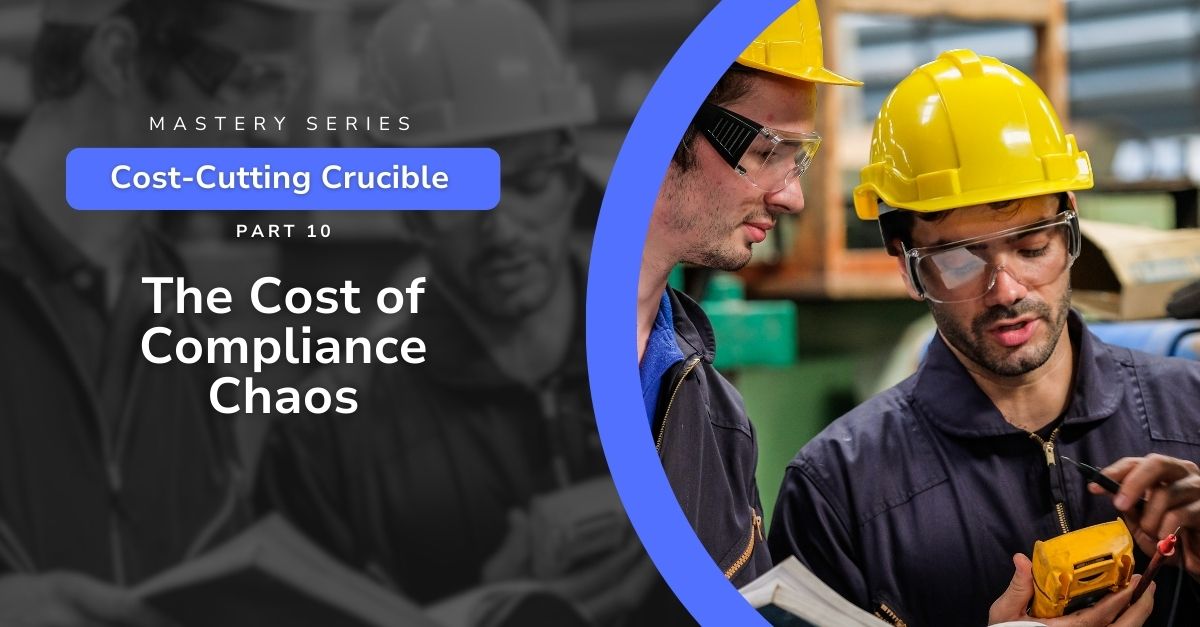
Regulatory compliance is a critical component of any manufacturing operation.
These drains don’t always take the form of fines or legal penalties. Instead, they manifest in secondary symptoms that quietly erode operational efficiency and financial performance over time.
Consider a less common example: the inability to efficiently track and document compliance data can lead to inconsistent supplier audits. This inconsistency increases the risk of quality issues, such as subpar raw materials entering the production line. In turn, the manufacturer faces increased rework costs and potential delays in fulfilling customer orders. The lack of a unified compliance system creates a chain of inefficiencies, turning what should be a simple regulatory requirement into a significant financial burden.
The consequences of fragmented compliance management often go unnoticed because they’re embedded in everyday operations—frequent production interruptions, missed opportunities for process improvements, and overreliance on a few key individuals for regulatory expertise. While not immediately obvious, these challenges act as hidden profit leaks that weaken competitiveness and hinder long-term growth.
In this, the last part of the Cost-Cutting Crucible Mastery Series, we’ll explore how expensive compliance costs stemming from fragmented regulatory management create these overlooked drains on profit. By addressing these secondary symptoms, manufacturers can regain control of their compliance processes and uncover opportunities to strengthen their financial performance and operational efficiency.
1Frequent Interruptions in Production to Address Compliance Violations:
Production halts are one of the most visible symptoms of fragmented compliance management. These interruptions often occur when compliance violations are discovered through audits, customer complaints, or internal reviews. Each halt creates a ripple effect: delayed orders, strained labor resources, and wasted materials. For example, if a product batch fails quality testing due to regulatory oversight, the time and cost of reworking or scrapping it significantly increase operational costs.
Migration: Adopt a preventive approach to compliance by embedding monitoring systems into daily production workflows. Tools like real-time compliance tracking software can identify issues as they arise, allowing immediate correction without disrupting the entire process. Training employees to recognize potential violations and escalate them before they impact production ensures smoother operations and fewer costly stoppages.
2Reduced Capacity to Apply for Compliance-Based Cost Incentives:
Many governments and industry organizations offer incentives for compliance certifications, energy efficiency programs, or sustainability initiatives. However, due to disorganized compliance records, manufacturers often fail to capitalize on these opportunities. Without accurate documentation or an efficient way to track incentive opportunities, organizations miss out on potentially lucrative benefits. For instance, failing to demonstrate adherence to environmental standards could disqualify a company from tax breaks or grants.
Migration: Centralize compliance documentation into a single, easily accessible platform. By digitizing records and automating updates, manufacturers can ensure eligibility for incentives. Designate a compliance officer or team to monitor and apply for relevant opportunities, ensuring deadlines and criteria are consistently met. Regular audits of compliance data can further highlight areas where the organization qualifies for cost-saving programs.
3Missed Opportunities to Streamline Compliance with Lean Principles:
When compliance processes operate in isolation from production systems, they create inefficiencies that conflict with lean manufacturing goals. Redundant checks, excessive documentation, and siloed workflows waste resources and increase compliance-related expenses. For instance, separate quality inspections for regulatory adherence and internal standards could be consolidated into a single streamlined process.
Migration: Integrate compliance management into lean manufacturing practices by mapping regulatory workflows and eliminating redundancies. Lean tools like Value Stream Mapping (VSM) can identify waste in compliance processes, enabling the organization to optimize without compromising standards. Collaborative workshops with cross-departmental teams can further enhance alignment and efficiency.
4Overdependence on a Few Employees for Compliance Expertise:
Relying heavily on a small group of employees for compliance knowledge creates vulnerabilities. Compliance efforts stall when these individuals are unavailable due to turnover, absences, or burnout. This bottleneck slows response times, increases error rates, and puts the organization at risk of noncompliance. Moreover, this over-dependence can lead to dissatisfaction among compliance staff, exacerbating retention challenges.
Migration: Develop cross-functional training programs to distribute compliance expertise. Use a knowledge-sharing platform to document critical compliance procedures, ensuring team accessibility. Succession planning and mentoring programs can further ensure that expertise is retained and transferred, reducing reliance on individuals.
5Inconsistent Interpretation of Quality Regulations Across Departments:
Regulations are often complex and subject to interpretation, especially involving multiple jurisdictions or overlapping standards. Inconsistent understanding across departments can lead to misaligned practices, rework, and noncompliance. For instance, one department might interpret a regulation more stringently than another, creating conflicting workflows that waste time and resources.
Migration: Establish a centralized compliance governance team to standardize interpretations and ensure uniform regulation application. Regular training sessions and workshops can reinforce these standards across departments. Additionally, using compliance management software with built-in guidance for specific regulations can help ensure consistency.
6Longer Resolution Times for Flagged Compliance Violations:
Resolving violations becomes a time-consuming process when compliance data is scattered across departments or facilities. This lack of centralized data slows investigations, prolongs production delays, and increases administrative costs. For example, locating documentation to address a flagged issue during an audit can take days or even weeks, compounding the violation’s impact.
Migration: Implement an integrated compliance management platform that consolidates regulatory data into a single source of truth. This system should offer real-time tracking, role-based access, and automated workflows to streamline resolution processes. Cross-functional compliance response teams can also be established to accelerate decision-making and corrective actions.
7Higher Turnover Rates Among Compliance-Focused Roles:
Compliance roles are often high-pressure positions that involve navigating complex regulations and tight deadlines. When compounded by inefficient systems and fragmented processes, these roles become even more challenging, leading to higher turnover rates. Each departure results in recruitment costs, knowledge loss, and operational disruptions.
Migration: Support compliance teams with modern tools and processes that reduce their workload and improve job satisfaction. Automating routine tasks, such as report generation and document updates, allows employees to focus on higher-value activities. Career development opportunities like certifications or advanced training can also improve retention rates.
8Difficulty Consolidating Regulatory Data Across Multiple Facilities:
Managing compliance data becomes exponentially more complex for manufacturers, with operations across multiple locations. Inconsistent data collection methods and disparate systems make tracking compliance at an organizational level difficult. This lack of visibility increases the likelihood of missed requirements and duplicative efforts.
Migration: Adopting a cloud-based compliance management system provides a unified view of regulatory performance across all facilities. Standardizing data collection methods and using dashboards to monitor key metrics can simplify consolidation efforts. Regular inter-facility audits can also help identify and resolve inconsistencies.
9Missed Deadlines for Mandatory Reporting Submissions:
Regulatory agencies require timely submissions of reports, such as environmental impact statements or safety audits. Missing these deadlines due to disorganized processes or poor tracking can result in fines, penalties, and reputational damage. These lapses can jeopardize licensing or certifications in industries with strict compliance requirements, such as food or pharmaceuticals.
Migration: Automate reporting schedules using compliance software that includes deadline reminders and pre-built templates. Assign a dedicated compliance coordinator to oversee submissions and ensure accountability. Regularly review upcoming reporting requirements to prevent last-minute scrambling.
10Limited Integration of Compliance Data with Production Analytics:
Siloed compliance data limits the organization’s ability to identify patterns and implement preventive measures. Manufacturers miss opportunities to enhance efficiency and reduce costs without integrating compliance metrics into production analytics. For example, tracking compliance-related downtime alongside production data could reveal underlying issues that require attention.
Migration: Integrate compliance data into existing analytics platforms to view operations comprehensively. Use predictive analytics to identify trends and anticipate compliance risks before they occur. Collaboration between compliance and operations teams can further ensure alignment and actionable insights.
Conclusions for Operations Leaders
Fragmented regulatory management is one of the hidden challenges that silently drains manufacturing profitability. While the direct costs of compliance, such as fines and penalties, may be obvious, the secondary symptoms—frequent interruptions, inefficiencies, and missed opportunities—can have an even greater impact on productivity and financial performance.
How POWERS Can Help
At POWERS, we specialize in uncovering and addressing hidden profit leaks that hinder manufacturing performance. Our proven strategies and tools empower manufacturers to take control of their operations, streamline processes, and achieve measurable results.
With the Digital Production System (DPS), POWERS offers a transformative solution designed to optimize compliance and improve productivity. DPS leverages AI-powered insights and real-time data to help manufacturers navigate regulatory complexities and turn compliance from a challenge into a strategic advantage.
Here’s how POWERS and DPS can help you boost productivity while managing compliance effectively:
- Enhanced Visibility: With intuitive dashboards that highlight actionable opportunities, you can gain real-time insights into compliance metrics, production performance, and potential risks.
- Predictive Insights for Production Risks: Use advanced analytics to anticipate compliance challenges before they disrupt your operations, enabling preventive actions that minimize downtime and costs.
- Operational Efficiency: Align compliance management with lean principles, eliminating waste and improving the efficiency of regulatory processes across all facilities.
- Sustainable Improvement: Foster a culture of accountability and collaboration through continuous improvement initiatives supported by DPS’s cutting-edge technology.
By combining decades of manufacturing expertise with AI-powered tools, POWERS ensures your compliance processes meet regulatory requirements and drive long-term profitability and growth.
Ready to take the next step? Let’s transform your approach to compliance and uncover opportunities to strengthen your operations. Contact us today to learn how POWERS and DPS can help you thrive in the competitive manufacturing landscape.
- Speak to an Expert: Call +1 678-971-4711 to discuss your specific challenges and goals.
- Email Us: Get tailored insights by emailing info@thepowerscompany.com
- Request an Assessment: Use our online contact form, and one of our expert manufacturing consultants will reach out to schedule an in-depth analysis of your operations.
Continue Reading from this Mastery Series
- Part 1 – How Poor Scheduling Burns Through Your Profit Margins
- Part 2 – How Hidden Energy Wastes Burn Through Your Bottom Line
- Part 3 – How Dead Weight in Your Safety Stock Undermines Your Bottom Line
- Part 4 – The Hidden Costs of Ignoring Preventive Maintenance Programs
- Part 5 – Mismatched Skills and Wasted Workforce Potential
- Part 6 – Poor Quality Control is Dragging Down Your Productivity and Profits
- Part 7 – Being Slow to Market Undermines Your Bottom Line
- Part 8 – Supplier Missteps That Drain Profitability
- Part 9 – The Cost of Continuing to Use Manual Processes
- Part 10 – The Financial Fallout of Fragmented Compliance