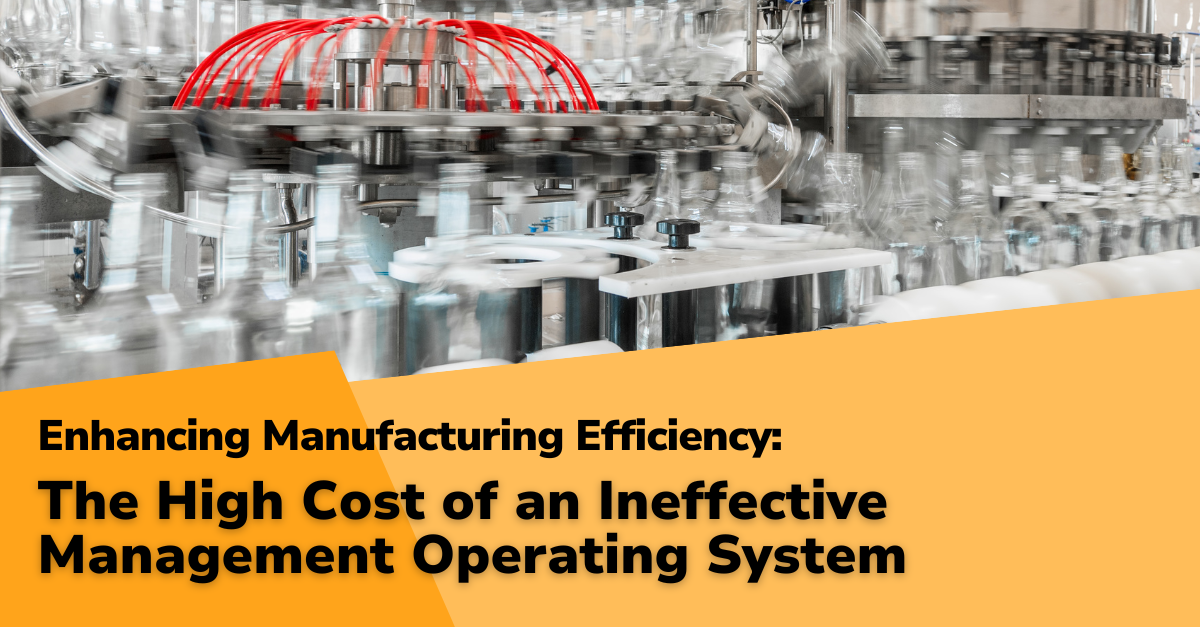
Manufacturing efficiency is complex and multifaceted, with various elements contributing to the overall success of a production operation. The Management Operating System (MOS) is a pivotal yet sometimes underestimated component.
Part four of our “Enhancing Manufacturing Efficiency” series delves into the critical impact an ineffective or absent MOS has on manufacturing costs, a concern of paramount importance to operations executives and stakeholders.
In the preceding parts of this series, we explored diverse aspects of manufacturing processes and the intricacies of managing efficiency, productivity, and quality issues. This installment builds on that foundation, highlighting how deficiencies in the MOS contribute to inflated costs in manufacturing. We dissect the top 10 ways a poorly implemented MOS can lead to increased costs, ranging from heightened material and labor costs to the subtler, equally significant impacts on energy consumption and brand reputation.
This analysis is crucial, especially in an era where manufacturing competitiveness is not just about product quality but also operational agility and cost-effectiveness. With global markets becoming increasingly competitive and margins thinning, the role of an efficient MOS in controlling and reducing costs cannot be overstated. By understanding these challenges, executives and stakeholders can better navigate the complex landscape of manufacturing efficiency, identifying critical areas for improvement and investment.
The insights provided here are backed by industry studies and our real-world experiences, illustrating the tangible effects of MOS inefficiencies. These insights serve as a cautionary tale and a roadmap for those seeking to optimize their manufacturing operations. This comprehensive analysis aims to equip decision-makers with the knowledge and tools to transform their MOS into a cornerstone of efficiency and profitability.
1Increased Material Costs
A deficient MOS often leads to inventory mismanagement, resulting in either excess stock, which ties up capital and storage space, or stockouts, causing production delays. Studies indicate that effective inventory management can reduce costs by up to 25%.
2Elevated Labor Costs
Without a well-implemented MOS, companies can experience low productivity due to inefficient workflows and overstaffing. Labor costs can account for as much as 70% of total business costs, making cost control in this area critical.
3Higher Energy Costs
Inefficient use of machinery and prolonged operational hours due to a poor MOS can substantially increase energy consumption. The U.S. Department of Energy suggests that optimized operations can reduce energy costs by 20%.
4Increased Rework and Wastage:
Poor quality control, a common consequence of an ineffective MOS, can lead to higher rates of defective products, necessitating rework or resulting in waste. This can increase production costs by up to 15-20%.
5Extended Machine Downtime
Inefficient maintenance planning, often seen with inadequate MOS systems, results in more extended machine downtimes, disrupting production schedules and inflating costs. Effective maintenance can reduce downtime by 30-50%.
6Inflated Overhead Costs
Lack of coordination due to a poorly implemented MOS leads to redundant tasks and higher overhead costs. Studies show that process optimization can reduce these costs by up to 25%.
7Supply Chain Disruptions
Weak integration with the supply chain under an ineffective MOS can cause delays and disruptions, leading to expedited shipping costs and loss of customer trust. Efficient supply chain management can reduce costs by up to 15%.
8Lost Sales and Market Share
The inability to meet customer demand promptly due to operational inefficiencies can result in lost sales and reduced market share. A streamlined MOS can improve order fulfillment rates by up to 20%.
9Increased Regulatory Non-Compliance Costs
Failing to comply with industry regulations, a risk in an inadequate MOS, can lead to significant fines and legal costs. Compliance management can save millions in potential fines and legal fees.
10Damaged Brand Reputation
Ongoing product failures and delivery delays erode customer trust and loyalty, impacting long-term profitability. An effective MOS can help build a solid bedrock of brand reputation and customer retention.
Conclusions for Manufacturing Operations Leaders
The impact of an ineffective or absent Management Operating System (MOS) extends far beyond mere operational glitches. As we have explored in this series, it can lead to a substantial escalation in various operational costs, from direct expenses like material and labor costs to indirect yet significant impacts on energy efficiency, regulatory compliance, and brand reputation. In today’s highly competitive and margin-sensitive manufacturing sector, the ability to control and optimize these costs is not just an operational necessity but a strategic imperative.
An effective MOS is the backbone of manufacturing efficiency, integrating various processes and ensuring they operate in harmony. It’s a linchpin for achieving not only cost-effectiveness but also operational excellence.
Companies that recognize and address the inefficiencies in their MOS can unlock significant potential for cost savings, improved productivity, and enhanced market competitiveness.
The journey towards an optimized MOS involves continuous improvement and adaptation, keeping pace with evolving industry trends and technologies.
We encourage operations executives and stakeholders to take a proactive approach to assessing their current MOS. Conduct a thorough analysis to identify areas for improvement and consider the insights provided in this series as a starting point. Remember, the journey towards manufacturing efficiency is ongoing, and pursuing an effective MOS is a critical step.
Unlock the Full Potential with POWERS
Embrace the full potential of a robust Management Operating System with POWERS. Set your manufacturing operations toward unparalleled operational excellence and transform your challenges into strategic advantages. Start your transformative journey today with expert guidance and customized solutions tailored to your unique operational needs.
Contact our team for detailed insights, personalized strategies, and a partnership focused on your long-term success in the dynamic manufacturing landscape. Reach out to us at +1 678-971-4711 or send an email to info@thepowerscompany.com.
Continue Reading from this Mastery Series
- Part 1 - Identifying Key Inefficiencies in the Absence of a Management Operating System
- Part 2 - Top 10 Pitfalls: Lack of an MOS Derails Productivity
- Part 3 - Top 10 Quality Issues at Risk Without a Robust Management Operating System
- Part 4 - The High Cost of an Ineffective Management Operating System
- Part 5 - Without an Optimized Management Operating System, Decision-Making is Severely Impaired
- Part 6 - Scaling Challenges of an Inadequate Management Operating System
- Part 7 - The High Price of Low Engagement: Unpacking the Operational Impact of Employee Discontent
- Part 8 - Safeguarding Success: Decoding the Impact of Compliance and Safety Issues
- Part 9 - Examining the Cost of a Slow Response to Market Shifts
- Part 10 - Charting Success: Understanding the Costs of Losing Competitive Advantage