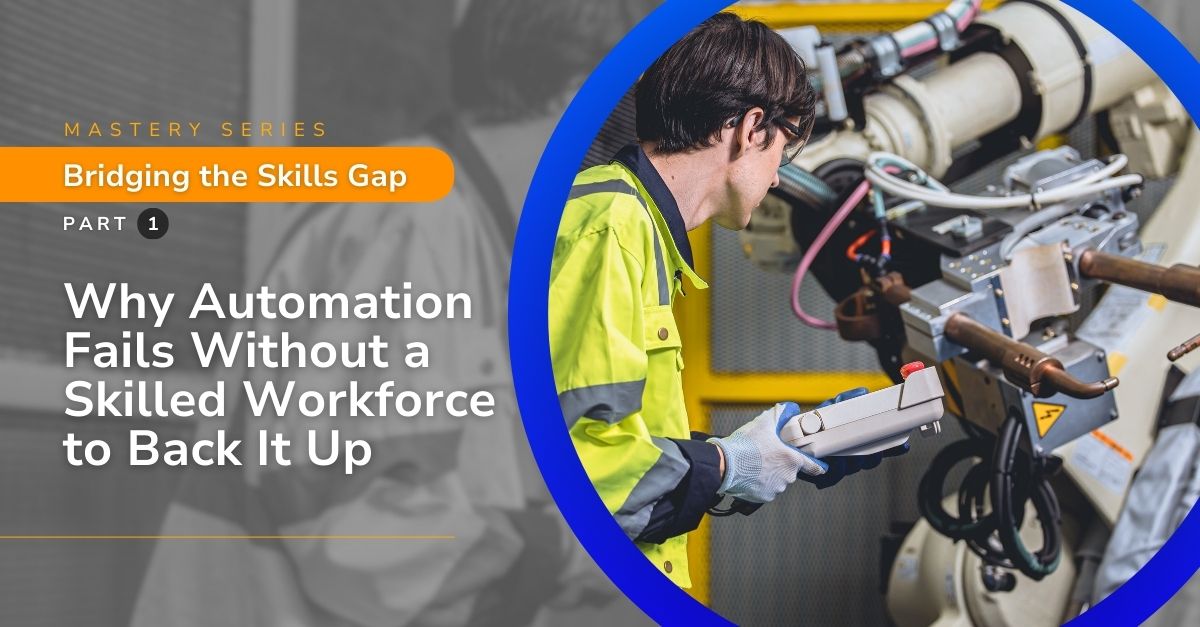
The shift toward automation in manufacturing offers the potential for improved efficiency and reduced costs. However, the promise of automation is often undermined when organizations fail to invest in upskilling or reskilling their workforce.
Many manufacturers expect automating processes to automatically drive efficiency, but automation often falls short of expectations without a skilled workforce to support these technologies.
For example, consider a plant that uses advanced robotics for material handling and assembly. Without proper training, workers may not fully understand how to program or adjust the robotic systems to accommodate changes in product specifications or material variations.
In cases where different raw materials require adjustments in the robot’s grip strength or positioning, untrained employees might leave the settings as-is, leading to increased defects or even damage to the equipment.
What should be a streamlined process instead becomes a source of production slowdowns, waste, and machine wear. This gap between automation capabilities and workforce skills erodes the potential efficiency gains that automation promises, causing significant downtime and costly errors.
Beyond these operational inefficiencies, the lack of upskilling can lead to secondary issues like the inability to respond to fluctuating demand. When employees aren’t trained to recalibrate systems for increased or decreased production volumes, the factory may experience overproduction or underproduction, contributing to higher inventory costs or unmet customer orders.
This is a direct result of insufficient training, where employees cannot optimize automated systems for real-world variations. These challenges don’t stem from automation itself but from the failure to align employee skills with new technologies, turning what should be an advantage into a liability.
This article explores ten key ways that neglecting upskilling your workforce amplifies the negative impact of automation on productivity, focusing on real issues managers face on the shop floor.
1Increased Dependency on External Technical Support:
When employees are not adequately trained to handle the complexities of automated systems, organizations become increasingly reliant on external technical support. Minor malfunctions or routine maintenance tasks that could be resolved in-house instead require expensive and time-consuming third-party assistance. This dependency leads to delays in production and significant cost overruns as external consultants are called in more frequently.
Mitigation: Investing in comprehensive training programs that equip employees with the knowledge needed to maintain and troubleshoot automated systems can drastically reduce this dependency. Cross-training key personnel ensures that technical issues are quickly resolved internally, minimizing production downtime and decreasing reliance on costly external support.
2Reduced Ability to Troubleshoot Automation Failures:
Automation systems can fail due to both hardware and software issues. When employees lack the skills to troubleshoot these failures, they may be forced to wait for specialized technicians, further slowing down operations. This creates bottlenecks in production, eroding the potential gains from automation and frustrating teams as machines stand idle.
Mitigation: Providing ongoing technical training, specifically in troubleshooting and basic diagnostics, empowers employees to resolve problems before they escalate. Managers can avoid unnecessary delays and keep operations running smoothly by creating a workforce capable of identifying and addressing issues on the fly.
3Slower Adoption of New Automation Technologies:
Automation technology is constantly evolving, and organizations that neglect upskilling will find it challenging to implement new tools. When employees aren’t trained in the latest technologies, resistance to change grows, and integrating new systems becomes a slow and painful process. This leads to missed opportunities for optimizing production and staying competitive.
Mitigation: Establishing a continuous learning and skill development culture will facilitate smoother adoption of new technologies. Regular workshops and hands-on training for new automation tools ensure that employees feel comfortable with changes, reducing resistance and accelerating the integration of advanced systems.
4Higher Error Rates in Automated Processes:
Automation does not eliminate the potential for human error; rather, it shifts the source of errors from manual tasks to system setup and oversight. Without proper training, employees may configure automated systems incorrectly, leading to higher error rates in production processes. These errors often go unnoticed until they result in defective products or equipment malfunctions, further compounding losses.
Mitigation: Upskilling employees on the intricacies of system setup and quality control reduces the likelihood of errors. Training workers to thoroughly understand the operations they are overseeing ensures that automated processes are fine-tuned and accurate, preventing costly mistakes.
5Inefficient Utilization of Automated Systems:
Even when automated systems are in place, a lack of upskilling can lead to inefficiencies in using these tools. Employees may only leverage a fraction of an automation system’s capabilities, leaving potential improvements in speed, quality, and capacity untapped. This inefficiency undermines the initial investment in automation.
Mitigation: Targeted training on the full functionality of automation tools allows employees to maximize the benefits of these systems. Ensuring workers understand all features and applications of automated tools will lead to more efficient use, driving productivity improvements and reducing wasted potential.
6Misalignment Between Automation Capabilities and Workforce Skills:
When automation systems are more advanced than the workforce’s skills, a misalignment can result in underperformance. Employees may struggle to effectively operate or collaborate with automated systems, creating frustration and a disconnect between human operators and their tools. This gap stifles innovation and efficiency.
Mitigation: Developing upskilling programs that bridge the gap between automation technologies and workforce capabilities ensures a smooth interface between human operators and machines. This alignment allows workers to harness the full potential of automation while fostering innovation and reducing operational friction.
7Increased Downtime Due to Automation Mismanagement:
Automation mismanagement, driven by a lack of operator training, often leads to extended downtime. Employees may be unable to restart systems after a fault, properly calibrate machines, or adjust to changing production demands, leading to prolonged periods of inactivity. This downtime directly reduces productivity and adds to production costs.
Mitigation: Ongoing training on system management, calibration, and adjustment techniques can empower employees to handle complex automation tasks easily. Businesses can reduce downtime and ensure continuous operation by fostering a deeper understanding of how to manage automated systems.
8Overburdened Workforce Due to Automation Gaps:
Automation gaps occur when systems are in place, but the workforce isn’t equipped to fully utilize them. As a result, employees may become overburdened with tasks that should be automated, such as manual data entry, oversight, or troubleshooting, while also dealing with their regular responsibilities. This creates burnout and decreases overall productivity.
Mitigation: Training employees to fully utilize automation capabilities can relieve the pressure on the workforce. Empowering employees to delegate routine tasks to automated systems allows them to focus on higher-value activities, preventing burnout and increasing employee productivity.
9Inaccurate Data Interpretation from Automated Systems:
Automated systems generate large volumes of data, but without proper training, employees may misinterpret this information or overlook key insights. Poor data interpretation leads to misguided decisions, inefficiencies in production, and misallocation of resources. When data is not utilized correctly, the benefits of automation are diminished.
Mitigation: Upskilling programs focusing on data literacy and analytics are essential to ensure employees can correctly interpret and act on data generated by automated systems. Training workers to analyze and apply insights from automation will lead to better decision-making and more efficient resource use.
10Decline in Employee Engagement Due to Automation Alienation:
Automation can create feelings of alienation among workers who lack the skills to interact with advanced systems. When employees feel disconnected from the tools they are supposed to use, their engagement and job satisfaction decline. This, in turn, leads to higher turnover rates, reduced productivity, and increased training costs for new hires.
Mitigation: Investing in upskilling that promotes collaboration between humans and machines can reduce feelings of alienation. By providing opportunities for employees to engage with automated systems and feel confident in their role within an automated environment, organizations can boost morale, increase retention, and improve productivity.
Conclusions for Operations Leaders
The potential benefits of automation in manufacturing are immense, but without a properly trained workforce, those benefits can quickly turn into obstacles.
Neglecting investment in upskilling amplifies the challenges posed by automation, leading to inefficiencies, increased downtime, and costly errors on the shop floor. From reduced troubleshooting abilities to misalignment between workforce skills and automation capabilities, the secondary symptoms of this oversight can significantly harm productivity.
By addressing these issues through targeted upskilling programs, manufacturers can reduce their dependency on external support and fully optimize their automation systems.
This is where POWERS can make a lasting impact. With deep expertise in workforce development and productivity enhancement,
POWERS offers tailored solutions that address the root causes of operational inefficiencies. Our approach ensures that your employees are equipped with the right skills to manage and optimize automation effectively, leading to long-term improvements in productivity and performance.
Here’s how POWERS can help you:
- Develop comprehensive upskilling programs to align workforce capabilities with automation technologies.
- Provide hands-on employee training to troubleshoot and maintain automated systems, reducing costly downtime
- Offer guidance on how to maximize the efficiency of your automation systems, ensuring optimal utilization.
- Work alongside leadership to foster a continuous learning and adaptability culture in your workforce.
By investing in your workforce and closing the skills gap, you’re not just improving productivity—you’re future-proofing your operation.
Let POWERS help you navigate the complexities of automation with a well-equipped, confident team that can drive your business forward.
- Speak to an Expert: Call +1 678-971-4711 to discuss your specific challenges and goals.
- Email Us: Get tailored insights by emailing info@thepowerscompany.com
- Request an Assessment: Use our online contact form, and one of our expert manufacturing consultants will reach out to schedule an in-depth analysis of your operations.
Continue Reading from this Mastery Series
- Part 1 – Why Automation Alone Won’t Boost Productivity
- Part 2 – Why Non-Technical Skills Are Increasingly the Key to Increasing Productivity
- Part 3 – The Widening Digital Divide is Leaving Some Companies in the Dust
- Part 4 – Lack of Upskilling Sabotages Problem-Solving, Decision Making, and Innovation
- Part 5 – The Link Between Upskilling and Employee Well-being
- Part 6 – Neglecting Upskilling Leaves Your Operation Vulnerable to Safety Issues
- Part 7 – How Neglecting Upskilling Erodes Legacy Knowledge and Hurts Productivity
- Part 8 – Failing to Upskill Frontline Leaders Can Derail Operations
- Part 9 – Skimping on Skills Training Sabotages the Bottom Line
- Part 10 – An Underdeveloped Workforce Means an Unscalable Operation