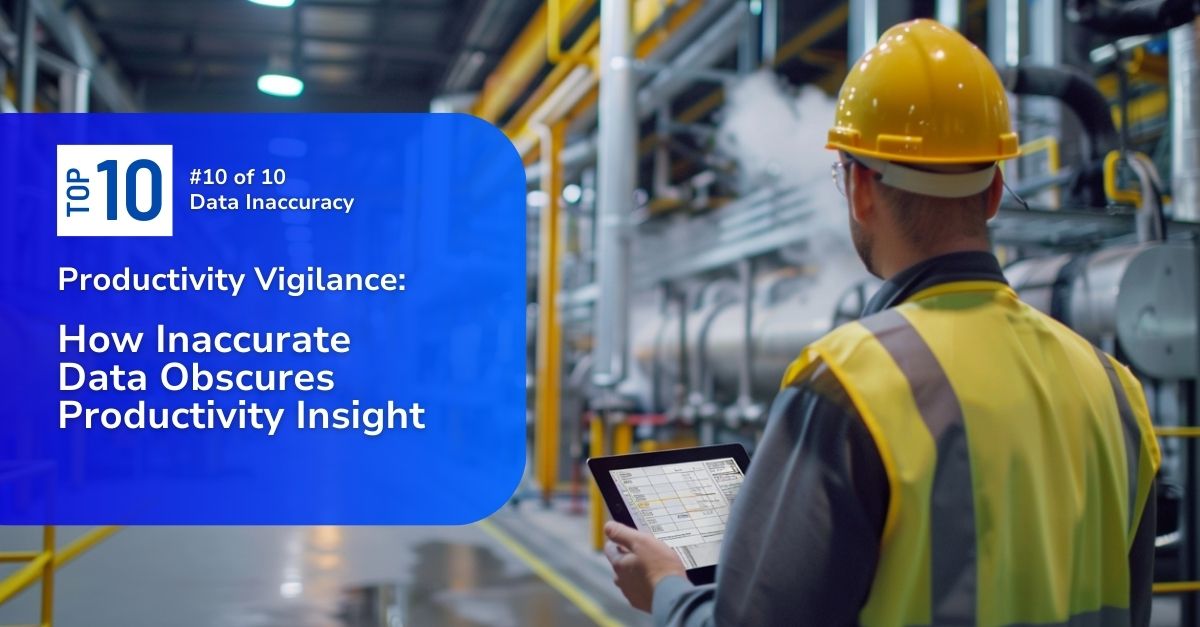
The effects of inaccurate data extend beyond immediate mistakes, creating less obvious symptoms that permeate the production environment.
These symptoms often manifest in subtle but impactful ways, such as misalignment in production schedules, inefficiencies in resource allocation, and unexpected downtimes. For instance, if inventory data inaccurately reflects stock levels, production planners may allocate resources inefficiently, leading to bottlenecks or idle times. This mismanagement not only disrupts the workflow but also diminishes overall productivity.
One less common yet significant example of how data inaccuracy affects productivity is through misguided expansion decisions. If the data used to forecast market demand and production capacity is inaccurate, a manufacturer might invest in expanding facilities or acquiring new equipment based on inflated growth projections. This could lead to overbuilt infrastructure and underutilized assets, resulting in higher overhead costs without a corresponding increase in production output. The financial strain from such miscalculations can force a company to cut back on other critical areas like maintenance, staff training, or technological upgrades, further hampering productivity.
By addressing these issues at their source and implementing robust data management practices, manufacturers can prevent the secondary symptoms of data inaccuracy and ensure smoother, more efficient operations.
1Inaccurate Material Yield Calculations:
Inaccurate material yield calculations lead to misestimating the raw materials required for production. When material yields are overestimated, excess raw materials are purchased, tying up capital in inventory that could be used elsewhere. Conversely, underestimations can cause material shortages, halt production, and lead to costly downtime. This inconsistency disrupts the production schedule and reduces overall efficiency.
Mitigation: Implementing robust data validation protocols and advanced analytics tools can help ensure accurate material yield calculations. Regular audits of yield data and incorporating real-time feedback from the production line can further refine these calculations. Training staff to understand the importance of accurate data entry and providing tools that simplify data recording can also reduce errors.
2Overproduction of Low-Demand Products:
Overproduction of low-demand products often results from inaccurate demand forecasting data. When production schedules are based on incorrect demand projections, resources are wasted on manufacturing items that do not sell, leading to excess inventory and increased holding costs. This ties up valuable resources and causes storage issues and potential product obsolescence.
Mitigation: Integrating real-time sales data and employing predictive analytics can enhance demand forecasting accuracy. Forecasts should also be reviewed and adjusted regularly to reflect actual market conditions. Implementing a just-in-time production system can also help minimize the risk of overproduction by aligning production closely with actual demand.
3Underutilization of High-Performing Equipment:
Data inaccuracy can obscure equipment performance, leading to underutilization of high-performing machines. This can occur when inaccurate or incomplete maintenance records, operational efficiency data, or production logs. As a result, equipment that could significantly enhance productivity is not used to its full potential, leading to suboptimal production rates.
Mitigation: Use accurate, real-time data collection systems to monitor equipment performance continuously. Implementing an automated maintenance management system that tracks equipment efficiency can help identify high-performing equipment. Regularly training maintenance and operations staff on using these systems ensures that data is accurate and utilized effectively.
4Misguided Equipment Maintenance Schedules:
Inaccurate data on equipment usage and performance can lead to misguided maintenance schedules. Performing maintenance too frequently wastes resources, while infrequent maintenance can result in unexpected breakdowns and costly repairs. Both scenarios disrupt production and reduce overall productivity.
Mitigation: Adopt predictive maintenance strategies that rely on accurate, real-time data. Sensors and IoT devices can provide precise data on equipment conditions, scheduling maintenance based on actual needs rather than estimated intervals. This approach minimizes downtime and extends the lifespan of machinery.
5Misguided Expansion Strategies:
When expansion strategies are based on inaccurate data, companies might invest in new facilities or equipment that do not align with actual production needs or market demand. This misallocation of resources can lead to financial losses and reduced productivity as new investments fail to generate the expected returns.
Mitigation: Base expansion decisions on comprehensive and accurate data analysis. Market research, production data, and financial projections inform expansion strategies. Regularly review and validate the data used in these analyses to ensure it reflects current conditions and trends.
6Delayed Implementation of Corrective Actions:
Inaccurate data can delay the identification and implementation of corrective actions. The resolution process is hindered when production issues or quality defects are not promptly and accurately reported. This delay prolongs the period during which the issue affects productivity, leading to increased scrap rates, rework, and downtime.
Mitigation: Implement real-time monitoring and reporting systems that provide accurate data on production processes. Encourage a culture of prompt reporting and quick response to issues. Using automated alert systems can ensure that any deviation from expected performance is immediately flagged and addressed.
7Misguided Selection of Raw Materials:
Selecting raw materials based on inaccurate data regarding their quality or performance can result in substandard products and increased production costs. Poor-quality raw materials lead to higher defect rates, more rework, and increased waste, all of which negatively impact productivity.
Mitigation: Establish rigorous testing and validation processes for raw materials. Use historical data and performance analytics to select suppliers and materials that consistently meet quality standards. Regularly review and update the criteria used for raw material selection to reflect current production needs and quality expectations.
8Overlooking Potential for Partnerships and Collaborations:
Inaccurate data can obscure opportunities for beneficial partnerships and collaborations. Without precise information on production capacities, market trends, and technological advancements, companies may miss out on synergies that could enhance productivity and innovation.
Mitigation: Maintain a centralized database of accurate, up-to-date information on production capabilities, market trends, and potential partners. Encourage cross-departmental collaboration and data sharing to identify and pursue partnership opportunities. Leveraging data analytics can also help uncover hidden opportunities for collaboration.
9Overestimation of Automation Potential:
Overestimating the potential benefits of automation based on inaccurate data can lead to misguided investments in technology. When the actual production needs and capabilities do not align with the perceived benefits of automation, companies may face integration challenges, increased costs, and disrupted workflows.
Mitigation: Conduct thorough feasibility studies using accurate data to assess the potential impact of automation. Pilot automation projects on a small scale before full implementation to identify potential issues and adjust strategies accordingly. Continuous monitoring and data analysis post-implementation can also help optimize automation efforts.
10Overlooking Potential for Process Standardization:
Inaccurate data can lead to overlooking the benefits of process standardization. Without clear and precise data on process performance, variability in production methods may go unnoticed, resulting in inefficiencies and inconsistent product quality.
Mitigation: Implement standardized data collection and reporting procedures across all production processes. Use this data to identify areas where standardization can improve efficiency and quality. Regularly review and update standard operating procedures to ensure they reflect best practices and current data insights.
Conclusion for Manufacturing Leadership
Data inaccuracy isn’t just an inconvenience; it’s a stealthy force that can undermine your manufacturing success. By recognizing its pervasive impact and proactively addressing the secondary symptoms, you can safeguard your productivity, profitability, and competitive edge.
The POWERS methodology – Prioritize, Organize, Work Efficiently, Evaluate, and Sustain – offers a comprehensive framework to tackle data inaccuracy head-on.
How POWERS Can Help
- Optimize Resource Allocation: Accurate data ensures that materials, equipment, and personnel are deployed effectively, minimizing waste and maximizing output.
- Enhance Decision-Making: Data-driven decisions based on accurate information lead to better strategies, from production planning to market expansion.
- Improve Customer Satisfaction: Reliable data helps you deliver consistent, high-quality products that meet customer expectations, fostering loyalty and repeat business.
- Increase Profitability: By eliminating the hidden costs of data inaccuracy – from excess inventory to production delays – you can unlock significant financial gains.
- Foster Continuous Improvement: A data-centric approach enables you to identify areas for improvement, implement changes, and track their impact, driving ongoing productivity gains.
- Speak to an Expert: Call +1 678-971-4711 to discuss your specific challenges and goals.
- Email Us: Get tailored insights by emailing info@thepowerscompany.com
- Request an Assessment: Use our online contact form, and one of our expert manufacturing consultants will reach out to schedule an in-depth analysis of your operations.
Continue Reading from this Mastery Series
- Part 1 – Without Top Talent, Top Productivity is Elusive
- Part 2 – How Blind Spots in Cost Analysis Hide Your Productivity Struggles
- Part 3 – When Supply Chain Issues Deliver A Productivity Hit
- Part 4 – Environmental Threats that Threaten Your Productivity
- Part 5 – Don’t Let Scaling Up Bring Down Your Productivity
- Part 6 – How Vulnerabilities to Disruptions Undermine Productivity
- Part 7 – Why Ignoring TPM Means Missing Out on Productivity Goals
- Part 8 – How Poor Training and Development Creates Productivity Shortfalls
- Part 9 – How Delayed NPIs Lead to Productivity Misses
- Part 10 – How Inaccurate Data Obscures Productivity Insight