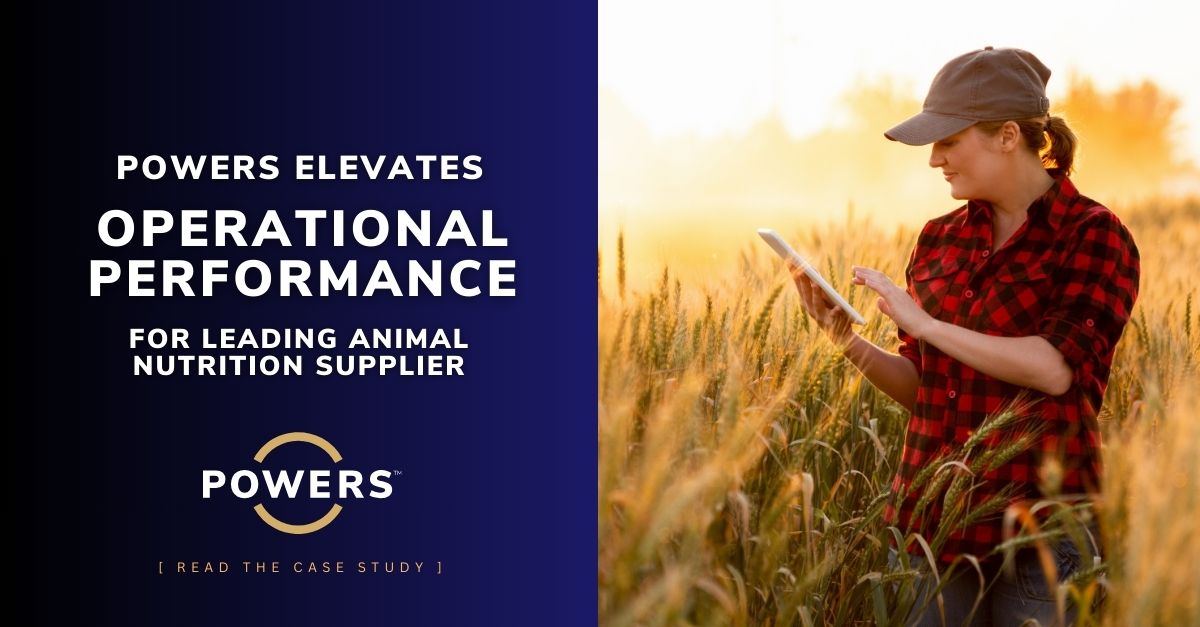
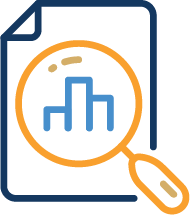
Project Overview
Overview
A major company in the animal nutrition sector faced operational challenges that threatened both its production capabilities and employee morale following a quality-related setback. Determined to enhance production throughput and establish a culture of continuous improvement, the organization enlisted POWERS for a 20-week engagement. This partnership focused on creating a robust Management Operating System (MOS) that would increase productivity, improve employee engagement, and set the organization on a sustainable path for long-term growth and operational resilience.
Through a structured assessment and transformation plan, POWERS collaborated with the company to identify root causes of inefficiency, foster a more engaged workforce, and implement a management system tailored to drive consistent performance improvements. This case study examines the challenges addressed, the transformative steps taken, and the results achieved.
Situation Analysis
The organization faced a combination of operational, cultural, and procedural challenges, each with far-reaching impacts on its overall performance:
- Operational Throughput: Production rates consistently lagged behind optimal levels, limiting the organization’s ability to meet growing demand and eroding its competitive edge……
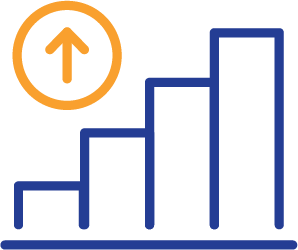
Performance Results
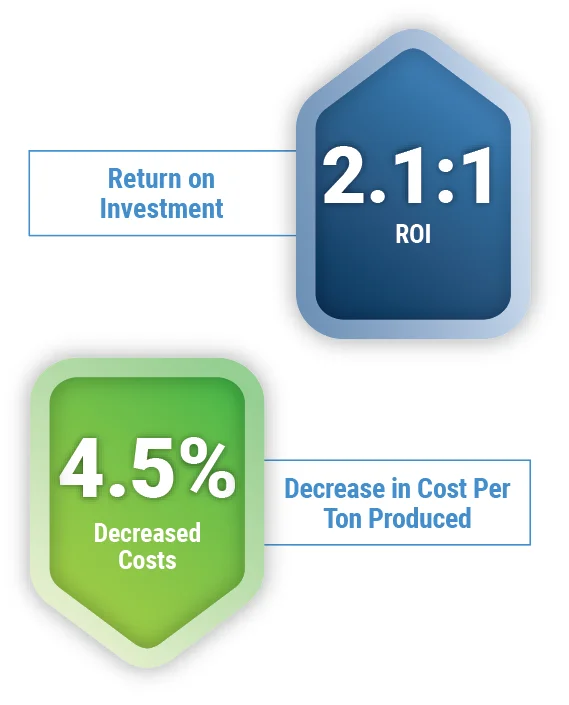
As Plant Manager, I am proud of the strides our management team has made in fostering an environment of continuous improvement and open communication. This growth has improved team morale and enhanced our operational efficiency, setting a strong foundation for sustainable success.
H.M. - Plant Manager
Read the Full Case Study Here
- Employee Morale: The recent quality setback has decreased employee morale, with uncertainty about future stability. Many employees expressed concern, fearing a potential reduction in operations or an eventual shutdown.
- Top-Down Management Style: Traditional, hierarchical management practices had resulted in limited input from frontline employees, who felt disconnected from the decision-making process. This lack of engagement led to detachment and low ownership of daily tasks.
- Delayed and Inaccessible Key Performance Indicators (KPIs): Performance metrics were reported monthly with delays, making it difficult for frontline employees to gauge their contributions to larger company objectives.
Recognizing the need for a more structured and transparent approach, the company partnered with POWERS to implement a transformative plan to improve operational efficiency and workplace culture.
Comprehensive Analysis
To understand the root causes of these challenges, our team conducted an in-depth analysis of the organization’s operations. This assessment revealed several core issues:
- Communication Gaps: The delay in monthly performance reports limited visibility into real-time progress, reducing the organization’s ability to make quick adjustments. Employees lacked daily insights, hindering effective problem-solving and accountability.
- Inconsistent Leadership Roles: Supervisory roles were loosely defined, resulting in management practices that were more reactive than proactive. This ambiguity led to inconsistent follow-through and missed opportunities for preventative actions.
- Lack of Goal Clarity Across Levels: Without clearly defined goals from the executive level to the production floor, employees were unsure how their daily responsibilities aligned with broader objectives. This lack of clarity impeded motivation and productivity.
The assessment highlighted an urgent need for a unified, transparent system to streamline communication, clarify leadership roles, and establish clear performance goals at every level.
The Transformative Plan
Our specialists and the company jointly developed a comprehensive plan to address these challenges, encompassing leadership development, an improved Management Operating System (MOS), and real-time performance tracking.
Leadership Development and Employee Engagement
- Empowering Supervisors: Our on-the-ground team coached supervisors to transition from reactive to proactive management, focusing on identifying and mitigating issues before they escalated. Supervisors were trained to adopt behaviors that prioritize preventative measures, fostering a more resilient and supportive team environment.
- Recognition Programs: A structured employee recognition program, including weekly awards to celebrate positive contributions, was introduced. These initiatives helped rebuild morale and reinforced desired behaviors, creating a culture where employees felt appreciated and valued.
- Daily Communication Meetings: The company implemented a daily Safety, Quality, Delivery, and Cost (SQDC) meeting, where teams could review daily objectives, discuss potential issues, and engage in real-time problem-solving. These meetings established a platform for transparent communication, aligning all employees on short-term goals.
Management Operating System (MOS) Implementation
- Goal Setting and Multilevel Reporting: The company adopted a tiered approach to goal-setting, establishing performance objectives at all levels, from annual targets to hourly expectations. This structured system gave employees a clear understanding of how their work contributed to the organization’s success and allowed regular adjustments to optimize performance.
- Daily/Weekly Operating Reports (DWOR): DWORs were introduced to provide timely insights into performance, empowering employees to make real-time adjustments and take ownership of their results. These reports became a cornerstone of accountability, enabling everyone, from frontline workers to management, to understand their impact on the company’s performance.
- Standardizing Production Processes: Key production lines were standardized, capturing critical operational knowledge and reducing performance variation between shifts. This process, known as centerlining, ensured consistent output and minimized disruptions.
- Enhanced Maintenance Planning: The organization strengthened its preventive maintenance processes with daily assignments tracked via Pocket Cards, which included clear goals and accountability measures for technicians. These daily plans helped optimize maintenance schedules, reduce downtime, and improve equipment reliability.
- Gemba Walks: Leadership began conducting regular Gemba walks to engage directly with frontline staff. This approach opened communication channels, enabling management to gather valuable insights and address issues as they arose, fostering a culture of continuous improvement.
Real-Time Quality and Performance Tracking
- Hold Tag Process: A structured process for tracking quality issues was introduced, enhancing traceability and responsiveness. The organization ensured timely interventions and prevented repeat quality incidents by documenting and monitoring each instance.
- Hourly Monitoring: Supervisors monitored hourly performance metrics to identify and correct deviations from goals, reinforcing the company’s commitment to real-time data-driven decision-making.
- Daily Attainment Tracking: Tracking daily performance achievements reinforced accountability and allowed employees to see how their contributions contributed to the company’s broader goals. This transparency helped cultivate a stronger sense of purpose and engagement.
Results
The project yielded substantial improvements in both performance and employee engagement, reflecting the effectiveness of POWERS’ structured approach:
- Financial Impact: The project achieved significant financial gains and delivered a return on investment of 2.09:1.
- Enhanced Shift Performance: The integration of Plan Actual Variance Action (PAVA) and DWOR methodologies provided immediate feedback to employees, improving engagement and consistency across shifts.
- Maintenance Efficiency: Daily Pocket Cards for maintenance assignments improved technician accountability, reduced downtime, and contributed to smoother, more reliable operations.
- Improved Quality Control: The Hold Tag process provided better control over quality issues, ensuring timely documentation of corrective actions and reducing the likelihood of quality-related setbacks.
- Employee Morale and Engagement: Through regular recognition programs and clearly defined goals, employees felt more connected to their work and valued for their contributions, translating to a more motivated and engaged workforce.
- Reduction in Labor Hours: Optimized staffing and task allocation led to a 4.5% reduction in labor hours and a lower cost per ton produced, underscoring the overall efficiency improvements.
Conclusion and Next Steps
By implementing a comprehensive Management Operating System and focusing on leadership development, the company has built a solid foundation for continuous improvement. Lean Manufacturing principles, structured audits, and real-time feedback are now woven into daily operations, promoting sustained performance gains and a culture of accountability. Looking ahead, the organization is committed to maintaining the progress achieved through POWERS’ guidance and actively engaging employees in its pursuit of operational excellence.