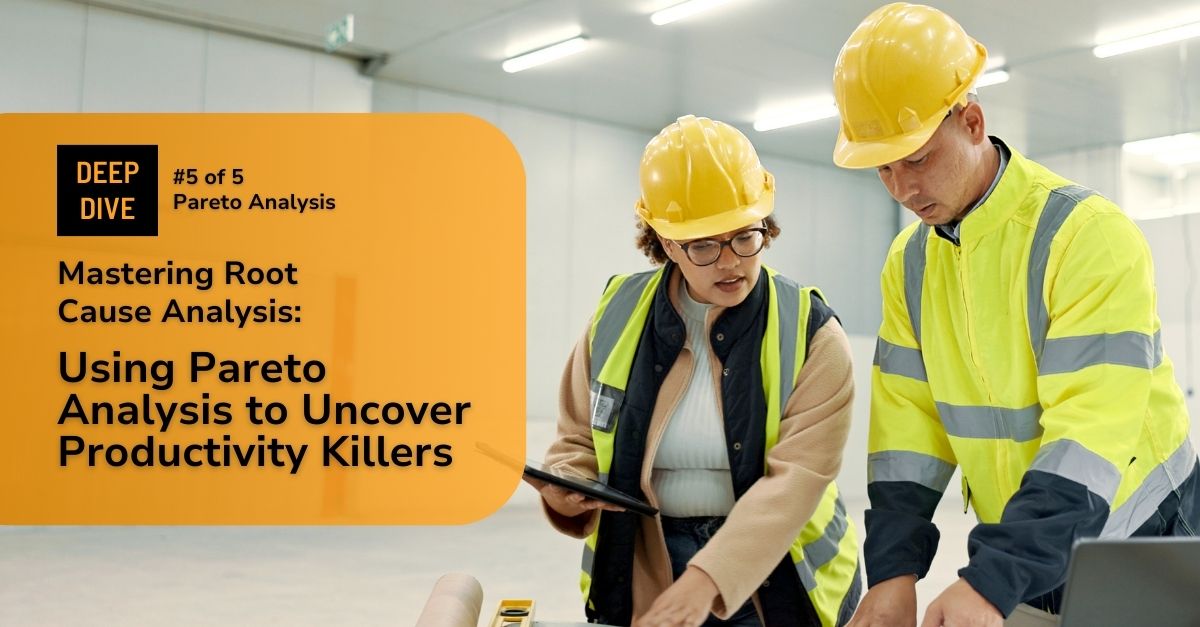
Among the various root cause analysis techniques critical to the success of the manufacturing industry, Pareto Analysis stands out for its effectiveness in pinpointing the most significant factors contributing to problems.
We dive deeper into the importance of Pareto Analysis, the steps to perform it, its applications, benefits, and potential challenges.
Understanding Pareto Analysis
Pareto Analysis is a statistical technique that helps identify the most significant factors contributing to a problem. Named after the Italian economist Vilfredo Pareto, this analysis is based on his observation that 80% of Italy’s wealth was owned by 20% of the population.* In a broader context, the Pareto Principle suggests that 80% of problems are typically caused by 20% of the causes.
This concept can be applied to various aspects of manufacturing, from identifying production defects to understanding equipment failures. Manufacturers can significantly improve their operations by identifying and addressing these critical issues.
Why Use Pareto Analysis in Manufacturing?
Pareto Analysis is an invaluable tool for the manufacturing industry because it enables companies to efficiently identify and address the most significant issues impacting the productivity of their operations. By focusing on the principle that 80% of problems are typically caused by 20% of the causes, manufacturers can prioritize their efforts on the areas that will have the highest impact.
This targeted approach enhances problem-solving efficiency and optimizes resource allocation, ensuring that time, money, and manpower are directed toward the most impactful issues. Moreover, Pareto Analysis helps uncover hidden patterns and trends in production data, providing deeper insights into underlying problems. As a result, manufacturers can achieve higher-quality products, reduce downtime, and increase overall productivity, making Pareto Analysis a cornerstone of effective root-cause analysis in the manufacturing sector.
Steps to Perform Pareto Analysis
Step 1Identify Problems and Causes
The first step in Pareto Analysis is to collect data on the problems and their causes. This data can come from multiple sources, including production logs, maintenance records, quality control reports, and employee feedback. Gathering accurate and comprehensive information is crucial to ensure the analysis is effective. For instance, a manufacturer might record instances of machine breakdowns, noting the specific cause each time, such as lack of maintenance, operator error, or material defects.
Step 2Categorize and Quantify Data
Once the data is collected, it needs to be categorized into groups, such as equipment failures, human errors, or material defects. Each category should then be quantified in terms of frequency and impact. This quantification helps in understanding which issues are the most prevalent and damaging. For example, if a manufacturer finds that equipment failures occur more frequently than human errors, they might categorize and quantify the types of equipment failures to understand which specific machines or components are most problematic.
Step 3Create a Pareto Chart
A Pareto Chart is a visual tool used in Pareto Analysis. It consists of a bar graph showing each category’s frequency or impact and a cumulative line graph representing the cumulative percentage of the total problems. To create a Pareto Chart, plot the categories on the x-axis and their corresponding frequency or impact on the y-axis. The categories should be arranged in descending order of significance. This visual representation helps quickly identify the most significant issues. For example, a manufacturer might create a Pareto Chart showing that 80% of production defects are caused by 20% of the processes.
Step 4Analyze the Chart
By examining the Pareto Chart, you can identify the ‘vital few’ causes that contribute to the majority of problems. The leftmost bars typically represent the most significant issues. Focus on these critical areas for problem-solving efforts. Understanding these key contributors allows for more targeted and effective interventions. For instance, if the chart shows that a specific machine causes the majority of downtime, the manufacturer can prioritize maintenance or replacement of that machine to reduce overall downtime.
Applications in Manufacturing
Pareto Analysis has numerous applications in manufacturing. For example, a manufacturer might use this technique to identify the most common causes of equipment downtime or determine which defects are most prevalent in their products. The manufacturer can significantly reduce downtime and improve product quality by addressing these top issues. Case studies have shown substantial improvements in production efficiency and quality through the application of Pareto Analysis. For instance, a manufacturer who applied Pareto Analysis to their quality control processes found that a significant portion of defects were due to a single type of material flaw, leading them to switch suppliers and reduce defects by 50%.
Benefits of Using Pareto Analysis
This leads to improved production quality and efficiency and enhances decision-making processes. Additionally, by continuously applying Pareto Analysis, manufacturers can maintain a cycle of continuous improvement. This iterative process helps adapt to new challenges and sustain high performance. For example, regular Pareto Analysis can help a manufacturer stay ahead of potential issues by identifying trends in equipment wear and tear, allowing for proactive maintenance.
Challenges and Limitations
While Pareto Analysis is a powerful tool, it does have its challenges and limitations. Collecting accurate data can be difficult, and there is a risk of overlooking minor issues that may be critical. It is essential to regularly update the analysis to ensure it remains relevant and comprehensive. Despite these challenges, the benefits of Pareto Analysis far outweigh the potential drawbacks. Complementing Pareto Analysis with other root cause analysis techniques is important to ensure a holistic problem-solving approach. For example, combining Pareto Analysis with Fishbone Diagrams can help in visualizing the relationships between different causes of a problem.
Conclusion
In conclusion, Pareto Analysis is an invaluable technique for root cause analysis in the manufacturing industry. By focusing on the most significant issues, manufacturers can achieve substantial improvements in productivity and efficiency. Implementing Pareto Analysis allows for a more strategic approach to problem-solving, driving continuous improvement. As manufacturing environments become more complex, quickly and effectively identifying and addressing key issues becomes increasingly important.
How POWERS Can Help Boost Productivity
At POWERS, we specialize in enhancing manufacturing productivity through tailored, results-based management consulting. Our unique approach, ‘Operationalizing Your Culture,’ aligns organizational culture with behaviors and skills that drive higher productivity and efficiency.
Contact us today to learn how we can help you identify and address your most pressing issues, driving continuous improvement and maximizing your manufacturing efficiency.
- Speak to an Expert: Call +1 678-971-4711 to discuss your specific challenges and goals.
- Email Us: Get tailored insights by emailing info@thepowerscompany.com
- Request an Assessment: Use our online contact form, and one of our productivity experts will reach out to schedule an in-depth analysis of your operations.
References
* “Causes, Consequences and Dynamics of ‘Complex’ Distributions of Technological Activities: The Case of Prolific Inventors”. https://core.ac.uk/download/pdf/6380749.pdf
Continue Reading from this Mastery Series
- Part 1 – The 5 Whys Technique Deep Dive
- Part 2 – Utilizing the Fishbone Diagram Deep Dive
- Part 3 – Fault Tree Analysis (FTA) in the Manufacturing Industry
- Part 4 – Failure Mode and Effects Analysis (FMEA) Deep Dive
- Part 5 – Using Pareto Analysis to Uncover Productivity Killers