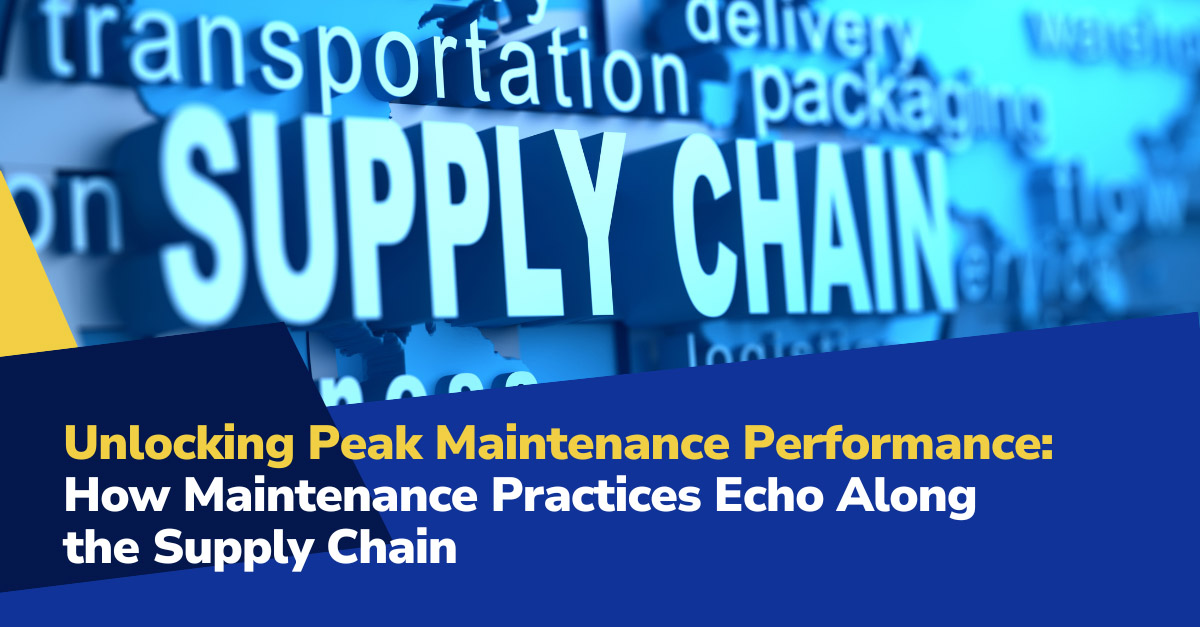
In manufacturing, a reliable production schedule is more than just a calendar; it’s the framework that keeps teams aligned, machines running, and orders shipping on time. But when maintenance is reactive, inconsistent, or under-resourced, even the most carefully built schedules can collapse fast.
Maintenance doesn’t just affect downtime; it alters labor needs, material flow, delivery windows, and even how leaders make day-to-day decisions. This post explores 10 specific ways weak maintenance practices disrupt production schedules and how a proactive approach can help you regain control.
How Poor Maintenance Practices Derail Your Production Schedule
1Escalated Downtime Costs:
When preventive maintenance is skipped or delayed, breakdowns become more frequent, and usually more severe. Unexpected equipment failures can rise 15–30%, instantly throwing off line sequencing, shift coverage, and delivery planning. Once the line stops, recovery time often ripples across multiple work centers, not just the affected one.
2Soaring Repair and Replacement Expenditures:
If technicians are working without clear documentation, don’t have access to spare parts, or are stretched too thin, repairs take longer than they should. In many plants, this can mean repair times doubling or tripling compared to standard expectations, causing schedule overruns that extend beyond a single shift and bleed into customer commitments.
3Diminished Equipment Efficiency:
Machines that are frequently offline for unplanned repairs or operating under derated conditions reduce line flexibility. Availability can drop by 10–20%, shrinking the daily output your facility can realistically hit. For teams trying to maximize OEE, this becomes a key roadblock to improving performance.
4Quality Control Compromises:
Maintenance failures can throw material flow off balance. Poorly timed breakdowns interrupt just-in-time systems and kanban loops, contributing to 5–10% drops in raw material or component availability. This often leads to costly workarounds, rushed orders, expedited shipping, or waiting on the dock for a pallet that should’ve been staged hours earlier.
5Safety-Related Financial Burdens:
As downtime, rescheduling, and throughput issues stack up, delivery timelines suffer. A 10–25% increase in missed ship dates isn’t uncommon when maintenance is unmanaged. That erosion of reliability damages long-term customer relationships and increases the odds of chargebacks, contract losses, or quality claims driven by rushed output.
6Elevated Energy Bills:
Machines running with overdue maintenance often lose performance, even if they don’t fail outright. Throughput can decline 10–20% as equipment slows down, experiences more jams, or requires more frequent resets. Operators lose rhythm, shifts fall behind, and batch timing gets thrown off. Every slowdown compounds across the schedule.
7Inventory Management Disruptions:
When machines go offline or don’t hit expected cycle times, production plans must be reworked on the fly. Line changes, overtime, and labor reassignments become daily headaches. This leads to a 5–15% increase in rescheduling effort, with planners spending more time fixing problems than optimizing performance.
8Labor Cost Inflation:
When lines fall behind, the most common response is labor overtime. Maintenance-driven disruptions often result in a 10–30% increase in overtime hours, either to make up lost time or to cover rework caused by rushed production. Over time, this adds pressure on already thin crews and contributes to burnout and turnover.
9Extended Production Cycle Times:
Without effective maintenance programs and tracking, forecasting becomes guesswork. Teams lose confidence in when machines will be available and how long repairs will take. Predictive accuracy can fall 20–30%, undermining decisions around staffing, material ordering, and capacity booking.
10Regulatory Compliance Expenditures:
If machine uptime is unreliable and performance fluctuates, capacity models quickly become disconnected from reality. Inaccurate assumptions about what your plant can produce lead to overpromising to sales and underdelivering to customers. Even a 15–25% drop in planning accuracy can trigger revenue losses and missed growth targets.
The POWERS Strategy:
Elevating ROA through Maintenance Excellence
At POWERS, we recognize that maintenance is not just about keeping equipment running; it’s about strategic asset optimization. Our Advanced Maintenance Performance (AMP) program is tailored to enhance your maintenance protocols, thereby improving ROA by ensuring that your assets are utilized efficiently and effectively.
Our comprehensive approach involves meticulously analyzing your current maintenance strategies and their impact on ROA.
We provide specialized training and strategic planning, focusing on enhancing your equipment’s efficiency, reliability, and lifespan. By optimizing these aspects, we aim to boost your net income and ROA, turning your maintenance operations into a key driver of financial success.
To discover how optimized maintenance can transform your company’s ROA, download our FREE Maintenance Assessment Guide. Embark on a journey towards maximizing asset value and bolstering your bottom line.
Contact the POWERS team at +1 678-971-4711 or email info@thepowerscompany.com for a comprehensive consultation to reshape how you view maintenance and asset management.
Continue Reading from this Mastery Series
- Part 1 - The Critical Link Between Maintenance and OEE
- Part 2 - How Maintenance Practices Shape Product Quality
- Part 3 - How Poor Maintenance Standards and Practices Impact Schedule Adherence
- Part 4 - How Maintenance Practices Echo Along the Supply Chain
- Part 5 - The Impact of Maintenance on Maximizing Return on Assets (ROA) in Manufacturing
- Part 6 - Poor Maintenance Practices Lead to Out-of-Control Operational Costs
- Part 7 - Navigating the Safety and Compliance Minefield in Manufacturing
- Part 8 - The High Cost of Overlooking Maintenance in Manufacturing Strategic Planning
- Part 9 - Poor Maintenance Practices Are a Hindrance to Technological Innovations
- Part 10 - Overcoming the ‘Reactive’ or ‘Run Till it Breaks’ Pitfall