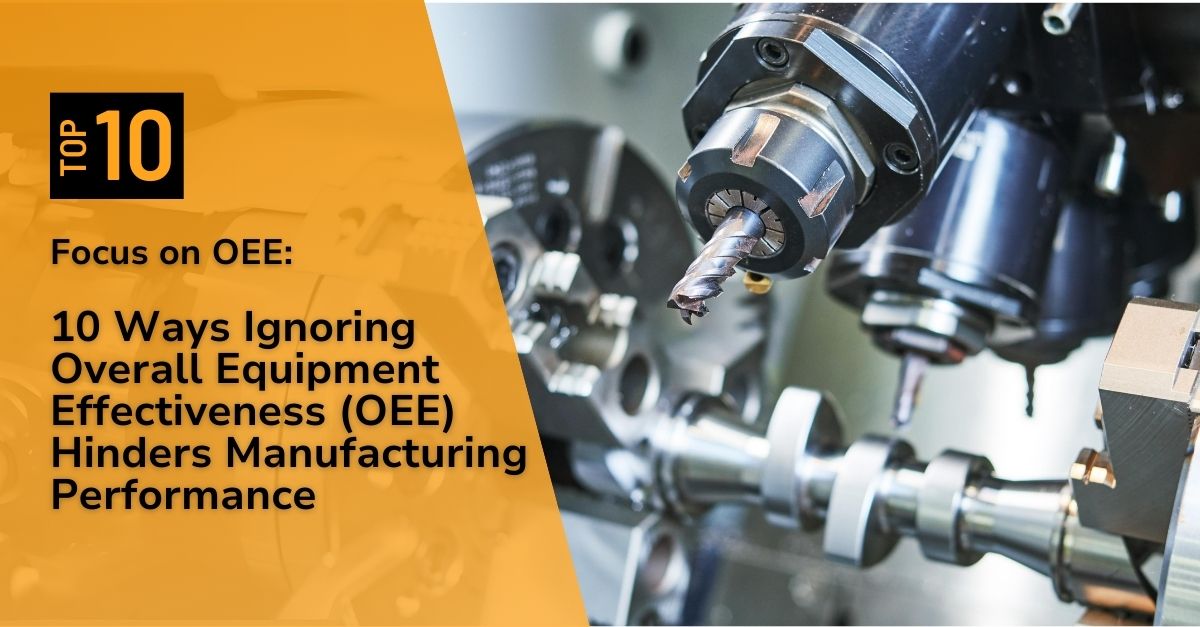
Every second counts in manufacturing. Efficiency, productivity, and profitability are critical. When those things are off course, immediate corrective measures are crucial. That’s why it’s imperative to examine your business using the most revealing diagnostic metric available: OEE
Availability reflects the percentage of time a machine is operational and churning out good products. Performance measures how fast a machine produces compared to its ideal speed. Finally, quality refers to the percentage of good, conforming products a machine produces compared to the total number.
- Availability: The percentage of time a machine is operational and producing good products.
- Performance: How fast a machine produces compared to its ideal speed.
- Quality: The percentage of good, conforming products produced compared to the total number.
A perfect OEE score of 100% signifies a utopian scenario where machines operate flawlessly at full potential, experiencing zero downtime, speed losses, or defects.
Unfortunately, this ideal is rarely achieved in the real world. Studies by Fiix (2023) indicate that the average OEE for many manufacturers hovers around 60%, leaving significant room for improvement. This gap between ideal and reality highlights the substantial performance gains achievable by focusing on OEE.
Ignoring OEE creates a blind spot for manufacturers, hindering their ability to identify and address critical issues that erode profitability. Let’s delve deeper into ten key ways neglecting OEE can hinder, stall, or impede your manufacturing success:
1Hidden Costs:
Without understanding OEE, manufacturers remain blind to the hidden costs associated with downtime, speed losses, and quality defects. These costs can snowball quickly, encompassing lost production time, wasted materials, scrap, rework, and the erosion of customer satisfaction.
2Inefficiency Breeds Inefficiency:
Ignoring OEE fosters a culture of inefficiency. Problems may fester unnoticed and unaddressed, leading to a gradual decline in overall performance. A focus on OEE encourages continuous process improvement, drives a proactive approach to problem-solving, and ensures machines operate at peak efficiency.
3Data-Driven Decisions vs. Flying Blind:
The lack of OEE data forces manufacturers to make decisions based on intuition rather than hard data. This results in poor investment decisions missed opportunities for improvement, and a lack of focus on critical areas. OEE data empowers data-driven decision-making, allowing manufacturers to allocate resources strategically and target areas with the most significant impact on performance.
4Lack of Accountability Undermines Performance:
Without OEE tracking, holding employees or departments accountable for performance is impossible. This leads to low ownership and decreased morale. OEE data fosters a culture of accountability, empowering employees to take ownership of their work and identify areas for improvement. Additionally, it establishes clear performance benchmarks, allowing for targeted training and development initiatives.
5Setting Up for Failure: Unrealistic Production Schedules:
Manufacturers without a clear OEE picture risk setting unrealistic production schedules. This stresses employees, leads to machine breakdowns, and diminishes quality. OEE data provides a realistic understanding of a machine’s capabilities, enabling manufacturers to set achievable production schedules that optimize resource utilization and minimize stress on both machines and employees.
6Customer Dissatisfaction:
Low OEE has a domino effect of negative consequences for customer satisfaction. Production delays lead to missed deadlines, which can strain relationships with clients. Inconsistent product quality further undermines customer trust. Ultimately, unhappy customers take their business elsewhere, impacting a manufacturer’s bottom line.
7Accelerated Equipment Wear and Tear:
Ignoring OEE leads to accelerated wear and tear on your equipment. Operating machinery under suboptimal conditions, neglecting preventive maintenance, and allowing quality defects to persist all contribute to premature equipment failures. This results in higher replacement costs, unplanned downtime, and lost production capacity.
8Competitive Disadvantage:
Companies ignoring OEE face a stark competitive disadvantage. Higher OEE scores directly translate into efficiency gains, allowing competitors to offer lower prices and win market share. Customers in today’s market expect both quality and fast turnaround times, demands that only highly optimized manufacturers with superior OEE can consistently meet.
9Missed Opportunities for Improvement:
OEE data is a treasure trove for streamlining manufacturing processes. Without tracking OEE, manufacturers are blind to the bottlenecks, inefficiencies, and recurring quality problems hindering their operations. OEE analysis reveals these critical pain points, allowing for data-driven decisions that optimize equipment, maintenance, and training for maximum impact on the bottom line.
10Stagnant Innovation:
In manufacturing, continuous improvement fuels innovation. OEE data paves the way by pinpointing areas for enhancing machine performance, reducing downtime, and boosting quality. This targeted approach fosters the development of new, more efficient processes. Companies ignoring OEE lack the flexibility and insights to keep pace with industry trends like automation and Industry 4.0, leaving them stagnant while competitors surge ahead.
Conclusions for Operations Leaders
Overall Equipment Effectiveness (OEE) provides manufacturers with a comprehensive and actionable view of production performance. Ignoring OEE leaves manufacturers vulnerable to hidden costs, inefficiencies, and a general lack of awareness regarding the true causes impacting their bottom line.
Prioritizing and tracking OEE empowers manufacturers to optimize operations, uncover improvement opportunities, and drive sustainable growth.
By embracing OEE as a core performance metric, manufacturers can break free from the cycle of reactive problem-solving and position themselves as leaders in their industry.
Additional Tips for Improving OEE
While OEE can be complex, you can implement several straightforward strategies immediately to see positive results. Here are a few additional tips to help you improve your OEE:
- Robust Preventive Maintenance: Prevent costly breakdowns with a proactive maintenance program. Learn About Our AMP (Advanced Maintenance Performance) Program
- Employee Training: Minimize downtime and defects by thoroughly training employees on proper operating procedures.
- Process Improvement Initiatives: Identify and eliminate bottlenecks to streamline operations.
- Empowerment: Encourage employees to actively identify and report problems.
- Regular Tracking: Consistently track and measure OEE to monitor trends and areas needing improvement.
How POWERS Can Help
POWERS understands the transformative impact of OEE tracking on manufacturing performance. That’s why our software is designed with Capacity Utilization and OEE as its cornerstone dashboard metrics. With POWERS, manufacturers gain:
- Real-Time Visibility: POWERS delivers real-time insights into OEE performance, empowering you to identify issues the moment they arise. This proactive approach minimizes downtime, prevents costly production delays, and safeguards product quality.
- Data-Driven Decision-Making: POWERS transforms OEE data into actionable recommendations guiding resource allocation, equipment upgrades, and process optimization, allowing you to drive tangible improvements.
- Accountability and Ownership: Transparent OEE tracking with POWERS fosters a culture of accountability and continuous improvement. Employees become empowered to identify bottlenecks, troubleshoot problems, and propose innovative solutions.
- Competitive Edge: POWERS gives you the tools to drive efficiency and outpace competitors. As your OEE scores climb, so do your operational efficiency, customer satisfaction, and, ultimately, profitability.
- Call: +1 678-971-4711
- Email: info@thepowerscompany.com
- Form: Request Assesment
Don’t wait. Start your journey to operational excellence and achieve peak overall equipment effectiveness with POWERS.
Continue Reading from this Mastery Series
- Part 1 – The Hidden Costs Undermining Your OEE Score
- Part 2 - Dig Deep to Eliminate Inefficiencies that Silently Sabotage Your OEE
- Part 3 – How Guesswork Kills OEE
- Part 4 – When Nobody Takes Ownership OEE Suffers
- Part 5 – When “Pushing Production” Costs You OEE Points
- Part 6 – The Customer Connection: When Dissatisfaction Drains Your OEE
- Part 7 – Death by a Thousand Cuts: How Wear and Tear Steals From Your OEE
- Part 8 – Competitive Disadvantage: The Hidden Enemy of OEE Excellence
- Part 9 – How Missed Opportunities for Improvement Means Missed OEE Potential
- Part 10 – Is Stagnant Innovation Stagnating Your OEE Results