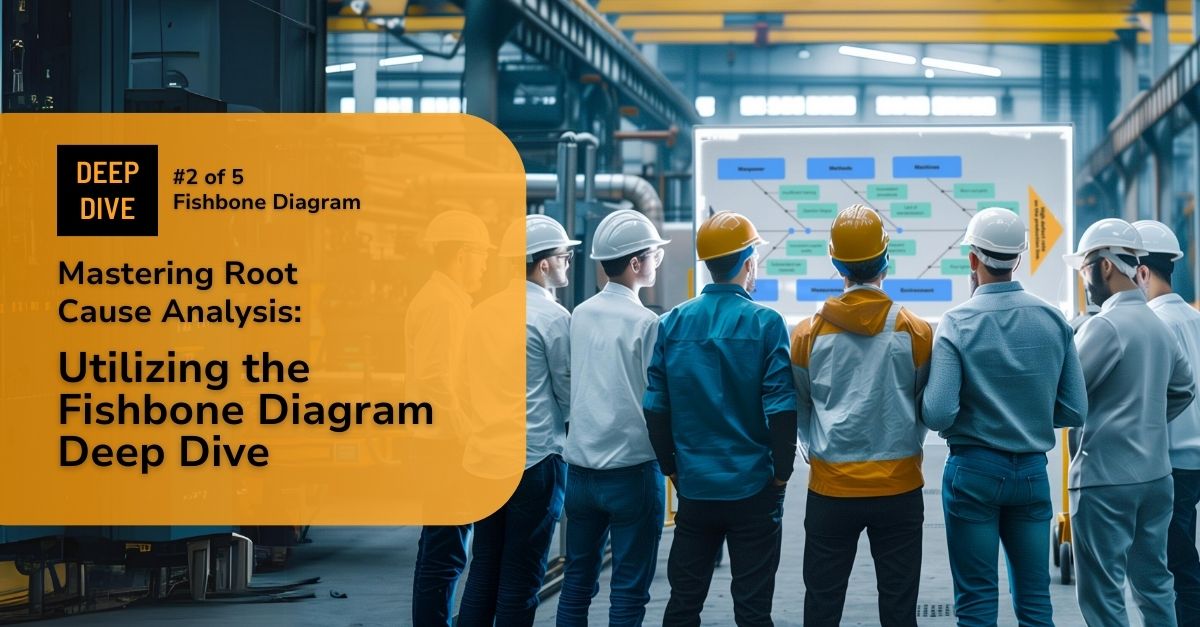
Root cause analysis (RCA) is a critical practice in the manufacturing industry, helping organizations identify, address, and prevent problems that impact productivity and quality.
One of the most effective tools for this purpose is the Fishbone Diagram, also known as the Ishikawa Diagram or Cause-and-Effect Diagram. This visual tool systematically identifies and presents all possible causes of a problem, categorizing them into significant groups to provide a structured approach to pinpointing root causes. This post will delve into the intricacies of the Fishbone Diagram, its benefits, the steps to create one, and practical examples to illustrate its application in the manufacturing sector.
What is a Fishbone Diagram?
A Fishbone Diagram is a visual tool used to identify, explore, and display all potential causes of a specific problem. It was developed by Dr. Kaoru Ishikawa, a pioneer in quality management, to aid in diagnosing the root causes of issues. The diagram’s structure resembles the skeleton of a fish, with the problem at the “head” and potential causes branching out as “bones,” making it a clear and intuitive tool for analysis.
The diagram typically includes the problem statement at the head and several major categories branching out, each containing possible causes related to that category.
This structure helps teams systematically explore all aspects of a problem,
ensuring a thorough analysis.
Benefits of Using Fishbone Diagrams in Manufacturing
Utilizing Fishbone Diagrams in manufacturing offers several advantages:
- Systematic Identification: It helps systematically identify potential causes, ensuring no aspect is overlooked. This comprehensive approach leads to more effective solutions by addressing the root causes instead of just the symptoms.
- Structured Approach: The diagram's structured format promotes a logical and organized approach to problem-solving. This structure is instrumental in complex manufacturing environments where multiple factors can contribute to a problem.
- Team Collaboration: It fosters teamwork and brainstorming, allowing diverse perspectives to contribute to the analysis. Organizations can leverage a wider range of skill sets and experience by involving team members from different departments.
- Focused Analysis: It helps teams focus on specific problem areas, leading to more effective solutions. This focused analysis can improve efficiency and reduce the time needed to identify and address issues.
Major Categories in a Fishbone Diagram
In manufacturing, the standard categories for a Fishbone Diagram typically include:
- Manpower: Human-related factors such as skills, training, and behavior. These factors can significantly impact production quality and efficiency.
- Methods: Processes, procedures, and ways of working. Ineffective or inconsistent methods can lead to variability in production outcomes.
- Machines: Equipment, tools, and technology. Equipment failures or inefficiencies can be a major source of production problems.
- Materials: Raw materials, components, and supplies. The quality and consistency of materials used in production can affect the final product quality.
- Measurements: Data, metrics, and measurement systems. Accurate and reliable measurement systems are essential for monitoring and controlling production processes.
- Environment: Physical conditions, workplace layout, and environmental factors. Environmental conditions like temperature, humidity, and lighting can influence production processes and product quality.
Steps to Create a Fishbone Diagram
1Identify the Problem
Clearly define the issue or problem to be analyzed. For example, “High defect rate in a production line.” It’s essential to have a specific and well-defined problem statement to ensure the analysis is focused and effective.
2Assemble the Team
Gather a cross-functional team with diverse expertise, emphasizing the importance of collaboration and open communication. Include team members from various departments such as production, quality control, maintenance, and supply chain to ensure a comprehensive analysis.
3Draw the Backbone
Create the main “fishbone” structure with the problem statement at the head. This backbone will serve as the foundation for the analysis, with major categories branching out from it.
4Identify Major Categories
Determine the main categories relevant to the problem. Use standard manufacturing categories or customize them as needed. The choice of categories should reflect the specific context and nature of the problem being analyzed.
5Brainstorm Potential Causes
Generate potential causes for each category through team brainstorming, encouraging open and non-judgmental discussion. Use techniques such as round-robin brainstorming or nominal group technique to ensure all team members contribute ideas.
6Populate the Diagram
Add the potential causes to the diagram under the appropriate categories, using sub-branches for more detailed causes. This step involves organizing and structuring the brainstormed causes in a clear and logical manner.
7Analyze and Prioritize Causes
Evaluate the listed causes to identify the most likely root causes. Use additional tools like the 5 Whys technique to drill down further. Prioritize the causes based on their impact and likelihood, focusing on the most significant ones for further investigation.
Practical Example in Manufacturing
Consider a real-life example: Analyzing high defect rates in a production line.
Problem Identification and Team Assembly
Problem: “High defect rate in the widget production line.”
Team: Production manager, quality control inspector, machine operator, and maintenance technician. Each team member contributes unique perspectives and expertise to the analysis.
Category Identification and Brainstorming
- Manpower: Insufficient training, operator fatigue. These factors could lead to mistakes and inconsistencies in production.
- Methods: Inconsistent procedures, lack of standardization. Variability in processes can result in inconsistent product quality.
- Machines: Worn-out parts, calibration issues. Equipment problems can directly impact the quality of the produced widgets.
- Materials: Substandard raw materials, inconsistent supplier quality. The quality of materials used can greatly impact the final product.
- Measurements: Inaccurate gauges, infrequent inspections. Reliable measurement systems are essential for maintaining quality control.
- Environment: Poor lighting, high humidity. Environmental conditions can affect both the production process and the workers' performance.
Diagram Creation and Cause Analysis
The team creates the Fishbone Diagram, populating it with the identified causes. They then prioritize the causes and find that inconsistent procedures and substandard raw materials are the primary contributors to the high defect rate. Further investigation reveals specific issues with supplier quality control and the need for process standardization.
An example Fishbone diagram based the scenerio outlined above
Tips for Effective Use of Fishbone Diagrams
- Focus and Diversity: Keep the team focused and encourage diverse viewpoints. A diverse team can provide a more comprehensive analysis by considering various perspectives and expertise.
- Data and Evidence: Use data and evidence to support the identification of causes. Collect and analyze relevant data to validate the identified causes and ensure the analysis is based on factual information.
- Review and Update: Review and update the diagram as new information becomes available. Root cause analysis is a continuous process, and the diagram should be updated as new insights emerge.
- Combine Tools: Combine the Fishbone Diagram with other analysis tools for deeper insights. Techniques such as Pareto analysis, Failure Mode and Effects Analysis (FMEA), and Statistical Process Control (SPC) can complement the Fishbone Diagram and provide additional insights.
Conclusion for Manufacturing Leadership
The Fishbone Diagram is an invaluable tool for root cause analysis in manufacturing, offering a clear, structured approach to identifying and addressing problems. By integrating this tool into regular problem-solving practices, manufacturing teams can enhance productivity, improve quality, and reduce defects. The systematic and collaborative nature of the Fishbone Diagram ensures that all potential causes are considered, leading to more effective and sustainable solutions.
How Powers Can Help
At The Powers Company, we specialize in helping manufacturing organizations improve their operational efficiency and productivity through expert root cause analysis and process improvement strategies. With our extensive experience and proven methodologies, we assist teams in effectively utilizing tools like the Fishbone Diagram to identify and address the root causes of their most pressing challenges.
Our tailored approach ensures that your team gains the insights and skills necessary to drive sustainable improvements and achieve measurable results.
If you’re ready to elevate your problem-solving skills and streamline your manufacturing processes, reach out to us today for professional guidance and support.
- Speak to an Expert: Call +1 678-971-4711 to discuss your specific challenges and goals.
- Email Us: Get tailored insights by emailing info@thepowerscompany.com
- Request an Assessment: Use our online contact form, and one of our productivity experts will reach out to schedule an in-depth analysis of your operations.