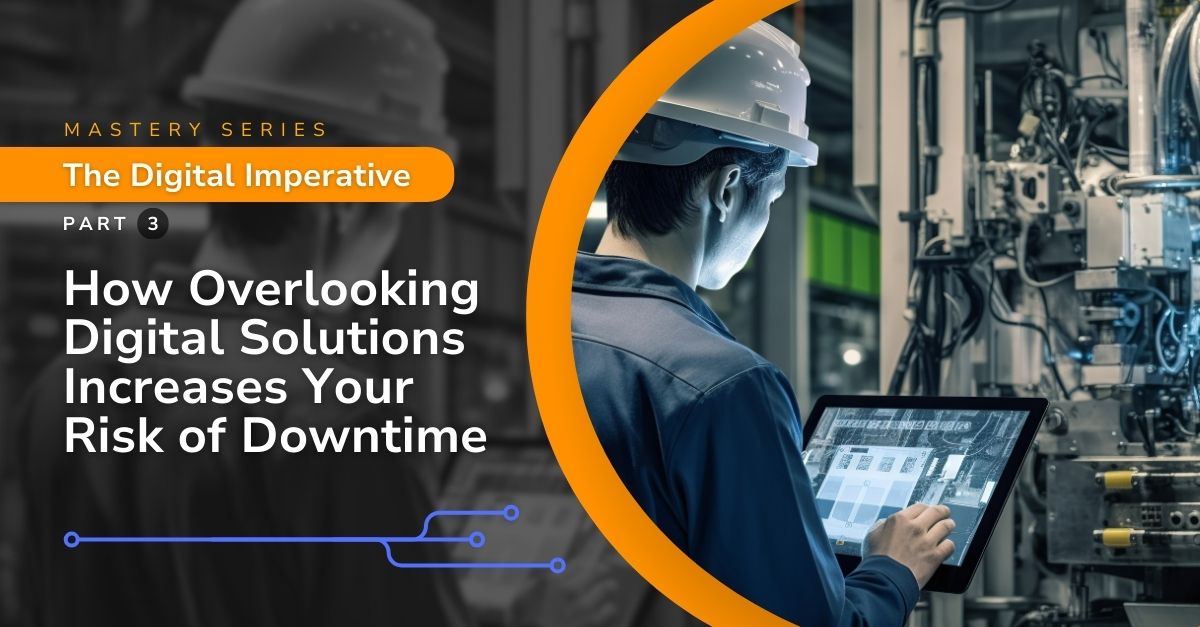
Manufacturers that resist the adoption of Industry 4.0 technologies face significant setbacks in productivity, especially when it comes to missed opportunities for predictive maintenance.
These missed opportunities often arise because of a failure to integrate advanced digital tools that enable real-time equipment monitoring, data analysis, and automation of maintenance tasks. Instead, traditional practices that rely on reactive maintenance or rigid preventive schedules become the norm, leading to inefficient use of resources and increased downtime.
Without it, shop floors suffer from various secondary symptoms that erode productivity.
One less commonly discussed example is the strain on inventory management. Stockpiling spare parts becomes the default approach when a plant lacks accurate predictive data on equipment wear and tear. This ties up capital in parts that may not be needed immediately while increasing the risk that critical components are still missing when an unexpected failure occurs. The result is a frustrating imbalance where too much inventory clogs the system, and essential parts aren’t readily available when required.
Neglecting digital transformation and missing out on predictive maintenance does more than just complicate inventory. It disrupts key operational areas, forcing skilled labor to focus on manual inspections, delaying identifying issues, and increasing reliance on reactive repairs. These inefficiencies ripple across the entire operation, limiting a manufacturer’s ability to stay competitive and agile in a rapidly evolving industry.
The following sections explore ten specific ways that failing to embrace predictive maintenance leads to reduced productivity and compromised operational efficiency. These issues stem from the broader challenge of failing to fully integrate Industry 4.0 principles.
1Inconsistent Machine Performance Tracking:
When manufacturers fail to implement predictive maintenance tools, tracking machine performance becomes inconsistent and unreliable. Without continuous monitoring systems, managers must rely on sporadic manual checks, which may miss subtle performance declines that signal impending production issues. This inconsistency can result in machines operating below optimal efficiency unnoticed for long periods.
Mitigation: Implementing sensors and IoT-based performance monitoring systems provides real-time data, allowing for a continuous overview of machine health. Using these tools, managers can track performance trends and address issues before they escalate, ensuring machines operate efficiently and reduce unplanned downtime.
2Poor Understanding of Equipment Lifecycle Data:
Manufacturers who fail to embrace digital transformation often lack detailed insights into their equipment’s lifecycle data. Without this information, it becomes difficult to predict when a machine is approaching the end of its operational life or when parts are likely to fail. This results in unexpected breakdowns that disrupt production schedules.
Mitigation: Companies can collect and analyze equipment lifecycle data by adopting predictive maintenance systems. This allows managers to better understand wear and tear patterns, schedule timely maintenance, and make informed decisions on equipment replacement, thereby avoiding sudden failures and extending the useful life of machinery.
3Increased Pressure on Manual Inspection Processes:
Without predictive maintenance, the burden falls heavily on manual inspection processes. This increases labor costs and heightens the risk of human error. Manual inspections can miss early signs of deterioration, especially if inspections are performed infrequently.
Mitigation: Automated monitoring systems relieve the pressure on manual inspections by continuously tracking equipment conditions. These systems can detect minute changes that humans might overlook, leading to earlier identification of issues. Integrating such technologies reduces the need for labor-intensive inspections while improving accuracy.
4Delayed Identification of Wear and Tear:
Without predictive maintenance, identifying wear and tear in equipment is often delayed until a breakdown occurs or performance visibly deteriorates. This reactive approach leads to more frequent machine downtime, increased repair costs, and a higher likelihood of extensive damage to equipment.
Mitigation: Predictive maintenance tools, such as vibration analysis and thermographic monitoring, enable the early detection of wear and tear. By continuously analyzing equipment conditions, these tools provide alerts when parts are wearing down, allowing maintenance teams to replace components before they fail and preventing costly downtime.
5Inability to Implement Cost-Saving Automation in Maintenance:
A lack of digital transformation often means manufacturers miss out on automating routine maintenance tasks. This results in higher labor costs, as skilled workers are required to perform time-consuming manual tasks. Additionally, the inability to automate can slow the response time to emerging issues, further reducing productivity.
Mitigation: Integrating predictive maintenance with automated maintenance workflows reduces the need for manual intervention. For example, IoT devices can trigger maintenance protocols automatically when certain conditions are met. This saves on labor costs and ensures faster and more consistent maintenance responses, keeping machines in optimal condition.
6Over-Reliance on Reactive Maintenance:
Neglecting digital transformation leads to an over-reliance on reactive maintenance strategies. Instead of addressing issues before they occur, teams are forced into a constant cycle of responding to machine failures. This approach is inefficient because it often results in overtime or hiring expensive outside contractors and frequent disruptions to production.
Mitigation: Transitioning to predictive maintenance shifts the focus from reactive to proactive strategies. Real-time data allows managers to schedule repairs or part replacements with available parts and labor before a breakdown occurs. This reduces the frequency of emergency maintenance, minimizes downtime, lowers labor costs, and allows for better planning of maintenance activities.
7Uncertainty in Optimal Replacement Times for Parts:
When digital tools are not in place, determining the optimal time to replace machine parts becomes a guessing game. Parts may be replaced too early, wasting resources, or too late, leading to equipment failures that halt production. This uncertainty can significantly impact operational efficiency.
Mitigation: Predictive maintenance systems provide data-driven insights into part wear, enabling managers to replace components at precisely the right time. This eliminates guesswork, reduces unnecessary part replacements, and prevents unexpected equipment failures, ensuring smoother production workflows.
8Inability to Accurately Forecast Maintenance Schedules:
Without predictive maintenance, forecasting future maintenance needs is highly challenging. Managers must rely on outdated maintenance schedules that don’t account for the actual condition of the equipment. As a result, maintenance may be performed too frequently or not frequently enough, leading to inefficiencies.
Mitigation: Using predictive maintenance, teams can develop dynamic maintenance schedules based on real-time data. This ensures that maintenance activities are conducted only when necessary, optimizing resource use and minimizing disruptions to production. Accurate forecasting also allows for better budgeting and resource allocation.
9Increased Frequency of Equipment Failures:
Without predictive maintenance, the frequency of equipment failures increases as issues go unnoticed until they cause significant damage. This leads to frequent production stoppages, increased repair costs, and extended downtime, negatively impacting overall productivity.
Mitigation: Predictive maintenance tools help prevent equipment failures by identifying potential problems early. By monitoring the health of machines continuously, managers can take corrective action before a minor issue turns into a major failure. This reduces the frequency of breakdowns and ensures smoother production processes.
10Overuse of Resources Due to Delayed Maintenance:
When maintenance is delayed, equipment may continue to operate in a degraded state, consuming more energy and materials than necessary. This overuse of resources not only increases operational costs but also shortens the lifespan of the equipment, leading to more frequent replacements.
Mitigation: By adopting predictive maintenance, managers can ensure that maintenance is performed optimally, preventing unnecessary resource consumption. This leads to more efficient use of materials, lower energy costs, and extended equipment life, all of which contribute to improved productivity and cost savings.
Conclusions for Operations Leaders
Neglecting Industry 4.0 and digital transformation, especially in predictive maintenance, presents challenges that negatively impact productivity and operational efficiency. From inconsistent machine performance tracking to delayed identification of wear and tear, these missed opportunities cost manufacturers time, resources, and competitiveness. Embracing predictive maintenance allows manufacturing operations to move from reactive to proactive strategies, significantly reducing downtime, improving equipment lifespan, and ensuring smoother workflows.
By implementing advanced digital systems, these organizations can reduce reliance on manual processes, forecast equipment needs with precision, and make smarter, data-driven decisions that enhance productivity across the board.
Ready to Elevate Your Manufacturing Operations with Real-Time Data and AI-Driven Insights?
POWERS offers a comprehensive solution for manufacturers eager to thrive in the digital era. We specialize in guiding you through the complexities of digital transformation and optimizing critical areas across your value chain to drive sustainable productivity and profitability.
With the introduction of DPS, our cutting-edge Digital Production System, we bring you the tools you need to stay ahead. DPS is the culmination of decades of our manufacturing operations expertise combined with the latest AI-powered technology designed to empower your operations like never before.
Here’s what POWERS DPS can do for you:
- Complete Visibility: Monitor production in real-time, identify inefficiencies, and streamline operations with intuitive dashboards and analytics.
- Enhanced Collaboration: Foster seamless communication across your team with instant data sharing and collaborative insights that drive continuous improvement.
- Data-Driven Decision Making: Utilize advanced AI to predict challenges, optimize scheduling, and make smarter decisions at every production stage.
- Boosted Productivity and Efficiency: Minimize downtime, maximize resource allocation, and unlock your workforce’s full potential.
By partnering with POWERS, you gain more than just a service—you gain a strategic advantage that positions your manufacturing operations for long-term success in a rapidly changing digital landscape. Reach out today to discover how we can help you transform your predictive maintenance strategy and achieve measurable improvements in productivity and profitability.
- Speak to an Expert: Call +1 678-971-4711 to discuss your specific challenges and goals.
- Email Us: Get tailored insights by emailing info@thepowerscompany.com
- Request an Assessment: Use our online contact form, and one of our expert manufacturing consultants will reach out to schedule an in-depth analysis of your operations.
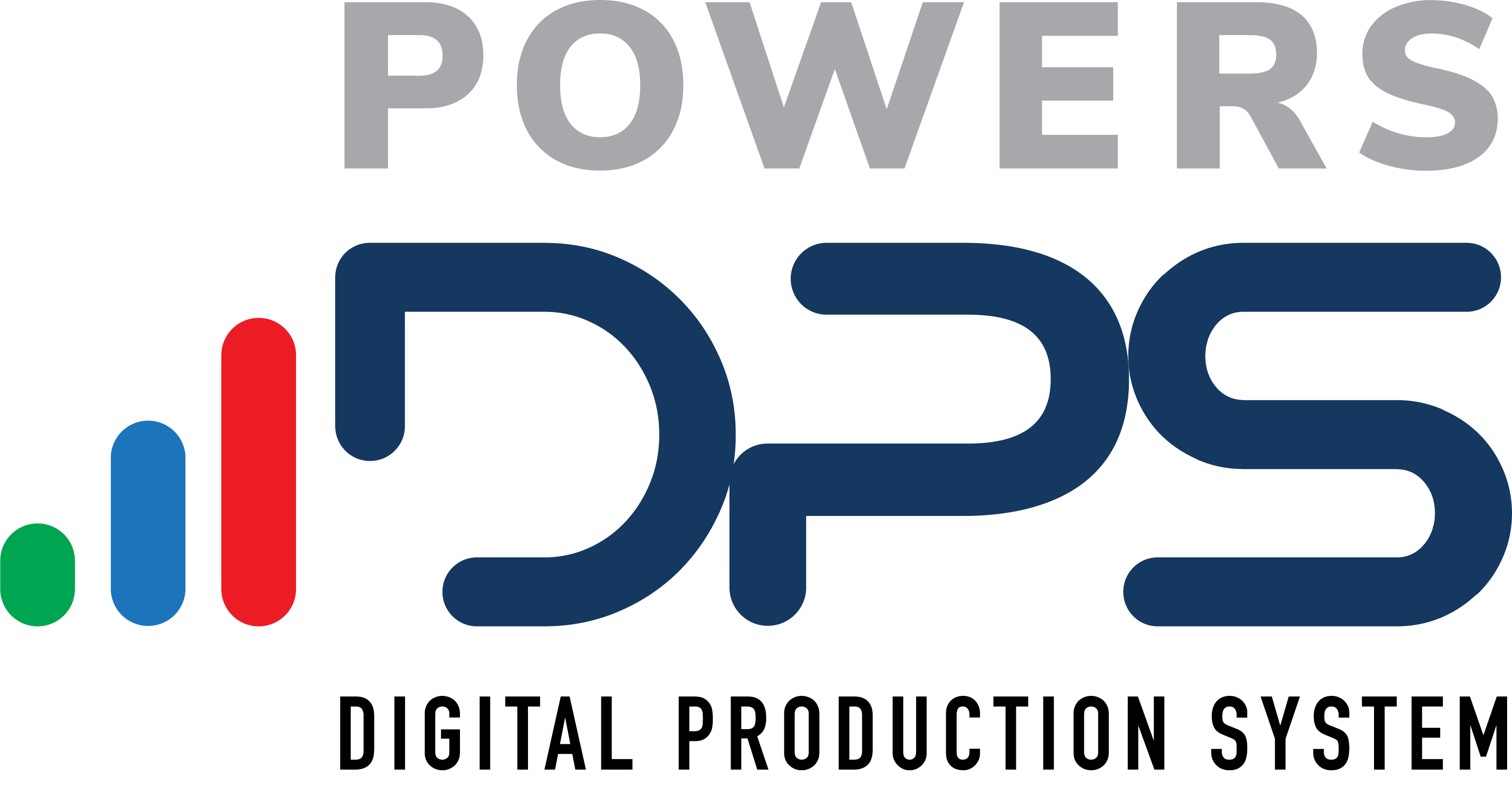
Start transforming your operations today with POWERS DPS. Contact us for a free consultation and see how digital transformation can revolutionize your manufacturing future. Learn More about DPS
Continue Reading from this Mastery Series
- Part 1 – Outdated Tech is Weakening Your Talent Pipeline
- Part 2 – How Legacy Systems Sabotage Your Cybersecurity and Productivity
- Part 3 – How Ignoring Digital Tools Leaves You Vulnerable to Downtime
- Part 4 – When Digital Stagnation Leads to Poor Communication and Production Chaos
- Part 5 – The Real Cost of Trying to Keep Up in the Market Without Digital Transformation
- Part 6 – Missing Out on Real-Time Data Drains Productivity and Profit
- Part 7 – How Failing To Go Digital Jeopardizes Regulatory Compliance
- Part 8 – How Outdated Inventory Practices Sabotage Your Operations
- Part 9 – Limited Customization Options are Driving Your Customers Away
- Part 10 – The Productivity Trap of Failing to Scale Digital Initiatives