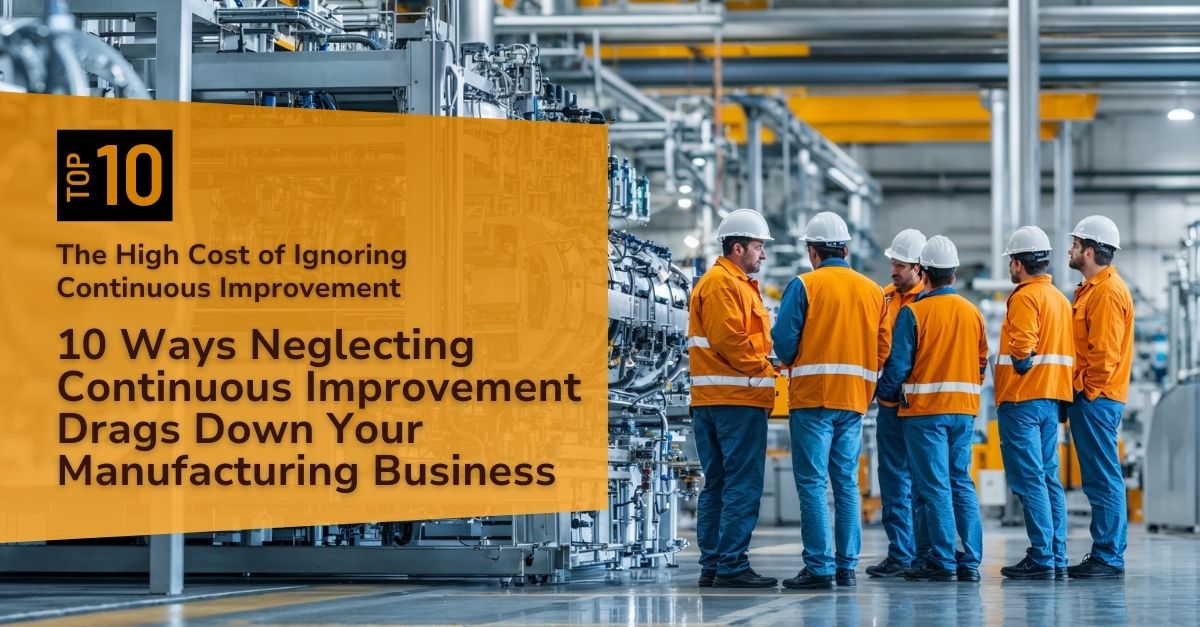
In manufacturing, progress isn’t just a luxury—it’s a necessity. A culture of continuous improvement isn’t about making small tweaks; it’s about fostering a mindset where every employee, from the shop floor to the C-suite, is constantly seeking ways to do things better, faster, and smarter.
Failing to cultivate this ethos isn’t simply a missed opportunity—it’s like dragging an unseen anchor that will inevitably slow you down and hinder your progress. The consequences of neglecting continuous improvement are severe and can lead to stagnation, increased costs, and loss of market share. But why do some manufacturing businesses struggle to prioritize continuous improvement? Several common culprits often stand in the way:
- Constant Firefighting: When urgent issues constantly demand attention, there's little time or energy left for proactive improvement initiatives.
- Poor Frontline Leadership Training and Development: Improvement efforts will flounder if supervisors and team leaders aren't equipped to identify and address inefficiencies.
- Lack of Top-Down Support: Without a visible commitment from leadership, continuous improvement can be seen as an optional extra rather than a core value. As a leader in your manufacturing business, your support and commitment to continuous improvement are crucial. Your actions and decisions set the tone for the entire organization, and by prioritizing continuous improvement, you can inspire your team to strive for excellence.
- Fear of Change: Employees may resist change if they feel threatened by new processes or technologies or if they lack the training to adapt.
- Short-Term Focus: Prioritizing immediate gains over long-term sustainability can lead to neglecting improvement efforts that may not yield immediate results.
The High Cost of Inaction: 10 Ways Neglecting Continuous Improvement Harms Your Business
Let’s explore the top 10 ways neglecting continuous improvement can inflict severe damage to your operation:
1Stagnant Productivity:
Without a commitment to constant refinement, processes become entrenched, inefficiencies linger, and productivity plateaus. Competitors who embrace improvement will surge ahead, leaving you in the dust.
2Swelling Costs:
Outdated equipment, inefficient workflows, and wasteful practices drain your bottom line. Every dollar squandered is a dollar your rivals can invest in innovation and growth.
3Quality Takes a Nosedive:
When improvement is an afterthought, quality suffers. Defects, rework, and customer dissatisfaction become commonplace, eroding your brand reputation and driving customers away.
4Employee Morale Plummets:
A stagnant environment breeds disengagement. Talented employees crave challenges and opportunities to grow. Without them, they’ll seek greener pastures, leaving you with a demoralized and underperforming workforce
5Innovation Grinds to a Halt:
A culture resistant to change stifles creativity and new ideas. You’ll miss out on groundbreaking technologies and process improvements that could revolutionize your operations.
6Customer Loyalty Evaporates:
In today’s competitive landscape, customers demand more than just a good product. They expect exceptional service, responsiveness, and continuous value. You’ll fail to meet their evolving needs without focusing on improvement.
7Market Share Dwindles:
Competitors who relentlessly pursue improvement will consistently deliver superior products and services at lower costs. Over time, they’ll capture your market share, leaving you struggling to stay afloat.
8Missed Growth Opportunities:
Without a culture of continuous improvement, you’ll be ill-equipped to capitalize on new market trends, emerging technologies, and expansion opportunities. However, by embracing continuous improvement, you can position your business to seize these opportunities and achieve sustainable growth.
9Safety Compromises:
Neglecting safety improvements puts your employees at risk and exposes your company to costly accidents, lawsuits, and regulatory penalties.
10Organizational Stagnation:
A lack of continuous improvement fosters a culture of complacency and resistance to change. This can permeate every level of your organization, hindering your ability to adapt and thrive in a dynamic business environment.
The Bottom Line for Operations Leaders:
Failing to build a culture of continuous improvement is a recipe for disaster in the manufacturing industry. It’s not a matter of if these negative consequences will manifest, but when.
At POWERS, we specialize in helping manufacturers embed continuous improvement into their DNA. Contact us today to learn how we can empower your team to embrace change, drive innovation, and achieve sustainable success in an ever-evolving marketplace.
Schedule a free consultation with a POWERS expert to assess your downtime risks and discover how our proven methodologies and cutting-edge technology can help minimize disruptions, optimize production, and achieve sustainable success.
Call +1 678-971-4711 to discuss your specific challenges and goals. Email us at info@thepowerscompany.com. Or, use our online contact form and one of our expert manufacturing consultants will contact you to schedule an in-depth analysis of your operations.
- Speak to an Expert: Call +1 678-971-4711 to discuss your specific challenges and goals.
- Email Us: Get tailored insights by emailing info@thepowerscompany.com
- Request an Assessment: Use our online contact form, and one of our expert manufacturing consultants will reach out to schedule an in-depth analysis of your operations.
Continue Reading from this Mastery Series
- Part 1 – When Progress Takes a Break, it Leaves Your Productivity Stalled
- Part 2 – Profit Erosion in the Production Line
- Part 3 – Quality Takes a Dive and Productivity Pays the Price
- Part 4 – When Morale Breaks Down So Does the Shop Floor
- Part 5 – When Innovation Pauses, Your Production Line Follows
- Part 6 – How Customer Loyalty Slips Through Your Fingers
- Part 7 – When Your Slice of the Market Becomes a Crumb
- Part 8 – When Opportunities Slip Through the Cracks
- Part 9 – Safety Shortsights and Their Costly Consequences
- Part 10 – Growth and Adaptation Slows to a Crawl