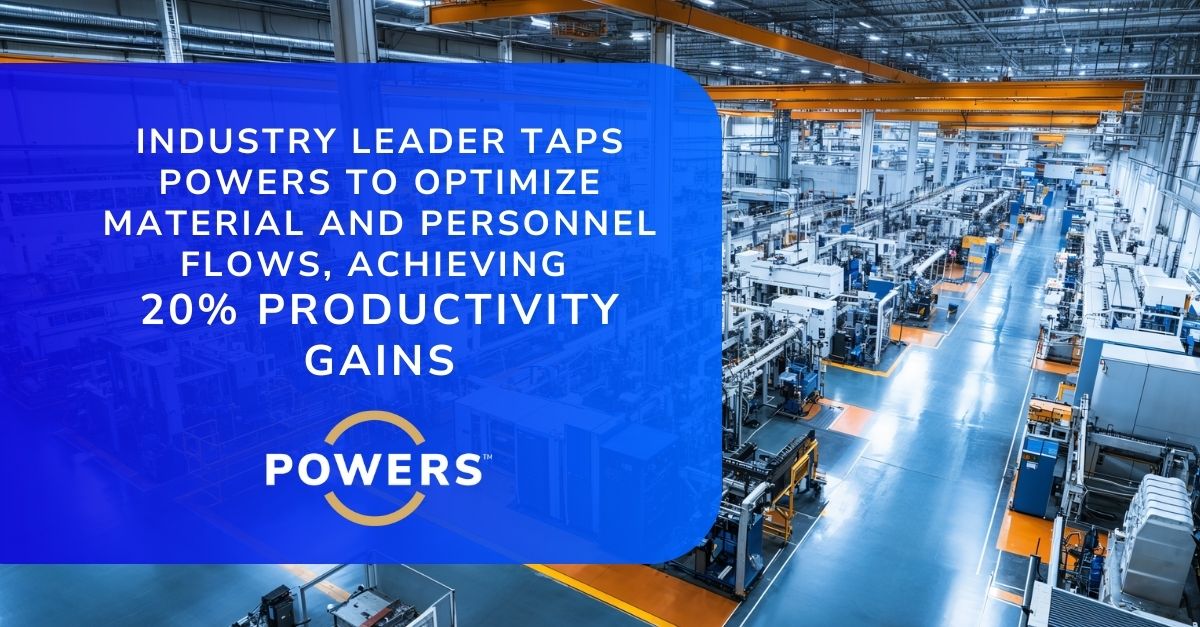
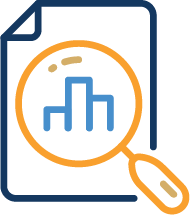
Project Overview
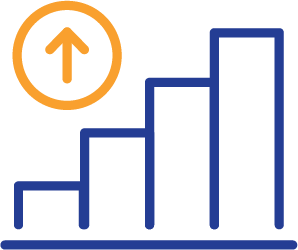
Performance Results
Executive Summary
A prominent manufacturer in the highly competitive automotive aftermarket parts and accessories sector, recognized the need to enhance its material and personnel flow within its production facilities to maintain operational efficiency and support future growth. The company enlisted the expertise of POWERS, an operations consulting firm specializing in manufacturing productivity. POWERS identified key inefficiencies in the facility layout and personnel movement through a comprehensive assessment. Their strategic recommendations, including adopting an optimized layout and improved safety measures, resulted in substantial improvements in the company’s operational efficiency, safety protocols, scalability for future expansion, and a remarkable 20% increase in productivity!
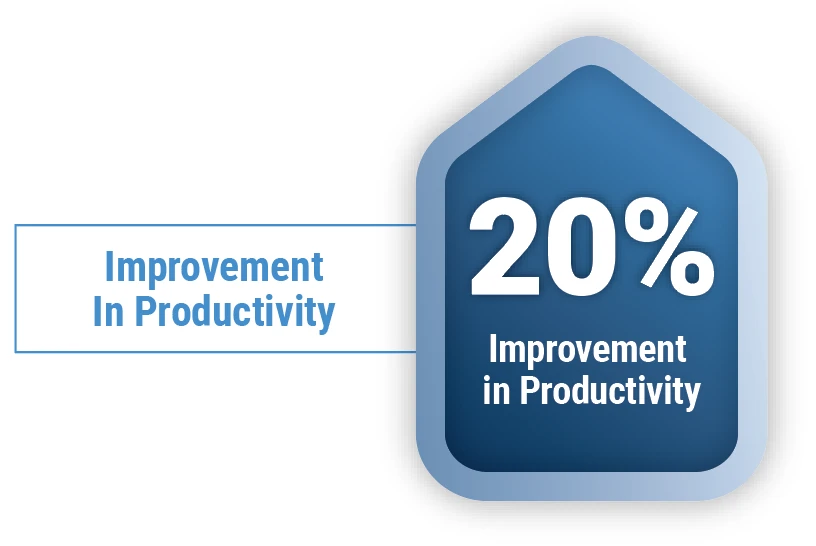
Read the Full Case Study Here
Introduction
The manufacturing industry demands continuous improvement and optimization of processes to remain competitive. For this leading manufacturer, known for its commitment to quality and innovation, the efficient flow of materials and personnel within its production facilities had become a critical area of focus. The company’s existing production layout was increasingly seen as a bottleneck that hindered productivity and posed safety risks. To address these challenges, the company sought the assistance of POWERS, a consulting firm renowned for its expertise in optimizing manufacturing operations to maximize productivity.
POWERS was brought in to conduct an in-depth assessment of the material and personnel flow within the company’s production facilities. The primary goal was to identify inefficiencies and recommend actionable improvements to enhance current operations and provide flexibility for future growth. The firm’s extensive experience in manufacturing productivity made it an ideal partner for this critical project.
Objective and Scope
The objective of the Material and Personnel Flow Study was to thoroughly assess the current manufacturing layout and processes at the company’s production facilities, which were located in two key sites. The POWERS team aimed to identify opportunities to streamline material flow, reduce inefficiencies in personnel movement, and improve overall operational effectiveness. This comprehensive study addressed immediate operational challenges and longer-term strategic goals, ensuring the company could thrive in a competitive marketplace.
The scope of the study included detailed site assessments at the company’s facilities in two locations. These assessments focused on understanding the existing processes, gathering quantitative and qualitative data, and mapping out the current material and personnel flow state. Our team worked closely with the company’s internal team to ensure that the recommendations would be practical, actionable, and aligned with the company’s overall business objectives.
Methodology
Our on-site team employed a systematic and data-driven approach to assessing the material and personnel flow within the company’s production facilities. The assessment was conducted in two phases: site assessments and data analysis with layout review.
Site Assessments:
The POWERS team conducted on-site evaluations at the company’s production facilities. These visits occurred over several days at each location, during which the consulting team collaborated closely with the company’s personnel. The goal was to understand the existing workflows deeply, observe daily operations, and identify any immediate inefficiencies. The team gathered detailed data on material movement from receiving to production and shipping and the flow of personnel within the facility. Special attention was paid to areas where material handling and personnel movement intersected, as these were potential points of congestion and safety hazards.
Data Analysis and Layout Review:
Following the site assessments, our team thoroughly analyzed the data collected. A grid system was established to facilitate a systematic review of the facility layout. This grid allowed for precise measurements and calculations of material and personnel flow, enabling the consulting team to accurately map out the current state. Material flow was analyzed from receiving raw materials, through production processes, and ultimately to shipping finished goods. Personnel flow was evaluated to identify unnecessary movement, potential safety risks, and areas where workflow could be streamlined.
Two layout options, Option 1 and Option 2, were developed based on the analysis. These options addressed the identified inefficiencies and improved the facilities’ overall operational flow. Each option was rigorously compared in terms of its effectiveness, potential impact on productivity, and ability to support future growth.
Findings
The assessment conducted by POWERS revealed several critical inefficiencies within the current production layout and personnel flow. The analysis identified areas where improvements were necessary to enhance operational efficiency and safety.
Material Flow Inefficiencies:
One of the key findings was the presence of significant inefficiencies in the movement of materials, particularly near the shipping and receiving areas. The existing layout resulted in congestion points that could slow down operations and increase the risk of delays in material handling. The analysis showed that the current pathways for material movement were not optimized, leading to unnecessary detours and excessive handling of materials. This inefficiency affected productivity and increased the likelihood of material damage and inventory inaccuracies.
Personnel Flow Challenges:
The study also highlighted challenges in the movement of personnel within the facility. Excessive movement was observed in areas where personnel had to navigate around material handling equipment, particularly forklifts. This not only slowed down operations but also raised serious safety concerns. The high level of interaction between personnel and forklifts in congested areas increases the risk of accidents, which could lead to injuries and operational disruptions. The POWERS team identified these high-risk zones and emphasized the need for a safer, more structured flow of personnel to minimize unnecessary movement and reduce the risk of accidents.
Evaluation of Layout Options:
We developed and evaluated two potential layout options—Option 1 and Option 2—to address the identified inefficiencies. Option 1 proposed realigning the production flow with the material warehouse in a different facility section. While this option provided some improvements, it also introduced new challenges, particularly regarding material flow distances and the complexity of personnel movement.
Option 2, on the other hand, emerged as the more favorable solution. This layout offered greater flexibility for future expansion and incorporated improved safety measures. The design of Option 2 strategically positioned production lines closer to the shipping areas, reducing material travel distances and minimizing the risk of congestion. Additionally, this layout allowed for the perpendicular installation of certain production lines, enabling the company to expand its operations more easily.
Recommendations
Based on the findings, POWERS made several strategic recommendations to optimize the company’s production facility layout and enhance material and personnel flow.
Adoption of Layout Option 2:
We strongly recommend the adoption of Layout Option 2. This layout was designed to provide enhanced flexibility and safety while addressing the inefficiencies identified in the current setup. One of the key recommendations was to install specific production lines perpendicularly between designated sections of the facility. This configuration would improve the current flow and create additional space for future expansion, ensuring the company could scale its operations without significant disruptions.
Material Handling Improvements:
To further enhance material flow, Our team also proposed a new method for loading materials onto carousels. This method was designed to reduce the reliance on forklifts in high-traffic areas, improving safety and reducing the risk of accidents. The company could achieve a smoother and more efficient flow of materials throughout the facility by streamlining the material loading process and minimizing the need for forklifts.
Personnel Flow Enhancements:
The team also recommended implementing structured pathways for personnel. These pathways would be clearly defined to minimize unnecessary movement and reduce the risk of accidents, particularly in areas where personnel and forklifts intersect. By creating dedicated paths for personnel, the company could enhance safety and improve the overall efficiency of operations.
Material Flow Adjustments:
To alleviate congestion near critical areas such as shipping and receiving, we suggested developing alternative pathways for material movement. These pathways would be designed to reroute materials from high-traffic zones, ensuring a smoother and more efficient flow. This adjustment would help reduce bottlenecks and improve the overall speed and accuracy of material handling.
Implementation Strategy
The POWERS team provided a comprehensive implementation strategy to guide the company through adopting the recommended layout and operational improvements. This strategy included a detailed plan for modifying the facility layout, adjusting operational practices, and ensuring a smooth transition to the new setup.
The implementation plan outlined the steps required to reconfigure the production lines and install the new material handling systems. It also included a timeline with key milestones to track progress and ensure the project remained on schedule. We emphasized the importance of regular monitoring and evaluation to assess the effectiveness of the new layout and make adjustments as needed.
To support the successful implementation of the recommendations, our team worked closely with the company’s internal team to ensure all stakeholders were aligned and the necessary resources were in place. The consulting firm also provided training and support to help the company’s personnel adapt to the new processes and workflows.
Conclusion
The collaboration between the company and POWERS resulted in a thorough and effective assessment of the material and personnel flow within the production facilities. The strategic recommendations, particularly the adoption of Layout Option 2, led to a 20% increase in productivity, along with significant improvements in safety and capacity for future growth. These outcomes demonstrate the value of optimizing operational workflows and the impact of strategic consulting on long-term business success.
Lessons Learned
This case study underscores the critical role detailed assessments and strategic layout planning can play in optimizing manufacturing operations. The partnership with POWERS proved to be a key factor in identifying and addressing inefficiencies that had previously hindered productivity and posed safety risks. The resulting 20% increase in productivity underscores the effectiveness of these improvements and the importance of engaging specialized consulting firms to achieve substantial operational gains.