.
Mitigation: Digital logbooks and shift management software can streamline the transition between shifts by providing a centralized platform where shift leaders can log updates, issues, and ongoing tasks. Incoming teams can quickly review this information, ensuring a smooth and efficient handoff with minimal disruption to productivity.
7Increased Errors in Order Processing Due to Unclear Instructions:
Order processing errors are more common in manual or poorly automated environments because of unclear or outdated instructions. Misinterpretations or omissions lead to incorrect production runs, wasted materials, and delays in fulfilling customer orders.
Mitigation: A robust Manufacturing Execution System (MES) that connects order processing directly to production instructions ensures no ambiguities. Digital work instructions can be updated in real-time, reducing errors and ensuring that each order is processed correctly and efficiently, leading to fewer mistakes and improved customer satisfaction.
8Lack of Real-Time Data Sharing Between Teams:
One of the core issues in a disconnected production environment is the lack of real-time data sharing. If teams operate with outdated information, they may make decisions based on incorrect assumptions, leading to inefficiencies, bottlenecks, and unnecessary production delays.
Mitigation: Introducing IoT (Internet of Things) sensors and real-time data platforms allows for seamless data sharing between teams. Managers and operators can access live production data, adjust workflows as needed, and make more informed decisions. Real-time visibility empowers teams to collaborate more effectively and improve overall productivity.
9Inability to Troubleshoot Equipment Malfunctions Quickly:
Without proper collaboration tools, equipment malfunctions take longer to diagnose and resolve. When technicians don’t have the right information, they may spend valuable time searching for manuals, consulting with other teams, or testing ineffective solutions.
Mitigation: Providing technicians with mobile access to equipment data, digital manuals, and real-time monitoring systems significantly speeds up troubleshooting. By leveraging predictive maintenance tools, teams can proactively address issues before they lead to costly downtime, reducing the overall impact on production.
10Siloed Decision-Making Among Department Heads:
In traditional manufacturing settings, department heads often operate in silos, making decisions without considering their impact on other areas of the business. This lack of cross-functional collaboration can lead to disjointed strategies, inefficient resource allocation, and poor overall performance.
Mitigation: Cross-functional digital platforms that integrate data from all departments foster a culture of transparency and collaboration. Regular cross-department meetings facilitated by data-driven insights ensure that decisions are made with the broader organization in mind. This leads to better resource allocation, improved decision-making, and a more cohesive production process.
Conclusions for Operations Leaders
Neglecting digital transformation isn’t just a missed opportunity—it’s a direct path to inefficiencies that can cripple manufacturing operations. The secondary symptoms of ineffective collaboration and communication, such as delayed response times, miscommunication across departments, and siloed decision-making, are preventable with the right tools and strategies. Industry 4.0 technologies enable manufacturers to stay agile, streamline processes, and make data-driven decisions directly impacting the bottom line.
At POWERS, we understand the challenges of digital transformation and know that it goes beyond merely adopting new technologies. Our approach is centered around guiding manufacturers through the complexities of integrating real-time data systems, optimizing communication workflows, and fostering collaboration across the entire operation. We provide more than just advice—we deliver actionable solutions tailored to improve productivity and profitability.
Our expertise, combined with the introduction of our Digital Production System (DPS), gives you the tools to transform your manufacturing operations from the ground up. Here’s how POWERS can help you enhance productivity and efficiency:
- Real-Time Operational Insights: Gain a clear, real-time view of your production processes to identify bottlenecks and inefficiencies as they occur.
- Seamless Communication: Enable instant data sharing across departments, improving coordination and reducing errors in order processing.
- Advanced Predictive Tools: Leverage AI-driven insights to forecast potential equipment malfunctions and prevent costly downtime.
- Streamlined Shift Handoffs: Reduce downtime during shift changes with digital handoff systems that keep all team members informed and ready to act.
POWERS is committed to helping manufacturers evolve with Industry 4.0 technologies, ensuring you catch up and stay ahead. Whether you’re struggling with communication breakdowns or operational inefficiencies, we’re here to guide you toward a more productive future.
Ready to unlock the full potential of your manufacturing operations? Contact POWERS today to learn how we can help you navigate the complexities of digital transformation and optimize your business for long-term success.
- Speak to an Expert: Call +1 678-971-4711 to discuss your specific challenges and goals.
- Email Us: Get tailored insights by emailing info@thepowerscompany.com
- Request an Assessment: Use our online contact form, and one of our expert manufacturing consultants will reach out to schedule an in-depth analysis of your operations.
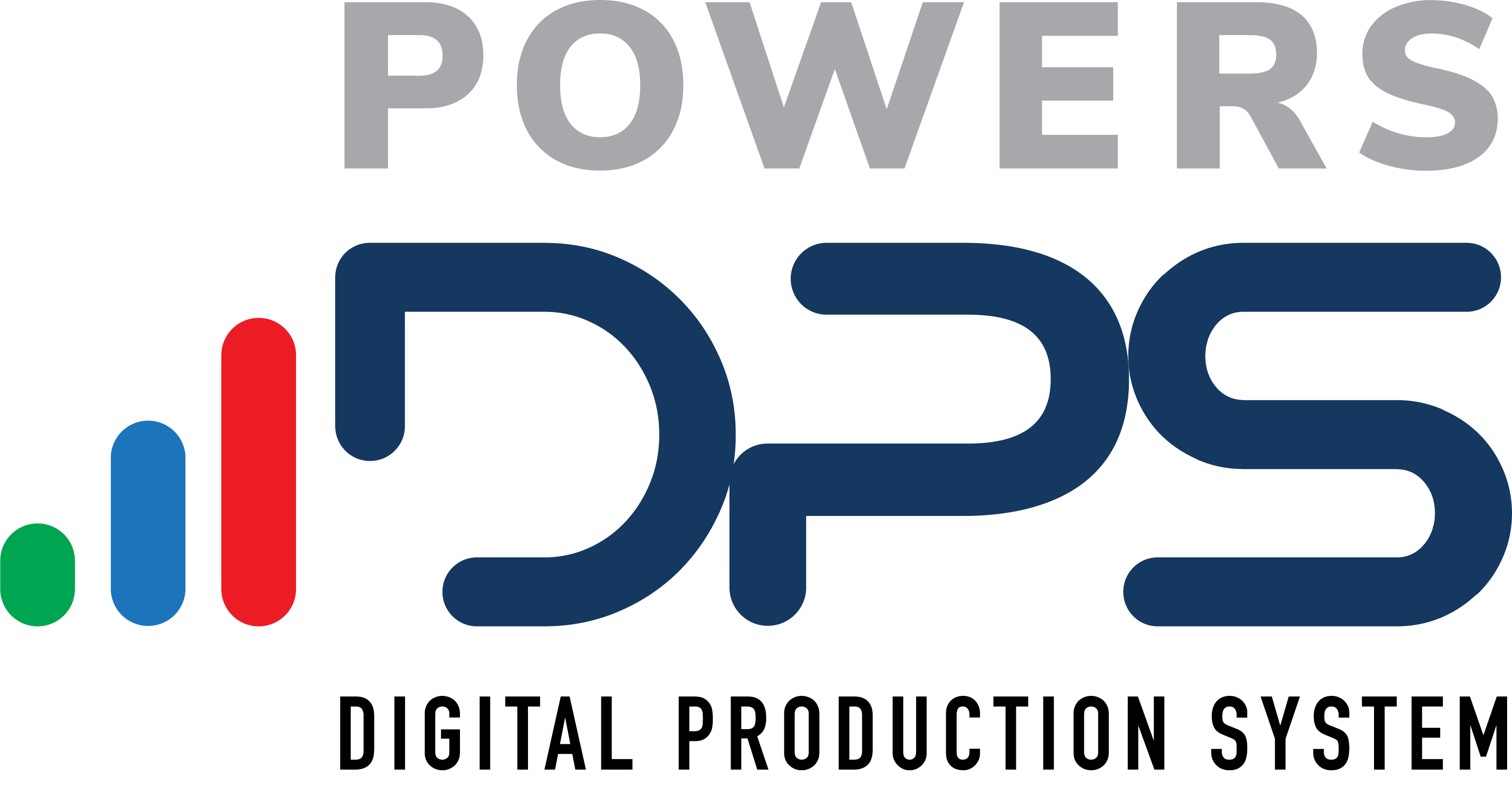
Start transforming your operations today with POWERS DPS. Contact us for a free consultation and see how digital transformation can revolutionize your manufacturing future. Learn More about DPS
Continue Reading from this Mastery Series
- Part 1 – Outdated Tech is Weakening Your Talent Pipeline
- Part 2 – How Legacy Systems Sabotage Your Cybersecurity and Productivity
- Part 3 – How Ignoring Digital Tools Leaves You Vulnerable to Downtime
- Part 4 – When Digital Stagnation Leads to Poor Communication and Production Chaos
- Part 5 – The Real Cost of Trying to Keep Up in the Market Without Digital Transformation
- Part 6 – Missing Out on Real-Time Data Drains Productivity and Profit
- Part 7 – How Failing To Go Digital Jeopardizes Regulatory Compliance
- Part 8 – How Outdated Inventory Practices Sabotage Your Operations
- Part 9 – Limited Customization Options are Driving Your Customers Away
- Part 10 – The Productivity Trap of Failing to Scale Digital Initiatives