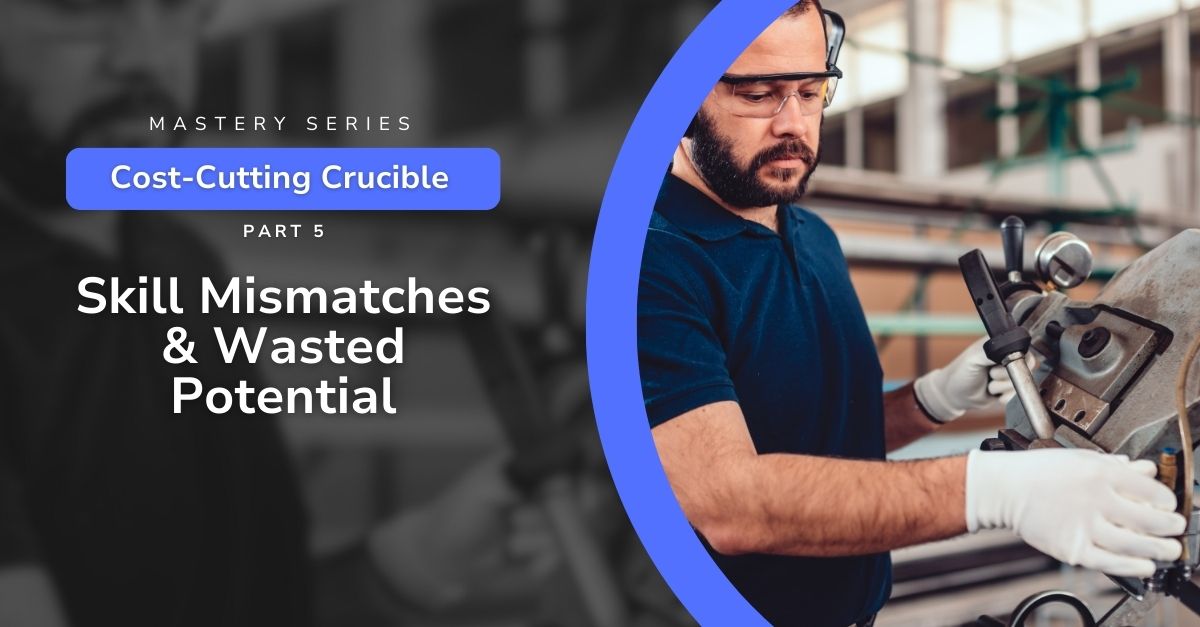
Hidden labor costs are some of the most elusive drains on profitability in manufacturing.
When workers are underutilized due to skill mismatches or ineffective task allocation, the organization absorbs unseen expenses that can significantly impact financial performance.
In many cases, these issues go unnoticed until they build up to a point where they directly affect operational output, limiting growth potential and costing the company far more than anticipated.
Consider a less common yet highly impactful example: a manufacturing facility dealing with inefficient troubleshooting. When an operator who lacks technical expertise is placed in a role requiring diagnostic skills, they may struggle to identify or fix minor equipment issues, leading to repeated breakdowns and delays. While this may appear to be a machine maintenance issue at first glance, the root cause is a mismatch between the operator’s skill set and the role’s demands. Every time the equipment fails, other employees are diverted from their tasks to assist, generating delays across multiple production lines. Over time, the plant’s operational costs increase, productivity suffers, and managers are forced to reconsider staffing and scheduling to regain control.
Such issues are classic examples of secondary symptoms resulting from hidden drains on profit. Poorly matched skills don’t just affect individual employees; they hinder workflow efficiency, reduce equipment uptime, and diminish capacity to meet production targets. Every misallocated task represents a missed opportunity to fully leverage the workforce, with cascading impacts on profitability.
Addressing these inefficiencies requires intentional task allocation and skill assessments, ensuring that every role aligns with employees’ strengths and that the organization’s full talent potential is utilized.
1Increased Rework Costs from Improperly Executed Tasks:
When tasks are assigned to employees without the requisite skills, errors become almost inevitable. This leads to rework, which slows down production and increases material waste, repair costs, and even the risk of delivering substandard products. In an environment where margins are tight, the cumulative effect of rework costs due to skill misalignment can be substantial, impacting profitability and eroding customer trust.
Mitigation Strategy: Conduct regular skills assessments to better understand each employee’s strengths and align them with tasks that suit their expertise. Use skill matrix mapping to help team leaders quickly see who is best suited for particular tasks, reducing errors and rework.
2Task Fatigue from Non-Skill-Aligned Duties:
Task fatigue quickly sets in when skilled workers are relegated to repetitive, non-challenging tasks. This results in decreased engagement, slower work speeds, and a greater likelihood of errors. Employees often lose motivation when they don’t feel their skills are being fully utilized, leading to lower-quality output and a gradual decline in productivity across the floor.
Mitigation Strategy: Rotate tasks among employees based on skill level and allow for skill-aligned duties that challenge more experienced workers. Consider using automation or less-skilled employees for lower-value tasks, allowing skilled workers to focus on complex, value-adding activities that maintain engagement and reduce fatigue.
3Reduced Capacity for Handling Peak Demands:
Underutilized labor can hinder the ability to meet demand during peak production periods. When employees are assigned tasks that don’t match their skill levels, the team’s ability to flex up for sudden demand spikes is limited, leading to overtime costs, delayed deliveries, and the potential for unfulfilled orders. Over time, this can impact customer satisfaction and erode the company’s reputation.
Mitigation Strategy: Create a flexible labor pool by cross-training employees on critical tasks, allowing them to step in and cover roles as needed. Establish a system for identifying and training backup employees for high-demand roles so production remains agile and adaptable during peak periods.
4Poorly Timed Task Handoffs Between Shifts:
When there is a skill mismatch in task allocation, the effectiveness of task handoffs between shifts suffers. Teams might repeatedly correct work from previous shifts, slowing overall productivity and extending cycle times. Poor task handoffs due to skill gaps often lead to confusion, delays, and inconsistent quality, which is particularly detrimental in a continuous production environment.
Mitigation Strategy: Standardize task handoff protocols across shifts, with clear documentation and checklists to confirm task status and completion level before a shift ends. Additionally, promotes cross-shift communication through shared digital tools, ensuring all employees stay informed of ongoing tasks and can adjust as needed.
5Over-reliance on Informal On-the-Job Training:
Informal training might seem efficient, but it can lead to knowledge gaps, inconsistent task execution, and reduced productivity. When employees rely on informal, inconsistent training, they are more likely to perform tasks differently or incorrectly, compromising product quality and workflow continuity.
Mitigation Strategy: Develop a standardized training program with theoretical and practical components. Establish a mentorship program that pairs new hires with experienced employees who can provide structured guidance. Training should also incorporate refresher courses to ensure employees are updated with industry best practices.
6High Turnover Among Skilled Workers Seeking Better Alignment:
Skilled employees who feel underutilized or mismatched in their roles are likely to leave, seeking positions that better utilize their talents. High turnover not only increases recruitment and training costs but also disrupts workflow, as replacements take time to reach full productivity. Furthermore, losing skilled workers often means losing valuable institutional knowledge.
Mitigation Strategy: Regularly assess employees’ skills and interests and realign their roles accordingly. Develop career progression paths that offer skilled workers opportunities to grow and take on challenges, reducing turnover and fostering a more engaged workforce. Recognize and reward employees who apply their expertise to improve processes.
7Limited Problem-Solving Input from Underutilized Talent:
Underutilized employees are often less engaged in problem-solving activities, leading to missed opportunities for process improvement. When skilled employees aren’t tapped for their insights, the facility misses out on innovative solutions that could streamline operations and reduce costs. This reactive approach to problem-solving ultimately makes the production process less resilient.
Mitigation Strategy: Establish a continuous improvement program that encourages input from all employees, regardless of their roles. Recognize and reward contributions to process improvements, fostering a culture where employees feel properly equipped to bring solutions and ideas.
8Reduced Organizational Knowledge Retention Due to Skill Misallocation:
When skilled employees are placed in roles that don’t require expertise, they cannot deepen or share their knowledge effectively, leading to poor knowledge retention across the organization. This slows down onboarding for new hires and reduces the overall skill level of the workforce over time, creating dependency on a few key individuals.
Mitigation Strategy: Facilitate regular knowledge-sharing sessions and document critical processes to ensure that knowledge is retained and accessible to the entire team. Additionally, consider pairing new hires with experienced mentors who can help transfer knowledge and skills effectively.
9Inconsistent Task Completion Times Across Shifts:
Skill mismatches often lead to significant variations in task completion times across shifts. Employees who aren’t fully proficient in their assigned roles tend to work slower and with less confidence, resulting in inconsistent output rates. This disrupts production flow, complicates scheduling, and ultimately reduces throughput.
Mitigation Strategy: Establish benchmark times for key tasks and monitor employee adherence. Identify shifts or individuals that consistently fall behind and provide targeted training or role adjustments as needed. Having measurable standards ensures that managers can quickly identify and address performance gaps.
10Limited Capacity to Scale Production Quickly:
Ineffective task allocation and skill mismatches reduce the plant’s ability to scale production efficiently. When demand increases, a lack of task alignment and cross-functional skills makes it difficult to ramp up operations without significant strain on the workforce. This leads to bottlenecks, quality issues, and potential revenue losses as the plant struggles to meet demand.
Mitigation Strategy: Implement a scalable task allocation system that categorizes roles based on skill and readiness. Prepare contingency plans that enable high-performing employees to lead task shifts when scaling up, ensuring that production can be adjusted smoothly and quickly in response to market demands.
Conclusions for Operations Leaders
Underutilized labor due to skill mismatches and ineffective task allocation are hidden profit leaks that gradually erode productivity and increase operational costs. Addressing these issues isn’t just about repositioning employees; it’s about creating a culture and system where each worker’s strengths are fully utilized, resources are allocated efficiently, and production is optimized to meet demand seamlessly. Recognizing and addressing these unseen costs can transform how manufacturing teams operate, helping to prevent profit loss and support long-term growth.
Our approach is comprehensive and data-driven, ensuring your operation is equipped to manage and thrive in an evolving industry. With the Digital Production System (DPS), we offer tools that combine decades of industry experience with advanced AI and real-time insights designed to elevate your operations.
Here’s how POWERS and DPS can transform your productivity:
- Complete Operational Visibility: Gain real-time insights into production, identify bottlenecks, and streamline workflows with comprehensive dashboards and analytics.
- Seamless Team Collaboration: Enhance cross-functional communication with instant data sharing and collaborative tools that drive continuous improvement.
- Proactive, Data-Driven Decisions: Leverage AI to anticipate challenges, optimize task allocation, and support smarter, faster decision-making across all production stages.
- Maximized Resource Efficiency: Minimize downtime and maximize resource utilization, ensuring your workforce is positioned to meet production demands and boost overall output.
Ready to unlock your operations’ full potential? POWERS is here to guide you, offering consulting and a pathway to sustainable productivity and profitability in the digital era.
- Speak to an Expert: Call +1 678-971-4711 to discuss your specific challenges and goals.
- Email Us: Get tailored insights by emailing info@thepowerscompany.com
- Request an Assessment: Use our online contact form, and one of our expert manufacturing consultants will reach out to schedule an in-depth analysis of your operations.
Continue Reading from this Mastery Series
- Part 1 – How Poor Scheduling Burns Through Your Profit Margins
- Part 2 – How Hidden Energy Wastes Burn Through Your Bottom Line
- Part 3 – How Dead Weight in Your Safety Stock Undermines Your Bottom Line
- Part 4 – The Hidden Costs of Ignoring Preventive Maintenance Programs
- Part 5 – Mismatched Skills and Wasted Workforce Potential
- Part 6 – Poor Quality Control is Dragging Down Your Productivity and Profits
- Part 7 – Being Slow to Market Undermines Your Bottom Line
- Part 8 – Supplier Missteps That Drain Profitability
- Part 9 – The Cost of Continuing to Use Manual Processes
- Part 10 – The Financial Fallout of Fragmented Compliance