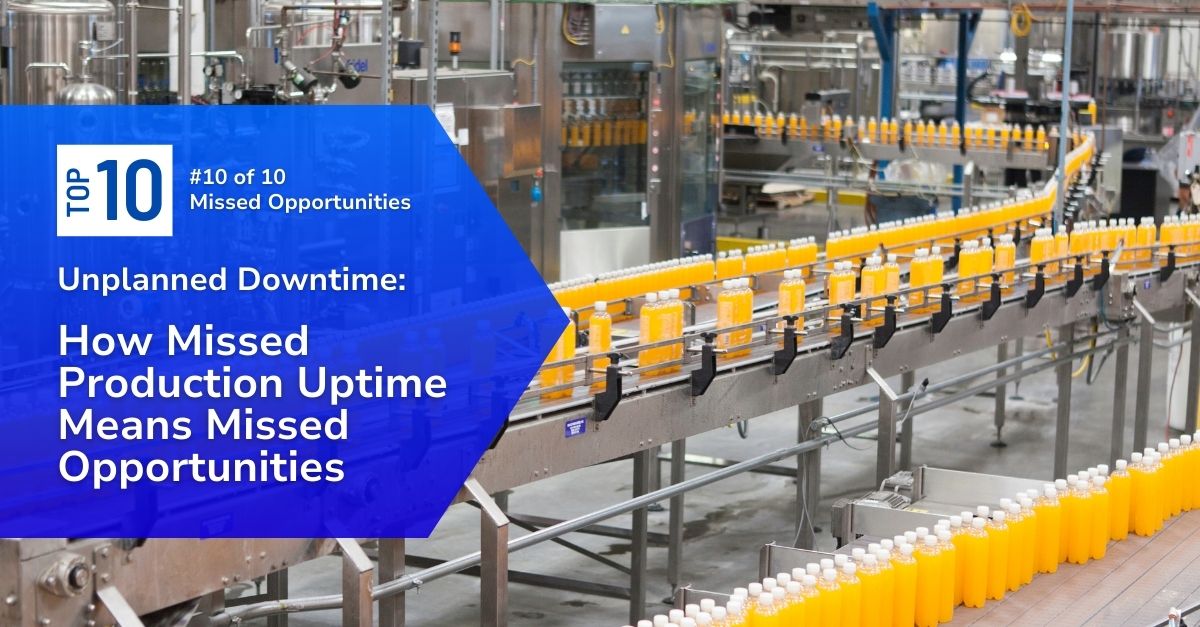
In the manufacturing industry, unplanned downtime represents a pervasive threat capable of derailing operations and causing significant missed opportunities.
These missed opportunities are not just abstract losses; they manifest in tangible, measurable setbacks that impede a company’s growth and competitive edge. When equipment fails unexpectedly or production lines halt, the immediate focus shifts to crisis management.
Consider the example of a manufacturer who misses out on a lucrative government contract due to unplanned downtime. Government contracts often come with strict deadlines and compliance requirements. When unplanned downtime strikes, production delays can result in the inability to meet contract terms, leading to lost revenue and damaged reputations. This example highlights how missed opportunities due to downtime can have far-reaching consequences beyond the immediate financial impact.
In this final part of our Unplanned Downtime Mastery Series, we will explore the top 10 ways that unplanned downtime results in missed opportunities, focusing on the secondary symptoms that real-world managers face on the shop floor. From delayed product launches to postponed talent acquisition, each point will be examined in detail, along with practical strategies to mitigate these challenges and improve productivity.
1Delayed Product Launches:
Unplanned downtime can severely disrupt the product development timeline, leading to delayed product launches. When production lines are halted unexpectedly, it causes a ripple effect that delays every subsequent product development phase. This delay can be critical, especially in competitive markets where being the first to market is a significant advantage.
Mitigation: To mitigate this issue, implement a robust predictive maintenance system. Predictive maintenance uses data analytics to predict equipment failures before they occur, allowing for planned maintenance activities that minimize disruption. Additionally, streamline your product development process with agile methodologies to ensure that even when delays occur, the team can quickly adapt and re-prioritize tasks to stay on track.
2Postponed Facility Upgrades:
Facility upgrades are often postponed due to unplanned downtime. When unexpected breakdowns occur, allocated resources for planned upgrades are diverted to address immediate repairs and maintenance. This delays the upgrade and prolongs the inefficiencies of older equipment.
Mitigation: Adopt a proactive maintenance strategy that includes regular audits and assessments of your facility’s infrastructure. Allocate a separate budget for emergency repairs to ensure that funds for planned upgrades remain unaffected. Moreover, consider phased upgrades that allow for incremental improvements without significant downtime.
3Reduced R&D Funding:
Unplanned downtime can drain financial resources, leading to reduced funding for research and development (R&D). When a significant portion of the budget is redirected to address emergency repairs, less capital is available for innovation and the development of new products.
Mitigation: Implement a cost-benefit analysis to prioritize maintenance activities and ensure efficient resource allocation. Additionally, explore alternative funding options for R&D, such as grants and partnerships, to ensure that innovation efforts continue despite financial constraints caused by downtime.
4Deferred Capital Investments:
Capital investments in new equipment, technology, or facilities are often deferred due to the immediate financial impact of unplanned downtime. This deferral can stall growth and expansion plans, keeping the company from seizing market opportunities.
Mitigation: Develop a comprehensive risk management plan that includes financial contingencies for unplanned downtime. Diversify your investment portfolio to ensure funds are not solely dependent on operational performance. Regularly review and update your capital investment strategy to align with market opportunities and internal capabilities.
5Missed Patent Filing Deadlines:
Unplanned downtime can disrupt the workflow of innovation projects, leading to missed patent filing deadlines. This can result in losing the intellectual property advantage and allowing competitors to capitalize on similar ideas.
Mitigation: Implement a project management system that tracks critical milestones and deadlines, including patent filings. Ensure that a dedicated team is responsible for overseeing patent processes, even during periods of downtime. Additionally, establish contingency plans to maintain progress on innovation projects despite operational disruptions.
6Stalled Innovation Projects:
Innovation projects often stall when unplanned downtime diverts resources and attention from long-term goals to immediate operational issues. This can hinder the development of new products and processes essential for staying competitive.
Mitigation: Encourage a culture of continuous improvement and innovation resilient to disruptions. Allocate dedicated resources and cross-functional teams to innovation projects to ensure they continue progressing even during operational challenges. Utilize flexible project management tools that allow for adaptive planning and resource reallocation.
7Abandoned New Technology Integration:
Integrating new technologies can be abandoned when unplanned downtime forces the reallocation of resources. This can prevent the company from modernizing its operations and benefiting from new technologies’ efficiencies and capabilities.
Mitigation: Create a detailed integration plan that includes risk assessments and mitigation strategies for potential downtime. Partner with technology vendors who offer comprehensive support and training to ensure a smooth transition. Additionally, pilot new technologies in small-scale implementations before full-scale deployment to minimize disruption.
8Loss of Early Mover Advantage:
Being an early mover in the market provides a competitive edge, but unplanned downtime can cause delays, resulting in lost opportunities to capitalize on being the first. This can allow competitors to catch up or even surpass your market position.
Mitigation: Enhance your market intelligence capabilities to promptly identify early mover opportunities. Establish a rapid response team to address downtime issues swiftly and minimize their impact on market positioning. Leverage strategic partnerships to share risks and resources, enabling quicker recovery and continued innovation.
9Interrupted Strategic Partnerships:
Unplanned downtime can interrupt strategic partnerships, strain relationships, and hinder collaborative projects. This can result in lost synergies and opportunities for mutual growth and innovation.
Mitigation: Maintain transparent communication with partners about your operational capabilities and challenges. Develop joint contingency plans that address potential downtime scenarios. Strengthen relationships through regular collaboration and shared goals to ensure resilience in the face of disruptions.
10Postponed Talent Acquisition:
Unplanned downtime often leads to postponed talent acquisition, as resources are diverted to address immediate operational needs. This can result in missed opportunities to recruit new skills and perspectives crucial for growth and innovation.
Mitigation: Incorporate workforce planning into your risk management strategy to ensure talent acquisition continues despite operational disruptions. Establish a talent pipeline through ongoing recruitment efforts and partnerships with educational institutions. Utilize temporary staffing solutions to fill immediate gaps while maintaining progress on long-term hiring goals.
Conclusion for Manufacturing Leadership
Unplanned downtime poses a significant threat to manufacturing operations, leading to missed opportunities that can severely impact a company’s growth, innovation, and competitive advantage.
At POWERS, we specialize in helping manufacturing companies navigate the complexities of operational disruptions and turn challenges into opportunities for improvement. Our comprehensive approach ensures that your organization is equipped with the strategies and tools needed to minimize unplanned downtime and capitalize on every opportunity for growth and innovation.
How POWERS Can Help
Our expert consultants work closely with your team to identify the root causes of unplanned downtime and implement effective solutions. Here’s how we can help:
- Predictive and Proactive Maintenance: Involves Using data analytics to predict equipment failures and conducting regular audits to ensure facility upgrades and maintenance activities are efficiently planned and executed.
- Comprehensive Risk Management: Developing financial contingencies and risk management plans to safeguard capital investments and strategic initiatives, ensuring continued funding for R&D and innovation projects.
- Flexible Project Management: Implement robust systems to track critical milestones and deadlines, encourage adaptive planning, and reallocate resources to maintain progress on innovation projects despite operational challenges.
- Strategic Partnerships and Workforce Planning: Enhancing market intelligence to identify early mover opportunities, developing joint contingency plans with partners, and integrating workforce planning into risk management to ensure continuous talent acquisition and development.
By partnering with POWERS, your manufacturing operation can achieve higher productivity and efficiency, transforming unplanned downtime from a barrier to an opportunity for growth. Contact us today to learn more about how we can help you operationalize your culture and drive sustainable organizational improvements.
- Speak to an Expert: Call +1 678-971-4711 to discuss your specific challenges and goals.
- Email Us: Get tailored insights by emailing info@thepowerscompany.com
- Request an Assessment: Use our online contact form, and one of our expert manufacturing consultants will reach out to schedule an in-depth analysis of your operations.
Continue Reading from this Mastery Series
- Part 1 – The Financial Burden of Breaking Down
- Part 2 – Eroding Maintenence Leading to Eroding Margins
- Part 3 – How Disrupted Production Leads to Unhappy Customers
- Part 4 –How Production Stoppages Can Break Your Supply Chain
- Part 5 – How Breakdowns Can Lead to Safety Shortcomings
- Part 6 – How Equipment Failures Drain Employee Drive
- Part 7 – How Constant Breakdowns Lead to Spiraling Maintenance Costs
- Part 8 – How Lost Production Time Leads to Lower Competitive Edge
- Part 9 – How Shop Floor Stoppages Lead to Regulatory Pitfalls
- Part 10 – How Missed Production Uptime Means Missed Opportunities