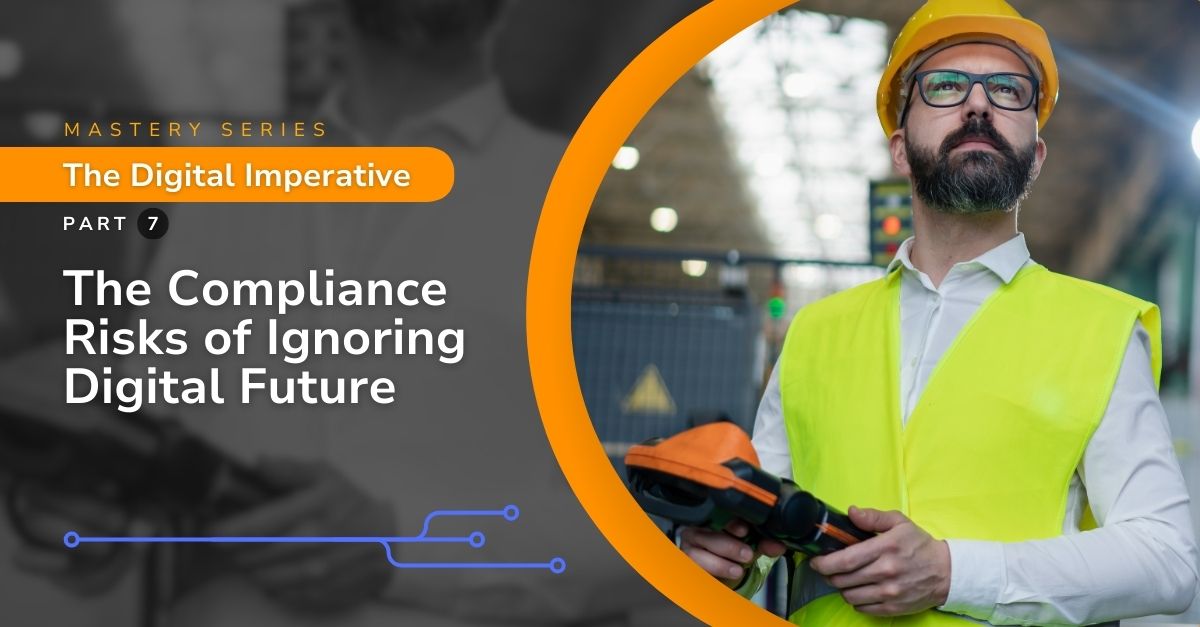
The manufacturing sector is experiencing rapid changes driven by technological advances and the demand for higher operational efficiency.
Industry 4.0 technologies like automation, artificial intelligence, and the Internet of Things (IoT) are now critical tools for staying competitive and meeting regulatory requirements. Yet, companies that fail to embrace these technologies and neglect digital transformation struggle to keep pace with evolving regulations.
A less common example of this problem is machine safety certifications, where equipment must regularly meet updated standards to remain compliant. In a digitally lagging facility, the lack of automated tracking systems for these certifications results in outdated or incomplete manual documentation. This increases the risk of equipment operating without current certifications, exposing the company to safety violations or legal consequences. The manual process of gathering and updating these certifications is prone to human error. It consumes valuable time that is better spent on production optimization, ultimately reducing overall operational efficiency.
Increased difficulty complying with evolving regulations is not just an administrative burden—it also creates a cascade of secondary symptoms across the organization. Managers face delays in adopting new safety protocols, inaccurate tracking of compliance data, and difficulties in training employees on new regulations. This increases the risk of non-compliance and puts additional strain on productivity, as more time is spent rectifying issues rather than driving continuous improvement. Manufacturers are left ill-equipped to adapt to the fast-changing regulatory landscape by neglecting digital transformation, resulting in avoidable operational setbacks.
1Missed Updates on Newly Implemented Safety Protocols:
Manufacturing safety protocols evolve with new technologies and industry advancements. When companies neglect digital transformation, they often miss critical updates, as manual systems lack the automation to notify key stakeholders of new compliance requirements. This can lead to outdated practices being followed on the shop floor, putting employees and the company at risk of safety violations and fines. As regulations shift, ensuring that all protocols are up to date is crucial for maintaining a safe, compliant environment.
Mitigation: Implementing real-time monitoring systems and digital platforms that automatically push notifications for updates in safety regulations can mitigate this risk. With the proper digital infrastructure, managers receive alerts when new safety protocols are rolled out, ensuring immediate action is taken to update practices. Regular software updates in a connected system allow faster adaptation to new regulations and improved safety compliance across the workforce.
2Poor Management of Compliance Risk Assessments:
Neglecting Industry 4.0 results in the reliance on manual risk assessments, which are time-consuming, prone to human error, and often fail to capture the full scope of compliance risks. Without digital tools, compliance managers struggle to assess and prioritize risks based on data, leading to incomplete or inaccurate evaluations. This often results in overlooked hazards and inefficient risk mitigation strategies, compromising safety and regulatory adherence.
Mitigation: Adopting automated risk assessment tools can vastly improve the accuracy and efficiency of compliance management. These tools allow for real-time data collection, analysis, and reporting, providing managers with a comprehensive view of potential risks. By leveraging advanced data analytics and AI, companies can prioritize risk areas more effectively and streamline implementing corrective actions, reducing non-compliance and improving overall productivity.
3Inaccurate Reporting of Safety Compliance Data:
When companies fail to digitize their reporting systems, they often face challenges with inaccurate or incomplete safety compliance data. Manual processes are vulnerable to inconsistencies, and the lack of real-time data hinders the ability to provide accurate reports during audits or inspections. This increases the risk of penalties for non-compliance and affects productivity, as managers must spend more time correcting errors or justifying discrepancies.
Mitigation: Integrating digital reporting tools that capture real-time compliance data ensures accuracy and transparency in safety reporting. These systems can automatically generate compliance reports from live data collected across the manufacturing floor. Automated data entry reduces the potential for human error and facilitates a smoother audit process, enabling managers to focus on core production activities instead of administrative tasks.
4Inability to Perform Accurate Compliance Audits:
Without embracing digital tools, many companies struggle to perform thorough compliance audits. Manual audits require extensive paperwork and data compilation, which is time-consuming and prone to omissions. Additionally, the lack of integrated systems can result in inconsistent audit results, making it difficult for organizations to demonstrate compliance across all areas of operation.
Mitigation: Digital audit management systems streamline the compliance audit process by providing a centralized platform for all compliance data. These tools allow for automated scheduling, tracking, and reporting of audits, ensuring that all necessary information is readily available. Auditors can access real-time data from various departments, increasing the accuracy of the audits and reducing the time spent gathering documentation. Organizations can avoid compliance issues with a digital approach and improve audit outcomes.
5Difficulty Training Employees on Updated Compliance Measures:
Neglecting digital transformation hampers the ability to effectively train employees on new compliance measures. Without digital training platforms, companies often rely on outdated manuals and in-person sessions, which are difficult to scale and monitor for effectiveness. This leads to inconsistent knowledge levels across teams, increasing the likelihood of non-compliance due to a lack of understanding.
Mitigation: Employing e-learning platforms and digital compliance training tools can help standardize the education process for employees. These platforms allow for easy updates to training materials, ensuring employees are always trained on current compliance measures. Progress can be tracked digitally, allowing managers to identify knowledge gaps and provide targeted support, leading to better compliance and improved productivity.
6Increased Likelihood of Non-Compliance Due to Lack of Digital Literacy:
When organizations fail to adopt Industry 4.0 technologies, they often face a workforce with limited digital literacy. This gap becomes especially problematic when compliance measures require digital reporting, training, or tracking systems. Employees uncomfortable with digital tools may struggle to properly follow compliance procedures, increasing the risk of violations.
Mitigation: Investing in digital literacy training for employees ensures they are proficient in using new technologies, enabling them to effectively engage with compliance systems. By building a digitally savvy workforce, organizations can improve adherence to compliance measures and reduce the likelihood of violations. Continuous training programs also help employees stay current on technology and regulatory changes.
7Inconsistent Tracking of Compliance Certifications and Renewals:
Manual systems for tracking compliance certifications and renewals are inefficient and prone to errors. Missed deadlines for certifications or renewals can lead to non-compliance penalties and create operational delays. Companies that do not use automated systems often find it difficult to maintain accurate records of certifications, especially as regulations evolve and requirements change.
Mitigation: A digital compliance management system can automate the tracking of certifications and renewals, sending reminders to managers when deadlines are approaching. These systems provide a centralized repository for all certification data, ensuring that documentation is up-to-date and accessible when needed. Automated tracking reduces non-compliance risk and ensures that operations continue without interruptions.
8Failure to Adapt to Industry-Specific Compliance Changes:
Different industries have unique compliance requirements, and as regulations change, companies that fail to keep up often face challenges adapting their processes. Organizations risk non-compliance without digital systems to track and implement these changes, resulting in fines, shutdowns, or lost business opportunities.
Mitigation: Industry-specific compliance software can help organizations stay current with regulatory changes. These platforms provide tailored compliance solutions that automatically update to reflect the latest industry standards. By leveraging digital systems, companies can quickly adjust their operations to meet new regulations, minimizing disruptions and maintaining productivity.
9Delays in Responding to Regulatory Inspections:
When compliance systems are not digitized, organizations often face delays in responding to regulatory inspections. Managers may struggle to compile the necessary documentation or demonstrate compliance, leading to extended inspection times and potential fines for delayed responses. These delays can disrupt production schedules and negatively impact productivity.
Mitigation: Digital compliance management platforms enable organizations to quickly generate and provide the necessary documentation during regulatory inspections. With all compliance data stored in a centralized system, managers can easily access and present the required information, reducing delays and ensuring smoother inspections. This not only improves compliance but also minimizes production downtime.
10Difficulty Maintaining Compliance Documentation:
Manually maintaining compliance documentation is a time-consuming process that often results in disorganized or incomplete records. Without a digital system, companies may struggle to keep track of all necessary documentation, especially as regulations evolve. Inaccurate or missing documentation can lead to non-compliance, penalties, and increased time spent on administrative tasks.
Mitigation: Implementing a digital document management system allows for the secure storage and easy retrieval of compliance documentation. These systems can automatically organize and update records as needed, ensuring that all documentation is accurate and accessible. By digitizing the documentation process, companies can reduce the administrative burden on managers and improve their ability to comply with evolving regulations.
Conclusions for Operations Leaders
Manufacturing organizations that fail to embrace Industry 4.0 and neglect digital transformation are disadvantaged when complying with evolving regulations. These companies not only struggle with meeting compliance requirements but also face a range of secondary symptoms that negatively impact productivity, including missed updates on safety protocols, inaccurate reporting, and delays in responding to regulatory inspections. Each issue creates operational inefficiencies that could be easily avoided with the proper digital infrastructure.
With our consulting services and the introduction of DPS, our innovative Digital Production System, we empower manufacturers to unlock the full potential of Industry 4.0 technologies. DPS integrates AI-driven insights with real-time data to optimize every aspect of your production, ensuring you remain compliant while maximizing efficiency.
Here’s how POWERS and DPS can help you stay compliant and boost productivity:
- Complete Visibility: Monitor safety protocols, compliance certifications, and real-time production data to stay current with the latest regulatory requirements.
- Operational Efficiency: Streamline workflows and enable faster decision-making with real-time data access.
- Centralized Data: Easily access and share key information across teams for better collaboration.
- Enhanced Training and Knowledge Sharing: Utilize DPS to deliver consistent, up-to-date compliance training to employees, ensuring everyone understands and adheres to the latest regulations.
- Data-Driven Decision Making: Make smarter decisions using AI-powered insights that optimize workflows and reduce the risk of regulatory violations, keeping your operations running smoothly.
Ready to take the next step in your digital transformation journey? With POWERS and DPS, you’ll meet today’s regulatory challenges and unlock sustainable productivity and profitability improvements across your entire operation. Don’t let outdated systems hold you back—embrace the future of manufacturing today.
- Speak to an Expert: Call +1 678-971-4711 to discuss your specific challenges and goals.
- Email Us: Get tailored insights by emailing info@thepowerscompany.com
- Request an Assessment: Use our online contact form, and one of our expert manufacturing consultants will reach out to schedule an in-depth analysis of your operations.
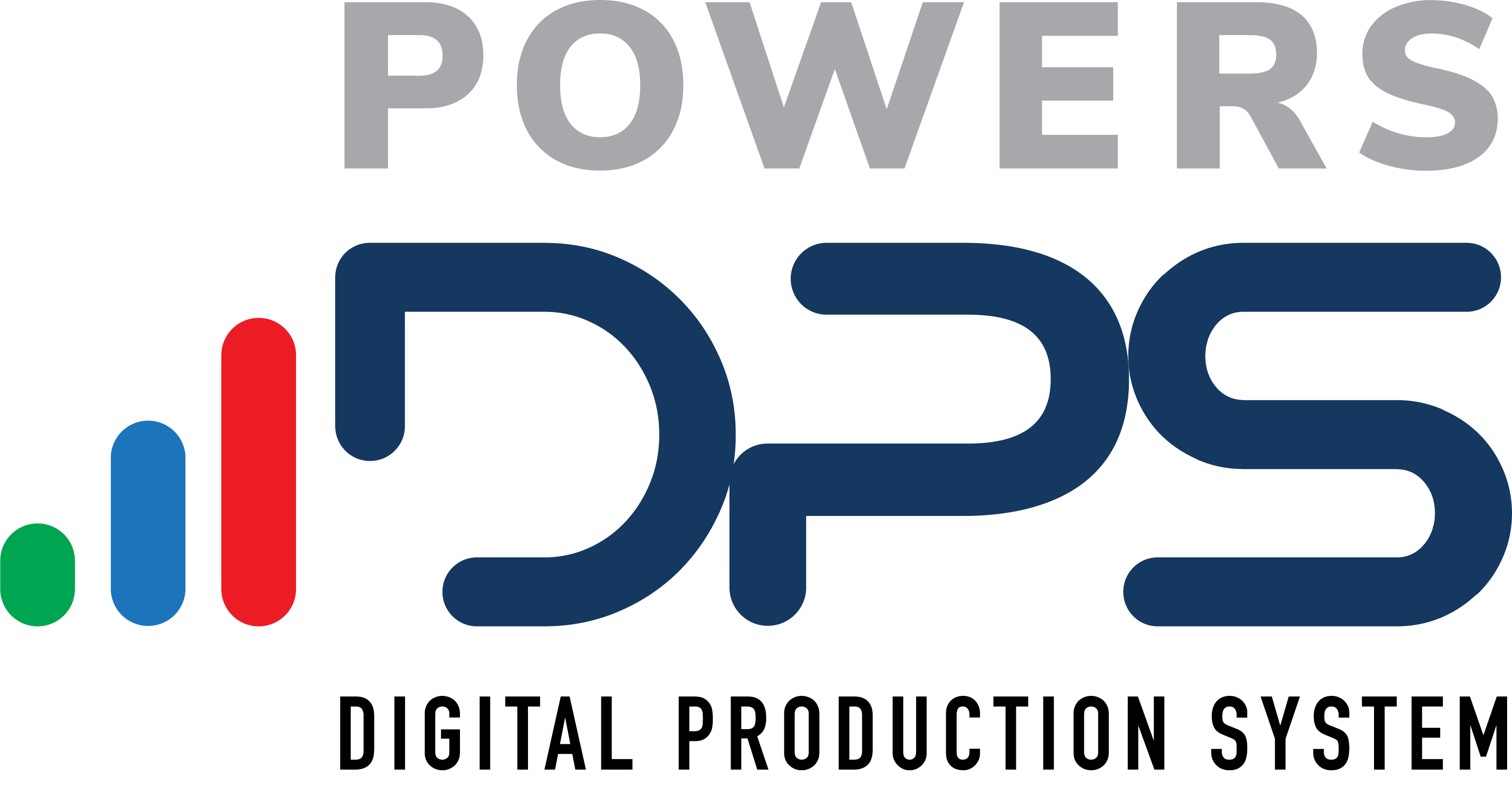
Start transforming your operations today with POWERS DPS. Contact us for a free consultation and see how digital transformation can revolutionize your manufacturing future. Learn More about DPS
Continue Reading from this Mastery Series
- Part 1 – Outdated Tech is Weakening Your Talent Pipeline
- Part 2 – How Legacy Systems Sabotage Your Cybersecurity and Productivity
- Part 3 – How Ignoring Digital Tools Leaves You Vulnerable to Downtime
- Part 4 – When Digital Stagnation Leads to Poor Communication and Production Chaos
- Part 5 – The Real Cost of Trying to Keep Up in the Market Without Digital Transformation
- Part 6 – Missing Out on Real-Time Data Drains Productivity and Profit
- Part 7 – How Failing To Go Digital Jeopardizes Regulatory Compliance
- Part 8 – How Outdated Inventory Practices Sabotage Your Operations
- Part 9 – Limited Customization Options are Driving Your Customers Away
- Part 10 – The Productivity Trap of Failing to Scale Digital Initiatives