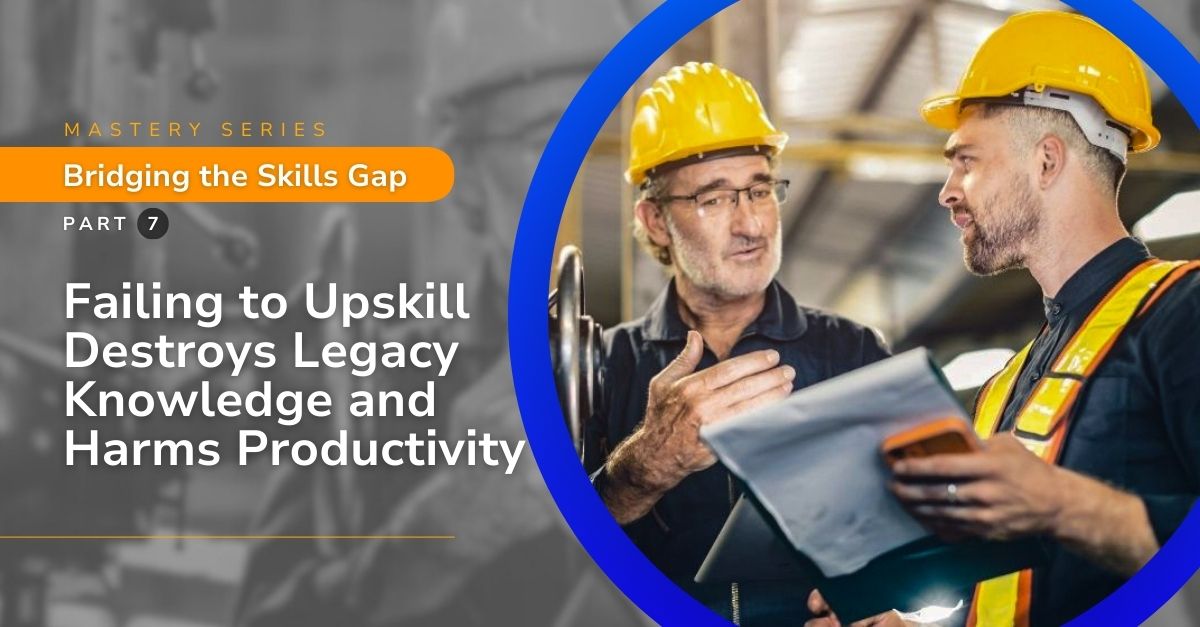
When manufacturing organizations fail to prioritize upskilling, one of the most critical and damaging consequences is the gradual erosion of legacy knowledge, sometimes called ‘tribal knowledge.’
Even routine tasks can become inefficient, and unforeseen issues multiply without it. The loss of the workforce knowledge baked in over decades on the job, doesn’t just affect immediate productivity; it creates a series of secondary symptoms that slowly erode the foundation of the workforce’s operational effectiveness.
For instance, consider a situation where a team member retires, taking with them years of experience maintaining a custom-built machine without a standardized manual. Lacking the specialized knowledge this individual had accumulated, the team became less efficient at identifying and resolving breakdowns. Each new issue takes longer to address, and missteps in maintenance become more frequent, leading to increased downtime.
This isn’t just about troubleshooting. It impacts every other process that relies on that machine, causing delays that ripple across the entire production line. This is just one of many ways that the loss of legacy knowledge from neglecting upskilling manifests itself, creating real consequences for manufacturing operations.
Longer onboarding times for new hires, reduced troubleshooting accuracy, and an increased reliance on a handful of employees to make crucial decisions are just the tip of the iceberg.
These problems might start small but can eventually lead to broader inefficiencies that severely hinder a company’s ability to stay competitive. Neglecting to invest in upskilling doesn’t just lead to individual knowledge gaps—it disrupts the entire ecosystem of operational productivity.
As we explore the top 10 ways the loss of legacy knowledge negatively affects manufacturing, we’ll focus on the granular, day-to-day challenges that managers encounter, offering practical insights into how these issues can be addressed.
1Decreased Accuracy in Troubleshooting Equipment Malfunctions:
When experienced employees leave or retire without proper knowledge transfer, troubleshooting equipment malfunctions becomes more prolonged and error-prone. Without legacy knowledge, technicians struggle to identify recurring issues quickly, often missing subtle patterns that would lead to faster diagnoses.
Mitigation: Implementing a comprehensive knowledge-sharing platform can help capture historical data and lessons learned from past malfunctions, reducing the risk of decreased troubleshooting accuracy. Regular upskilling programs that include practical troubleshooting training and case studies from seasoned technicians ensure that newer employees build the diagnostic expertise they need to maintain efficiency on the shop floor.
2Longer Onboarding Times for New Hires:
Loss of legacy knowledge slows the onboarding process for new employees. New hires often spend extended periods acclimating to operational practices that experienced employees could efficiently communicate. The absence of informal knowledge transfer, typically through mentorship or shadowing, leaves new employees struggling to adapt.
Mitigation: Introducing a structured mentorship program where experienced workers pass down explicit and implicit knowledge to new employees can dramatically shorten onboarding times. Upskilling senior employees with modern training techniques also improves their capacity to transfer knowledge effectively and efficiently to newcomers, ensuring seamless integration into the team.
3Reduced Capacity for Contingency Planning:
When critical legacy knowledge is lost, the ability to craft effective contingency plans diminishes. Employees who understand the company’s history of challenges and successful interventions are better equipped to foresee potential future risks. Without this depth of insight, teams are left vulnerable to disruptions, with limited foresight to anticipate and respond to crises.
Mitigation: To combat reduced contingency planning capacity, companies should document previous challenges and their resolutions in a centralized system accessible to all relevant employees. Regularly updated contingency training sessions and scenario-based planning exercises ensure that teams remain prepared to handle unforeseen disruptions with the benefit of historical context.
4Over-Reliance on a Few Individuals for Critical Information:
In many organizations, a handful of long-tenured employees become the gatekeepers of critical information. This over-reliance creates significant bottlenecks when these individuals are unavailable or leave the organization, causing delays in decision-making and operational inefficiencies.
Mitigation: To reduce overreliance on key individuals, establishing a rotational job shadowing system allows multiple team members to gain exposure to critical processes. Cross-training employees across various functions ensures that important knowledge is distributed more evenly across the workforce, preventing disruptions in case of absenteeism or turnover.
5Delayed Decision-Making Due to Lack of Historical Context:
When legacy knowledge erodes, decision-makers lack the historical context to make informed choices. Historical trends, past project outcomes, and prior mistakes are essential in avoiding repeated missteps, but without that knowledge, decisions can be delayed or misguided.
Mitigation: Implementing a robust knowledge management system that tracks project histories and key decision points can ensure that relevant historical data is readily available to all decision-makers. Regular workshops that include scenario analysis highlighting past decisions and their outcomes can help newer employees better grasp the company’s historical context.
6Decreased Ability to Train New Employees Effectively:
The erosion of legacy knowledge significantly impacts the ability to train new employees. Without experienced workers to guide and mentor them, new hires often struggle to grasp the nuances of operations, resulting in prolonged learning curves and higher error rates.
Mitigation: Establishing formal training programs with detailed documentation and video tutorials can help bridge the knowledge gap. Upskilling senior employees in training, mentoring, and coaching best practices ensures they can deliver effective and consistent education to new hires, reducing the burden of informal knowledge transfer and improving overall training efficiency.
7Increased Reliance on External Contractors for Expertise:
A direct consequence of losing legacy knowledge is that organizations increasingly turn to external contractors to fill expertise gaps. While contractors may bring specialized skills, their involvement often comes at a much higher cost (especially in emergency situations) and with less familiarity with the company’s specific operational needs.
Mitigation: Reducing dependency on external contractors requires internal knowledge retention through regular skill-building initiatives. Continuous training and development programs focusing on foundational and specialized skills will empower existing employees to handle complex tasks in-house, ensuring that critical expertise remains within the organization.
8Misapplication of Specialized Skills in Routine Operations:
The misapplication of specialized skills occurs when employees lack the legacy knowledge to differentiate between when to apply complex solutions and when simpler methods suffice. This misjudgment can lead to inefficiencies, wasted resources, and operational mistakes.
Mitigation: By fostering a learning workplace that emphasizes the strategic application of skills through upskilling and mentoring, employees can gain the discernment needed to use the right tool for the job. Providing employees with decision-making frameworks can help them choose the most appropriate methods for specific tasks.
9Loss of Efficiency in Root Cause Analysis:
Effective root-cause analysis requires an in-depth understanding of past equipment failures and process disruptions. When legacy knowledge fades, teams may struggle to perform efficient root-cause analyses, leading to superficial fixes that fail to address underlying issues.
Mitigation: To maintain efficiency in root cause analysis, companies should create a digital archive of past incidents and resolutions that employees can reference during investigations. Investing in continuous training on advanced root cause analysis techniques will ensure that employees develop the critical thinking skills necessary to identify and resolve issues effectively.
10Overdependence on Outdated Documentation:
As legacy knowledge erodes, many organizations rely on outdated documentation to guide operations. However, this documentation may no longer reflect current processes or technological advancements, leading to inefficiencies and potential errors.
Mitigation: To avoid overdependence on outdated documentation, companies should implement a system for regularly updating and validating process documentation. Upskilling employees on the importance of process management and continuous improvement will ensure that documentation remains accurate and reflects current best practices.
Conclusions for Operations Leaders
The loss of legacy knowledge caused by neglecting investment in upskilling has far-reaching consequences in manufacturing. From longer troubleshooting times to increased reliance on outdated documentation, the gradual erosion of this valuable knowledge base hinders operational efficiency and productivity.
The secondary symptoms—like misapplied skills, delayed decision-making, and longer onboarding times—directly affect the day-to-day operations on the shop floor, leading to significant disruptions in production schedules, increased costs, and lowered competitiveness. Addressing these issues requires more than just plugging knowledge gaps; it demands a proactive approach to continuous improvement, training, and skill development.
Our tailored upskilling programs and operational strategies are designed to address your organization’s specific challenges, ensuring that the loss of legacy knowledge does not hinder growth and efficiency.
By partnering with POWERS, your organization can achieve:
- Improved troubleshooting accuracy through knowledge retention and skill-building programs.
- Faster onboarding times with structured training processes that transfer explicit and implicit knowledge.
- More efficient decision-making by leveraging historical context and reducing over-reliance on a few individuals.
- Increased capacity for root cause analysis with better access to historical data and problem-solving expertise.
POWERS brings a hands-on approach to enhancing productivity, ensuring that your team retains and continuously builds on essential knowledge. With our experience in operations management, finance, and human resources, we work closely with your leadership to align your workforce’s skills with your long-term business goals. Contact us to learn how POWERS can help your organization stay competitive by preserving and enhancing your legacy knowledge base.
- Speak to an Expert: Call +1 678-971-4711 to discuss your specific challenges and goals.
- Email Us: Get tailored insights by emailing info@thepowerscompany.com
- Request an Assessment: Use our online contact form, and one of our expert manufacturing consultants will reach out to schedule an in-depth analysis of your operations.
Continue Reading from this Mastery Series
- Part 1 – Why Automation Alone Won’t Boost Productivity
- Part 2 – Why Non-Technical Skills Are Increasingly the Key to Increasing Productivity
- Part 3 – The Widening Digital Divide is Leaving Some Companies in the Dust
- Part 4 – Lack of Upskilling Sabotages Problem-Solving, Decision Making, and Innovation
- Part 5 – The Link Between Upskilling and Employee Well-being
- Part 6 – Neglecting Upskilling Leaves Your Operation Vulnerable to Safety Issues
- Part 7 – How Neglecting Upskilling Erodes Legacy Knowledge and Hurts Productivity
- Part 8 – Failing to Upskill Frontline Leaders Can Derail Operations
- Part 9 – Skimping on Skills Training Sabotages the Bottom Line
- Part 10 – An Underdeveloped Workforce Means an Unscalable Operation