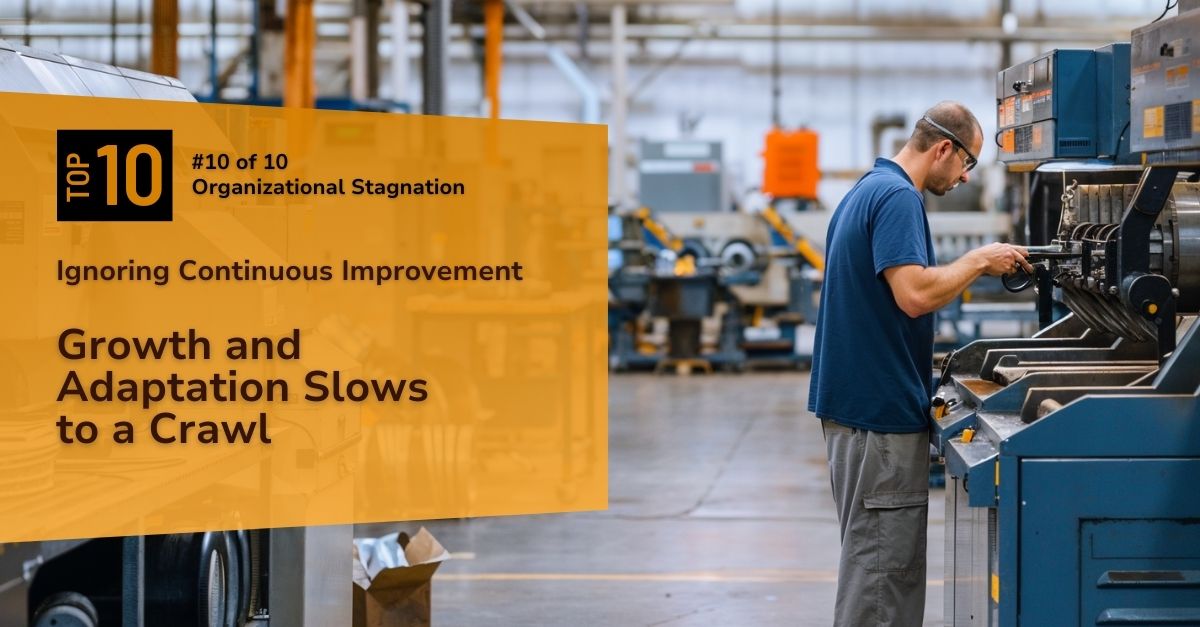
Neglecting continuous improvement can lead to a dangerous state of organizational stagnation, where growth and adaptation slow to a crawl.
As operations settle into old habits and outdated processes, the ability to compete in a dynamic market environment diminishes, leading to a gradual decline in productivity, efficiency, and innovation.
For example, consider a manufacturing plant that has ignored continuous improvement in its maintenance protocols. Over time, machinery begins to operate at less than optimal efficiency due to overlooked wear and tear. Initially, this might cause minor delays or increased energy consumption—issues often dismissed as part of the normal operational challenges. However, as these inefficiencies compound, they impact the entire production line. Output decreases while costs rise as machines break down more frequently and require extensive repairs. The plant’s capacity to meet production targets diminishes, and customer satisfaction wanes as delivery times extend. This seemingly minor neglect can snowball into a significant barrier to achieving organizational goals.
This example highlights a less obvious secondary symptom of organizational stagnation: the incremental deterioration of core operational assets like machinery. When the focus on continuous improvement is lost, the long-term health of essential equipment and processes is compromised, leading to costly inefficiencies that are difficult to reverse. In a competitive manufacturing landscape, these inefficiencies can be the difference between leading the market and falling behind competitors who are quicker to innovate and adapt.
1Incremental Build-Up of Waste and Inefficiencies:
When continuous improvement initiatives are sidelined, waste and inefficiencies gradually accumulate within processes. This build-up is often so subtle that it goes unnoticed until it significantly impacts operations. Over time, these inefficiencies can lead to increased costs, longer lead times, and a decline in overall productivity. Managers may find themselves firefighting daily issues rather than focusing on strategic growth, as inefficiencies manifest as production and resource allocation bottlenecks.
Mitigation: Organizations should regularly review and refine their processes through lean practices like Kaizen or Six Sigma to combat this. By systematically identifying and eliminating waste, managers can ensure that operations remain streamlined and efficient. Encouraging a continuous feedback and improvement culture can also help spot inefficiencies early before they become entrenched problems.
2Diminishing Return on Investment in New Projects:
Without continuous improvement, the effectiveness of new projects tends to decline over time. Initial enthusiasm wanes as old problems resurface and the expected return on investment diminishes. This is particularly true for capital-intensive projects where the lack of iterative refinement can lead to suboptimal outcomes. Managers may observe that projects fail to deliver anticipated productivity gains or cost savings despite significant investments.
Mitigation: Organizations should embed continuous improvement cycles into the lifecycle of every project. Regular assessments and adjustments based on real-time data can help maintain project momentum and ensure that investments continue to yield returns. Implementing post-project reviews that focus on lessons learned and areas for improvement can also prevent stagnation.
3Fragmentation of Data and Information Flow:
Organizational stagnation often results in fragmented data and information flow. When continuous improvement is ignored, there’s a lack of coordination in how information is shared and utilized across departments. This fragmentation can lead to decision-making based on incomplete or outdated information, causing delays, errors, and a general lack of alignment with organizational goals.
Mitigation: To address this, companies should focus on integrating their information systems and ensuring that data flows seamlessly across all departments. Implementing a centralized data management system and fostering a culture of transparency can help improve the accuracy and timeliness of information. Continuous improvement initiatives should also focus on enhancing communication channels and ensuring that data is leveraged effectively in decision-making.
4Reduced Agility in Response to Market Changes:
In a dynamic market, the ability to pivot quickly in response to changes is crucial. However, organizations that neglect continuous improvement often find themselves slow to react. This reduced agility can be detrimental, especially in industries where market conditions fluctuate rapidly. Managers may struggle with outdated processes and rigid structures that hinder their ability to implement necessary changes swiftly.
Mitigation: Organizations should adopt a continuous improvement framework emphasizing flexibility and adaptability to enhance agility. Regularly reviewing market trends and adjusting operations can align the organization with external changes. Empowering teams to make decisions quickly and providing them with the tools to adapt can also significantly improve responsiveness.
5Reduced Capacity to Manage Complexity in Operations:
As organizations grow, their operations naturally become more complex. Without continuous improvement, managing this complexity becomes increasingly challenging. Processes that once worked well may no longer be sufficient, leading to inefficiencies and increased strain on resources. Managers often find themselves overwhelmed by the sheer volume of tasks and the interconnectedness of various processes.
Mitigation: Continuous improvement practices like process mapping and root cause analysis can help organizations manage complexity more effectively. By breaking down complex operations into manageable components and systematically improving each, managers can regain control and ensure that operations remain efficient. Regular training and development programs can also equip teams with the skills to handle increasing complexity.
6Diminished Organizational Resilience to Economic Downturns:
Organizations that neglect continuous improvement are often less resilient during economic downturns. Without a culture of ongoing improvement, they may lack the efficiency and adaptability needed to weather tough times. This diminished resilience can result in deeper cuts, loss of key talent, and a prolonged recovery. Managers may find themselves unprepared for the financial pressures of a downturn, leading to rushed and often ineffective decisions.
Mitigation: Building resilience through continuous improvement involves regularly assessing and optimizing operations to ensure they are lean and adaptable. Scenario planning and stress testing can help organizations prepare for potential downturns. Organizations can better withstand economic challenges and emerge stronger by focusing on efficiency and adaptability.
7Slow Adoption of Best Practices Across the Organization:
Adopting best practices can be painfully slow in organizations where continuous improvement is neglected. This reluctance to change can stem from entrenched habits, fear of disruption, or a lack of awareness of new methods. As a result, productivity suffers as teams continue to operate with outdated practices that no longer align with industry standards.
Mitigation: To accelerate the adoption of best practices, organizations should foster a culture of learning and improvement. Regular training sessions, cross-functional teams, and knowledge-sharing platforms can help spread best practices more quickly. Additionally, leadership should actively champion these practices, setting an example and encouraging their adoption throughout the organization.
8Erosion of Cross-Functional Collaboration:
Cross-functional collaboration is critical for innovation and efficiency. However, when continuous improvement is sidelined, collaboration across departments often deteriorates. Silos form, communication breaks down, and teams become isolated, leading to missed opportunities and inefficiencies. Managers may notice that projects stall due to a lack of coordination and shared goals.
Mitigation: To rebuild cross-functional collaboration, organizations should prioritize continuous improvement initiativesencouraginge teamwork and communication. Structured collaboration tools and regular cross-departmental meetings can help break down silos. Encouraging joint problem-solving and recognizing collaborative achievements can foster a more integrated and cooperative work environment.
9Widening Gap Between Organizational Goals and Outcomes:
Neglecting continuous improvement can create a significant gap between what an organization aims and accomplishes. This gap often results from misaligned processes, outdated strategies, and a lack of ongoing assessment and adjustment. Managers may struggle to understand why their efforts aren’t translating into the expected results, leading to frustration and decreased morale.
Mitigation: Continuous improvement practices like regular goal-setting and performance reviews can help close the gap between goals and outcomes. Companies can ensure that their efforts are effective by continually refining strategies and aligning processes with organizational objectives. Involving employees in goal-setting and providing them with the resources to succeed can also improve alignment and motivation.
10Slow Response to Industry Trends:
The failure to keep up with industry trends is a common consequence of ignoring continuous improvement as competitors adopt new technologies, methodologies, and practices. Organizations that remain stagnant risk falling behind. This slow response can lead to a loss of competitive advantage and a declining market share. Managers may find themselves scrambling to catch up, often at a higher cost and with less effectiveness.
Mitigation: Organizations should integrate continuous improvement into their strategic planning to stay ahead of industry trends. Regularly monitoring industry developments and investing in innovation can help maintain a competitive edge. Encouraging a forward-thinking mindset and providing teams with the tools and training to implement new trends can also ensure that the organization remains agile and competitive.
Conclusions for Operations Leaders
Organizational stagnation is not just a hindrance to growth—it’s a threat to the very survival of a manufacturing business in today’s fast-paced, competitive market. When continuous improvement is neglected, the resulting inefficiencies, outdated processes, and slow adaptation to change can cripple productivity and erode the company’s ability to innovate.
We work directly with your leadership team to identify and address the root causes of safety issues, implementing strategies that prevent accidents and enhance overall operational efficiency.
POWERS Can Help You:
POWERS specializes in helping manufacturing organizations overcome the challenges of stagnation by embedding continuous improvement into the fabric of their operations. Our approach is hands-on, data-driven, and tailored to each client’s unique needs. We don’t just identify the problems—we work alongside your team to implement sustainable solutions that drive measurable results.
POWERS specializes in embedding continuous improvement into manufacturing operations to combat organizational stagnation. By partnering with us, you can expect:
- Streamlined Operations: We help eliminate inefficiencies and optimize processes, ensuring your operations run smoothly and efficiently.
- Enhanced Agility and Resilience:We equip your organization with the tools and practices to quickly adapt to market changes and withstand economic downturns.
- Effective Data Integration: We ensure seamless data flow across your organization, enabling informed decision-making and alignment with strategic goals.
- Proactive Innovation: We help you stay ahead of industry trends and adopt best practices quickly, maintaining your competitive edge.
At POWERS, we understand the unique challenges that manufacturing organizations face and are here to help you overcome them. Don’t let organizational stagnation hold you back—partner with us to unlock the full potential of your operations and drive sustainable growth.
- Speak to an Expert: Call +1 678-971-4711 to discuss your specific challenges and goals.
- Email Us: Get tailored insights by emailing info@thepowerscompany.com
- Request an Assessment: Use our online contact form, and one of our expert manufacturing consultants will reach out to schedule an in-depth analysis of your operations.
Continue Reading from this Mastery Series
- Part 1 – When Progress Takes a Break, it Leaves Your Productivity Stalled
- Part 2 – Profit Erosion in the Production Line
- Part 3 – Quality Takes a Dive and Productivity Pays the Price
- Part 4 – When Morale Breaks Down So Does the Shop Floor
- Part 5 – When Innovation Pauses, Your Production Line Follows
- Part 6 – How Customer Loyalty Slips Through Your Fingers
- Part 7 – When Your Slice of the Market Becomes a Crumb
- Part 8 – When Opportunities Slip Through the Cracks
- Part 9 – Safety Shortsights and Their Costly Consequences
- Part 10 – Growth and Adaptation Slows to a Crawl