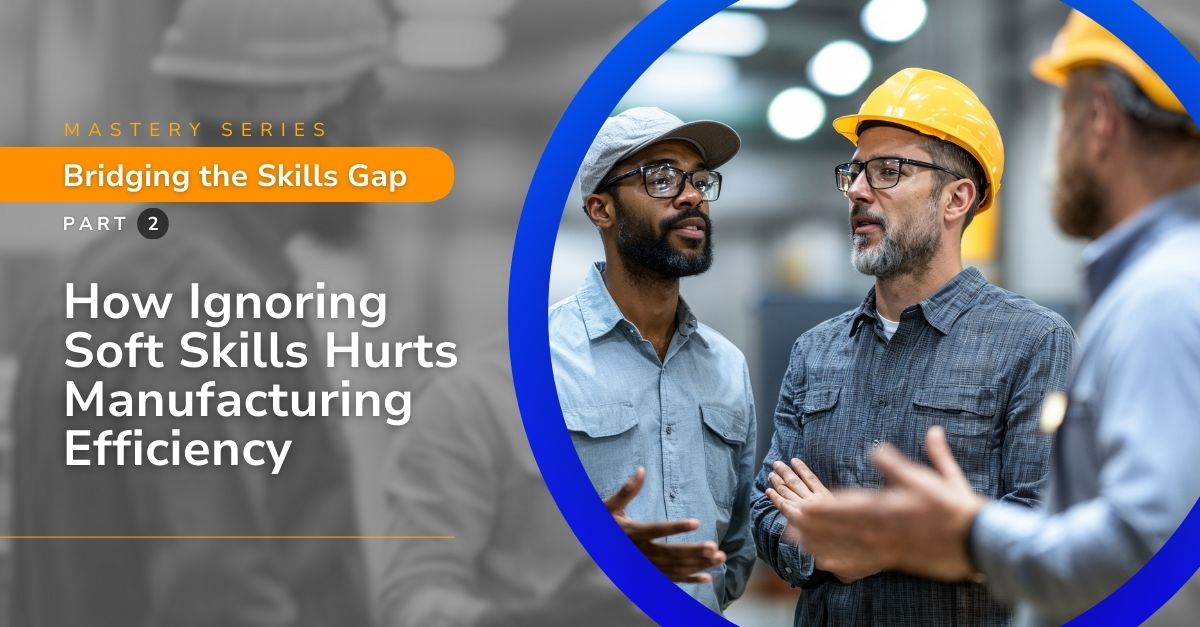
In manufacturing environments, where efficiency and precision are essential to maintaining productivity, non-technical skills are often overlooked.
While technical abilities remain essential, many organizations fail to recognize that non-technical skills like communication, adaptability, and problem-solving are critical to operational success.
These challenges aren’t immediately obvious but manifest over time as secondary symptoms, creating complex issues that experienced managers must tackle on the shop floor.
For instance, a common yet underappreciated issue involves the inability to identify inefficiencies early in the production process. When teams lack collaboration and cross-functional communication skills, they often fail to share observations about small deviations or inconsistencies in production runs.
What could have been an easy fix, like adjusting machinery settings or recalibrating tools, becomes a bigger problem when unnoticed by one department and not communicated to another. This can result in defective products, unnecessary downtime, or costly rework—all of which diminish productivity.
These problems highlight a larger trend: the growing importance of non-technical skills. As manufacturing continues to evolve with automation and new technologies, employees are expected to manage these advancements through teamwork, clear communication, and rapid adaptability.
Without the proper investment in upskilling these areas, companies face longer problem-solving cycles, increased miscommunication, and strained leadership roles; all hamper productivity and efficiency on the shop floor. Neglecting to address the development of non-technical skills can create operational bottlenecks that ripple through the entire manufacturing process.
1Slower Problem-Solving During Operational Challenges:
Minor operational issues can snowball into significant disruptions when non-technical skills like critical thinking and problem-solving are underdeveloped. On the shop floor, where rapid decision-making is often required, employees without these skills rely solely on their technical abilities. This limited problem-solving capacity can slow production as workers struggle to address unexpected issues effectively.
Mitigation: Organizations must invest in training programs that develop critical thinking and decision-making skills in real-world contexts to mitigate this. Encouraging cross-departmental collaboration and problem-solving exercises can expose employees to diverse viewpoints, enabling them to approach operational challenges holistically.
2Misinterpretation of Instructions or Goals, Leading to Errors:
Communication is a key non-technical skill that directly impacts productivity. Workers who lack effective communication skills are more prone to misinterpreting instructions or failing to understand the broader goals of a task. This often results in errors, rework, and wasted resources—issues that can cascade across production lines and affect deadlines.
Mitigation: Upskilling initiatives focusing on clear communication can drastically reduce these errors. Training that emphasizes active listening, asking the right questions, and confirming understanding will enable workers to align their actions with operational objectives, thereby improving efficiency and accuracy.
3Lower Resilience to Unexpected Crises on the Shop Floor:
In fast-paced manufacturing environments, crises are inevitable. Workers lacking emotional resilience and adaptability—two critical non-technical skills—tend to buckle under pressure, exacerbating the impact of unexpected breakdowns or delays. This can paralyze production, as these employees cannot think on their feet or handle stress effectively.
Mitigation: To counter this, companies should prioritize training to build emotional resilience. Simulation exercises that replicate high-pressure situations can help workers develop the mental toughness needed to stay calm and problem-solve under duress, ensuring continuity in the face of adversity.
4Inability to Delegate Tasks Effectively, Straining Leadership Roles:
Poor delegation is common among employees who haven’t been trained in leadership skills. Managers and team leaders often find themselves overburdened because they don’t trust their team members to take on complex tasks. This inability to delegate effectively strains leadership, leading to burnout and slower decision-making processes on the shop floor.
Mitigation: Providing leadership training that includes task delegation and trust-building coaching can help alleviate this issue. Equipping managers with the skills to assess team capabilities and assign strengths-based tasks will lead to more efficient workflows and reduced leadership strain.
5Inability to Handle Feedback Constructively, Reducing Overall Growth:
A workforce that struggles with receiving feedback constructively will find it difficult to improve over time. Employees who take feedback personally rather than as an opportunity to grow tend to stagnate in their roles. This negatively affects productivity, as ongoing errors or inefficiencies remain unaddressed due to a lack of openness to learning.
Mitigation: Organizations can foster a culture of constructive feedback by providing effective training on giving and receiving feedback. Role-playing exercises where employees practice providing and receiving feedback in a supportive environment can build confidence and foster a growth-oriented mindset across the shop floor.
6Unclear Roles and Responsibilities Leading to Task Duplication:
When workers are unclear about their roles and responsibilities, tasks are often duplicated, and essential steps are missed. This inefficiency directly results from poorly defined boundaries and inadequate non-technical skills like organization and communication, which are crucial for clearly delineating roles on the shop floor.
Mitigation: Managers should implement clear job descriptions and set expectations through structured onboarding programs to address this. Team meetings that clarify roles and responsibilities also help ensure everyone understands their position within the larger operation, reducing task duplication and streamlining workflows.
7Reduced Collaboration Across Departments, Leading to Silos:
A lack of collaboration between departments is a common symptom of underdeveloped interpersonal skills. Employees who lack the ability or inclination to communicate across silos tend to focus on their tasks, missing the bigger picture of the company’s goals. This can lead to inefficient operations and the development of bottlenecks when cross-functional input is required.
Mitigation: Encouraging cross-functional teamwork through training programs and team-building exercises can help break down silos. These initiatives can teach employees the importance of collaborating and sharing information, leading to a more cohesive and productive shop floor environment.
8Lack of Adaptability in Response to Changing Production Demands:
Manufacturing environments are subject to frequent changes in production schedules, customer demands, or technology upgrades. Workers who lack adaptability find it difficult to cope with these changes, leading to delays and resistance to new processes. This rigidity often results in production inefficiencies and missed opportunities.
Mitigation: By incorporating adaptability into upskilling initiatives, organizations can quickly equip employees with the skills to adjust to new situations. Training that includes change management principles and scenario-based learning will enable workers to embrace shifts in the production landscape, keeping operations smooth and productive.
9Difficulty in Training Junior Staff in Collaborative Techniques:
Seasoned employees who lack strong mentorship and collaborative skills often struggle to train junior staff effectively. This can result in gaps in knowledge transfer, as new hires may miss out on the nuanced, hands-on learning needed to integrate smoothly into the team. Over time, this knowledge gap hampers productivity, as junior employees take longer to reach proficiency.
Mitigation: Organizations should provide mentorship training focusing on collaboration and knowledge sharing to remedy this. Creating structured mentorship programs can also facilitate more effective training, helping junior staff learn the soft skills they need to contribute fully to the team.
10Difficulty Implementing Cross-Functional Initiatives:
Cross-functional initiatives are critical for innovation and overall productivity, but employees without strong collaboration and leadership skills often struggle to implement these programs. The inability to manage interdepartmental relationships and communicate effectively across functions can lead to the failure of otherwise promising initiatives.
Mitigation: Investment in leadership and collaboration training is essential to successfully implementing cross-functional projects. Workshops focusing on cross-departmental communication, project management, and leadership can help bridge the skills gap and drive successful initiatives that boost productivity.
Conclusions for Operations Leaders
As we have explored, neglecting investment in upskilling creates secondary symptoms that directly affect productivity, from slower problem-solving and miscommunication to difficulty implementing cross-functional initiatives. Addressing these challenges requires a targeted approach beyond technical training and focuses on developing the soft skills necessary to improve collaboration, adaptability, and leadership on the shop floor.
POWERS can help your organization tackle these complex challenges. Our hands-on approach is designed to identify the specific areas where upskilling is needed and create tailored solutions that drive measurable improvements in productivity.
With POWERS, your organization can expect:
- Enhanced communication across teams and departments, reducing errors and misinterpretation of instructions.
- Improved problem-solving and decision-making capabilities, allowing for faster responses to operational challenges.
- Stronger leadership skills promote better delegation and clearer role definitions.
- A collaborative work environment that breaks down silos and supports cross-functional initiatives.
- Greater adaptability to changing production demands, ensuring efficiency in fast-paced environments.
Our proven methods help organizations unlock their full potential by ensuring their workforce has the non-technical skills needed to thrive in today’s manufacturing environment. Let us help you drive productivity improvements that make a lasting impact on your bottom line.
- Speak to an Expert: Call +1 678-971-4711 to discuss your specific challenges and goals.
- Email Us: Get tailored insights by emailing info@thepowerscompany.com
- Request an Assessment: Use our online contact form, and one of our expert manufacturing consultants will reach out to schedule an in-depth analysis of your operations.
Continue Reading from this Mastery Series
- Part 1 – Why Automation Alone Won’t Boost Productivity
- Part 2 – Why Non-Technical Skills Are Increasingly the Key to Increasing Productivity
- Part 3 – The Widening Digital Divide is Leaving Some Companies in the Dust
- Part 4 – Lack of Upskilling Sabotages Problem-Solving, Decision Making, and Innovation
- Part 5 – The Link Between Upskilling and Employee Well-being
- Part 6 – Neglecting Upskilling Leaves Your Operation Vulnerable to Safety Issues
- Part 7 – How Neglecting Upskilling Erodes Legacy Knowledge and Hurts Productivity
- Part 8 – Failing to Upskill Frontline Leaders Can Derail Operations
- Part 9 – Skimping on Skills Training Sabotages the Bottom Line
- Part 10 – An Underdeveloped Workforce Means an Unscalable Operation