
When manufacturing companies fail to embrace Industry 4.0, they leave themselves vulnerable to various operational inefficiencies that can severely impact productivity.
Digital transformation is no longer a luxury but a necessity for optimizing processes, particularly regarding inventory management.
Manufacturers rely on outdated, manual methods to manage their inventory without modern, data-driven systems. This leads to inefficiencies that drive up carrying costs and disrupt the supply chain. These issues don’t just stay within inventory control—they spread into other operational areas, slowing down production and negatively impacting financial performance.
One lesser-known example is the increased costs of maintaining specialized inventory items for custom-built machinery. Manufacturers relying on legacy inventory systems may over-order niche components with long lead times, tying up capital in inventory that will take months to turn over.
With no real-time data on how these parts are being used or replenished, companies are forced to stockpile more than necessary. The result is higher carrying costs, wasted warehouse space, and excess labor dedicated to tracking slow-moving items—all symptoms of neglecting digital transformation.
This situation is common for companies in aerospace manufacturing, where certain materials or parts are difficult to source and have limited shelf lives. By failing to embrace digital inventory solutions, companies often err on the side of caution and overstock, leading to inventory obsolescence, inflated overhead, and poor allocation of resources. These issues are exacerbated by the manual entry of data, reliance on outdated communication systems between departments, and the inability to predict demand fluctuations—factors that all tie back to the broader consequence of neglecting digital transformation in manufacturing.
In part 8, we’ll explore how neglecting Industry 4.0 leads to inefficient inventory management and increased carrying costs, diving into specific symptoms like stock inaccuracies, failure to implement just-in-time practices, and over-reliance on buffer stock. Each of these issues poses unique challenges to productivity, but they are all solvable with the right digital approach.
1Failure to Identify Optimal Reorder Points:
Companies struggle to pinpoint optimal reorder points without digital systems to analyze inventory trends accurately. This often leads to either stockouts or over-ordering, which disrupts the supply chain. Manual tracking methods fail to account for real-time sales or usage patterns, making it nearly impossible to maintain the right inventory levels.
Mitigation: Embracing advanced inventory management software with real-time analytics allows businesses to track demand patterns and historical usage accurately. Automated systems can calculate optimal reorder points dynamically, adjusting in response to seasonality, promotions, or market changes. This mitigates stockouts and reduces excess inventory, leading to lower carrying costs and improved operational flow.
2Inability to Predict Inventory Demand Fluctuations:
Manual inventory systems lack predictive analytics, making it difficult to forecast fluctuations in demand. Without data-driven insights, businesses may understock high-demand items or overstock slower-moving ones, tying up capital and creating bottlenecks in the supply chain.
Mitigation: Predictive analytics tools powered by machine learning can analyze past trends, external factors, and real-time data to accurately forecast demand. This enables businesses to adjust their purchasing strategies proactively, ensuring the right products are available when needed, reducing excess inventory, and improving cash flow.
3Increased Labor Costs from Manual Inventory Tracking:
Manual inventory tracking is time-consuming and labor-intensive, often requiring additional staff to perform routine checks. Errors in counting or entering data can lead to discrepancies that take hours, or even days, to resolve, further increasing labor costs and causing operational delays.
Mitigation: Automating inventory management through digital platforms reduces the need for manual checks and data entry. RFID technology and barcode scanning can instantly update inventory levels in the system, minimizing errors and reducing labor requirements. This frees employees to focus on higher-value tasks, driving productivity while cutting labor costs.
4Difficulty in Coordinating Just-in-Time Inventory Practices:
Without real-time data and sophisticated inventory management systems, implementing just-in-time (JIT) inventory practices becomes extremely challenging. Companies relying on outdated methods face delayed supplier communication, resulting in inventory shortages or overstocking as a buffer against uncertainty.
Mitigation: Digital transformation can enhance JIT practices by enabling real-time communication between suppliers and production teams. Inventory management systems integrated with supplier networks allow for automated ordering and replenishment based on actual consumption data. This reduces buffer stock, cuts carrying costs, and keeps inventory levels lean and efficient.
5Over-Reliance on Buffer Stock to Avoid Stockouts:
Many companies hold excessive buffer stock to avoid stockouts, tying up capital and increasing storage costs. This approach results from an inability to accurately forecast demand or manage supplier lead times efficiently, both symptoms of neglecting digital inventory tools.
Mitigation: Adopting a demand-driven inventory management system can reduce reliance on buffer stock. These systems use real-time sales data, supplier performance metrics, and predictive analytics to optimize inventory levels, ensuring that stock is ordered and delivered as needed. This reduces the need for expensive buffer inventory, freeing up working capital and storage space.
6Frequent Stock Inaccuracies Due to Manual Entry Errors:
Manual data entry is prone to human error, leading to frequent inaccuracies in stock levels. These discrepancies can cause delays in production, unexpected stockouts, and the need for emergency orders, all of which disrupt the flow of operations and inflate costs.
Mitigation: Implementing an automated inventory tracking system that uses barcode or RFID scanning eliminates the risk of human error in data entry. These systems ensure real-time accuracy in stock levels, reducing the need for frequent cycle counts or reconciliations. Accurate inventory data enables smoother operations, reduces downtime, and enhances productivity.
7Increased Lead Times Due to Inefficient Inventory Reconciliation:
Inefficient manual reconciliation of inventory records often leads to extended lead times. When stock discrepancies are discovered, investigating the cause and reconciling physical counts with system records is wasted, which delays ordering and restocking processes.
Mitigation: Digitizing the inventory reconciliation through integrated warehouse management systems can significantly cut lead times. Automated data collection provides a real-time view of stock levels, instantly flagging discrepancies and streamlining reconciliation. By minimizing delays, companies can maintain optimal stock levels, reduce lead times, and improve customer satisfaction.
8Limited Visibility into Inventory Across Multiple Sites:
Companies operating across multiple locations without a centralized digital inventory system often struggle with limited visibility into stock levels at each site. This can lead to overstocking in some locations and stockouts in others, increasing carrying costs and lowering overall efficiency.
Mitigation: A cloud-based inventory management system provides real-time centralized visibility across all sites. With this level of transparency, managers can balance stock between locations, reduce over-ordering, and quickly transfer stock where it’s needed most. Improved visibility reduces unnecessary holding costs and enhances supply chain efficiency.
9Over-Ordering Slow-Moving Items That Tie Up Capital:
Without accurate data on item turnover rates, companies often over-order slow-moving products, which ties up valuable capital and increases storage costs. This results in high carrying costs and decreased liquidity, hindering the company’s ability to invest in other business areas.
Mitigation: Advanced inventory management systems that track item turnover and sales velocity can help managers make data-driven purchasing decisions. By identifying slow-moving items, businesses can reduce excess orders, focus on high-demand products, and optimize their inventory mix. This improves cash flow and reduces the cost of holding obsolete inventory.
10Increased Spoilage or Obsolescence of Inventory:
Companies that fail to digitally track expiration dates or obsolescence risk stockpiling goods that may spoil or become obsolete before they can be sold. This is especially critical in industries with perishable goods or fast-evolving products, leading to significant financial losses from unsellable stock.
Mitigation: Implementing automated inventory tracking with features to flag products nearing expiration dates or obsolescence reduces waste. Real-time alerts enable managers to take proactive action, such as discounting items or adjusting purchasing strategies to prevent spoilage. This system helps reduce inventory carrying costs, prevent unnecessary losses, and improve profitability.
Conclusions for Operations Leaders
Neglecting digital transformation in manufacturing doesn’t just lead to inefficient inventory management—it creates a chain reaction of missed opportunities, inflated costs, and reduced productivity. The challenges of relying on outdated systems can result in higher labor costs, lost visibility into stock levels, and overstocking slow-moving items, which drain capital and limit operational flexibility. These inefficiencies hinder your ability to remain competitive, especially as industry leaders increasingly adopt AI-driven systems and real-time data analytics to streamline their processes.
The key to overcoming these challenges lies in embracing the right digital tools, such as those provided by POWERS.
How POWERS Can Help:
At POWERS, we don’t just diagnose the problems—we offer tailored solutions to help you thrive in the digital age. Our Digital Production System (DPS) is designed to equip manufacturers with the tools to transform their operations from inventory management to overall productivity. With DPS, you can access real-time data and AI-powered insights that empower you to make smarter, faster decisions.
Here’s how POWERS and DPS can improve your productivity:
- Comprehensive Operational Visibility: Monitor all aspects of your manufacturing processes in real time, ensuring seamless operations and timely interventions.
- Intelligent Forecasting: Leverage AI-driven insights to predict market trends and operational needs, enabling proactive decision-making and resource optimization.
- Streamlined Communication: Real-time data sharing enhances coordination between teams and departments, ensuring accurate and timely responses to production needs.
- Improved Resource Allocation: Automating routine tasks minimizes labor costs associated with manual inventory tracking, freeing up your team for higher-value work.
- Enhanced Efficiency: Leverage AI-driven insights to predict and resolve inefficiencies before they disrupt operations, reducing downtime and boosting overall throughput.
With the expertise of POWERS and the powerful capabilities of DPS, you can take control of your inventory management, reduce carrying costs, and unlock new levels of productivity in your manufacturing operations. Ready to embrace Industry 4.0 and transform your business? Contact POWERS today to start your digital transformation journey.
- Speak to an Expert: Call +1 678-971-4711 to discuss your specific challenges and goals.
- Email Us: Get tailored insights by emailing info@thepowerscompany.com
- Request an Assessment: Use our online contact form, and one of our expert manufacturing consultants will reach out to schedule an in-depth analysis of your operations.
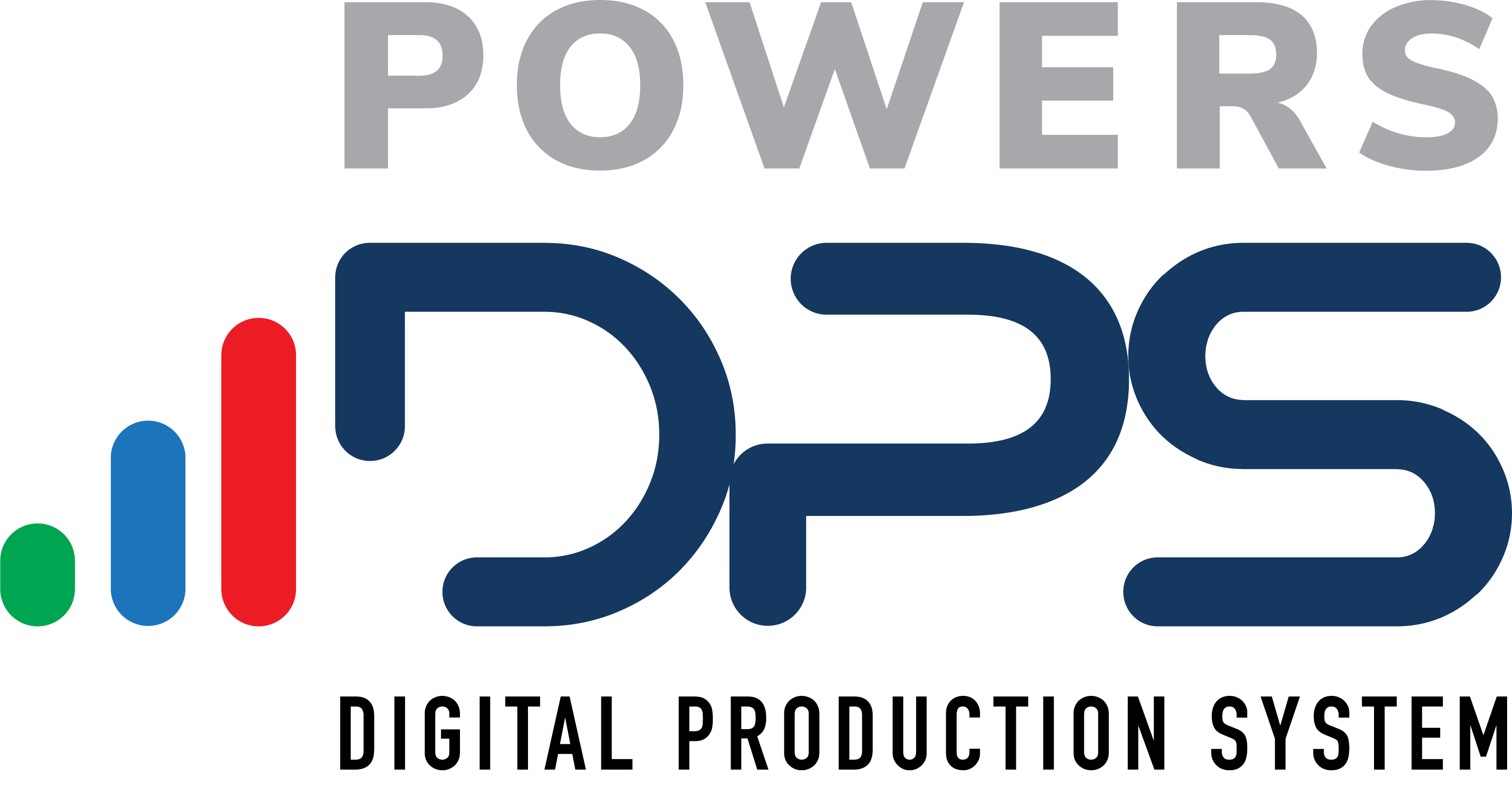
Start transforming your operations today with POWERS DPS. Contact us for a free consultation and see how digital transformation can revolutionize your manufacturing future. Learn More about DPS
Continue Reading from this Mastery Series
- Part 1 – Outdated Tech is Weakening Your Talent Pipeline
- Part 2 – How Legacy Systems Sabotage Your Cybersecurity and Productivity
- Part 3 – How Ignoring Digital Tools Leaves You Vulnerable to Downtime
- Part 4 – When Digital Stagnation Leads to Poor Communication and Production Chaos
- Part 5 – The Real Cost of Trying to Keep Up in the Market Without Digital Transformation
- Part 6 – Missing Out on Real-Time Data Drains Productivity and Profit
- Part 7 – How Failing To Go Digital Jeopardizes Regulatory Compliance
- Part 8 – How Outdated Inventory Practices Sabotage Your Operations
- Part 9 – Limited Customization Options are Driving Your Customers Away
- Part 10 – The Productivity Trap of Failing to Scale Digital Initiatives