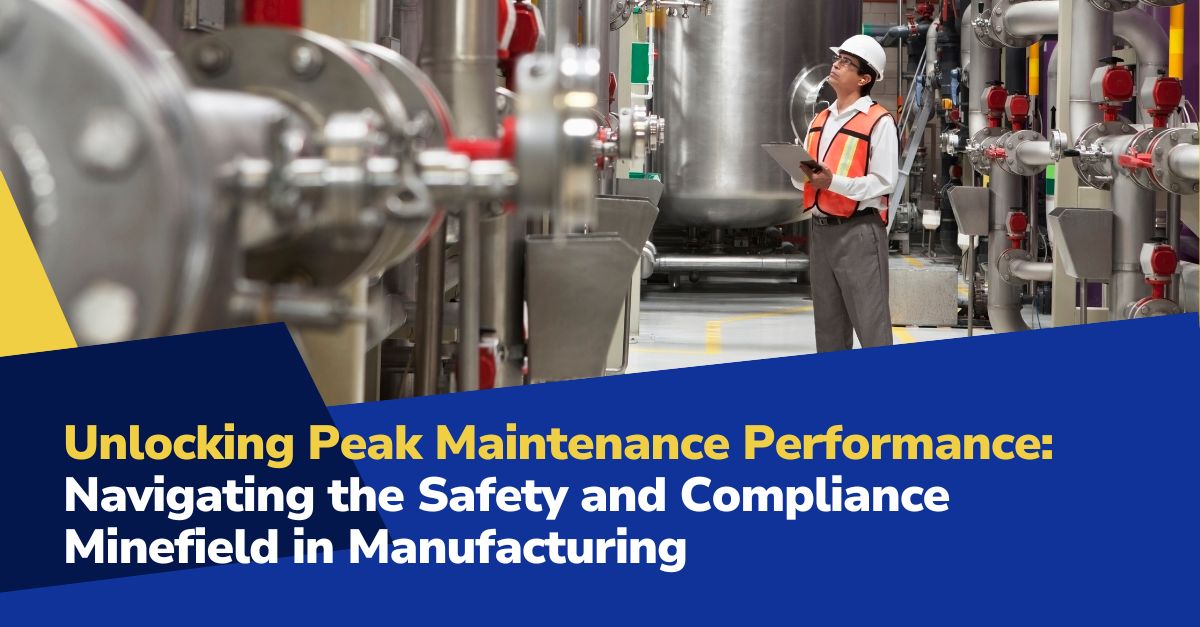
The critical role of maintenance in the manufacturing sector extends far beyond ensuring the smooth operation of machinery. It is fundamental to ensuring workforce safety and adhering to stringent regulatory standards.
This seventh installment of our series delves into the top 10 ways that subpar maintenance practices amplify safety and compliance risks, leading to escalated operational costs and potential legal repercussions.
1Elevated Accident Risks:
Poorly maintained equipment is a significant hazard, leading to workplace accidents. According to industry reports, equipment failure accounts for approximately 10% of workplace injuries in manufacturing settings.
These accidents incur costs beyond immediate medical expenses, affecting long-term disability claims and the loss of skilled labor. The indirect costs, such as the time lost in production and investigation, can be substantial.
2Regulatory Fines and Sanctions:
In the manufacturing industry, adherence to safety regulations, such as those set by OSHA, is mandatory. A lapse in maintenance can lead to violations of these standards, resulting in fines exceeding $100,000. These fines are financial penalties and serve as public records of safety negligence, impacting the company’s public image.
3Increased Insurance Premiums:
Insurance companies assess the risk profile of manufacturing entities with great detail. A history of poor maintenance leading to safety issues can significantly increase insurance premiums, reflecting the increased risk associated with insuring the operation. This rise in premiums can have a long-term financial impact on the company.
4Downtime Due to Safety Incidents:
Safety incidents can immediately halt production lines, leading to unplanned downtime. This disrupts the supply chain and results in costs related to idle labor and delayed order fulfillment. The cost of restarting production can also be significant, especially if specialized machinery recalibration is required.
5Legal Liabilities and Litigation Costs:
Manufacturers may face legal battles when accidents occur due to negligent maintenance. The costs associated with litigation, potential settlements, or judgments can be financially draining. Additionally, the reputational damage from public legal proceedings can have long-lasting effects on customer trust and business relationships.
6Compromised Worker Morale and Productivity:
The psychological impact of working with poorly maintained equipment on employees is profound. Workers who feel unsafe are less productive and more prone to errors, which can lead to further safety risks and reduced operational efficiency. The cost of low morale is evident in higher turnover rates and the need for additional recruitment and training.
7Loss of Reputation:
In the digital age, news of safety lapses spreads quickly and can significantly damage a brand’s reputation. Rebuilding consumer trust after a safety incident can take years and require substantial investment in public relations and customer engagement strategies.
8Training and Retraining Costs:
Inadequate maintenance often necessitates additional training and retraining of staff, particularly following safety incidents. This incurs direct costs and diverts resources from productive activities, impacting the operation’s overall efficiency.
9Environmental Hazards:
Poor maintenance can lead to environmental incidents, such as chemical spills, posing significant safety risks. These incidents can result in environmental compliance violations, cleanup costs, and potential legal action from environmental regulatory bodies.
10Resource Drain on Safety Monitoring and Compliance:
To mitigate risks, companies often need to allocate more resources to safety monitoring and compliance. This can divert funds from other critical operational areas, impacting the company’s overall financial health and efficiency.
The POWERS Difference:
Safeguarding Through Maintenance Excellence
At POWERS, we recognize that maintenance is a cornerstone of safety and compliance in manufacturing. Our Advanced Maintenance Performance (AMP) program is meticulously designed to address these challenges.
By implementing AMP, manufacturers can significantly reduce the risk of accidents, ensure compliance with safety regulations, and maintain a positive reputation in the industry.
Are you ready to transform your maintenance practices into a bulwark of safety and compliance? Contact our dedicated team at +1 678-971-4711 or info@thepowerscompany.com for a comprehensive assessment and tailored solutions.
Let’s build a safer, more compliant, cost-effective manufacturing environment.
Continue Reading from this Mastery Series
- Part 1 - The Critical Link Between Maintenance and OEE
- Part 2 - How Maintenance Practices Shape Product Quality
- Part 3 - How Poor Maintenance Standards and Practices Impact Schedule Adherence
- Part 4 - How Maintenance Practices Echo Along the Supply Chain
- Part 5 - The Impact of Maintenance on Maximizing Return on Assets (ROA) in Manufacturing
- Part 6 - Poor Maintenance Practices Lead to Out-of-Control Operational Costs
- Part 7 - Navigating the Safety and Compliance Minefield in Manufacturing
- Part 8 - The High Cost of Overlooking Maintenance in Manufacturing Strategic Planning
- Part 9 - Poor Maintenance Practices Are a Hindrance to Technological Innovations
- Part 10 - Overcoming the ‘Reactive’ or ‘Run Till it Breaks’ Pitfall