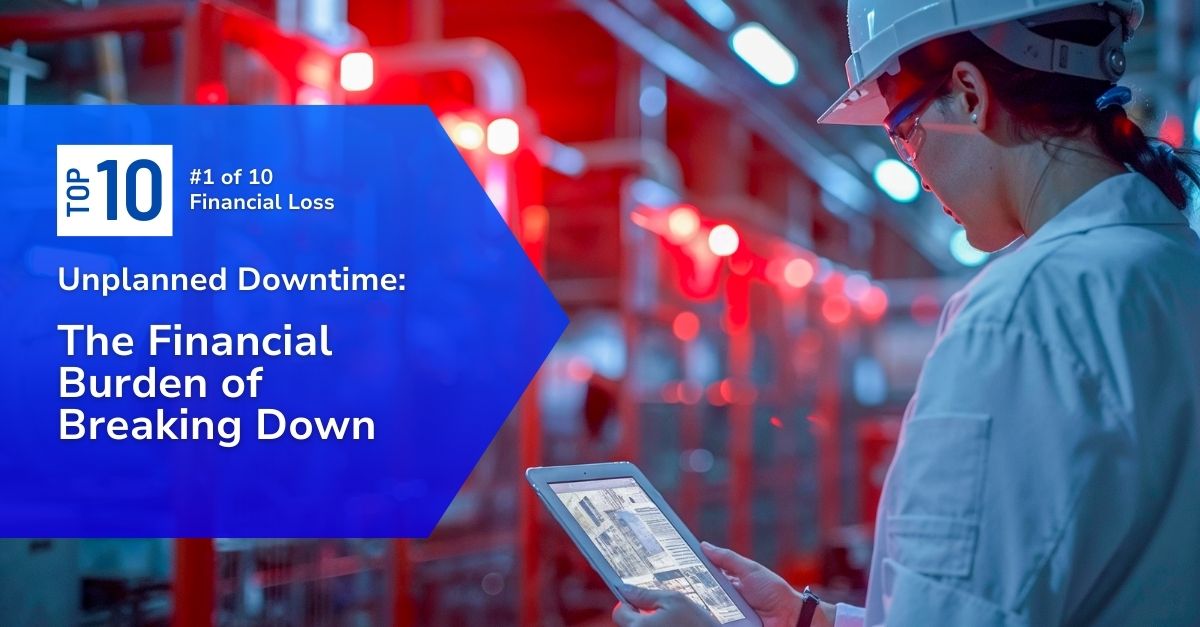
Unplanned downtime in manufacturing is more than just an interruption in production; it triggers a cascade of secondary symptoms that collectively contribute to significant financial loss.
Each minute of unplanned downtime not only halts the production line but also sets off a chain of events that strain resources, inflate costs, and disrupt the intricate balance of the manufacturing process.
Consider the example of unbalanced inventory levels. When a critical piece of equipment fails unexpectedly, it often leads to a misalignment in inventory management. Production schedules are thrown off, resulting in either an overstock of raw materials that can’t be processed or a shortage of finished goods ready for delivery. This imbalance ties up capital in unsold inventory and can force companies to incur additional costs to expedite orders and replenish critical components. More robust preventive maintenance and predictive analytics could have avoided such financial strain.
The top ten ways that unplanned downtime leads to financial loss are nuanced and interconnected, affecting various aspects of the manufacturing process. Each issue, from increased overtime wages to diminished worker productivity, has its own challenges and requires targeted mitigation strategies to manage effectively. By delving into these secondary symptoms, managers can better understand the full scope of unplanned downtime’s financial impact and implement proactive measures to minimize its occurrence and severity.
1Excessive Administrative Costs:
When equipment unexpectedly fails, administrative tasks surge. This includes unplanned meetings, emergency planning sessions, and additional documentation efforts to trace and manage the downtime incident. These tasks divert attention from productive activities, increasing administrative overhead. The cost of reallocating administrative resources and the potential overtime needed to manage these tasks can be substantial.
Mitigation: Implement a robust preventive maintenance schedule and invest in predictive maintenance technologies. This proactive approach minimizes unexpected failures and reduces the administrative burden of reactive planning and reporting. Additionally, a computerized maintenance management system (CMMS) can streamline documentation and scheduling, freeing up administrative resources for more strategic activities.
2Increased Overtime Wages:
Unplanned downtime often results in extended work hours to meet production targets once the equipment is back online. Overtime wages can quickly accumulate, leading to significant financial strain. The need to rush production after a downtime event can also lead to increased errors and accidents, further driving up costs.
Mitigation: Adopt a flexible staffing model that includes cross-training employees. This ensures that available workers can be efficiently redeployed during downtime to other productive tasks, reducing the need for overtime once operations resume. Implementing shift rotations and providing adequate rest periods can help manage fatigue and maintain productivity, even under tight schedules.
3Elevated Maintenance Costs:
Emergency repairs are typically more costly than scheduled maintenance due to the urgency and potential need for expedited parts shipping. This reactive maintenance also interrupts planned maintenance schedules, compounding costs. The lack of preparation for emergency repairs can lead to inefficiencies and increased labor costs as maintenance teams scramble to address issues.
Mitigation: Develop a detailed maintenance management system that prioritizes predictive maintenance. Utilizing data analytics to forecast potential failures allows maintenance to be conducted in a controlled and cost-effective manner. Investing in high-quality, durable parts and establishing long-term contracts with suppliers can also reduce the costs associated with emergency repairs.
4Missed Sales Opportunities:
Unplanned downtime can lead to missed deadlines and unmet production quotas, resulting in missed sales opportunities. This directly impacts revenue and market competitiveness. When orders are delayed or canceled due to downtime, the ripple effects can damage relationships with key clients and disrupt supply chains.
Mitigation: Enhance communication and coordination with the sales team to manage customer expectations proactively. Having a buffer stock of critical products can also mitigate the impact of short-term production halts. Developing solid relationships with customers and being transparent about potential delays can help maintain trust and loyalty even when issues arise.
5Loss of Customer Trust Due to Delays:
Repeated delays caused by unplanned downtime erode customer trust and can lead to lost business. Customers may seek more reliable suppliers, further diminishing revenue. Losing customer trust can also damage the company’s reputation, making it harder to acquire new business and retain existing clients.
Mitigation: Implement a transparent communication strategy with customers, providing regular updates and realistic timelines. Investing in reliability-centered maintenance (RCM) can significantly reduce the frequency of unexpected downtime. Offering compensation or discounts for delayed orders can also help maintain customer satisfaction and loyalty.
6Unplanned Equipment Rentals:
When critical equipment fails, companies may need to rent replacements to maintain production, leading to unexpected rental expenses that can quickly add up. The logistics of securing and integrating rental equipment into existing processes can also be time-consuming and disruptive.
Mitigation: Maintain an inventory of critical spare parts and establish relationships with rental companies to negotiate better rates and terms. Long-term, investing in redundant systems for critical processes can mitigate the need for emergency rentals. Conducting regular audits of equipment performance and reliability can also help identify potential issues before they require rental solutions.
7Emergency Repair Costs:
Emergency repairs often involve premium charges for expedited parts and labor, significantly inflating maintenance budgets. The urgency of these repairs can also lead to rushed decisions and suboptimal solutions, potentially causing further issues down the line.
Mitigation: Create a contingency fund specifically for emergency repairs and invest in comprehensive training for in-house maintenance teams to handle urgent repairs more cost-effectively. Building relationships with suppliers for faster, more cost-effective sourcing of parts can also reduce the financial impact of emergency repairs.
8Unbalanced Inventory Levels:
Downtime can disrupt inventory balance, leading to excess stock of some items and shortages of others. This imbalance ties up capital in unsold inventory and can lead to stockouts of critical components. The resulting inefficiencies can hinder production schedules and affect overall operational effectiveness.
Mitigation: Implement an advanced inventory management system that uses real-time data to adjust inventory levels dynamically. Just-in-time (JIT) inventory practices can also help in maintaining optimal stock levels. Regularly reviewing inventory levels and adjusting procurement strategies based on production forecasts can further prevent imbalances.
9Excessive Expediting Costs:
To recover lost production time, companies may expedite shipping for parts and materials, incurring substantial additional costs. The need for rapid transportation and handling can significantly increase expenses, further straining financial resources.
Mitigation: Plan for contingencies in supply chain management and establish strong relationships with suppliers to negotiate better rates and lead times for expedited orders. Using local suppliers where possible can also reduce the need for expedited shipping. Implementing more efficient production scheduling and planning can help mitigate the impact of unforeseen delays.
10Diminished Worker Productivity:
Frequent unplanned downtime disrupts workflow, leading to idle time and decreased overall worker productivity. The stop-start nature of work during these periods can also diminish employee morale. Over time, this can lead to increased turnover and higher training costs for new employees.
Mitigation: Implement continuous improvement programs like Lean and Six Sigma to streamline processes and reduce downtime occurrences. Engaging employees in these initiatives can also boost morale and productivity by fostering a culture of proactive problem-solving. Providing regular training and development opportunities can further enhance employee engagement and efficiency.
Conclusion
Unplanned downtime in manufacturing is a complex issue with far-reaching financial implications. The top ten secondary symptoms, from excessive administrative costs to diminished worker productivity, highlight the multifaceted nature of the problem. Addressing these issues requires a comprehensive approach that integrates predictive maintenance, advanced inventory management, flexible staffing models, and continuous improvement programs.
Mitigating the financial impact of unplanned downtime not only involves addressing the immediate mechanical failures but also requires a proactive strategy to manage the cascading effects on administration, labor, inventory, and customer relations.
How POWERS Can Help
At POWERS, we specialize in enhancing manufacturing productivity through tailored, results-based operations management consulting. Our unique approach aligns the systems, processes, and behaviors that drive higher productivity and efficiency. We work directly with frontline leadership to implement effective root cause analysis techniques like Fault Tree Analysis (FTA) to identify and address the underlying causes of unplanned downtime.
Our hands-on method ensures sustainable improvements and measurable ROI by focusing on key areas such as:
- Predictive Maintenance: Implementing advanced predictive maintenance technologies to forecast and prevent equipment failures before they occur.
- Inventory Management: Utilizing real-time data analytics to maintain balanced inventory levels and reduce the financial strain of overstock and shortages.
- Staffing Optimization: Developing flexible staffing models and cross-training programs to minimize overtime costs and enhance workforce productivity.
- Continuous Improvement Mindset: Applying our decades of operations experience to streamline processes, reduce downtime occurrences, and foster a culture of proactive problem-solving.
By partnering with POWERS, manufacturers can transform their operational processes, reduce unplanned downtime, and achieve significant productivity improvements.
Our tailored solutions are designed to address the specific challenges faced by your organization, ensuring that you can maintain a competitive edge in the market.
Contact us today to learn how we can help you identify and address your most pressing issues, driving continuous improvement and maximizing your manufacturing efficiency.
- Speak to an Expert: Call +1 678-971-4711 to discuss your specific challenges and goals.
- Email Us: Get tailored insights by emailing info@thepowerscompany.com
- Request an Assessment: Use our online contact form, and one of our expert manufacturing consultants will reach out to schedule an in-depth analysis of your operations.
Continue Reading from this Mastery Series
- Part 1 – The Financial Burden of Breaking Down
- Part 2 – Eroding Maintenence Leading to Eroding Margins
- Part 3 – How Disrupted Production Leads to Unhappy Customers
- Part 4 –How Production Stoppages Can Break Your Supply Chain
- Part 5 – How Breakdowns Can Lead to Safety Shortcomings
- Part 6 – How Equipment Failures Drain Employee Drive
- Part 7 – How Constant Breakdowns Lead to Spiraling Maintenance Costs
- Part 8 – How Lost Production Time Leads to Lower Competitive Edge
- Part 9 – How Shop Floor Stoppages Lead to Regulatory Pitfalls
- Part 10 – How Missed Production Uptime Means Missed Opportunities