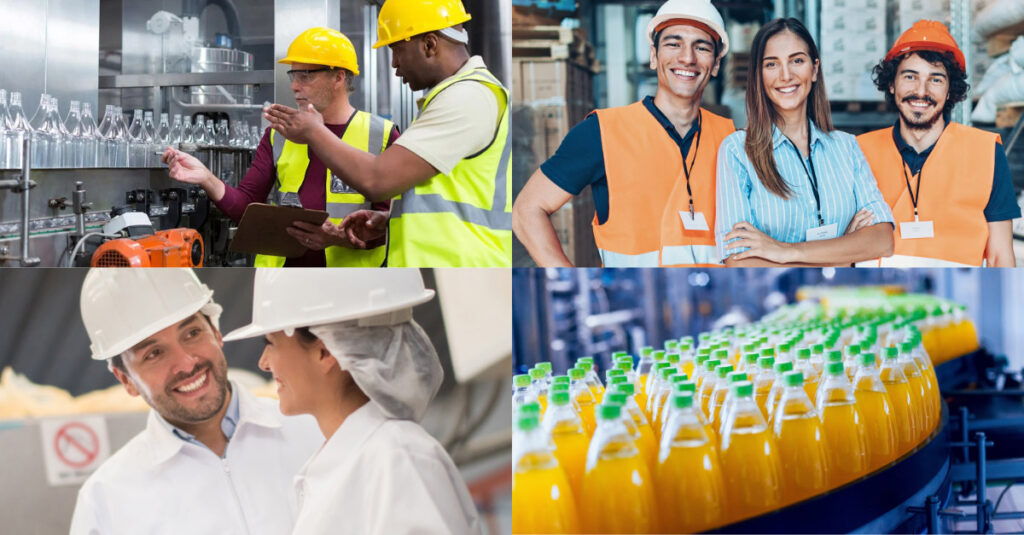
When we think of manufacturing operations and how to optimize them, we often focus on the tangible, measurable elements—streamlined processes, modern machinery, and the latest software. These are indeed crucial, but another vital yet often overlooked element is workplace culture.
Culture is the fabric of an organization. It’s the collective behaviors, beliefs, and values that characterize a group of people. In a manufacturing environment, it can significantly impact the overall efficiency of operations, particularly a key metric like Overall Equipment Effectiveness (OEE).
OEE is a standard for measuring manufacturing productivity. By combining availability, performance, and quality, OEE offers a balanced view of how well a manufacturing operation is running.
Culture as a Facilitator of Proactive Maintenance
A culture of accountability and ownership can foster an environment where machinery and equipment are well maintained and monitored. When each employee understands the significance of their role and treats the equipment as their own, it can result in higher machine availability, thus improving the OEE. Proactive and preventative maintenance become the norm, and breakdowns and unplanned downtime are minimized. Moreover, a collaborative culture that encourages knowledge sharing and cross-functional cooperation can lead to valuable insights and innovative solutions for optimizing equipment effectiveness, driving overall productivity gains in the manufacturing process.Culture and Performance
The way your workforce operates machinery directly impacts the performance element of OEE. In a culture that values quality and efficiency, operators will be more inclined to run machinery at optimal speeds and adhere to established standard operating procedures (SOPs).A culture of continuous improvement empowers employees to identify process bottlenecks and suggest enhancements, driving ongoing optimization of equipment performance and ultimately boosting overall manufacturing productivity.
They’ll also be more likely to communicate deviations promptly, enabling quicker corrections and minimizing performance impacts. Finally, a culture of open communication and empowerment encourages operators to share their insights and ideas for equipment optimization, creating a collaborative environment where innovation and efficiency thrive and further maximizing the performance element of OEE.
Culture’s Impact on Quality
Manufacturing defects significantly hamper the quality element of OEE. Cultivating a culture of continuous improvement and excellence can help keep defect rates low. When employees feel their input is valued, they’re more likely to suggest and implement process improvements that boost product quality.
Additionally, a culture that promotes adequate training and ongoing skill development can ensure workers are well-equipped to maintain high standards of quality. By integrating quality control measures into every stage of the manufacturing process and empowering employees to take ownership of quality outcomes, companies can establish a culture that not only enhances the OEE but also strengthens customer satisfaction and brand reputation.
Fostering a Culture for Higher OEE
Creating a culture that supports higher OEE isn’t something that happens overnight. It requires conscious effort and the commitment of everyone, from top-level management to the shop floor. Here are a few strategies:
1Encourage Open Communication:
Empower all employees to voice concerns, suggest improvements, and report issues. Open communication can uncover hidden bottlenecks or problems that hinder OEE.
2Reward and Recognize:
Regularly recognize and reward those who contribute to improving OEE. This encourages ownership and fosters a culture of continuous improvement.
3 Invest in Training:
Regular training sessions to upgrade skills and knowledge can boost employees’ confidence and performance, contributing to a higher OEE.
4Lead by Example:
Leaders and managers must exemplify the behaviors and attitudes they wish to see. Consistently adhering to SOPs, valuing proactive maintenance, and demonstrating a commitment to continuous improvement can shape a culture that positively influences OEE.
At the end of the day, a positive and engaged workplace culture is not just a ‘nice-to-have’ but a strategic advantage. Organizations that understand this and strive to build such a culture will see tangible benefits in their operational efficiency and bottom line. The machinery and software are crucial cogs in the manufacturing wheel, but let’s not forget the most important one: the people and the culture they create. By investing in people, you’re ultimately investing in improved OEE and greater operational efficiency.
The POWERS Difference
We are a dedicated and results-driven management consulting firm uniquely positioned at the intersection of workplace culture and operational performance. We partner with growth-oriented organizations to cultivate a culture of excellence that fuels productivity, drives efficiency, and strengthens competitive advantage.
Leveraging our deep industry expertise and innovative methodologies, we build synergies between people and processes, creating holistic, sustainable change that translates into measurable business outcomes.
Our team has helped executive leadership across many industries operationalize their culture for rapid and sustained performance improvement, increased competitive advantage, greater value, and a stronger bottom line.
To put our experienced team and proven track record to work for you, schedule an initial discovery and analysis by calling +1 678-971-4711, or emailing us at info@thepowerscompany.com