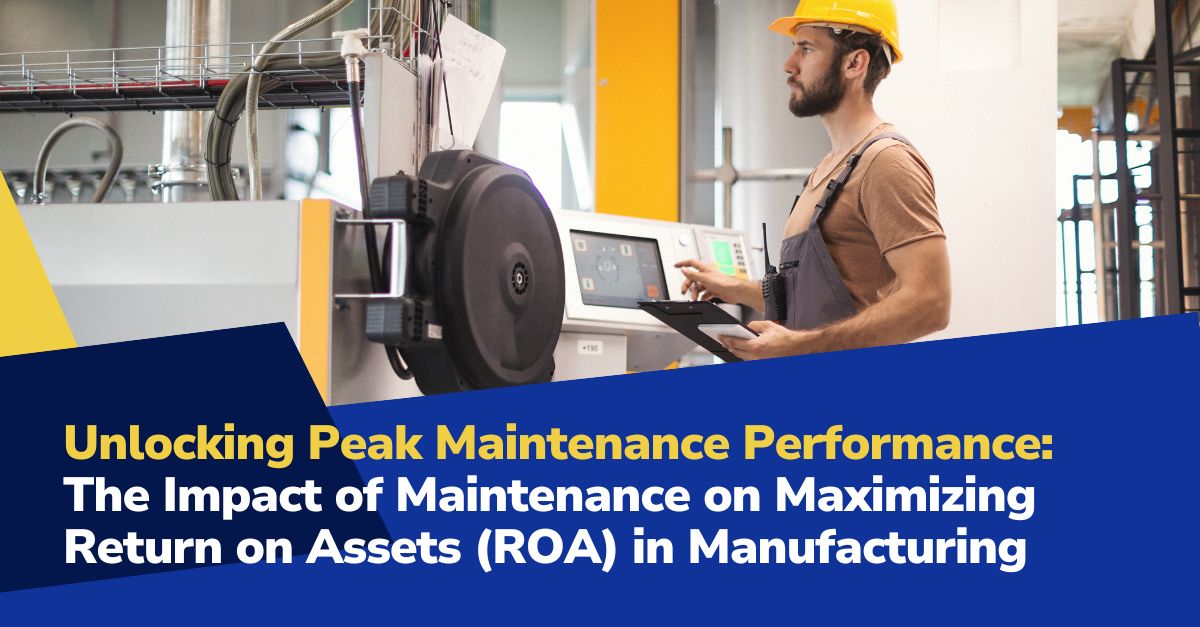
The precise choreography of maintenance in manufacturing doesn’t just ensure the smooth operation of machinery; it acts as a critical support for the sprawling web of the supply chain.
When maintenance disciplines start to crumble, the repercussions ripple through the network with surprising speed and reach, touching everything from the initial stages of procurement to the final phases of delivery.
In this insightful fourth installment of our series, we delve into the top 10 ways inadequate maintenance standards and practices unleash a series of shockwaves through a manufacturer’s supply chain.
We dissect the complex and often subtle ways that maintenance tasks are interconnected with the pulse of the supply chain, reinforcing the vital connection between diligent manufacturing maintenance and the overall strength and efficiency of the supply network.
Disruptive Ripple
Effects: The Extensive Reach of Maintenance
The robustness of a supply chain is only as formidable as its most vulnerable juncture. Often operating in the shadows, the influence of maintenance in manufacturing stretches across the entire spectrum of the supply chain, with significant and far-reaching consequences:
1Supplier Downtime Contagion:
Lackluster maintenance can exacerbate supplier downtime by a staggering 20%, causing a chain reaction that impedes the steady flow of raw materials and components essential for continuous production.
2Increased Lead Times:
Neglected or improperly performed equipment maintenance can lead to a dramatic increase in lead times—between 10-30%—placing severe pressure on the supply chain and magnifying the risk of running out of critical stock at the worst possible times.
3Transportation Tangles:
The delays stemming from maintenance issues can introduce a 5-15% increase in transportation complications, as altered product availability timelines disrupt the logistics and planning foundational to smooth supply chain operations.
4Quality Quarrels:
A direct consequence of inadequate maintenance is the 10-25% surge in quality control challenges encountered at the outset, which have a domino effect, causing disruptions that flow downstream and affect every subsequent phase.
5Forecasting Frustrations:
The lack of maintenance reliability can diminish the accuracy of supply chain forecasting by up to 20% due to the unpredictability of production outputs that result from these maintenance shortcomings.
6Inventory Inaccuracies:
A neglected maintenance regime can swell inventory mismatches by 5-10%, leading to overstocking or understocking dilemmas that complicate inventory management and order fulfillment processes.
7Customer Commitment Cracks:
When maintenance standards are deficient, the reliability of deliveries can plummet by 15-20%, which can quickly erode customer trust and undermine contractual commitments, with long-term repercussions for business relationships.
8Cost Climbs:
Unanticipated maintenance challenges can inflate the costs associated with the supply chain by 10-20%, eroding profitability through unforeseen rush orders and the need for expedited shipping to meet tight deadlines.
9Warranty Woes:
An increase of 5-15% in warranty claims and product returns can often be traced back to maintenance-related production flaws, which put additional strain on the supply chain and customer service resources.
10Compliance Complications:
The unpredictability introduced by maintenance issues can lead to a 20% higher risk of supply chain compliance breaches, which may result in substantial fines and even forced halts in production, causing significant disruption and potential loss of reputation.
The POWERS Influence:
Bolstering Supply Chain Resilience Through Maintenance
With a clear-eyed understanding of the profound effects of maintenance on the supply chain, POWERS Manufacturing Productivity Experts have meticulously developed the Advanced Maintenance Performance (AMP) program. This program is meticulously designed to strengthen each link in the supply chain with robust and proactive maintenance practices.
AMP is not just a vision; it is a practical, actionable framework that ensures each element in the supply chain is fortified against the unpredictability of maintenance mishaps.
Through AMP, we provide a detailed analysis identifying the critical intersections where maintenance and supply chain operations meet, offering specialized training to address these gaps and laying out a comprehensive strategic plan to ensure ongoing resilience and reliability.
It’s time to reinforce the backbone of your supply chain with proactive maintenance. With the POWERS difference, you gain a partner in analyzing the multifaceted ways maintenance shapes your supply network, ensuring each link is robust and reliable.
Are you ready to revitalize your supply chain and guard against the detriments of maintenance malpractice? OurFREE Maintenance Assessment Guide is the first step toward robust reinforcement. Contact our dedicated POWERS team at +1 678-971-4711 or info@thepowerscompany.com for a detailed consultation.
Together, we can synchronize your supply chain with peak maintenance performance, creating a symphony of efficiency and reliability that resonates through every facet of your operations.
Continue Reading from this Mastery Series
- Part 1 - The Critical Link Between Maintenance and OEE
- Part 2 - How Maintenance Practices Shape Product Quality
- Part 3 - How Poor Maintenance Standards and Practices Impact Schedule Adherence
- Part 4 - How Maintenance Practices Echo Along the Supply Chain
- Part 5 - The Impact of Maintenance on Maximizing Return on Assets (ROA) in Manufacturing
- Part 6 - Poor Maintenance Practices Lead to Out-of-Control Operational Costs
- Part 7 - Navigating the Safety and Compliance Minefield in Manufacturing
- Part 8 - The High Cost of Overlooking Maintenance in Manufacturing Strategic Planning
- Part 9 - Poor Maintenance Practices Are a Hindrance to Technological Innovations
- Part 10 - Overcoming the ‘Reactive’ or ‘Run Till it Breaks’ Pitfall