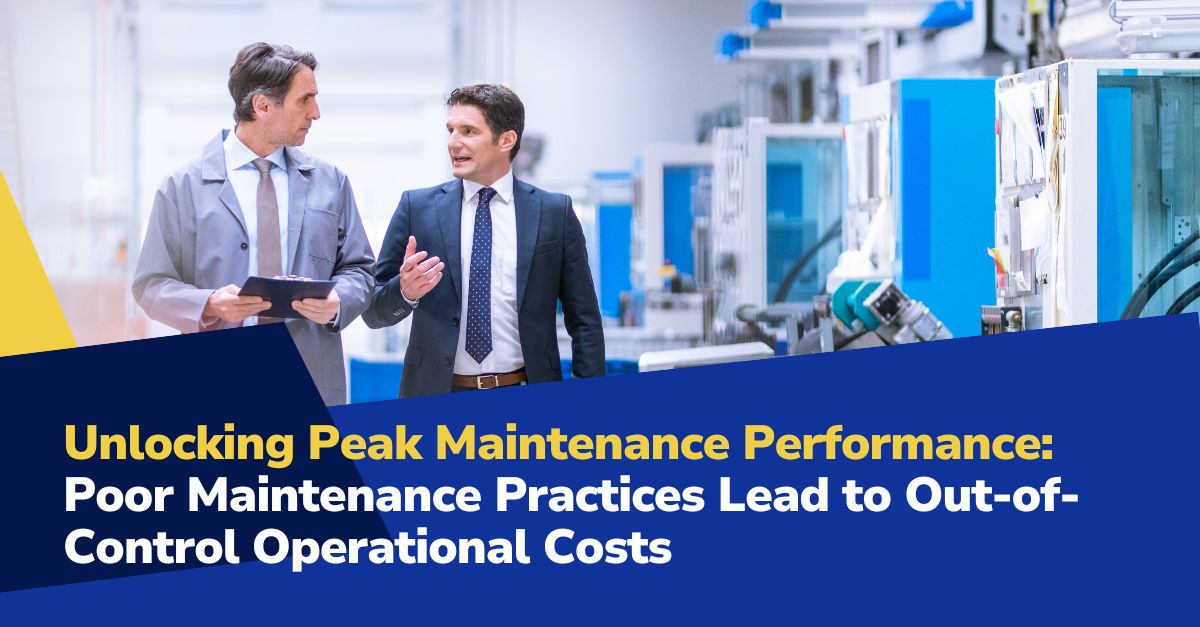
In this insightful sixth installment of the POWERS’ ‘Unlocking Peak Manufacturing Maintenance Performance’ series, we delve deeper into understanding how poorly executed maintenance standards and practices can significantly inflate operational costs in the manufacturing sector.
This article draws on the extensive expertise of the POWERS team, which is renowned for optimizing manufacturing operations. It highlights the top 10 cost-inflating consequences of inadequate maintenance.
The High Cost of Poor Maintenance
1Emergency Repairs and Off-Hours Work:
Emergency repairs, especially those needed outside regular working hours, can be vastly more expensive than scheduled maintenance. The urgency and immediacy required for these repairs often necessitate premium labor rates, sometimes up to double the standard cost, and expedited parts delivery, which can dramatically increase the overall expense.
2Unplanned Downtime:
Unanticipated equipment failures lead to unscheduled downtimes, ultimately disrupting the manufacturing process. This work stoppage halts production and necessitates rushed deliveries and inflated labor costs due to overtime wages. The cost of downtime in manufacturing can be staggering, often amounting to thousands of dollars per hour, directly impacting the bottom line.
3Increased Equipment Wear and Tear:
Inadequate maintenance accelerates the deterioration of machinery. This equipment degradation leads to more frequent and often more severe breakdowns, necessitating costly repairs and parts replacements, which could have been mitigated with regular maintenance.
4Reduced Equipment Efficiency:
Poorly maintained equipment typically consumes more energy and operates less efficiently. This inefficiency translates into higher energy bills and increased resource consumption, adding a significant and avoidable cost to the operational budget.
5Quality Control Issues:
Neglect in maintenance can lead to inconsistencies in product quality. This results in an increase in defective products, waste, and rework, which not only incurs direct costs but can also damage the manufacturer’s reputation and lead to loss of customer trust.
6Safety Hazards and Compliance Risks:
Overlooking maintenance can create serious safety hazards in the workplace, potentially leading to accidents and injuries. These incidents can result in costly legal liabilities, fines, and increased insurance premiums, not to mention the immeasurable cost of harm to employees.
7Extended Lead Times:
Delays in production due to maintenance issues can significantly extend lead times. This affects the manufacturer’s ability to meet customer demands on time and can lead to contract penalties and lost business opportunities.
8Inventory Imbalances:
Unpredictable equipment performance can lead to overproduction or stockouts, causing inventory imbalances. These imbalances often result in additional costs related to storage, handling, and potential product obsolescence.
9Increased Administrative Burden:
The fallout from poor maintenance practices extends to administrative functions. The extra effort required to manage and coordinate repairs, handle customer complaints, and reorganize production schedules adds a layer of indirect costs that can be substantial.
10Long-Term Asset Degradation:
Consistently poor maintenance practices can significantly reduce the lifespan of manufacturing equipment. This premature degradation necessitates earlier-than-expected capital investments for equipment replacement, impacting long-term financial planning and profitability.
The POWERS Approach
The POWERS company addresses these challenges head-on with its Advanced Maintenance Performance (AMP) program. This program provides the tactical and technical know-how and builds an actionable plan. It focuses on proactive maintenance to prevent the issues listed above and to enhance overall operational efficiency, thereby reducing costs and improving productivity.
Conclusions for Senior Operations Leaders
Effective maintenance is a pivotal factor in controlling operational costs and ensuring the longevity and success of manufacturing operations.
By adopting robust and strategic maintenance practices, manufacturers can sidestep the steep costs associated with poor maintenance, paving the way for sustainable growth and enhanced profitability.
For a detailed consultation on improving your manufacturing maintenance practices and reducing operational costs, contact the POWERS team at +1 678-971-4711 or info@thepowerscompany.com.
Continue Reading from this Mastery Series
- Part 1 - The Critical Link Between Maintenance and OEE
- Part 2 - How Maintenance Practices Shape Product Quality
- Part 3 - How Poor Maintenance Standards and Practices Impact Schedule Adherence
- Part 4 - How Maintenance Practices Echo Along the Supply Chain
- Part 5 - The Impact of Maintenance on Maximizing Return on Assets (ROA) in Manufacturing
- Part 6 - Poor Maintenance Practices Lead to Out-of-Control Operational Costs
- Part 7 - Navigating the Safety and Compliance Minefield in Manufacturing
- Part 8 - The High Cost of Overlooking Maintenance in Manufacturing Strategic Planning
- Part 9 - Poor Maintenance Practices Are a Hindrance to Technological Innovations
- Part 10 - Overcoming the ‘Reactive’ or ‘Run Till it Breaks’ Pitfall